Wooden pole construction
Under wooden pole type refers to a type of construction, in pressure treated wood poles but clamped as supporting pillars without foundation with concrete casing in the ground. This has the advantage that all vertical and horizontal effects are diverted directly into the ground and additional stability measures, such as stiffening against horizontal thrust by wall panels or corresponding diagonal struts, can be dispensed with.
In Germany , this type of construction is mainly used in agriculture , as it is a very inexpensive variant to accommodate livestock and agricultural goods. In addition, the support clamped directly into the subsoil is the simplest type of support for a roof.
This construction method with the simple wooden support as a load-bearing element and the foundation of structures on piles is one of the oldest methods of building structures in human history. Already in the prehistory around 1100 BC Round wood piles were used for the construction of housing estates ( see: Pfahlbaumuseum Unteruhldingen ). In archeology, the remaining post holes are an important aid for localizing structures.
The modern wooden pole construction draws on experience of 7–8 decades, especially from North America and Scandinavia . Development in Germany began around 40–50 years ago. The emergence of the standard, DIN 18900, took another twenty years to come. This standard only permits single-storey buildings for agriculture and trade, e.g. B. stables, barns, sheds, warehouses, multi-purpose halls, but also open spaces and covered parking spaces. With its simple design, the wooden mast construction allows such buildings to be built inexpensively. The economic efficiency is mainly achieved through the elimination of strip foundations , wind bracing and complex connecting structures between the concrete foundation and the wooden structure. Another advantage is that buildings can be easily expanded thanks to the individual clamping of the masts.
Wood protection
According to DIN 18900, only wooden masts from the pine group and the spruce group are used as load-bearing masts . However, the prerequisite for the safe use of these masts is chemical wood protection , since the mast is exposed to the soil moisture in the ground and above the ground to a wide variety of weather conditions as well as fungi and animal pests . The usual variant for the impregnation of masts is the use of coal tar oil . This process is also the only permitted wood preservation process with hydrophobic impregnation agents for wooden mast construction. As a method of introducing coal tar oil, only pressure impregnation is permitted for wooden poles . In this large-scale process, the wood is soaked in lockable pressure-tight kettles with positive and negative pressure and the protective agent is thus pressed into the cavities of the wood. The depth of penetration varies depending on the type of wood.
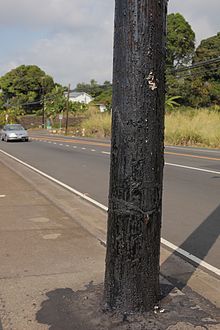
The pine logs that are often used in wooden mast construction are impregnated right down to the core. It is a bit more problematic when using spruce logs. Since the coal tar oil cannot penetrate as well, only depths of up to 15 mm are achieved here. For this reason, only pressure impregnation with water-insoluble preparations is permitted for spruce and fir. In order to improve the penetration behavior, DIN 18900 therefore stipulates that the round timbers must be mechanically pretreated in the particularly stressed earth-air area. This critical area is limited to about 500 mm below and 400 above the later ground level. Pretreatment is understood to mean that the wood is given small cuts and slits so that the protective agent can penetrate deeper. This is done mechanically or laser-optically, whereby only the slot perforation process has made it to industrial application maturity. Once the wood has been pretreated, it goes into the pressure impregnation plant. The overpressure or the underpressure is generated in the impregnation vessel via a compressor or a vacuum pump. The tar oil preparations in the measuring vessel or in the storage container are then processed directly in delivery form. The protective agent penetrates the wood through tiny cracks, cut cells and medullary rays. In addition, the capillary pressure forces of the boiler have a positive effect and push the oils through the cell and cell wall cavities into the interior of the wood. If there is no longer any possibility of movement for the liquid due to decreasing capillary forces, it remains in the cavities of the wood. There is no further penetration, because tar oils are practically insoluble in water and therefore cannot diffuse. However, since tar oils never dry out, they remain in the wood forever as an extremely viscous liquid. Temperature fluctuations will only change the viscosity of the oil; at high temperature it becomes thinner; at low temperatures it becomes tougher. Ultimately, this leads to the fact that the oil slowly migrates down the wooden pole over time and will later be particularly concentrated there. Close to the floor, tears may leak out and even run off outside in the case of intense heat.
According to the standard, in addition to the most frequently used boiler pressure impregnation, alternating pressure impregnation and swivel tank pressure impregnation are also permitted for the foot area of the mast.
Alternatively, there is impregnation with a copper salt solution, which gives the mast a greenish tint, and other active ingredients.
The foundation
The simplest variant of the foundation would be to place the log support in the borehole and fill the cavity between the mast and the borehole wall with compacted gravel. Even if this was the usual method in the past, it turned out that after compaction there is only a little stiff restraint, which becomes stiffer due to the consolidation of the gravel-sand mixture, but also in the final state does not achieve the same stiffness as the stability of the structure and, above all, compliance with the deformation limits would be fully guaranteed.
For this reason, DIN 18900 makes the requirement for a concrete coating. This must be carried out with a compacted concrete of strength class B 10 (today: C 8/10) and firmly connected to the ground. The thickness of the jacket wall should be at least 10 cm thick and the consistency at least earth-moist K1. In addition, there are separate requirements for the subsoil and the depth of the borehole, i.e. the subsoil must have at least medium-density storage in non-cohesive soils and an at least stiff consistency in cohesive soils.