Fixative
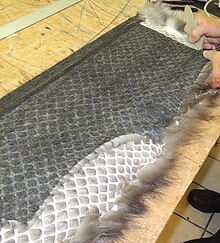
Fixing materials are inlay or intermediate materials for clothing with a surface made of meltable substances that are permanently bonded to the outer fabric with the help of fixing presses by a thermal welding process, in the case of furs with the leather side of the pelts . This gives the fixed surfaces support, protects against expansion and, depending on the material, causes more or less stiffening. The fixing material is preferably used in the front parts of outerwear, the front edges and the bust (front fixing) as well as for the lower collar. The fixing replaces the pricking , the sewing on of strengthening, possibly also warming interlinings and means a comparatively considerable saving of labor. If the shoulder area is also provided with an iron-on (sealable) insert, this is known as shape fixing .
properties
Ideally, the outer fabric and the insert should combine to form a harmonious unit when fixing. In addition to the rationalization effect against pricking, which was previously common, it creates a light and soft grip. If high-quality inserts that are resistant to cleaning, fully compensate for the tension differences between the outer fabric and the insert and have the same shrinkage behavior as the outer fabric, are also accepted in the model genre. By coating both sides with the adhesive of the fixing material, two materials can be connected to one another without affecting quality, which saves sewing (collar corners, back slit). The lamellar print is a modification of the coating of fixable interlinings for the front fixation, which allows fixation on fluffy outer fabrics. All of the inlay materials, fleeces and fabrics that are common in the clothing industry are also manufactured to be fixable.
The adhesive mass, the melt-adhesive spread on sealable inlays, is based on polyamide , polyester or polyethylene as well as their mixtures. The spread can cover the entire surface, be interrupted (point or grid, microfine) on one side or on both sides (especially for collars and waistband inserts). For fabrics that are difficult to fix, there are special adhesives with smaller adhesive dots (crinkle, crash, crespo, natural silk , cashmere wool ) and for various types of finish ( silicone ), as well as for leather and fur.
Work process
The fixing process with the fixing press requires a temperature between 120 and 150 ° Celsius, with a pressure of 100 to 150 g / cm² and a pressing time of 6 to 25 seconds. For the special area of fur fixing materials, a fixing gap temperature of 75 ° Celsius and above and a pressure of 100 g / cm² with a fixing time of 15 seconds apply. The ironing temperature depends on the manufacturer's instructions for the fixing material and the textile material to be fixed (silk, wool, synthetic, etc.) or, in the case of fur, on the type of fur (fatty furs may be better not to fixate (foals), thin-leather types of fur such as hamsters , possibly at a very low temperature). For smaller areas or reworking, the iron is occasionally used in bespoke tailoring and skinning .
The high-frequency fixing technology achieves a particularly gentle and permanent connection between the fixing material and the upper material . The high-frequency energy known from microwave technology only acts on the adhesive and maintains the natural moisture of the outer fabrics; the expansion changes only minimally. This ensures a special match with the pattern in all production stages. It is possible to fix the small and large cut parts at the same time. Due to the low working temperature of 120 ° there is hardly any heat radiation and almost all outer fabrics can be fixed. A gloss formation and an adhesive strike through are avoided.
The process of pricking is not required, and in the production of jackets and suits there is also no need to hide or stitch the outer fabric together with the wadding. In the case of double fixation, an insert material that is fixed to the entire front of the jacket is fixed to an equally deformable, shaping insert, the plaque, without the plaque acquiring its final three-dimensional shape through the cut. Multi-area insoles are also used, in which the stiffening effect is specified differently for the shoulder, chest and lap areas, with a flowing transition.
history
The textile industry may have started fixing intermediate materials around the mid-1960s. The technology only came into the fur industry around 1970, when it was possible to develop fixing adhesives with low melting temperatures.
supporting documents
- ↑ a b c d Alfons Hofer: Textile and fashion dictionary . 7th edition, Volume 1, Deutscher Fachverlag, Frankfurt am Main 1997, keywords "double fixation", "front fixation", "adhesive compound", "high frequency fixation technology". ISBN 3-87150-518-8 .
- ^ A b Alfons Hofer: Textile and Model Lexicon . 7th edition, Volume 2, Deutscher Fachverlag, Frankfurt am Main 1997, keywords “lamella printing”, “multi-area inserts”, “sealable inserts”, “stabilize”, “hide”. ISBN 3-87150-518-8 .
- ↑ a b Ingeborg Heider: 42 million meters of interlining material per year (Kufner Textilwerke KG., Munich). In: Die Pelzwirtschaft No. 1, CB-Verlag Carl Boldt, Berlin January 25, 1978, pp. 16-18.