Heating controller
A heating controller is a device for controlling heating systems with the aim of keeping a preselected room temperature constant in all supplied rooms.
Correctly used and adjusted heating controllers ensure energy-saving heating operation.
Modern controllers are able to change the system temperatures in hot water heating systems ( flow temperature , return temperature ) depending on requirements. This avoids oversupply, minimizes distribution losses and increases the energy efficiency of modern heat generators ( condensing boilers , heat pump heating systems , solar systems ).
In addition, they offer time-dependent intervention options, such as absence mode, night shutdown or night reduction , they ensure that the heating system is switched off when the heating limit is reached .
The Energy Saving Ordinance (§ 14) in Germany requires central heating systems (i.e. those heating systems that distribute heat generation and heat output to different devices and supply at least two rooms with heat) either a room temperature-controlled or outside temperature-controlled control, as well as a timer.
Control types
Room temperature-dependent control
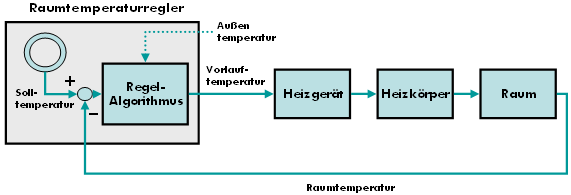
Technically, a heating controller connected to a heating device represents a control loop structure. The current room temperature corresponds to the controlled variable that is to be influenced. The difference between the value of the controlled variable and its setpoint , i.e. the desired room temperature, results in the control difference . The heating controller uses the control difference to determine the manipulated variable with which the room temperature is influenced.
Controller types differ based on the manipulated variable and how it is operated.
Controller types:
- Manual control : if an external controller is not required, the flow temperature can be set using a rotary control on the device. In this case, the controller setting must be adjusted manually to the current heat demand and personal perception.
- 2-point controller : The flow temperature can only have two values: either the maximum value set on the device control dial (heater on) or the minimum value (heater off).
The manipulated variable is determined by a temperature sensor . Such simple bimetal regulators are mostly only used today when frequent switching on and off ( cycling ) does not cause excessive wear of the heating devices, e.g. B. with electric heaters
A more precise control of the room temperature can be achieved with cascade control . Instead of regulating the heating output directly from the heating controller, the controlled system is divided into sections that are easier to control:
- Thermostat : From the difference between the desired room temperature and the actual value (control difference), the heating controller determines the control variable for the flow temperature (master control ). This serves as the setpoint of the downstream slave controller in the heater, which in turn regulates the flow temperature of the heating water.
- Continuous controller : As a constant manipulated variable, the flow temperature can assume continuous values between minimum and maximum values. Continuous control usually only makes sense if the output of the heater can be adapted approximately to the current heat demand of the building. Otherwise there will be strong overshoots in the flow temperature, which can no longer be compensated for by modulating the heating output alone. As a result, the burner starts ("cycles") frequently, which means that optimally economical operation is not guaranteed. In this case, two-point control is recommended in order to achieve longer burner runtimes. Many heating controllers can be switched between two-point and continuous operation.
When using today's room temperature-dependent heating control , the activity of the heater is only on the temperature conditions of a space -. The so-called guiding or directing space made dependent on a centrally supplied space group -. If the set temperature of this room is reached, the central heating device switches off and with it all other heating elements. So that all rooms are still adequately supplied with heating power, a room is selected as the lead room that requires the greatest heat output - even after taking into account any external heat influences such as e.g. B. TV, computer, people, animals, solar radiation, etc. (i.e. the heating will have to run the longest there until the room has the desired temperature.)
The placement of the temperature sensor must also be taken into account. Sensors should not be located on cold outside walls or in the immediate vicinity of external heat sources.
Radiator dimensions are usually chosen to match the heated room, so that all rooms in a centrally heated room group usually heat up at a similar rate (at least if there are no significant external heat influences). This is why there is rarely a room in a centrally supplied room group that always needs longer to heat up with any power setting on its radiators - including the highest - than all other rooms, even with their highest power settings on their radiators. In this case, the necessary output gradient can be created artificially by “braking” the output of the radiator in the lead room, so that more time is required to heat the room.
The throttling of the water flow through the radiators in the lead room can be done using adjustable lockshields. On radiators with presettable manual valves, the flow can be throttled at these valves.
In the other rooms, the desired temperature can then be set with conventional thermostatic valves. If the lead room should take too long to be heated up satisfactorily, the flow rate on its radiators can simply be increased a little.
An advantage of the artificial creation of the guide room is that a selection can usually be made from several rooms. In this way, aspects such as a particularly favorable installation location for the control device can also be taken into account.
Advantages:
- with constant external heat influences on the lead room, quick reaction to external heat influences in the other rooms
- Ideally, the heater and heating pump only run when there is an actual need for heat in at least one room.
Disadvantage:
- The temperature of the living rooms is controlled depending on the lead room
- In the event of poor coordination of the lead room or fluctuating external heat influences on the same, undersupply in the other rooms
- If there is insufficient thermal insulation (especially in the non-management rooms) or if the rooms are oriented differently, no need-based heat supply
- The lead room must be heated continuously, otherwise continuous control is not possible.
- If the lead room has cooled down significantly (e.g. after vacation), it takes a long time to heat up
- Depending on the usage / location, more frequent user interventions may be necessary, e.g. B. Sunshine heats the lead room and thus other rooms are undersupplied
- unsuitable for larger properties and apartment buildings
Outside temperature-based control
The currently measured outside temperature is also suitable as a reference variable for heating control. With weather-compensated control, the appropriate flow temperature is determined from the measured value for the outside temperature with the help of a so-called heating curve . This in turn serves as the setpoint for the boiler temperature control in the heater. The heating curve is defined by the slope and parallel shift and must be manually adapted to the respective building. In the case of weather-compensated control, the use of thermostatic valves on the radiators is also useful to ensure a constant room temperature. Careful adjustment of the heating curve is necessary in order to utilize the energy saving potential.
Advantages:
- No dependence on reference rooms, therefore standard for larger properties
- user friendly
Disadvantage:
- Without outside temperature compensation, the flow temperature is adjusted too quickly in the event of outside temperature fluctuations.
- internal external heat influences may not be taken into account.
Outside temperature compensation
This measure is intended to improve the disadvantage of adapting the flow temperature too quickly. This is particularly useful for well-insulated buildings or for large buildings.
Room temperature connection
Possibly useful for individual objects. In this case, the heating controller calculates the setpoint for the flow temperature from the measured values for the outside and room temperature; the effects of external heat are recorded. This is unnecessary with surface heating , as this has a so - called self - regulation effect.
Regulation via the difference in flow / return temperature of the heating
This type of control makes use of the fact that when there is an increased heat demand, the return temperature drops while the flow temperature remains the same. The controller then increases the flow temperature.
Advantages:
- It is no longer necessary to determine the heating curve, and no user intervention is required. Room and outside temperature sensors are omitted. External heat influences are recorded. Unnecessary burner starts are avoided with boilers with sliding temperatures.
Disadvantage:
- The heating system requires careful hydronic balancing , otherwise the controller will not correctly process the temperature difference between the flow and return.
- Assign individual rooms z. If, for example, constant ventilation increases the heat consumption, the return control reacts by increasing the flow temperature. All rooms are heated with a higher flow temperature. This can lead to a cancellation of the central night setback and consequently to an increasing energy consumption.
Further features of a heating controller
Night reduction
The heat loss of a heated system (house or room) depends (see basics) on the difference between the inside and outside temperature and its thermal insulation .
Since the lack of solar radiation does not warm the environment at night, the outside temperature drops and heat loss increases. This can be counteracted by the so-called night reduction.
Provided that the usage habits (absence, ventilation, sweating, sitting ...) of the "residents" allow it, it can be economical to change the setpoint for the room temperature depending on the time of day.
For example, a lower room temperature (reduced temperature) is sufficient for sleeping at night than during the day. On the other hand, the absence of residents on workdays can also offer a reasonable time frame.
The savings can only be estimated as the heat difference varies daily over the course of 24 hours.
In addition, the so-called night reduction can only be used once every 24 hours.
Modern heating controllers therefore offer a daily or weekly program that automatically switches between the daily and reduced temperature at programmable times.
Note:
A room-related individual thermostat setting, e.g. B. by radiator thermostats is a useful addition that should not be forgotten when planning. Unplanned things like ventilation or excursions shouldn't become “energy guzzlers”.
Basics:
Since the heat loss of a building is proportional to the temperature difference between the interior and exterior (→ Fourier's law ), energy can be saved through such night-time reduction . However, the effect in highly insulated buildings or in buildings with a very high thermal capacity (e.g. solid walls) is small. The widespread view that reheating costs more energy than would be saved by lowering, on the other hand, cannot be justified physically.
From a structural point of view, the inhabited space is a constantly changing complex, with temperature, oxygen content and humidity changing frequently. The appearance of condensation (low temperatures for condensing water) in or on the walls contributes to heat conduction and mold formation. Minimizing condensation makes sense as energy, building materials and the health of residents are valuable.
execution
Heating controllers are usually connected to the heater with a 2-wire (for the thermostat) or a 3-wire cable. In the event that such a line is not available or a more flexible installation of the controller is desired, controllers with radio transmission are on the market.
Checking the heating controller
With a temperature-humidity data logger it is very easy to check the control behavior of heating systems over longer periods of time. The data logger records the temperature of the living space. If the data logger is placed directly on the radiator, it records the course of the flow temperature. The data is transferred to the PC via the USB interface and displayed by the included software.
See also
Individual evidence
- ↑ patent DE19740418 .
- ↑ Room temperature-based control. In: Control heating. October 1, 2019, accessed October 1, 2019 (German).