crumple zone
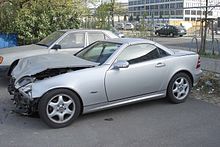
As a crumple zone to areas designated a vehicle which deform in the event of a collision and thus energy by deformation work absorbed. The term first became known in automotive technology, then it found its way into other areas, such as rail vehicles or aircraft construction. The crumple zone goes back to a patent filed on January 23, 1951 and granted on August 28, 1952 by the engineer Béla Barényi with the title "Motor vehicles, especially for the transport of people". The first vehicle model built according to this concept (division of the body into three “boxes”: soft front end, rigid passenger cell, soft rear) was the Mercedes-Benz W 111 (“tail fin”) from 1959 .
In the early days of automobile construction, vehicles were designed to be as rigid as possible, so that in the event of a collision with an obstacle or another vehicle, the car itself was often only slightly deformed (frame construction). As a result, the inmates were subjected to enormous delays . The idea of the crumple zone aims to reduce the acceleration acting on the occupants and can be derived from the equation for work .
In the event of a crash, the kinetic energy contained in the vehicle is converted into deformation energy. The work done (change in energy) is the integral of the force along the path covered in the crash . With Newton's second axiom it follows for the one-dimensional case:
with idealized constant assumed negative acceleration on impact. The energy to be converted to a standstill is given by the kinetic energy of the vehicle moving at speed :
Equating gives the (negative) acceleration for a given length of the crumple zone and speed:
Deformation zones (crumple zones)
The deformation zones of an automobile can be divided into the areas of the vehicle front, side and rear .
- Front: In frontal collisions, the highest speeds relative to the obstacle usually occur, which is why the design of the front end is of the greatest importance. In most automobiles, the motor is located in this area, which despite the high forces that occur is practically non-deformable and therefore does not consume any energy. Most of the energy is absorbed by the cross members, which are usually constructed as hollow profiles made of sheet steel. In the event of uneven force introduction (offset crash, vehicle only hits an obstacle with part of the front end of the vehicle), longitudinal beams, among other things, ensure that the forces are distributed as evenly as possible on structures on the side facing away from the impact.
- Side: In the event of a side impact, only a very small deformation path is available, and at the same time the structure is mainly subjected to bending, both of which are disadvantageous for energy absorption. The side impact is therefore the most critical form of impact. Inside the door are parts such as loudspeakers, window lifting and door closing mechanisms. In order to prevent these parts from penetrating into the passenger compartment, a corresponding inner door panel is used. Side airbags act as an inner deformation zone between the passenger and the side wall.
- Rear: The rear impact is quite unproblematic, as the relative speeds to the obstacle are usually rather low and a large deformation path is free of disturbing elements such as B. is an engine block . Only the fuel tank is usually in the rear. In order to achieve the legally required tightness of the fuel systems, the tank is placed as far forward and down as possible, often under the rear seat bench.
In modern automobiles, the body is specifically designed for crash behavior. The front of the vehicle can be roughly divided into three zones:
- The first area is designed to prevent collisions at low speeds, e.g. B. in parking bumps to prevent permanent damage to the vehicle. This is achieved through elastic elements such as the front apron. In some vehicles, the bumper is filled with foam or similar elastic materials.
- In the event of less severe collisions (up to approx. 20 km / h), the second area should ensure that the load-bearing structure of the vehicle is not damaged and that repairs can be carried out as cheaply as possible. For this, among other so-called crash tubes or crash boxes inserted. Crash tubes consist of a hollow steel profile , which converts the impacting energy by rolling up the profile. The image shows the undeformed crash tube on the left and the rolled up crash tube on the right.
- The third area is the so-called survival space, which is designed to be as rigid as possible in order to ensure the survival of the occupants.
Zones 1 and 2 therefore fall under the crumple zone category.
compatibility
Compatibility is understood to mean the attempt to keep the risk of injury as low as possible for everyone involved, even when the other parties involved in an accident are different (e.g. heavy sedans versus small cars, but also cars versus pedestrians / cyclists, etc.) Put simply, this works according to the principle: the larger and heavier the vehicle, the softer the deformation zones. This leads to the fact that z. B. when a small car collides with a heavier, larger vehicle, the latter absorbs the greater part of the kinetic energy of both vehicles, since it usually has a much larger deformation path. The risk of injury for the occupants of the smaller vehicle is not significantly increased compared with the occupants of the heavier vehicle. However, this development is still relatively new.
A crash test in the mid-1990s in which a Mercedes-Benz S-Class sedan (W 140) collided with an Opel Corsa B generated greater public attention with regard to the unequal mass ratios of vehicles of different classes in an accident . After the frontal crash with 50/50 overlap of the vehicles, the S-Class showed only marginal deformations, while the crumple zone of the Corsa collapsed completely and caused damage to the passenger cell. In response to these test results, Mercedes comprehensively adapted its occupant protection to the compatibility and requirements of collisions with smaller vehicles.
See also
Web links
Individual evidence
- ↑ Patent No. DBP 854 157, Lifesaver for Thousands. In: Global Media Site Daimler AG . January 23, 2009, accessed April 4, 2019 .