Palletizer
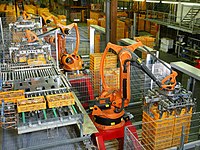
A palletizer or palletizing robot is a process automation system that automatically collects packages on load carriers . The well-known 4- or 6-axis industrial robot systems can be used for this task.
There are basically four types of palletizers: the articulated arm robot , as layer palletizer as linear robot or as Portalpalettierer .
Articulated robots
Articulated arm robots are often used in the automotive industry, usually 6-axis machines with a spherical gripping area. Their area of application is extensive and they are flexible, special adaptations are necessary for each area of application.
Layer palletizer
With a layer palletizer, complete layers of a pallet load are placed on a pallet. Layer palletizers are considered to be the most powerful palletizers. Layer palletizers are generally distinguished by two different modes of operation.
- Layer palletizer with pallet lift: the product is fed in at a higher level (e.g. +3200 mm). The empty pallet is lifted under the pre-grouped layer. By opening a sliding floor, the layer is placed on the pallet.
- Layer palletizer with layer lift: product infeed often at the bottom (e.g. +1000 mm). The pre-grouped layer is lifted over the pallet and the layer is set down by opening a sliding floor.
The version of the palletizer with pallet lift is considered a more powerful variant.
Linear robot
Linear axis robots are used for moving packages or sorting tasks. Thanks to this design, the workspace is ideally cubic, so it can only be used efficiently with free access from above. Systems of this type usually consist of three axes of movement for positioning in space and an axis of rotation for tool alignment or object positioning. The work area must be designed in such a way that there is no need to access it from below, the longitudinal axis does not need to be rotated 360 ° and there are as few dependent evasive movements as possible. In addition, the higher the machine travels, the lower the accuracy of the target. The vibrations then occurring must be taken into account.
Portal palletizer
The portal palletizer is a portal robot consisting of three linear axes. A linear robot can drive completely through the cubic space. While an articulated arm robot always has to turn around its own axis, a portal robot can always drive the most direct route.
Gantry robots are elevated robot systems that span a cubic gripping area through three linear main axes. Full portals stand on four feet, half portals stand on two feet. The actual robot kinematics or the moving axes are located above this elevation.
The feet of this type of robot have to be very robust and massive so that the dynamics of the overhead axes cannot introduce vibrations into the entire structure. Due to their construction, portal robots can cover a fairly large work area. Another advantage is that the load capacity is also quite high, as the loads to be carried can be easily absorbed on both sides via the upper portal axes. If you disregard the legs, the product can be fed in from all sides and from all directions. The types of gantry robots that are offered for palletizing tasks usually have a fourth axis (axis of rotation) in order to be able to align the packages on the pallet.
Final packaging systems
Ready-packed products that are packed in bags or sacks are layered on a transport pallet with the help of a palletizer . The technology required for this is very extensive, as the process is carried out fully automatically. The product must be fed to the palletizer via conveyor belts or roller conveyors. This rotates and turns the product in a process-controlled manner so that the complete layering on a pallet consists of differently arranged layers. After the pallet is finished, the loaded pallet is either stored immediately or further packed. This is followed by another station in production: the products are placed on the pallet, e.g. B. further packed and secured by a film winder or welded in a large plastic bag. The product is then ready for transport.
Storage systems
In addition to the pure application of the palletizer in the final packaging area, for palletizing outer packaging, these machines are also used for product handling on fully automatic assembly or production lines. It enables a workpiece to be machined to be clamped and aligned outside of the machine tool . This saves this expensive machine from unnecessary downtime.
The palletizers are loaded with products (or with products to be loaded) workpiece carriers ( trays ) via a double belt conveyor from the outside automatically. Several workpiece carriers are placed on top of each other on the feed path. The stack enters the palletizer and the workpiece carriers are removed by a separating device . The workpiece carrier is moved to the transfer position via a horizontal table axis and positioned there. The workpiece carriers are filled or emptied via a further handling axis at the fixing station. Depending on the process, palletizing or depalletizing, the products are removed from the workpiece carriers by a gripping system located on the handling axis and placed on the assembly line, or they are picked up from the production line and placed in the workpiece carrier.
After the processing process, the full (empty) tray is moved from the table axis to a third position in the palletizer and stacked there. If a certain number of trays are available, the stack is moved out of the palletizer via the double belt conveyor and made available again outside the machine.
The area of application of this type of palletizer is more likely to be seen in magazining or in storing workpieces. Often there are small parts or individual parts that are fed to an assembly process or come from a production process (injection molding machines). However, cans or bottles used for a filling process can also be isolated and made available for filling.
Today's palletizing systems allow a positioning accuracy on a machine tool of less than a hundredth of a millimeter, and that within a few seconds. This is done either manually or automatically using a pallet changer . The clamping of the workpiece on the pallet on the back, usually on the back, enables 5- sided machining, which is also essential for efficient machining of the workpiece. Several successive work steps can be carried out on a wide variety of machine tools equipped with the same palletizing system. Intermediate checks on measuring machines are also possible.
Palletizing cell
A palletizing cell is a particularly compact, modular, standardized and therefore cost-effective robot cell for the fully automatic palletizing of products. The cell contains a palletizing robot with gripper, a palletizing station, a feed conveyor system for the products and, if necessary, a pallet conveyor system for the fully automatic delivery and removal of the pallets. Further optional components are a pallet magazine, interlayer magazine or camera technology. For security reasons, the entire cell is surrounded by a protective fence. The gripper technology is adapted to the respective product. The cell is often mobile and can be moved if necessary. The advantages for the customer compared to an individual solution are the faster planning phase, shorter delivery times and lower costs as well as the compact and mobile structure.
Manufacturers are e.g. B. de Man Automation , AKON Robotics , Krüger Industrieautomation .
Individual evidence
- ↑ Compact palletizing cell for more efficiency. de Man Automation + Service GmbH & Co. KG
- ↑ palletizing cell. AKON Robotics, Bremen
- ↑ palletizing cell. Krüger Industrieautomation GmbH, January 13, 2020 .