Lead time
The throughput time ( English throughput time or lead time ) is the time that an object or an entity needs to run through a system. The calculation of the lead time depends on the respective system and entity types.
Lead time in production
The lead time is a central term in production control. Within production , the lead time refers to the period of time that is required from the start of processing to the completion of a finished product . In detail, the lead time is made up of set-up time , processing time and idle time ; for some authors the transport time is also shown separately.
In the context of the sequence problem , which is solved by scheduling , the times are differentiated as follows:
- The idle time is the unwanted waiting time of the product within the production system.
- The processing time is the time that is technically required to manufacture the product. This also includes desired idle time, such as drying after painting.
- The set-up time results from the property of some resources to be able to carry out different processes. To do this, however, the resource must be set (set up) in the correct state. A simple example is a food processor that first has to be equipped with the right blades for a planned processing.
- The transport time is the time required to transport the product before and after processing
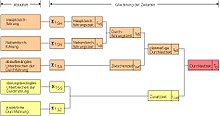
Fundamentally different REFA after expiration types for
- the people (activity - interruption - recovery) and an associated job time
- the operating resources (use - interruption) and an associated operating resource time which, together with the set-up time, becomes the occupancy time and
- the subject of work (changing, checking, lying down, storing).
Since the distinction is irrelevant for the lead time, and the times for people and the equipment are defined symmetrically, the lead time is used as an umbrella term for implementation . The main and secondary execution form the execution time . Together with the intermediate time resulting from the process -related interruption , they form the planned lead time (through a workstation ). The actual lead time can be extended compared to the planned one by an additional time , formed from times for disruption-related interruptions and additional operations .
For the lead time through several workstations, the individual lead times are added together with an intermediate time that represents the idle, storage and transport times between the workstations. In view of the factual imprecision of the above, customary definition (when exactly does processing start: placing of the production order? Provision of the material? First work step? And when exactly is the completion of the product: last work step? Provision in dispatch? ...) to one clear indication of what belongs to the lead time and what does not.
For use as a key figure, lead time can be divided into mean lead time and order-related lead time . In this context, the cycle time forms the time for the production of entire order complexes.
In material requirements planning, the lead time is used as a lead time in order to calculate the point in time at which a required material must first be available at another location (e.g. in the warehouse ) so that it can be delivered on time (e.g. on an assembly line ) Available. This is also known as 'retrograde termination'.
Reduce lead time
The goal in production should always be to keep the costs of a production order as low as possible. This can be achieved, among other things, by reducing the lead time, whereby the reduction must not impair the quality of production.
- On the one hand, there is the possibility of increasing the capacity of a workplace. Due to the higher capacity, more can be produced in the same time (throughput). The concept only makes sense when there are bottlenecks (see: Theory of Limitations , Bottleneck (Logistics) , Production Program )
- On the other hand, the throughput can be increased by increasing the intensity (e.g. increasing the electrical power), since the relationship between throughput time and throughput is inverse. The possibilities are mostly limited, however, since the optimal performance of systems and the best working pace for people are usually already planned.
- In order to save set-up time, similar orders that are to be produced promptly can be combined into one order ( lot ). This means that the set-up time does not arise for every job , but only for the first one. By increasing the lot size, the average throughput time per piece on the individual workstation can be reduced; The processing times for the orders and the average processing times can increase significantly because of the additional waiting and idle times. Lot formation also affects flexibility and readiness to deliver .
- The main potential therefore lies in the organization of order processing and work organization . For example, the One-Piece-Flow and Chaku-Chaku concepts aim to reduce throughput times in multi-variant series production.
- The transport times can be reduced (slightly) by arranging the production facilities in a sensible way and using high-frequency transport systems.
- If partial lots are formed from a product for transport (transport lot <> production lot), a first partial lot can already be processed further at work system B by overlapping work steps, while work system A produces the second partial lot. Ideally, you are back to one-piece flow and chaku chaku.
Throughput times for heterogeneous production
In the case of complex technical products that are composed of many individual parts and assemblies and that are manufactured in heterogeneous production areas, the respective throughput times are often very different. One possibility to reduce throughput times is to outsource individual production sections from sequential production lines and to partially parallelise production. This approach is often found in the automotive industry. There z. B. removed the vehicle doors at the beginning of the final assembly and then completed in separate door assemblies. At the end of the assembly line, these doors are then delivered back to the final assembly line and installed. Or certain production volumes are relocated to pre-assembly by a service provider or a supplier. The pre-assembled module is then installed in the vehicle, often just-in-sequence. If the cycle times between the production areas differ significantly, there is a further possibility of setting up several parallel production lines or flexible production cells for certain parts or assemblies.
Little's law
According to Little's law , the following relationship applies between lead time, stocks and throughput:
in which:
DLZ: processing time (unit: time)
Circulating stock: stocks that are within the process (unit: pieces)
Throughput : process output within a certain time (unit: pieces per time)
See also
literature
- Joachim Käschel , Tobias Teich: Production Management . Volume 1: Basics, production planning and control, textbook and exercise book (= Society for Corporate Accounting and Controlling (GUC). Series of textbooks. Vol. 7). GUC Society for Corporate Accounting and Controlling, Chemnitz 2004, ISBN 3-934235-19-0 .
- Hans-Peter Wiendahl: Production control. Logistic mastery of manufacturing processes based on the funnel model. Hanser, Munich et al. 1997, ISBN 3-446-19084-8 .
- Wilmjakob Herlyn: PPS in the automotive industry. Production program planning and control of vehicles and assemblies. Hanser, Munich 2012, ISBN 978-3-446-41370-2 .