High-bay warehouse
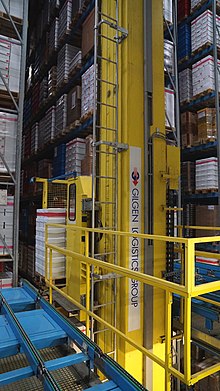
A high bay warehouse (HBW) is a warehouse with shelves from a height of 12 meters, currently the maximum height is approx. 50 meters. The capacity of a high-bay warehouse ranges from a few thousand pallet spaces to several hundred thousands. It is a storage system that uses a lot of space and requires high investments to be made. Most of these systems are managed fully electronically with a warehouse management system. The goods are transported within the warehouse by storage and retrieval machines (SRM). Both flat and long goods can be stored in high-bay warehouses .
High-bay warehouses are mostly built from a steel structure; however, there are also more rarely pure wooden shelves. There are currently six wood high-bay warehouses in Europe (as of March 2015); the highest of them at 30 m in Kleinheubach . The range of design variants for shelving systems is large. There are numerous mixed forms between a fully automatic high-bay warehouse in a silo design and a manually operated racking system, built in a hall. In particular, one only speaks of silo construction when a shelf represents the supporting substructure for the roof and facade.
storage area

Here the goods are stored in the high rack. Between two rows of shelves there is an aisle in which storage and retrieval machines (SRMs) move. B. can only drive in the longitudinal direction of the aisle by rails or induction to store and retrieve goods on the shelves.
The storage and retrieval machines are controlled automatically when picking is carried out in the pre-zone (goods to person). However, they can also be operated manually when picking is carried out directly on the shelf (person to goods). In a warehouse with automatic operation, this part is secured by fences and light barriers for access by people for security reasons.
Each aisle has a storage and retrieval area. There, in an automatically operated high-bay warehouse, the loading units are moved by means of conveyor technology and moved to the loading and unloading points for the forklifts . In the case of manually operated high-bay warehouses, the foremost places on the shelf at the front are designed as transfer places to the forklifts.
Pre-zone
The high-bay warehouse includes a feed or storage area through which the goods are delivered and from which the storage and retrieval machines pick up the goods for storage. Similarly, a retrieval area is required where the storage and retrieval machines deposit the goods after retrieval.
Components of this conveyor technology can be chain conveyors , driven roller conveyors, gravity roller conveyors, lifting tables, turntables, converters, driverless transport vehicles , transfer carriages and vertical conveyors . A special feature of the storage and retrieval machines is a truck shuttle system for each storage level, as is the case in the fully automated compact warehouse.
In automatic order-picking warehouses, order-picking stations are arranged in the front zone. The pallet comes from the high-bay warehouse to the picking station, the goods are removed, booked out and the pallet goes back to the high-bay warehouse.
In the pre-zone, the goods are also identified for the warehouse management system or the material flow computer , this point is called the I point ( identification point ). The goods are provided with automatically readable identifiers , for example with a barcode or smart label , and are managed by the warehouse management system from here until they are booked out.
Administration and control
A high-bay warehouse is managed and controlled by an IT system. The landscape of these systems is very heterogeneous. An ERP system is almost always connected. This often includes a warehouse management system (WMS), which in turn communicates with a material flow computer. The material flow computer controls the conveyor technology in the front zone, the storage and retrieval machines and possibly technology in other trades. In less complex systems, the material flow computer is usually integrated in the warehouse management system.
The IT system coordinates the storage and retrieval of goods according to certain guidelines. The optimization of the software to the individual requirements is largely responsible for the performance of the warehouse.
Storage is often based on the principle of dynamic storage - previously called chaotic storage . Put simply, this means that the system looks for any free space and stores the goods. If necessary, this chaotic principle can be supplemented by rules. For example, one can demand that a material that is present in several containers is distributed over several rows of shelves in such a way that different storage and retrieval machines can outsource the material. This ensures that the material is available even if a storage and retrieval unit fails.
The ABC strategy to increase handling performance is also widespread . The most frequently required articles are stored here in the A area (close to the storage / retrieval location) of the warehouse. In the A area, the travel distances are relatively short and so are the storage / retrieval times. Similarly, the B-area in the middle distance is used for articles that are less frequently used and the C-area in the rear part of the warehouse for articles that are rarely used.
It is also possible to distribute the stored goods as evenly as possible in terms of weight in order to load the shelf structure evenly.
See also
- Parking shelf
- Automatic small parts warehouse
- Distribution center
- Flat goods storage
- Long goods storage
Relevant standards
- FEM 9.222 rules on the acceptance and availability of systems with storage and retrieval machines and other trades
- FEM 9.831 calculation bases for high bay storage and retrieval systems
- FEM 9.832 Calculation bases for SRM small parts stores
- FEM 9.851 Proof of performance for RBG seasons
Web links
Individual evidence
- ↑ pallet high bay warehouse (HRL) ( Memento of 6 June 2011 at the Internet Archive ).
- ^ Mission Accomplished ( Memento of September 29, 2007 in the Internet Archive ). (English)
- ↑ The highest timber racking warehouse in Europe in Kleinheubach . In: Wertheimer Zeitung of December 9, 2010
- ↑ Specialist portal for logistics decision- makers