Whip effect (supply chain management)
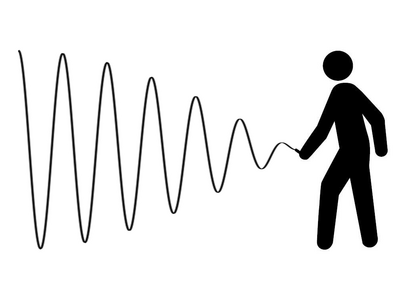
The term whiplash effect (Engl. Bullwhip effect , whiplash effect ) refers to the phenomenon that orders placed with the suppliers tend to be more volatile than sales to the customer and therefore deviate from the demand and that this gap in upstream direction of the supply chain escalates, the fluctuation thus enlarged towards the origin of the supply chain. The term plays a central role in supply chain management as part of risk management , as it highlights the need for integration and coordination along the supply chain.
overview
The whip effect is a central phenomenon in supply chain management that results from dynamic supply chain processes . He describes how the different demand trends and even small changes in end customer demand lead to fluctuations in order quantities, which can build up like a whip along the logistics chain. The example ( beer game ) developed around 1960 at the Massachusetts Institute of Technology (MIT ) takes up this problem in a playful way. Among other things, four causes of the whip effect are identified:
- Processing of demand signals
- Order bundling
- Bottleneck Poker
- Price fluctuations
Causes and consequences
Processing of demand signals
The whip effect occurs as soon as an actor's demand forecast is based on the observed demand. A surge in demand is interpreted as a signal for high future demand and the demand is exaggerated and passed on to the supplier. This distortion is even exacerbated by long delivery times.
Order bundling
Bundle orders mean that orders are placed in larger quantities in order to reduce fixed costs and to use volume discounts or graduated prices. Therefore, periods without an order are followed by periods with a large order quantity. Suppliers encourage these fluctuations by granting volume discounts ( hockey stick phenomenon ). Depending on the forecast method chosen, these outliers in the order amount can in turn lead to incorrect forecasts with regard to future demand.
Bottleneck poker and quantity allocation ( rationing and shortage gaming )
Feared shortages and supply bottlenecks, i.e. irrational behavior in the form of “hamster purchases”, usually also induce buyers to plan the order quantities generously. These surcharges add up to large booms in demand across several stages of the supply chain. However, if the bottleneck does not occur, the companies initially cover their requirements from the inventories created, which in turn leads to an extension of the ordering intervals.
Price fluctuations
Price fluctuations between the individual stages of the supply chain can also lead to fluctuations in order quantities. If, for example, a buyer suspects rising prices, it is to be expected that the current demand will increase and the buyer will build up supplies that are not tailored to the current demand situation. As a result, his demand will be lower in the next periods and the ordering intervals will be longer.
Countermeasures
In most cases, a lack of information flow between the companies involved in the logistical chain leads to the causes mentioned above. Therefore, the countermeasures are aimed at improving the exchange of information. One initiative that aims at this is, for example, Collaborative Planning, Forecasting and Replenishment (CPFR). For example, point-of-sale data is used directly as a source of information by manufacturers. A manufacturer is then not dependent on indirect information through orders from dealers, but can react directly to end customer requests.
In order to cushion the effects of bundled orders on order fluctuations, the operational processes can be designed in such a way that they reduce order fluctuations. For example, in retail, products are delivered on mixed pallets, i.e. different products on the same pallet. This reduces the delivery quantity of the individual product, since not a whole pallet but only part of a pallet is delivered. At the same time, the delivery frequency based on the individual product is increased if mixed pallets are delivered more frequently. The individual branch receives less of a single product per delivery, but the more frequent deliveries mean that the total remains the same. A more frequent delivery has the advantage that it is possible to react more quickly to fluctuations in end customer demand. At the same time, the required safety stock to protect against future fluctuations in demand is lower, and thus also possible fluctuations in orders.
Everyday Low Prices (EDLP) are cited as a counter-strategy to order fluctuations due to price fluctuations, i.e. constant prices. It should be noted, however, that targeted advertising measures, for example, which often include strong price fluctuations, are an important sales instrument. Undesirable effects (customers: inventory purchases, substitution purchases, ... manufacturers: production bottlenecks, fluctuations in sales, ...) can be mitigated by coordinating measures ( efficient promotion ). It should also be noted that the effects of price fluctuations can also occur as a result of price measures taken by the competition, i.e. unchanged own prices are perceived by customers as having changed relative to the competition.
In order to avoid supply bottlenecks due to hamster purchases, in the event of a bottleneck, the scarce products should be allocated based on historical inquiries, for example. This way, no customer has an incentive to place excessive orders. If the customer knows that he is only getting the same as last year, then he cannot influence the quantity delivered by placing orders. If, on the other hand, the customer knows that he is only getting half, he will order twice as much as he needs.
Another method is the supplier-managed inventory (ger .: vendor managed inventory ). The supplier takes care of his customer's inventory.
As a possible way to prevent the bullwhip effect is the concept of cumulative quantities considered, but it must be applied by all partners in the supply chain alike. The required quantities are practically only "passed on" along the supply chain. The required quantities are shifted one after the other from one metering point (logistics) to the next metering point, using the planned or calculated lead time between the metering points as the lead time. The deviations and fluctuations caused by lot sizes are offset against each other via the cumulative determination of requirements for the successive calls, so that the whiplash effect is avoided.
See also
literature
- J. Forrester: Industrial Dynamics. John Wiley & Sons, New York 1961.
- Hau L. Lee, V. Padmanabhan, S. Whang: The Bullwhip Effect in Supply Chains. In: Sloan Management Review. 38 (3), 1997, pp. 93-102.
- W. Herlyn: The Bullwhip Effect in expanded supply chains and the concept of cumulative quantities. In: T. Blecker, W. Kersten, M. Ringle (Eds.): Innovative Methods in Logistics and Supply Chain Management. epubli, Berlin 2014, ISBN 978-3-8442-9878-9 , pp. 513-528.
Web links
- Explanation of the bullwhip effect ( PDF ; 111 kB)
- Explanations of the bullwhip effect
- Explanatory video about the bullwhip effect of the Ruhr University Bochum CC-BY
Individual evidence
- ↑ a b c d e f Hau L. Lee et al: Information Distortion in a Supply Chain: The Bullwhip Effect ( Memento of the original from May 13, 2013 in the Internet Archive ) Info: The archive link was automatically inserted and not yet checked. Please check the original and archive link according to the instructions and then remove this notice. . (PDF; 991 kB). In: Management Science. 43, 4, 1997, pp. 546-558. In the original: “phenomenon where orders to the supplier tend to have larger variance than sales to the buyer (ie demand distortion), and the distortion propagates upstream in an amplified form (i. E., Variance amplification)”.
- ↑ Based on Gerhard Knolmayer , Peter Mertens , Alexander Zeier: Supply Chain Management based on SAP systems: Perspectives on order processing for industrial companies. Springer, Berlin 1999, ISBN 3-540-65512-3 .
- ^ W. Herlyn: The Bullwhip Effect in expanded Supply Chains and the Concept of Cumulative Quantities. 2014, ISBN 978-3-8442-9878-9 , pp. 513-528.