Lane
In mining, a guide rod is a beam on which a cage is guided in the shaft . Guide rails are installed in the shaft in such a way that the bucket is guided either on the front surfaces or on one or two side surfaces.
Basics
If a bucket is moved up or down in the shaft, the rope movement inevitably causes the bucket to move back and forth. In order to minimize these movements, the shafts were provided with a special shaft lining, which was referred to as awning. The lateral shapes and dimensions of the conveying vessels had to correspond to those of the barrel. The toning had to be carried out very precisely so that the delivery bucket did not get stuck anywhere. Shafts that were equipped in this way could only be used to a limited extent as weather shafts. Another form of shaft guidance was the guidance of the conveying vessels on iron rails (guardrails) or square pieces of wood, which were called a guide tree or guide rod. The guide trees were usually made of square timber four inches thick . Good, non-bending oak was used as the wood. The guide trees were very firmly connected to the shaft timbering.
material
Track battens can be made of wood or steel. Up until the first half of the 20th century, the laths in Saigeren shafts were made exclusively of wood. The reason for this was that up to this point in time there were frequent breaks in the hauling ropes and the safety devices of that time were only suitable for wooden guide rails.
Wood
Wood types with high wear and flexural strength are suitable for wooden track battens. It is also important that the timbers are available in great lengths of five to twelve meters. Great lengths are required to keep the number of butt joints low. The wood of the American pitch pine , which is a hard, resin-rich and elastic pine, is particularly suitable for wooden laths . But also oak or the wood of the Australian eucalyptus tree Jarrah is used. This wood has the advantage over oak that it has grown straighter, contains fewer branches and has longer trunks. Several laths can also be cut from the trunk of the Jarrah wood, which is not feasible with other types of wood. The reason for this is that when cutting the guide stick with all other types of wood, the heartwood must come into the center of the cross-section of the guide stick. This is necessary so that the guide bar does not twist. Track battens made from laminated wood are also used. These woods have the advantage that they are more abrasion-resistant than guide battens made from heartwood. The requirements that are placed on wooden track battens are regulated in DIN 21341.
Steel laths
Steel track slats are made from profile steel. For this purpose, two identical U-irons are welded on the sides with a plate made of flat iron. Steel track battens have the advantage over wooden track battens that they are resistant to breakage and wear. This practically eliminates the possibility of guide rails breaking. Steel laths also require fewer repairs. Shafts in which steel laths are used cannot spread a fire, nor can a fire develop in these shafts. Since steel guide rails do not swell or shrink, they can also be installed with lower tolerances. However, guide rails in shafts that are exposed to high rock pressure have the disadvantage that the conveyor cage is exposed to hard impacts due to the displacement of the guide rails due to the rock pressure . This disadvantage can be compensated for with adjustable fastenings.
Attachment
Track battens are attached to the grooves in the shaft . These lines are firmly connected to the shaft lining at intervals of a maximum of three meters for wooden laths and a maximum of 4.5 meters for steel laths. The strokes can be made of wood or steel. In the case of steel laths, the lines must also be made of steel if the distance between the lines is greater than 4.5 meters. In the case of wooden laths, they are attached to the grooves with threaded screws. To prevent the guide shoes from getting stuck, the heads of the threaded screws are embedded several centimeters into the crossbar. There are also special guide rail shoes to connect the guide rails to the screeds. The guide lath shoe is screwed to the single line with two screws each. The guide shoes distribute the load in the wood over a larger area. In the case of steel guide rails, special guide rails are used that are tailored to the guide rail profile. The guide rail is grasped from the outside by side stop bars and attached to the screed from the inside with special clamping pieces and high-strength screws. With this connection, the fastening takes place due to the frictional forces, so the guide rails can be positioned more precisely in the vertical direction during assembly. These connections are always placed on a single line or console so that the guide rails do not move at the connection points between two guide rails under the lateral pressure of the guide shoes or guide rollers of the conveyor cage moving past. Each guide rod, with the exception of the folding guide rods or the guide rod end pieces, must be attached to at least three grooves or consoles.
wear
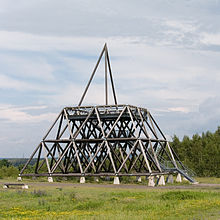
Track slats wear out during operation due to the friction of the guide shoes. Wear is reduced by a special guide rail grease. This grease is applied in liquid form to the dry guide rails and prevents dry friction between the guide shoes. But steel laths are also subject to a certain amount of wear. If guide rails are weakened by a certain amount in cross-section, they must be replaced for safety reasons. In the case of steel track battens, the maximum permissible wear is less than six millimeters. In the case of wooden track battens, wear on the flanks may not exceed 15 millimeters per flank and on the front side a maximum of ten millimeters. The exact wear and tear of each guide rod is determined with a guide rod tester.
Individual evidence
- ^ Walter Bischoff , Heinz Bramann, Westfälische Berggewerkschaftskasse Bochum: The small mining dictionary. 7th edition, Verlag Glückauf GmbH, Essen, 1988, ISBN 3-7739-0501-7 .
- ↑ a b c d e Technical requirements for shaft and inclined conveyor systems (TAS). Verlag Hermann Bellmann, Dortmund 2005.
- ^ A b Heinrich Veith: German mountain dictionary with evidence. Published by Wilhelm Gottlieb Korn, Breslau 1871.
- ^ A b Franz Rziha: Textbook of the entire art of tunneling. First volume, published by Ernst & Korn, Berlin 1867.
- ↑ Winfried Sindern, Olivier Gronau: Steel wire ropes - proven service providers of shaft hoisting systems. In: Ring Deutscher Bergingenieure eV (Hrsg.): Mining. Volume 61, No. 4, Makossa Druck und Medien GmbH, Gelsenkirchen April 2010, ISSN 0342-5681 , pp. 155-164.
- ^ A b c d e Carl Hellmut Fritzsche: Textbook of mining science. First volume, 10th edition, Springer Verlag, Berlin / Göttingen / Heidelberg 1961.