Composite armor
A composite armor is armor that consists of different layers of materials. It is intended to ensure the greatest possible protection against various forms of attack with armor-piercing ammunition . These include shaped charge and impact projectiles , squeeze head ammunition and anti-tank mines . To this end, various materials are incorporated into the composite armor. The composite armor was used for the first time on the Soviet T-64 main battle tank .
Basics
The development of shaped charge projectiles and missiles after 1942 posed an enormous threat to tanks, as they could penetrate steel armor of thicknesses that made it impractical to build a tank that was safe against it. This was particularly evident during the Yom Kippur War , when many Israeli tanks were destroyed by Soviet anti-tank guided missiles . This also led to an accelerated development of composite armor on the west side, which was first used in the following generation of battle tanks ( Leopard 2 , M1 Abrams , Challenger 1 ).
The aim of composite armor is to achieve the required level of protection by combining a wide variety of materials, the weight of such an arrangement being considerably less than the weight of armor made of homogeneous armor steel with the same protection. The protective effect of composite armor is specified in RHA , this corresponds to the level of protection of an armored steel plate with this same thickness. The effectiveness of composite armor is indicated with two values:
- TE (thickness effectiveness): RHA equivalent of armor compared to its thickness
- E M (mass efficiency): Index number for the mass-related (protective) efficiency of armor compared to armor steel, higher values mean better protective effect
A wrought aluminum alloy of the Al-5XXX type, for example, has a TE of 0.6. A 100 mm thick aluminum plate therefore has a protection level of 60 mm armor steel. To achieve a protective effect of 100 mm RHA, 166.66 mm aluminum would be necessary:
An aluminum alloy has only 34.6% the density of a steel alloy. The E M value of the aluminum alloy is therefore:
By nature and by definition, armor steel has TE = 1 and E M = 1. This calculation is a greatly simplified example, as composite armor reacts differently to different threats (hollow charge, hard core bullet, APFSDS). The E M values of a titanium alloy under APFSDS bombardment vary, for example, from 1.44 to 1.9, depending on the penetrator material, length / diameter ratio and speed.
Armor steel
RHA
Rolled armor steel ( rolled homogeneous armor ), improved in the mechanical properties of tensile strength and hardness compared to structural steel through heat treatment and rolling , was first used in World War II. Later, new alloys were developed to increase toughness ( ductility , for high elongation at break ) while still having high hardness (up to 300 Brinell ). This is achieved through alloy components such as manganese, molybdenum, vanadium, chromium, nickel or the inclusion of carbon cementite and nitrogen. Armored steel has been the basis of armored vehicles until recently because it is easy and cheap to manufacture and process compared to other materials.
Armored steel structures can be welded as well as cast from rolled steel, with rolled steel having a tensile strength that is around a tenth higher than cast steel.
HHA
Hardened steel plate ( high-hardness armor ). Due to the higher hardness, which is sometimes over 600 HB, the material can no longer be used for load-bearing structures because it is too brittle. Since steel cannot be hardened with plates of any thickness, several thin plates are often hardened and placed on top of one another. The TE of hardened steel can be up to 1.6. One application example is the Leopard 1 A3. Modern armor steels combine hardened surface layers and tough base layers (e.g. Hardox ).
Perforated armor
With perforated armor, small holes are drilled in steel plates. Ideally, the diameter should be less than or equal to the anticipated threat. The panels are then hardened so that the inner wall of the holes also benefits. When installing, several panels can be stacked one behind the other, the hole patterns should alternate in order to achieve “mini spaced armor ”. Ideally, the holes should be drilled at an angle in order to set impacting projectiles in rotation through the hard inner walls; alternatively, the plate can also be inclined, as shown in the picture on the right. The protective effect of perforated armor corresponds roughly to an armored steel plate of the same thickness, but the weight is up to 50% less due to the holes. Thus TE≈1 and E M ≈2 can be estimated.
Light metals
Magnesium alloys
Magnesium alloys are the lightest metals for armor construction. Thanks to the processing options, armored hulls and other supporting structural parts made of magnesium are also possible.
The AZ31B alloy is, for example, less weight than an Al-5XXX aluminum alloy when fired from machine guns and cannons, but performs worse than a steel plate of the same weight. This magnesium alloy is only more effective than rolled homogeneous armor steel (RHA) against splinters. Magnesium is not used in modern tanks, since glass fiber reinforced plastic has roughly the same properties, but has a slightly lower density.
Aluminum alloys
Aluminum alloys are used more often in armor construction. Aluminum makes it possible to design load-bearing structural parts that are not important for armor protection, such as rollers, to be lighter. Wrought aluminum alloys from the Al-7XXX group are generally used for armor elements , but cold-rolled aluminum-magnesium alloys such as those in the M113 are also used. The use of aluminum-lithium alloys is still in the test phase. The ballistic properties are slightly better (in terms of weight) than armor steel, but it drives up costs and takes up more space. That is why aluminum alloys cannot completely replace armor steel as a construction material.
Armor made of aluminum alloys is used where weight plays an important role. A frequent use is found in armored personnel carriers and light battle tanks such as the M8 Armored Gun System , heavy battle tanks were only experimentally built with aluminum (e.g. MBT-80). Aluminum was used as part of the composite armor in the T-80 and rumored to be used in the Leopard 2 .
Titanium alloys
The idea is to use high-strength titanium alloys such as Ti-6Al-4V, which have roughly the same strength characteristics as armor steel. Since the bullet resistance (TE, thickness effectiveness) corresponds to 80-90% that of armor steel (at only 57% of the weight), one has a very effective armor material that can also be used for load-bearing structural parts. However, due to the complicated manufacturing process, titanium is ten times more expensive than conventional steel.
Titanium alloys are therefore only used as special armor; their use as a construction material is limited. The commander's hatch on the M2 Bradley is made of a titanium alloy; For the M1 Abrams, among other things, the blow-out panels, the engine cover and the commander's hatch were manufactured from titanium. Titanium is used as part of the composite armor in the Leclerc and VBCI .
Ceramic armor
Ceramic materials have a high degree of hardness and compressive strength, but in contrast to metals, they are rather brittle. In contrast to metals, which behave like fluids at high pressures (that is, the projectile "floats" through the armor like a submarine through water), ceramic reacts by cracking. Fragments of the ceramic penetrate into the metal spike of a shaped charge or into a penetrator, thereby expanding it or are compressed in front of the spike and inhibit progress far more effectively than armor steel can. Composite armor made of ceramic is used almost everywhere today, from bullet-resistant vests to tanks. The E M value of ceramic armor can be above 4. Al 2 O 3 , SiC and B 4 C are often used for this . The thickness of the ceramic plates can range from a few millimeters to a few centimeters.
First generation
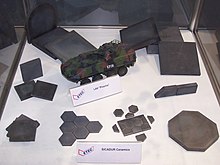
The first composite armor with ceramic consisted of a plate of hard material such as borosilicate glass or metal matrix composites , which was stuck in a sandwich of steel or aluminum plates. The well-known Burlington is, for example, a sandwich honeycomb core composite , in which the outer skin consists of aluminum oxide ceramic tiles in honeycomb shape, which are glued to a matrix of ballistic nylon. A reproducible production of each individual ceramic plate and compliance with very tight tolerances are important. Close installation is only possible if this requirement is met. Any joint larger than 0.3 mm represents a weak point in bullet resistance. Armouring that is constructed in this way has no weight advantage over armor steel when it has to protect against bullets. However, due to its weight advantage and relative simplicity, this design remains the first choice for other applications. Boron carbide ceramics are glued to Dyneema fabric in the UH-60 and some body armor , while steel and silicon carbide are used in the Piranha armor .
Second generation
In the course of armor development, it was recognized that the protective effect of the ceramic against impact projectiles can be significantly improved if it is prevented from splintering. To do this, the ceramic must be held in shape by three axes. The realization of this requirement is complex - adhesive is ruled out here. The ceramics can be used in blind holes in a steel, aluminum or titanium plate; the openings are then plugged and welded shut. The sintering of the metallic matrix around the ceramics is possible as well as the pressing in the still liquid melt or overmolding of the ceramics with liquid metal. The material that contains the ceramics should be as hard and stiff as possible. If armor steel is used for this, it can also be hardened. This is followed by a thick layer of fiber composite material , usually made of aramid or glass fibers . The original Chobham armor was built according to this principle.
Third generation
In further investigations it turned out that the effectiveness of ceramic armor can be further increased if the ceramic-containing layer is provided with a further back plate (support layer). This has the task of keeping the first layer in shape so that it is not stressed by high bending moments when it is hit . Fiber composite materials are too soft for that. When penetrating through the ceramic, there is also the problem that the fiber composite layer forms a “crater”, which can damage adjacent ceramics that are glued on and a larger area is affected by the impact. Modern structures therefore have three layers.
The most effective - also against impact projectiles - is an intermediate layer made of a hard and dense material. Because even with materials not an ideal material exists for this purpose, a high effort is required again. In order to obtain a hard and at the same time dense material, blind holes can be drilled in a steel or nickel plate and a heavy material can be filled in, as with the ceramic-containing layer . The plate can still be hardened after welding. Depleted uranium (density: 19.2 g / cm³) and tungsten (density: 19.25 g / cm³) alone are too soft for this. The armor of the Challenger 2 is said to contain uranium dioxide nuggets and rubber , for example . The structure with a heavy metal layer is also known as Dorchester armor.
If protection against impact projectiles is less important, the intermediate layer can be constructed from a stiff and light material. A laminate made of fiber composite panels and sheet metal can be used for this, for example. A balsa wood panel can be used instead. When metal foams (mostly made of aluminum) are used, the foams are made in blocks the size of the ceramic and glued to them to improve multi-hit ability and energy absorption. This armor was used in the Composite Armored Vehicle (CAV). The Japanese Type 10 main battle tank is said to use carbon fiber reinforced plastic for this purpose. Behind the intermediate layer, there is also a thick layer of aramid , glass fiber reinforced plastic or Dyneema fabric .
Reactive armor

The reactive armor (explosive reactive armor (ERA)) is placed on the armor in the form of tiles. It consists of a layer of explosives, which in turn is covered with a plate. If the cover plate is punctured, the layer of explosive explodes and hurls the plate towards the projectile. For a good protective effect, it is important that the tiles are separated from one another so that only the tiles directly affected explode when bombarded. Classic reactive armor is largely ineffective against tandem shaped charges .
First generation
The first reactive armor used only cover plates with low mechanical strength, mostly thin steel plates (see right). Shaped charges, in particular, can be fended off well because the cumulative jet is swirled. Classic reactive armor is largely ineffective against mass bullets .
Second generation
Further developments use a more stable cover plate several centimeters thick. Versions known as heavy reactive armor such as Kontakt-5 can also reduce the penetration capacity of APFSDS ammunition by causing the penetrator to rotate.
Third generation
The latest reactive armor is integral, i.e. integrated into the composite armor. This means that shaped charges and machine gun fire can be repelled better. One example of this is cactus reactive armor. Since an exploding layer needs a kind of “blow-out opening”, reactive arrangements have also been developed that work without explosives. These structures, known as NERA (Non-explosive reactive armor), use an intermediate layer made of an inert material, for example rubber , which deforms the panels if they are hit. The effect is not quite as high as with the explosive version, but tandem shaped charges can also be influenced.
Spaced armor
A spaced armor consists of several plates that are arranged one behind the other with an air gap in between. The principle is based on the fact that the shaped charge spike is optimized for a certain distance, behind which the penetration performance decreases. The penetration power of an RPG-7 is optimally 330 mm, after 610 mm from the detonation point it is only 127 mm RHA. It therefore makes sense to increase the overall depth of the armor in order to be able to repel shaped charges better. Spaced armor renders squeeze-head ammunition ineffective and protects the ceramic armor better against fire from machine weapons and HE shells.
First generation
Initially, thin steel plates were attached to the armor with fixed spacers. In the integrated version, cavities are left in the armor, an example of this is the battle tank 70 . The most visible application is side skirts .
Second generation
Improved versions use a shock-absorbing attachment of the bulkhead assembly that attaches to the base armor. The rubber elements are called "shock mounts". The structure reduces the loads that are transferred to the basic armor in the event of a projectile impact. In the integrated version, cavities are left in the armor; these are filled with a low density material such as polyurethane , polyethylene and polystyrene . The front plates can thus be supported on the rear ones, this reduces the bending moments . The first versions of the T-72 used polyurethane in the tub front. A bulkhead arrangement with polystyrene is said to have been used in the Leopard series.
Third generation
Further improvements are based on the partially shock-absorbing arrangement, for example of a sandwich consisting of two steel plates with rubber filling, in order to additionally benefit from the NERA effect. Alternatively, ceramic-containing layers or HHA are also conceivable. The cactus ERA and Kontakt-5 also form a bulkhead arrangement. Inclined arrangements can cause bullets to rotate when penetrating through and thus reduce their penetration performance.
Fiber reinforced plastics
Composite materials such as GRP or CFRP have a low density, good insulation properties against heat ( napalm ) and noise and are therefore suitable for the chassis of a tank in addition to layer material . Further advantages are the elimination of the spall liner, which is only necessary for metal and consists of a thin layer of aramid or dyneema inside the vehicle to reduce the splinter cone. The elimination of parasitic mass is also an advantage; Parasitic mass is the name given to the use of heavy armor material in places with low protection requirements. This advantage can be used to use thicker armor in other, more vulnerable areas. Developments for this took place in the USA under the Composite Armored Vehicle Program (CAV) and in Great Britain under the ACAVP (advanced composite armored vehicle program) from QinetiQ , where an armored personnel carrier with a hull was made from GRP. Due to the fact that it is almost twice as high as an aluminum vehicle, the concept has not yet caught on.
See also
- AMAP
- Chobham armor
- Metal matrix composite
- Mexas
- Technical ceramics
- Shatter layer - application of the functional principle in fortress construction
literature
- Paul J. Hazell: Modern Armor Material and Systems. Cranfield University, Shrivenham, Oxfordshire.
- Rolf Hilmes: Main battle tanks today and tomorrow: Concepts - Systems - Technologies. Motorbuchverlag, Stuttgart 2007, ISBN 978-3-613-02793-0 .
Individual evidence
- ↑ http://www.dtic.mil/cgi-bin/GetTRDoc?AD=ADA392783&Location=U2&doc=GetTRDoc.pdf
- ↑ A Ballistic Evaluation of Ti-6Al-4V vs. Long Rod Penetrators ( Memento from June 21, 2016 in the Internet Archive )
- ↑ Scribd.com Armor Basics (English)
- ↑ Gun vs Armor: Cast Armor ( Memento from August 22, 2010 in the Internet Archive ) (English)
- ↑ http://www.arl.army.mil/arlreports/2007/ARL-TR-4077.pdf
- ↑ K. Sampath: Welding aluminum armor ( Memento from May 4, 2017 in the Internet Archive ), ADVANCED MATERIALS & PROCESSES / OCTOBER 2005
- ↑ http://www.tms.org/pubs/journals/JOM/9705/Montgomery-9705.html
- ↑ Archive link ( Memento from October 8, 2011 in the Internet Archive )
- ↑ W. Kolkowitz, TS Stanislaw: extrusion and Hot Rolling - Two Advanced Fabrication Techniques for the Preparation of whisker-metal composites. Proceedings of the 14th National Symposium and Exhibit, Vol. 14 - Advanced Techniques for Material Investigation and Fabrication, 5-7 Nov 68, Cocoa Beach, Florida, Paper No. 11-4A-3
- ^ D. Long: Modern Ballistic Armor - Clothing, Bomb Blankets, Shields, Vehicle Protection. Boulder 1986, pp. 82-84.
- ↑ ALOTEC ALUMINUM OXIDE CERAMICS FOR PERSONAL AND OBJECT PROTECTION (PDF file; 336 kB)
- ^ Henry S. Chu, Kevin M. McHugh, Thomas M. Lillo: Manufacturing Encapsulated Ceramic Armor System Using Spray Forming Technology. Publications Idaho National Engineering and Environmental Laboratory, Idaho Falls 2001.
- ↑ Patent US4836084 : Armor plate composite with ceramic impact layer. Filed February 20, 1987 , published June 6, 1989 , applicant: Akzo NV, inventor: Laurens B. Vogelesang, Marcel LCE Verbruggen, Cornelis G. Paalvast.
- ↑ Patent EP0826134 : Multi-layer armor protection material. Registered on March 14, 1996 , published on December 22, 1999 , inventor: Gerd Kellner.
- ↑ RPG-7 Manual of the United States Army Training and Doctrine Command , November 1976
- ↑ G. van Zelm, BA Fonck: Leopard-1 Gevechtstank. De Tank, June 1991, p. 53.