BBS (brand)
BBS | |
---|---|
![]()
|
|
Owner / user | BBS GmbH, BBS Motorsport GmbH, BBS-Washi Wheels GmbH |
Introductory year | 1970 |
Products | Alloy wheels |
Markets | Automobile, motorsport |
Website | http://www.bbs.com/ |
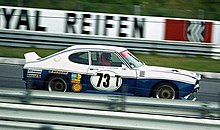
BBS is a brand of light alloy wheels for passenger cars and motorsport . The original company was founded in Schiltach in the Black Forest in 1970 and, after an eventful history, is now divided into three companies. The BBS GmbH provides wheels for cars ago, the BBS Motorsport GmbH produces wheels for motorsports and the BBS Japan Co. Ltd. high quality forged wheels.
BBS has been owned by the Korean NICE GROUP since 2015 .
history
In 1970 Heinrich Baumgartner and Klaus Brand founded the company BBS in Schiltach in the Black Forest. The name emerged as a short form for Baumgartner, Brand, Schiltach. Initially, body parts made of plastic were manufactured in the company until a new, three-part motorsport bike was designed in 1972. This was based on an idea from Martin Braungart , the lead racing engineer of the Ford Capri touring car factory team , in order to be able to quickly vary the rim width and offset on the race track . In addition, different materials (aluminum, magnesium ) and manufacturing processes appropriate to the demands ( drop forging and rolling for aluminum materials, casting of magnesium alloys) can be optimally combined with one another. From then on, the company was strongly represented in motorsport. The company continued to develop. Shortly afterwards, the first foreign subsidiary was founded in France, the three-part wheels were introduced for the retrofitting business and achieved large sales on the aftermarket . As a result of these positive developments, BBS went public in 1987, trading as BBS Motor Vehicle Technology AG. After three more years, the subsidiaries in Japan and the USA were founded, as well as a branch in Italy.
The company celebrated its 25th anniversary in 1995, when Michael Schumacher and Benetton Renault won the Formula 1 World Championship on BBS bikes for the second time. Numerous other successes in motorsport on BBS bikes followed. In addition, the retrofit market was revolutionized this year with the two-part RS wheel, which is today a design classic around the world.
As the company expanded at the Schiltach location, the paint shop and logistics center in Herbolzheim was opened on 7000 m 2 in 2000/01 . The conveniently located location with connection to the A5 enables fast shipping worldwide. In February 2007, BBS Motor Vehicle Technology AG had to file for insolvency. The company management stated that one would have to cope with a large drop in profits due to the sharp rise in aluminum prices. In the meantime, production continued. The company was bought up by the Belgian company Punch International NV and continued as BBS International GmbH. In July 2009, the Punch International holding parted with large parts of its automotive division “because of the effects of the financial crisis” and sold BBS to the Punch majority shareholder, Creacorp NV.
On December 30, 2010, bankruptcy had to be filed again. The reason given was that BBS can be split cleanly in this way. In the course of this insolvency, the motorsport sector (BBS Motorsport GmbH) and the forged wheel area (BBS Washi Wheels GmbH) were sold to the Japanese ONO group, which has relocated their new company headquarters with the associated production facility to Haslach im Kinzigtal. About 40 people are employed there. On April 1, 2012, Tyrol Equity AG (Innsbruck) joined forces with co-investor Udo Wendland in the newly renamed BBS GmbH.
In June 2015, the majority stake in BBS GmbH was taken over by NICE Holdings Co., a Korean listed industrial group. It has committed itself to supporting the implementation of the BBS growth strategy.
In July 2020, BBS had to file for bankruptcy again in the wake of the automotive crisis.
technology
In order to develop a durable light alloy wheel, numerous computer-aided design steps are carried out at BBS before the wheels are first cast. Each type of wheel is modeled three-dimensionally using the CAD software and goes through various FEM analyzes. With the finite element method , the properties of a type of wheel with regard to its structural behavior, e.g. B. Fatigue strength and dynamics, determined and optimized. This analysis can be used to simulate how a type of bike will behave under real operating conditions and loads. A failure mode and effects analysis ( FMEA ) is already carried out in the development phase . Each new type of wheel is then simulated in order to achieve a high, stable casting quality later on during casting. The mold and flow-forming tools are manufactured under our own management, internally or externally.
Aluminum , silicon , strontium and other components are heated and melted in melting furnaces to over 750 degrees. After the quality of the alloy has been checked, the liquid material is made available for casting. BBS uses the low-pressure chill casting process to manufacture a cast blank . The manufactured aluminum alloy is pressed into the multi-part mold with a pressure of up to 1.2 bar. After cooling to below 400 ° C, the mold is opened so that the cast blank is ready for further processing. In order to rule out the possibility of air being trapped in the blank during casting or surface defects, all wheels are subjected to an X-ray test and defective wheels are sorted out. In the next production step, the wheels of the Performance Line are machined using the flow-forming process . Here, the cast blank produced using the low-pressure casting process is heated and the rim is rolled out under high pressure. The rim base becomes thinner, the material is compressed and the strength is increased. As a result, the bike is more stable and lighter.
In addition, there is a special heat treatment that all BBS wheels undergo. The material can form a closer bond and tensions are minimized. This guarantees a consistently high level of strength and achieves a long service life for the wheels. The finishing touches are done by fully automatic CNC milling and turning machines. The precise mechanical processing achieves a high level of concentricity and low imbalance. Some wheels are also reduced in weight by back-milling the spokes. With back milling, the optimal ratio between weight and stability is achieved. A special CNC milling process is used to remove parts of the wheel spoke that are on the side, which are insignificant for strength, in order to reduce the rotating mass of the wheel.
Furthermore, the wheels can be optimized using the "Air Inside Technology". With this method, hollow chambers are created in the wheels, for example in the spokes or in the inner and outer shoulder. With this construction based on the hollow chamber principle, the rotating masses are extremely reduced. At the same time, the stability and load capacity of the bike are improved.
BBS achieves the special shine of the wheels by manufacturing the alloys in-house. Furthermore, a three-layer coating makes the surface more resistant. BBS uses ceramic polishing for the highest brilliance of the rim. The wheel is polished in several processing steps with small ceramic particles. For a special finish, some wheels at BBS are diamond turned, exposing the surface down to the aluminum, creating a special, two-tone look. To protect against corrosion, each wheel is finally given a chemically chrome-free passivation layer and an environmentally friendly three-layer coating (primer powder, water-based paint and acrylic powder). In addition, BBS developed a collision protection for rims, which protects the wheel from damage (e.g. collision with the curb). The customer can replace this collision protection himself. All 100% tests (such as X-ray, unbalance, leak tightness and three visual assessments) are documented on each wheel. For approval, each new type of bike is tested for structural strength and fatigue strength on various test stands. The material and the surface treatment are also tested in the laboratory according to various specifications and then approved. Requalification tests from the series are carried out at regular intervals.
design
Two years after the company was founded, the first three-part racing car wheels were produced, which were developed in order to be able to quickly vary the rim width and offset on the racetrack.
In the 1970s, the company gained a special reputation in the manufacture of light alloy wheels with cross-spokes, which are characterized by a very high number of spokes: the RS wheel. It was in production for road and racing vehicles until the mid-1980s.
Since the late 1980s, wheels with Y-spokes have been introduced in many variants instead of cross-spokes, initially with seven spokes.
In addition, BBS manufactures wheels with 5 and 10 Y-spokes that are tailored to specific vehicles depending on the wheel, such as the SV wheel, which was initially developed for SUVs. The newly developed XA falls outside the framework of the previously known BBS design.
Awards
In 2008 BBS won the rims category in the readers' choice of sport auto magazine . BBS was also ahead in the 2013 elections for AutoBild and auto motor und sport .
Web links
Individual evidence
- ↑ Tyrol Equity gives BBS to Koreans . In: Tiroler Tageszeitung Online . June 3, 2015 ( tt.com ).
- ↑ 40 years of Capri: Fast ring lap and review of racing history - Oldtimer-Markt 12/2009, p. 16
- ↑ "Bank and stock exchange - barriers for newcomers" ( Time on June 26, 1987)
- ↑ Japanese Ono Group takes on insolvent Radbauer BBS . December 15, 2011 ( platow.de ).
- ↑ BBS has filed for bankruptcy, Reifenpresse.de from July 16, 2020
Coordinates: 48 ° 15 ′ 59.5 ″ N , 8 ° 22 ′ 0 ″ E