Drill bit
Drill bits are tools used in deep boreholes or tunnel bores in order to drive the drill string through rock formations and to develop underground storage facilities or traffic routes . Driven by the rotation of the drill string or the underground drill motor, they break up the rock, which in the directional drilling process is transported above ground by a drilling fluid or compressed air . For this purpose, drill bits have nozzles , from which the drilling fluid or compressed air exits at high speed and high pressure in the direct drilling process , or a central opening through which the drilling fluid together with the removed cuttings reaches the drill pipe and thus upwards in the indirect drilling process .
There are several different drill bits for the various drilling methods, which are adapted to the properties and drillability of the subsoil to be drilled.
Chisel types for deep drilling
The direct drilling method is used for deep drilling .
Fishtail chisel

The fishtail chisel, which is no longer used today and is made from a flat steel blade, takes its name from the cutting edge that is split in the middle like a fishtail, one part of which is bent forward and the other backward . The drilling fluid emerges from an opening. It was used in soft formations and its shape has a cutting effect on the rock to be drilled.
Roller chisel
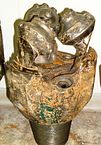
The roller chisel was invented by Howard Robard Hughes Sr. in 1909.
A roller bit usually has three movable rollers. Rows of teeth are milled out of them as cutting elements for softer rock or they are fitted with hard metal pins (warts) for harder rock . The rock is removed by the pressure of the rotating rollers, whereby the local compressive strength of the rock is exceeded and rock particles are broken out of the bond. The nozzles from which the drilling fluid emerges are located between the rollers on the bit body.
Diamond chisel
Diamond chisels have been used since the 1950s. Natural or artificial diamonds are used as cutting elements . In contrast to roller chisels, diamond chisels have no moving parts.
In the case of a diamond chisel with a surface , diamonds are sintered onto the chisel surface , which destroy the stone by cutting.
In an impregnated diamond chisel , diamond fragments are worked into a matrix , a body made from tungsten carbide powder. During drilling , this matrix wears out, allowing new diamond fragments to emerge, which can then work on the rock. This type of chisel is used for very hard, abrasive rock. Here, the rock to be drilled is ground or sanded down.
In the middle of this bit there is one or more nozzles from which the drilling fluid emerges.
PDC chisel
Polycrystalline Diamond Compact (PDC) chisels were used in oil and gas exploration in the North Sea from 1976 and are now used worldwide.
PDC chisels also have no moving parts. They have several ribs, also called wings, in which polycrystalline diamond plates are embedded as cutting elements . The rock is removed by peeling- cutting or splintering-shearing, with the cutting edges plowing into the surface of the rock. The nozzles from which the drilling fluid emerges are located between the ribs.
Hybrid chisel
Hybrid chisels, a combination of roller and PDC chisels, have been used for some time.
Chisel types for shallow and well drilling
The indirect drilling method is often used for shallow and well drilling .
Eccentric roller bits
The eccentric roller bit has strip-like cutting blades on the drill head, which dig into the loose rock without the rock being destroyed. The shaft is slightly curved and connected to the drill head by ball bearings. The inlet opening for the drilling fluid is in the middle.
Large hole roller chisel
Large-hole roller bits are heavy, circular drill heads equipped with several chisel rollers, also stepped in several levels. These are used for harder rock or heavily consolidated loose rock. The inlet opening for the drilling fluid is in the middle.
Wing chisel
Wing chisels have carbide-tempered cutting blades on their (often three) wings, with which it can dig well into cohesive loose sediments such as clay or silt . For an improved penetration into the cohesive soil layers, these bits are provided with a point at the lower end in front of the inlet opening for the drilling fluid.
Impact drill bit

In the percussion drilling process , a drill bit is hit on the bottom of the borehole by moving the drill string up and down, thereby breaking up the rock. A special rotary percussion process is down-the- hole hammer drilling , in which the percussion drive is located in the borehole, directly above the bit, so that no energy is lost in the drill string. The compressed air or water operated percussion piston lets the chisel hit the bottom of the borehole up to 3000 times per minute. The compressed air or water used as drive energy exits through nozzles in the chisel and cleans the borehole.
Drill bits
A ring drill bit is used to extract a core . These are available in the deep drilling area as roller chisels, PDC chisels or diamond chisels. In contrast to drill bits, drill bits do not destroy the entire volume of rock given by the tool diameter, but only an annular area and create the cylindrical drill core through a round recess in the center. This is picked up above the drill bit and can be brought to the surface by removing the drill rod or by pulling the core pipe using a steel cable.
See also: core hole drilling , drill bit
- Drill bit as heraldic symbol
Nienhagen (district of Celle) in Lower Saxony
Ampfing in Bavaria
Puchkirchen am Trattberg in Upper Austria
Web links
- Deep geothermal drilling in the crystalline. Prof. Dr.-Ing. Matthias Reich, Institute for Drilling Technology and Fluid Mining, TU Bergakademie Freiberg; Dipl.-Ing. Bernhard Prevedel, Scientific Drilling, GFZ Potsdam. Conference "Deep Geothermal Energy Saxony", November 24, 2011, Dresden , PDF 1.95 MB; accessed on February 21, 2020
- Information brochure from Comdrill on core drilling methods for deep drilling in geology, accessed in February 2016
Individual evidence
- ↑ Elektrotechnische Zeitschrift: Beihefte, Volume 64, Issues 1–6, VDE Verlag 1943, p. 147.
- ↑ Roller chisel patent
- ↑ Martin Kaltschmitt, Ernst Huenges, Helmut Wolff: Energy from geothermal energy. German Verl. For basic industry, Stuttgart 1999, ISBN 3-342-00685-4 , p. 116.
- ^ Heinrich-Otto Buja: Handbook of deep, shallow, geothermal and horizontal drilling technology. Vieweg & Teubner, Wiesbaden 2011, ISBN 978-3-8348-1278-0 , p. 439.
- ^ Baker Hughes - Kymera Hybrid Drill Bit Technology
- ^ Lower Saxony State Office for Ecology, Lower Saxony State Office for Soil Research: Materials for the Lower Saxony Contaminated Site Manual - Geological Exploration Methods . Springer, Heidelberg 1997, ISBN 978-3-642-64386-6 , p. 111.
- ^ Ingrid Stober, Kurt Bucher: Geothermie . Springer, Heidelberg 2012, ISBN 978-3-642-24331-8 , p. 91.