Tunnel boring machine
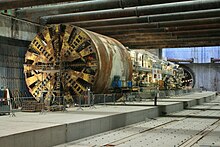
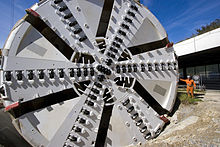
A tunnel boring machine ( TBM ) is a machine that is used to build tunnels . It is particularly suitable for hard rock . Such large machines are also used in tunnel construction in loose rock, which is unsuitable for driving by means of blasting technology . Tunnel boring machines belong together with the shield machines (SM) to the tunnel boring machines ( TBM ).
Structure and types
The most important part of a TBM is the drill head ; it has a diameter of up to 20 meters and consists of a chisel carrier with rotating roller bits that transports the broken rock backwards. The device in the rear part of the drill head has a length of up to 200 meters with auxiliary devices for large diameters.
Tunnel boring machines are full headers , which means that, unlike partial headers , they cut the entire tunnel cross-section in one work step.
Such machines are usually supported by conveyor belts to quickly remove the overburden that occurs during work, or they carry a construction train with them, for example to bring precast concrete parts for the tunnel to be built afterwards to the similarly tracking tunnel lining machine - shotcrete is also possible , which can be brought in via conveyor belts or concrete mixer trucks and brought to the tunnel walls on site.
Components of a tunnel boring machine
- Dismantling shield with roller chisels, feed and tensioning devices
- Facilities for the installation of support and expansion measures
- Equipment for material removal (shear systems)
- Supply unit for electricity and compressed air to operate the roller bits, as well as ventilation, and water to cool the bits
- Transport equipment for excavated material, proppants and finishing materials
Classification of tunnel boring machines
One subdivides into open tunnel boring machines (open gripper machines and open double gripper machines ) and shield machines ( single shield machines and double shield machines , also telescopic shield machines ).
- Open tunnel boring machines are suitable for driving in stable rock and are varied for the excavation of roads tunnels (road and rail), line studs (electricity, water, gas) pressure water galleries (hydro), as well as tunnels for geological investigations or funiculars in the high mountains used . The main components of the open tunnel boring machine are the drill head with the associated drive, bracing device (bracing) and the feed device ( Kelly ).
-
Shield machines are used for driving in stable to non-stable rock formations and are regularly used for driving traffic tunnels (railways and roads) and line tunnels (electricity, water, gas). The eponymous component of these tunnel boring machines is the shield or shield jacket . These are tubular steel constructions in which all other components of the machine as well as movement spaces for material and personnel are embedded. These parts are the drill head with drive, the propulsion mechanics and the robot-like device for installing the tunnel lining, the so-called erector. The tunnel lining - mostly consisting of precast concrete parts - is installed with the erector under the protection of the rear shield jacket, the so-called shield tail.
- Single shield TBMs only have a single shield jacket.
- Double shield or telescopic shield TBMs are in fact a combination of an open and a single shield TBM, with the feed and erector located in the inner, rear shield shell, on which an outer, front shield shell enclosing the drilling unit can be moved axially in a telescopic manner. This enables a high rate of advance to be achieved.
Work steps in tunneling
The drilling takes place in several steps:
- the actual advance, in which a rotating cutting wheel digs the face under pressure ,
- the ring construction in which after completion of driving the tubbing with a erector lining the Ausbruchslaibung and seal. Then the drill presses itself between the anchoring rings and pushes itself forward again.
- With the New Austrian Tunneling Method (NÖT), the use of segments is not applicable; The main supporting element is the surrounding stable mountain range. Reinforced shotcrete, rock anchors and lattice girders are used as additional securing means.
With the help of a foam system that creates foam with tensides and water under pressure, the face can be consolidated in the soft subsoil in such a way that sandy soils and clay soils can be drilled. In muddy ground, the environment is frozen with liquid nitrogen ( ground freezing ).
Single use or reuse
Tunnel boring machines usually leave a partially completed tunnel with a smaller cross-section than the excavation diameter and the shield diameter of the machine. This is due to tubbings, protruding rock drill anchors, tunnel linings and installations such as the roadway, drainage and ventilation pipes. This means that a TBM can only advance in one direction and cannot be retracted. The operator must therefore retain a certain amount of leeway to withdraw the shield in the event that individual parts fail or become clogged with rocks so that certain parts can be replaced or broken down. The material and time required for repairs is high due to the limited accessibility and the procurement of replacements.
If tunnels are only approached from one side, i.e. drilled in one direction, the machine is again on or near the surface when the tunnel breakthrough and could, provided the size allows transport, be taken to the next site. If the machine - more or less broken down into parts - is turned around and moved a bit, it can be used to build a second, parallel tube.
Large TBMs can only be transported disassembled by land - road or rail. The shield must also be able to be dismantled. Ships with a sufficiently large cargo hold exist, but only in rare cases is it possible to bring a TBM directly to the place of use by water.
If - typically for long - tunnels are approached from two sides or even more places, a TBM inevitably has to be dismantled in the mountain. This can be done with the intention of quickly reassembling a functioning machine with these and possibly new parts; for use nearby or elsewhere. If there is no foreseeable need for a machine of this type, a few parts are preserved and dismantled for reuse and the machine frame is dismantled and scrapped.
The list of the largest tunnel boring machines (below) contains examples of the re-use of TBMs over large geographical distances: Netherlands – China, Germany – Russia.
Manufacturing companies and history
In 1844, the Scottish engineer and inventor was William Brunton (* 26. May 1777 in Dalkeith , † 5. October 1851 in Neath (Wales)) with the idea of a construction of a tunnel between England and France Hammer by compressed air for pushing and drilling to propel; the compressors required had not yet been developed at this point. His machine resembled a giant drill the diameter of the tunnel, which was supposed to crush the rock and throw the fragments into the drilled shaft for removal.
With butt drilling based on the Fowler patent from 1849, mechanical drilling began in 1857, and the introduction of the compressed air operated hammer drilling machine shortened the construction time for the Mont-Cenis tunnel from 25 to 12 years.
On impact drills , the piston and drill rod are connected by a wedge lock. With a number of strokes of 250 to 300 strokes per minute, they work with strokes of 50 to 250 mm and with total weights of up to 280 kg can only work on clamping slides with hand crank screw spindle feed on a clamping column or on the tripod.
Around 1870 there were first attempts to use a tunnel boring machine for faster driving during the construction of the Hoosac tunnel on the east coast ( Boston ) of the USA and at the same time the risk of injury to the workers - from working with hammer and chisel as well as blasting with black powder (only later did the precursors of the Jackhammer and nitroglycerin used here for the first time) - to reduce. At the press presentation on site, it was over after around 15 centimeters: It got stuck. The cast iron chisels turned out to be too soft and the steam engine too weak to drive them.
In 1897, J. G. Leyner from Denver developed the hammer drill . It worked according to the beating principle with air purging, whereby the piston hits the drill insertion end with only 1/10 of its weight at 1500 beats per minute and a twist spindle with pawls moves the drill 12 to 45 degrees per beat when the piston falls over the drill sleeve . These devices, too, were initially used, like the impact drills, on clamping columns or tripods with clamping slides and manual feed. After 1918, they already achieved 10 to 13 times the performance of impact drills, but with higher air consumption.
The further development of these hammer drills led, with the replacement of the twist gear unit in 1955, to a pressure drive and finally to a hydraulic motor drive with a constant high torque.
The further development based on Brunton's ideas in tunnel and gallery construction, which is increasingly being used in underground railway construction when the ground conditions are suitable, is characterized by the use of tunnel or gallery driving machines for diameters of up to 10.5 meters. The idea was picked up again in the 1960s and initially only used in mining and then in underground relocations. Lug and the tunnel-boring machines represent the underground void without the intermittent duty cycle drilling, blasting, loading and conveying continuously forth by using tools that are suitable for the upcoming mountain, by machining to 11.7 kN / cm² with warts chiseling or cutting rollers to 21.6 kN / cm² attack the breast and continuously release the degraded material behind them. They have been built in the USA since 1950 in a wide variety of shapes. The advantages lie in avoiding loosening by eliminating the need for blasting, reducing the over-profile and requiring fewer personnel. Disadvantages are the high investment costs and the running costs of tool wear. The Alkirk-Lawrence pilot anchor machines and the Oil Shaleminer , which drive a pilot anchor in advance, on which the drill head pulls against the chest, have become known. Robbins Company machines have been in use since the early 1960s , in which the drill cuttings that have been split off by the cutting of the milling head are picked up by buckets or excavator buckets and poured onto the discharge belt at the top. English and Japanese developments of shield tunneling machines work within a tunneling shield that is supported by the extension, with a large milling head that encompasses the entire face, or at Mitsubishi Heavy Industries with four milling heads rotating in opposite directions. In Germany, it was the machines from Demag , Wirth and Atlas Copco and the shield driving machines from Bade-Holzmann that paved the way for tunnel and gallery construction in the 1960s. In the meantime, suitable fully mechanical tunneling machines have also been developed in the Federal Republic of Germany for the construction of sloping tunnels, for the construction of vertical shafts and for the gradual expansion of the cross-sections up to 11 m. For rock strengths of 20 kN / cm², wart, tooth and disc cutters are used.
Full headers have been used for profiles with a diameter of 2 to 6.4 m, weights from 48 to 90 t and lengths from 11.5 to 21 meters since 1966 . Depending on the material and diameter, their drive power is between 240 and 950 kW, their drilling head speeds are between 12.7 and 5 revolutions per minute and the contact pressure is up to 8000 kN. The construction of the tunneling machines shows the following components:
- the drill head equipped with 8 to 10, 18 to 23 and 18 to 33 roller bits,
- the dust shield with rubber seal behind the drill head,
- Scrapers and shovels that feed the cuttings via a chute to the single-chain scraper conveyor installed under the machine or a troughed rubber belt, which at the end transfers it to an ascending loading belt,
- two to four electric motors with a total output of 240 to 950 kW, which provide the drive via cardan shafts, gears and clutches,
- a hydraulic system for bracing, pushing forward and supporting.
The machine is held in the tunnel tube by means of claws by a front and rear bracing with at least 130 N / cm². The contact pressure of the drill head is 1600 kN at 2 m to 6400 kN at 6 m diameter. The tunnel boring machines are controlled from a control station in the tender; they can be turned with a radius of 80 m for a diameter of 2.4 m and a radius of 150 m for a diameter of 6 m; a laser is used for tax control. The first device was used in 1966 to drive a 2800 m long sewer tunnel in green sandstone with a diameter of 2.1 m in Dortmund; the 6-meter device was used in 1973 on the Lower Rhine.
The fourth tube of the Hamburg Elbe Tunnel was built between 1997 and 2000 using the TRUDE shield tunneling machine, which weighs 2,000 tons and has an outside diameter of 14.20 m. The largest tunnel boring machine in the world at the time, with 111 paring knives for soft rock and 31 roller bits for hard rock, extended the tunnel an average of 6 m / day. The cutting wheel with the "Mixshield technology" was developed by the Herrenknecht company from Schwanau . Characteristic were the five spokes, which were accessible from the inside for the first time, for changing the cutting tools, and an independently controllable center cutter.
In Switzerland, smaller profiles were initially produced with tunneling machines in the 1960s. From 1970, large tunnels for road and rail traffic were also excavated with tunnel boring machines. By the end of the 1990s, 19 large road or double-track railway tunnels with a total length of 83 km had been driven with TBMs. The Gotthard Base Tunnel was created between 2002 and 2010 with the 400 m long and 2700 t heavy gripper tunnel boring machines Heidi (S ‑ 211) and Sissi (S ‑ 210) from Herrenknecht AG . The drill heads of the machines had a diameter of around 9.5 m and were equipped with more than 60 roller bits. They were driven by ten engines with 350 kW each.
The drill head as with the drive at the front end of the feed device, in technical jargon Kelly is called struck (the kelly was in the petroleum drilling a housing fixed to the lowered drilling shaft top pipe section of polygonal cross section (such as an oversized Allen key ) which guide and rotating a turntable with this same polygonal opening took over, the pipe could be lowered in the guide of the drilling table with increasing drilling depth). The feed device consists of an inner part to which the drill head is attached, the inner kelly, and an outer part, the so-called outer kelly. The outer kelly of the machine is fixed in the drilled tunnel tube by means of bracing. The inner kelly with the drill head attached to the front end slides during the drilling process parallel to the drilling direction in the outer kelly in the drilling direction forwards. Inner kelly and outer kelly are connected to one another via the feed cylinder. The feed cylinders push the inner kelly forward along with the drill head. The drill head of the machine is provided with cutting rollers, which are equipped with hard metal rings and are called disc cutting rollers. The rotary drive of the drill head is equipped either with hydraulic motors or electric motors, whereby the electric drive variant has become the more common nowadays. Stepless control of the speed of the drill head has meanwhile become standard in modern tunnel boring machines. A steel shield is arranged around the drill head of the machine, the drill head casing, which on the one hand takes on a support function for the drilled tunnel tube and on the other hand serves as head protection against any falling rock. The excavated rock is removed by conveyor belts and either loaded into wagons for transport out of the tunnel or transported out of the tunnel by conveyor belt. Immediately after the drilling process, the drilled tunnel is supported with what is known as the initial securing system if necessary. This initial securing can consist of heavy rock anchors, steel support arches and / or steel mats, depending on the requirements. Shotcrete is also used. The final extension of the bored tunnel tube will be brought in behind the machine at a later point in time and will follow the tunnel boring machine.
There are only a few companies in the world that manufacture these machines. In Germany these are the companies Herrenknecht AG from Schwanau and Aker Solutions (formerly Aker Wirth GmbH) from Erkelenz ; the Robbins Company in the USA, Mitsubishi , IHI , Kawasaki and Hitachi Zosen in Japan are other manufacturers. NFM Technologies SA in France built with licenses from MHI ( Mitsubishi Heavy Industries ) and later SHMG (Shenyang Heavy Machinery Group). Former Canadian manufacturer Lovat was bought by Caterpillar in 2008 and shut down in 2013.
Herrenknecht puts the global market for machine tunnel construction equipment at around 1.5 billion euros, of which the company claims to cover around 1.1 billion euros (as of 2014).
With ultrasonic drills ( "ultrasonic drilling" ), a faster driving than Fräsbohrern is possible. The BADGER (tunneling robot) is a research project funded by the EU to create an autonomously working earth drilling robot that produces the tunnel walls as a concrete 3D printer . BADGER is an apronym for "ro B ot for A utonomous un D er G round trenchless op ER ations, mapping and navigation".
Well-known projects
The following is a list of tunnel projects that have been implemented with tunnel boring machines or are still under construction:
Germany
- Albvorland tunnel ( new Wendlingen – Ulm line )
- Boßler Tunnel ( new Wendlingen – Ulm line )
- City-Tunnel Leipzig (trunk line tunnel for the S-Bahn in Central Germany, Leipzig)
- Filder Tunnel ( Stuttgart 21 rail project )
- Finne Tunnel ( new Erfurt – Leipzig / Halle line )
- Kaiser Wilhelm Tunnel (second tunnel tube between Ediger-Eller and Cochem)
- Katzenberg Tunnel (Karlsruhe – Basel rail link)
- Combined solution (Karlsruhe) (Karlsruhe underground tram)
- New Schlüchtern tunnel (second tunnel under the thistle lawn near Schlüchtern)
- North-South light rail (Cologne)
- TRUDE (A7 motorway, fourth Elbe tunnel tube, Hamburg)
- Tunnel north-south long-distance railway (Tiergarten tunnel , Berlin)
- Rastatt Tunnel (new / upgraded Karlsruhe-Basel line)
- U-Bahn line 5 (Berlin) (extension between Alexanderplatz and Brandenburg Gate, Berlin)
- VERA (subway line 4, Hamburg)
- Construction section 40 of the Emscher sewer (two parallel, ten kilometer long tunnel tubes between Bottrop and Oberhausen)
Austria
- Brenner base tunnel (parts of the north access route)
- Koralm tunnel (section of the Koralm railway)
- Pfänder tunnel (west tube)
- Semmering Base Tunnel (Fröschnitzgraben section)
- Wienerwaldtunnel (railway connection)
Switzerland
- New Alpine Transversal Railway (NEAT):
- Vereina tunnel (meter-gauge railway tunnel with Y-division)
- Weinberg tunnel (railway tunnel, Zurich)
- Zimmerberg Base Tunnel (railway tunnel, Zurich. 1st stage)
Others
- Canal de Navarra (Spain)
- Citytunnel Malmö (rail connection in Malmö, Sweden)
- Eurotunnel (rail link England-France)
- Great Belt Railway Tunnel (Denmark)
- Hallandsås tunnel (Gothenburg – Lund railway line, Sweden)
- Niagara Tunnel Project ("Big Becky", TBM with 14.4 m diameter; breakthrough May 2011; completion summer 2013)
- Westerschelden Tunnel (Netherlands)
- Hsuehshan Tunnel (Taiwan National Highway No. 5)
- Crossrail (rail link in London)
List of the largest tunnel boring machines
No. | year | country | tunnel | Manufacturer / technology | diameter |
---|---|---|---|---|---|
1 | 2015 | Hong Kong | Tuen Mun - Chek Lap Kok motorway tunnel | Herrenknecht Mixshield | 17.60 |
2 | 2011 | United States | Replacement tunnel for the Alaskan Way Viaduct, Seattle | Hitachi Zosen EPB shield | 17.48 |
3 | 2016 | Italy | Santa Lucia Tunnel ( A1 ) | Herrenknecht EPB sign | 15.87 |
4th | 2015 | China | Yangtze River Tunnel on the Wuhan Metro | Herrenknecht Mixshield (2 ×) | 15.76 |
5 | 2011 | Italy | Sparvo tunnel ( A1 ) | Herrenknecht EPB sign | 15.55 |
6th | 2011 | China | Shanghai West Yangtze River Tunnel | Herrenknecht Mixshield, ex No. 8 | 15.43 |
7th | 2010 | China | Qianjiang Tunnel, Hangzhou | Herrenknecht Mixshield, ex No. 8 | 15.43 |
8th | 2006 | China | Shanghai Changjiang Daqiao | Herrenknecht Mixshield (2 ×) | 15.43 |
9 | 2005 | Spain | Madrid Calle 30 motorway tunnel | Herrenknecht | 15.20 |
Mitsubishi | 15.00 | ||||
10 | 2013 | Italy | Caltanissetta Tunnel, Sicily (SS 640) | NFM Technologies | 15.08 |
11 | 2011 | China | Weisan Road Tunnel, Nanjing | IHI / Mitsubishi / CCCC Slurry TBMs (2 ×) | 14.93 |
12 | 2012 | China | Hongmei Road Tunnel, Shanghai | Herrenknecht Mixshield | 14.93 |
13 | 2008 | China | Yangtze River Tunnel Nanjing | Herrenknecht Mixshield (2 ×) | 14.93 |
14th | 2013 | China | ? | Herrenknecht Mixshield, ex No. 13 | 14.93 |
15th | 2006 | China | Jungong Road Tunnel, Shanghai | NFM Technologies, ex No. 17 | 14.87 |
16 | 2004 | China | Shangzhong Road Tunnel, Shanghai | NFM Technologies, ex No. 17 | 14.87 |
17th | 2000 | Netherlands | Groene Harttunnel (railway) | NFM Technologies | 14.87 |
18th | 2006 | Canada | Niagara Tunnel Project | Robbins Hard Rock Gripper TBM | 14.40 |
19th | 2013 | New Zealand | Waterview Connection, Auckland | Herrenknecht EPB sign | 14.41 |
20th | 2004 | Russia | Silberwald motorway tunnel, Moscow | Herrenknecht Mixshield, ex No. 22 | 14.20 |
21st | 2001 | Russia | Lefortovo Tunnel , Moscow | Herrenknecht Mixshield, ex No. 22 | 14.20 |
22nd | 1997 | Germany | 4. Tube of the New Elbe Tunnel | Herrenknecht Mixshield ( TRUDE ) | 14.20 |
23 | 2009 | China | Yingbinsan Road Tunnel, Shanghai | Mitsubishi EPB sign, ex No. 24 | 14.27 |
24 | 2007 | China | Bund Tunnel, Shanghai | Mitsubishi EPB sign | 14.27 |
25th | 2004 | Japan | Namboku line of the Tokyo Metro | IHI EPB sign | 14.18 |
26th | 1994 | Japan | Tōkyō-wan-Aqua-Line (Trans Tokyo Bay) | 8 TBM: 3 Kawasaki, 3 Mitsubishi, 1 Hitachi, 1 IHI | 14.14 |
27 | 2010 | Spain | SE-40 motorway , Seville | NFM Technologies (2 ×) | 14.00 |
Web links
- Explanations of the TBM using the example of the Leipzig City Tunnel
- Installation of a blind segment ring using the Leipzig City Tunnel as an example
- Video: How a single shield tunnel boring machine works. In: bauforum24.tv , 2011, 3:44 min.
Individual evidence
- ↑ Tunnel boring machines for hard rock. ( Memento from February 12, 2013 in the web archive archive.today ) In: Aker Wirth GmbH , accessed on May 5, 2015.
- ↑ Single shield TBM - Rapid advance in changing mountain conditions. Herrenknecht AG website, accessed on September 14, 2018
- ↑ Double shield TBM - continuous advance at top speed. Herrenknecht AG website, accessed on September 14, 2018
- ^ Journal Über Land und Meer , Tunnel between England and France, Deutsche Verlags-Anstalt , Berlin, 1881.
- ↑ Georg Garbotz , Construction machines once and now , in: Baumaschine und Bautechnik , Frankfurt am Main, ISSN 0005-6693 , 22nd year, issue 5, 1975, p. 153 ff.
- ↑ TRUDE - The largest shield tunneling machine in the world. In: Museum der Arbeit , Hamburg, accessed on May 5, 2015.
- ↑ Leonhard Schmid, Josef Elmiger: How is due to the high percentage of machines tunneling in Switzerland . In: Tunnel technology for future tasks in Europe . Balekma-Verlag, Rotterdam 1999, ISBN 90-5809-051-5 , pp. 59-71.
- ↑ Gotthard Base Tunnel. In: Herrenknecht , March 2011, accessed on May 5, 2015.
- ↑ Single shield TBM. In: Herrenknecht , accessed on May 5, 2015.
- ↑ Max Hägler: "The German is really afraid of everything" . In: Süddeutsche Zeitung . January 20, 2014, p. 16 .
- ↑ International Mining Technology Hall of Fame
- ↑ What is the BADGER project?
- ↑ Robot BADGER Can Drill Underground and 3D Print Tunnels
- ^ Niagara Tunnel Project. Technical facts. By: Ontario Power Generation and Strabag , accessed May 5, 2015.
- ↑ Tracking the world's mega-TBMs , TunnelTalk
- ↑ Chronicle - a success story for over 35 years herrenknecht.com, until 2015, accessed December 11, 2016.
- ↑ XXL tunnel boring machines in the Yangtze River DeltaXXL tunnel boring machines in the Yangtze River Delta , March 14, 2014
- ↑ "Used a world's largest diameter 14.18 m double shield tunnel boring machine for the construction of the Tokyo Metro Namboku Line's Azabu section construction"