Linear motor
A linear motor ( English linear motor or linear synchronous motor (LSM) ) is an electrical drive machine. In contrast to the common rotating machines, a linear motor does not set the objects it drives in a rotating movement, but pushes them on a straight or curved path ( translational movement ). The term linear motor is also used for drives in which the moving part ( “runner” ) rotates but is only partially surrounded by the stationary stator ( e.g. turntable or washing drum drives ). Drives for linear movements such as voice coils , the principle of which does not allow for different forces or speeds, are not referred to as linear motors , but only combined with the linear motors under the broader term linear actuator .
The linear motor was invented before the rotary motor. In 1854 Charles Grafton Page patented a solenoid linear motor with a slider crank (US patent 10480 "Improvement in electro-magnetic engines"). The machine was intended to drive locomotives .
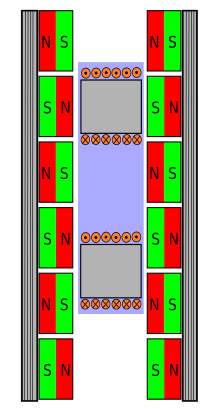
Working principle
Direct explanation
The magnetic fields of the rotor and the magnetic fields of the stator ("travel path") are always combined (the electromagnets are supplied with current with the correct polarity) that the rotor is pulled a distance "forward" (and is repelled by the magnetic field behind it). If it has reached the position to which it was pulled, the polarity is reversed and the rotor is now pushed away from this position and drawn towards the next magnet coil / permanent magnet. Because the runner has two slightly offset magnetic field generators, at least one of them is always “halfway”, which enables the direction of travel (forwards or backwards) to be determined.
Derived from the rotary motor
In principle, rotary motors of all principles could be converted into linear motors by a projection that depicts the round air gap on a straight line, with the originally circular electrical excitation windings ( stator ) being arranged on a flat path. In the linear motor, the rotor, which rotates in the three-phase motor, is drawn over the travel path by the longitudinally moving magnetic field. This is where the frequently used term traveling field machine comes from .
In practice, either three-phase asynchronous machines (the magnetic field is not permanently coupled with the movement) or three-phase synchronous machines in the broader sense (which also includes linear reluctance machines and linear stepper motors) are used. The use of commutated DC machines is possible, but rather unusual. The required distance between the rotor and the linear winding can be maintained, for example, with wheels or air cushions or by floating on a regulated electromagnet.
In contrast to rotating brushless machines, in linear motors the actively energized part is often (but not necessarily) moved while the passive part stands still. The rotor (translator, slide) of the linear motor then corresponds topologically to the stator of the rotating machine and the stator (stator, track, rail) corresponds topologically to the rotor of the rotating machine.
Use in industry
Linear motors are used in machine tools , positioning systems and handling systems in machining centers. Conventionally, feed forces are generated by a rotating electric motor and converted into a translational movement in a transmission. The movement is thus brought about indirectly . Linear motors, on the other hand, make it possible to directly represent a translational movement, which is why they are also called direct drives .
Linear motors have in this area the advantage of high accelerations of up to 6 g and traversing speeds up to 800 m / min (48 km / h). The maximum forces that can be achieved with asynchronous polysolenoid linear motors are currently 30 kN. Concepts with cooled, superconducting coils are also being developed to achieve even higher mechanical forces. They are also better suited for use in clean rooms because of the few parts that rub against each other .
Linear motors are also often used in positioning devices or various other types of machines, such as in ultrasonic microscopes , plasma cutting systems , laser cutting systems and water jet cutting systems. Linear motors are also suitable as pumps for liquid metals (for example sodium circuit in nuclear power plants), with the coils being permanently mounted and moving the liquid metal as a runner in the flow tube.
Linear motors are also used for rail drives ( Transrapid / RailCab HSST or roller coasters ).
Linear motors are increasingly being built into small household electrical appliances such as electric toothbrushes, electric razors and oral irrigators because of their many design advantages. Magnets made of neodymium-iron-boron are used as stator .
Use in the technology of data processing
With the so-called "Winchester disk system" IBM -3340, linear motors were used to replace the previous hydraulic drives for the hard disk drive.
In some more expensive CD players, the pickup system is also driven by a linear motor.
Specialist literature
- Günter Springer: Expertise in electrical engineering. 18th edition, Verlag Europa-Lehrmittel, Wuppertal 1989, ISBN 3-8085-3018-9 .
- Gregor D. Häberle, Heinz O. Häberle: Transformers and electrical machines in power engineering systems. 2nd edition, Verlag Europa-Lehrmittel, Haan-Gruiten 1990, ISBN 3-8085-5002-3 .
- Günter Boy, Horst Flachmann, Otto Mai: The master's examination in electrical machines and control technology. 8th edition, Vogel Buchverlag, Würzburg 1990, ISBN 3-8023-0725-9 .
Web links
- Superconducting linear motors ( Memento from October 28, 2006 in the Internet Archive ) (PDF; 611 kB)
- Applet for visualizing the field in an asynchronous or synchronous machine or in a linear motor
- Flash animation for the Transrapid system
- Linear drives for roller coasters - articles with animated principles
Individual evidence
- ↑ Kurt Gerecke and Klemens Poschke: IBM Storage System Compendium ( accessed on October 29, 2012).