Natural stone facade anchoring
The natural stone facade anchoring of panels has existed in Germany since the 1930s and today (2008) it is an essential field of work for the stonecutter . Not only are plates attached to structures with stainless steel anchors, but also measured beforehand on the building and manufactured with stone processing machines such as stone saws , stone grinding machines and stone drilling machines.
history
With the decline of solid buildings made of natural stone in the building industry at the beginning of the 20th century and the emergence of buildings made of reinforced concrete, the technology of anchoring natural stone slabs was developed as an alternative to solid stone . In addition, the Bauhaus style, with designs without building decorations , made the use of ornamented stone, which required a certain thickness, obsolete and simplicity was in demand.
Mies van der Rohe's German pavilion at the world exhibition in Barcelona (1929) , which was clad with travertine and serpentinite , is considered to be trend-setting for the new architecture, which was designed with natural stone slabs. Possibly one of the first structures in which the new offset technology with "thin" natural stone slabs was used on a large scale is the midnight building in Stuttgart made of Cannstatter travertine (1926–1928) by Ludwig Eisenlohr junior and Oscar Pfennig . A large building project with around 33,000 m² facade panels made of Cannstatt travertine was the IG-Farben-Haus in Frankfurt (1928–1931) by Hans Poelzig . Other large buildings clad with natural stone during this period were the " Disch-Haus " (Roman travertine) by Bruno Paul in Cologne (1929) and the Shell house in Berlin with Roman travertine (1930–1931) by Emil Fahrenkamp . This technology was implemented on a large scale at the Reich Aviation Ministry (1935), today Detlev-Rohwedder-Haus , with around 42,000 square meters of exterior facade made of Kirchheim shell limestone .
The assembly system at that time followed four principles: "Continuously firm uprising [of the natural stone slabs], adhesive bond with back-up mortar, anchoring to prevent tilting, force-fit mortar bond in the joints."
- Early buildings clad with natural stone
The midnight building in Stuttgart (1926–1928)
The Disch House in Cologne (1929)
The Detlev-Rohwedder-Haus (former Reich Aviation Ministry ) (1935)
The Shell House in Berlin (1930–1932)
According to the current state of knowledge, this anchoring and relocation technology is unsatisfactory, as the anchoring was carried out with iron anchors and the facade panels were back-mortared. Water can penetrate the joints through fine cracks and cause frost damage. Furthermore, the thermal expansion leads to tension in the large-area bond between the panels; this can cause cracks in the stone slabs and peeling of the mortar from the substrate. War damage from the Second World War and its improper restoration in the post-war period damaged the natural stone façades that were anchored with this technology.
After the end of World War II, this technology continued to be used. On July 1, 1961, the German Natural Stone Association published anchoring examples in which the consulting civil engineer Johannes Wieczorek carried out static calculations that were checked by the Bavarian State Trade Agency in Würzburg and provided the prerequisites for standardization. The development and production of stainless steel anchors in series, which was carried out by the Lutz company in Wertheim , progressed promptly . Furthermore, in his 1962 work, The Outer Wall, Professor Schaupp pointed out the importance of rear ventilation with regard to water vapor diffusion and thermal insulation . He also made clear the need for expansion joints between the individual stone slabs. This standard, which is still valid today, provides for a 3-centimeter-thick plate made of hard stone , which is attached to 4 anchoring points, as well as the corrosion-resistant stainless steel anchoring made of V4A steel with a rear ventilation of a 2-centimeter-thick layer of air . This made it possible to decouple the natural stone slabs from the water balance of the thermal insulation behind them.
conditions
- Design requirements: The outer skin of a building becomes a design element of the building through the choice of stone, the format of the panels and the choice of the joint cut. The stone facade creates a designed image through the surface treatment , texture as an accumulation of minerals in the natural stone and drawing of the stone material (color, color change, veins).
- Economic requirements: In contrast to other building materials, natural stone is extracted and manufactured with little energy and cost; it is not flammable, and it can also be disposed of without any problems because it is a natural material. From a medium-term economic perspective, natural stone is one of the most cost-effective building materials.
- Technical requirements: The natural stone must be weatherproof, the building structure behind it must be protected and the thermal insulation must be optimally installed. Each facade panel must be able to move freely individually due to the thermal expansion of natural stone. Therefore, the joints on the panels should either remain open or only be closed with elastic joint compounds.
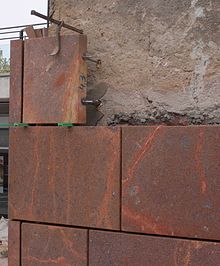
Principles of anchoring
The natural stone slabs are generally anchored at four points. A special case is the plate anchored at three points. The anchor pins enclose the panel edges at least 25 millimeters deep. The holes in the panel edges must not be less than the distance to the panel outer edges of 10 millimeters for static reasons (anchor pin breakout load).
The construction of today's natural stone facades:
- Natural stone slabs with a minimum thickness of 30 millimeters for hard stone and 40 millimeters for soft stone
- Air layer with a distance from the natural stone slab to the thermal insulation at least 20 millimeters (firedamp side up to 50 millimeters)
- Thermal insulation according to the requirements of the applicable thermal insulation ordinance
- Mounting base made of concrete and masonry with a minimum strength of 12 N / mm²
If these prerequisites are met and the appropriately dimensioned standard anchors made of V4A steel have been determined, no static calculation is required, but the requirements of a so-called type - tested anchoring are met.
Anchor types and anchoring technology
There are so-called mortar anchors, which are mortared into drill holes in concrete and masonry with high-quality, quick-setting cement mortars. Furthermore, dowel anchors are used to fasten in the building substrate or on V4A rail substructures. The so-called undercut anchoring, anchoring in the back of the panel and not in the panel edges, is a special case. This also applies to the welded anchors, where the stainless steel anchors are welded to steel plates in the concrete.
Basically, the anchor pins of the retaining anchors have a retaining function in vertical joints that enclose the panels in the upper fifth of the panel side . The support anchors, which enclose in the lower fifth of the plate side, fulfill a double function, a carrying and holding function . The latter also bear the weight of the individual panels. If it is anchored in the horizontal joint, only support anchors are used. Other types of anchors are pillar and screw anchors. There are also special anchors for special applications and large-format panels.
Furthermore, natural stone slabs can also be attached to rails.
The anchoring common today is done with mortar anchors, as they represent the cheapest alternative.
literature
- Heinrich Rhein: Natural stone facades. Displacement technology and basics of design. In: Educational center for the stonemasonry and sculpture trade. The manual for daily work with natural stone. 2., revised. Edition, Ebner Verlag. Ulm 1994, ISBN 3871881376 .
- Alfred Stein: Dimensioning of natural stone facades. ISBN construction and dimensioning according to DIN 18516. Callwey-Verlag. Munich 200. ISBN 3766714074
- 100 years of associations of the natural stone industry, natural stone, claim and obligation , ed. v. German Natural Stone Association V., Marktheidenfeld 2000.
Web links
- Certificate of usability for natural stone. Material testing and research institute Neuwied (PDF)
Individual evidence
- ↑ Anchoring or fastening of massive components made of natural stone was already carried out in ancient Greece, with cantilevered and statically stressed components being secured and introduced using iron anchors
- ^ German Natural Stone Association: 100 years of associations. P. 15 (see literature)
- ^ German Natural Stone Association: 100 years of associations. P. 19 (see literature)
- ↑ 100 years of associations in the natural stone industry. P. 23 (see literature)