Tilt sensor
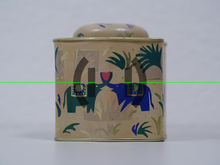
An inclination sensor is a precision mechanical or electrical measuring device that establishes the exact reference to the perpendicular direction for an instrument or vehicle frame or monitors changes in the inclination angle .
Sensors suitable for geodesy were developed in the 1970s and were initially called inclination or height compensators or electronic level .
Measurement principles
There are numerous methods of measuring inclinations with respect to the perpendicular direction determined by gravity. The solder or plumb modeled function pendulum body, which are supported mechanically or electromagnetically and their location electronically , inductively , capacitively or optically measured. Gyro platforms determine a change in position relative to the starting position and work independently of gravity.
Microelectromechanical systems typically use spring-mass systems that determine the deflection of small test masses depending on the position with the principles listed above.
Other sensors work with liquids. They use either the reflection or refraction of a light beam by the liquid level or a resistance measurement or capacitance measurement depending on the position of the liquid.
The thermal processes represent another group: There is a small heating element in the measuring cell. The heated gas rises in the measuring cell through convection . There are temperature sensors around the measuring cell that detect the alignment of the heat flow in the measuring cell and use this to determine the position of the system.
Digital camera
Some digital cameras and smartphones have three acceleration sensors that are perpendicular to one another, with the help of which the direction of the perpendicular in relation to the device can be determined and saved in the metadata of the image files.
The extract from the EXIF data in the adjacent JPEG file shows, for example, the corresponding (rounded) measured values:
Accelerometer Z : 250 Accelerometer X : -1 Accelerometer Y : 55 Camera Orientation : Normal Roll Angle : 0 Pitch Angle : -12.4
The camera recorded the picture in landscape format (camera orientation = "normal"). The roll angle was around 0 ° because the camera was leveled to the side. The pitch angle was 12.4 ° because the camera was tilted. Since it was inclined downwards in the viewing direction, the pitch angle is given as negative. The acceleration values in X- (right / left), Y- (front / back) and Z-direction (bottom / top) are given as rounded integer values in the number range from -256 to 256, and the secondary condition applies:
This maximum value of 256, which occurs when the camera is stationary, corresponds to the acceleration due to gravity .
The roll angle results from the acceleration values as follows:
The pitch angle results from the acceleration values as follows:
Applications in geodesy
Small inclination sensors are built into the substructure of modern theodolites and total stations . They can be very precise (0.5–1 ″) because they only require a small measuring range . They take on the function of a height compensator for the vertical circle , but also monitor the inclination of the vertical axis in both directions.
Own add-on devices are also on the market, e.g. B. for laser trackers or for sounding . Particularly precise inclination sensors are built into astrogeodesy instruments , for example in modern prism astrolabes or CCD zenith cameras .
Industrial sensors
Industrial sensors typically have a lower accuracy, but larger measurement and temperature ranges than geodetic sensors. Typical are 15 ° to 60 ° measuring ranges with accuracies in the per mil range (i.e. a few 0.01 ° angle errors) and application ranges from −30 to +70 ° C.
The spectrum of use ranges from accident protection , for example on excavators and cranes, to machine monitoring and industrial robots . With a smaller measuring range (a few degrees), accuracies of 5 '' to 10 '' can be achieved. The sensors typically transmit the measurement data electronically as a voltage level or via a current interface . Digital transmissions are also common, for example in the serial RS232 format or via the Controller Area Network protocol. The standardized CANopen profile (CiA 410) exists for use in industrial automation technology .
Web links
- Overview of inclination sensors for industry