Building lime
Building lime is a collective term for building materials made of limestone used in construction . Building lime is a very old building material and was processed in ancient times. Nowadays, building limes are mainly used as a mineral binder in construction. They are used to produce lime mortar, which is used as masonry and plaster mortar . Building lime can be used for soil consolidation in the field of subsoil improvement . Furthermore, building lime is available in the form of limestone powder in the cement types Portland limestone cement and, if necessary, Portland composite cement . The limestone powder content results in faster hardening and higher early strength compared to normal Portland cement.
In the hardened state, pure lime mortar has a considerably lower strength than cement mortar with the same mixing ratios. However, it is comparatively easier to process. Lime plaster has good water vapor permeability and is therefore usually used indoors.
When handling building limes, it should be noted that these building materials have a strong alkaline effect and can cause skin burns if they come into contact with the skin. Particular caution is required when "extinguishing" (mixing with water) the quicklime. The reaction with water is exothermic and quickly releases a lot of heat. Contact with the resulting lime splatters is dangerous. Eyes and mucous membranes in particular need to be protected, otherwise blindness can occur. It is also important to only use air lime when mixing with gypsum, since mixtures with hydraulic lime and gypsum lead to severe damage caused by drifting.
Manufacturing
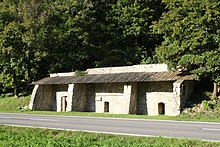
A distinction is made between air lime, which only hardens in the air, and lime with hydraulic properties. Air lime is obtained from limestone (CaCO 3 ) or dolomite rock (CaCO 3 ∙ MgCO 3 ). A lime made from limestone is called white lime, a dolomite lime made from dolomite rock. Natural hydraulic limes are made from marl limestone. In addition to the non-hydraulic base lime, they contain the so-called hydraulic factors silica (SiO 2 ), aluminum oxide (Al 2 O 3 ) and iron oxide (Fe 2 O 3 ). After the raw materials have been broken down, they are broken down and ground. The material is then fired in a shaft furnace at temperatures of 900 ° C to 1200 ° C. When burning, the limestone (CaCO 3 ) decomposes into carbon dioxide (CO 2 ) and calcium oxide (CaO), so-called quicklime. When burning marl-containing limestone, so-called clinker minerals (tricalcium aluminate, dicalium silicate and tetracalcium aluminate ferrite) are also formed from calcium oxide (CaO) and the hydraulic factors.
Firing process (over 900 ° C):
CaCO 3 → CaO + CO 2
Quicklime is sold as unslaked lime in the form of lump lime or fine lime. It still has to be deleted before processing. To extinguish the calcium oxide, water is added, which converts it into calcium hydroxide (Ca (OH) 2 ), so-called hydrated lime (also called slaked lime), and gives off large amounts of heat during the reaction. If just as much water is added as is stoichiometrically necessary for the conversion , it is called dry quenching. Wet quenching, on the other hand, involves adding more water than stoichiometrically required.
Deletion process:
CaO + H 2 O → Ca (OH) 2
This manufacturing process is part of the technical lime cycle. The re-hardening of the building lime takes place when the hydrated lime (Ca (OH) 2 ) combines with the absorption of carbon dioxide from the air and the release of water (see “ Dry living ”) to form calcium carbonate (limestone) [1]. This closes the cycle. The triggering of this reaction requires the presence of water. Therefore hydrated lime can also be stored in paper bags without hardening.
Hardening (simplified):
Ca (OH) 2 + CO 2 → CaCO 3 + H 2 O
Forms and names of the lime
In the past, quicklime was usually supplied in lump form (lump lime) and slaked wet on the construction site in order to obtain lime slurry, which was then mixed with sand. In some cases, sand was added to the lump lime for mortar production before it was extinguished, which should lead to better mortar properties and somewhat mitigate the strong extinguishing reaction.
In the past, water lime was used to describe weakly hydraulic limes which were burned from clayey limestone (lime marl ) below 1250 ° C. They harden through both carbonation and hydration .
In addition to calcium hydroxide, hydraulic limes contain so-called hydraulic factors such as silicates (e.g. SiO 2 ), aluminates (e.g. Al 2 O 3 ) and iron oxides (e.g. Fe 2 O 3 ) from which calcium silicates and calcium aluminates are formed . The hydraulic part of the binding agent can also harden under water, since no admission of carbon dioxide is necessary.
To obtain a hydraulically hardening binder, lime can also be mixed with cement or with latent hydraulic additives such as metakaolin, brick powder, blast furnace slag and pozzolans ( trass limestone , volcanic ash or fly ash ). The production method of hydraulic building lime from limestone and volcanic earth has been known since ancient times.
Nomenclature according to DIN
In Germany, according to the lime standard DIN EN 459-1 (old DIN 1060), a distinction is made between air lime and lime with hydraulic properties for standardized building limes.
Air limes are further divided into white limestone (abbreviation CL) and dolomite limestone (abbreviation DL). In the standard-compliant designation of air lime, the abbreviation is followed by a number. With white lime, this number indicates the total content of calcium oxide (CaO) and magnesium oxide (MgO). The standard includes the white limes CL 90, CL 80 and CL 70. In addition, there is a classification according to their delivery form as unslaked limes (Q), hydrated lime (S), lime dough (S PL) or milk of lime (S ML). The types of dolomite lime are DL 90-30, DL 90-5, DL 85-30, DL 80-5. As with white lime, the first number indicates the total content of CaO and MgO. The second number indicates the minimum content of magnesium oxide (MgO). Furthermore, dolomite lime is classified into unslaked lime (Q) or hydrated lime (S) according to the form in which it is supplied. Semi-slaked dolomite hydrated lime is classified as (S1).
According to the standard, the group of limes with hydraulic properties includes hydraulic lime (code HL), natural hydraulic lime (code NHL) and formulated lime (code FL). The number in the abbreviation of the lime indicates the minimum compressive strength in N / mm². A distinction is made between the compressive strength classes 2 N / mm², 3.5 N / mm² and 5 N / mm².
In the case of formulated lime, the mass fraction of available lime as Ca (OH) 2 is also relevant and is identified with the letters A (40–80 M%), B (25–50 M%) or C (15–40 M%). Since formulated lime is not a fixed mixture of different building limes with hydraulic and / or pozzolanic additives, the composition is specified in accordance with the DIN EN 459-1 standard (Appendix D).
According to DIN , a distinction is made as follows:
group | sorts | Short name | Commercial form |
---|---|---|---|
Air lime | White lime (CL) | CL 90
CL 80 CL 70 |
Unslaked lime (Q) |
Hydrated lime (S)
Lime dough (S PL) Milk of lime (S ML) |
|||
Dolomite lime (DL) | DL 90-30
DL 90-5 DL 85-30 DL 80-5 |
Unslaked lime (Q) |
|
Half-cleared (S1) | |||
Hydrated lime (S) | |||
Lime with hydraulic
properties |
Hydraulic lime (HL) | HL 2
HL 3.5 HL 5 |
will not after
Commercial form distinguished |
Natural hydraulic lime (NHL) | NHL 2
NHL 3.5 NHL 5 |
||
Formulated Lime (FL) | FL A 2
FL B 2 FL C 2 FL A 3.5 FL B 3.5 FL C 3.5 |
Pit lime versus hydrated lime
The difference between slaked lime and hydrated lime is the extinguishing process used. Puddle lime is created by wet slaking with a stoichiometrically disproportionately large amount of water. Hydrated lime, on the other hand, is produced by dry slaking with steam.
The properties (e.g. plasticity) of the slaked lime improve with the duration of the "soaking" (sump lime, fatty lime), which is particularly important if the lime is to be used as a lime paint. Pit lime that has not been stored for too short a period may still contain particles that have not been extinguished, which are subsequently extinguished. This is problematic because the extinguishing is accompanied by an increase in volume of around 70% and the particles can thus spark a disruptive effect (limestone drift).
Traditionally, lime was stored as sump lime for up to three years before use. It used to be swamped in lime pits that existed in many places. It was also common on construction sites to sump the lime first. The lime slurry must always be stored under a layer of water while it is soaking in order not to react with the carbon dioxide in the air. Today, slaked lime should soak in at least a few weeks, but better months. The manufacturer's specifications for the minimum sump duration must be observed.
In the case of dry slaked hydrated lime in powder form, on the other hand, storage under water for one day is sufficient. Apparently there is no further change after that.
For the production of mortar, powdered limes (hydrated lime), slaked “dry” with water vapor in extinguishing drums, are predominantly used today. Wet slaked lime is used in exceptional cases for plaster or paint.
use
Setting process
A lime mortar hardens through carbonation . This exothermic reaction requires water, which is initially present in the air in the form of added mixing water and later in the form of water vapor. Together with carbon dioxide, the water forms carbonic acid (H 2 CO 3 ) from the air , which binds to the lime base and splits off water in the process. The reaction can be represented as follows:
Ca (OH) 2 + H 2 CO 3 → CaCO 3 + 2 H 2 O
In the case of air lime mortar, slow setting is of particular importance so that a clean microcrystalline structure can develop. Lime plaster applied to a highly absorbent base or exposed to direct sunlight can " burn up ", ie. that is, it dries out before it has set sufficiently. Lime also hardens cleanly at temperatures above 5 ° C (lime coatings at over 10 ° C) and "freezes" in frost. In both cases, loose crystals form without bonding, so that the plaster chalked or crumbled. Furthermore, an excess of water in the mortar can delay the reaction. Another problem arises when a diffusion-proof coating is applied too early to the mortar layer. There is then no supply of CO 2 for the reaction and the process can come to a standstill.
However, if the CO 2 concentration in the air is increased, for example by installing coke ovens in combination with good air circulation, the hardening of the lime accelerates. In addition, a warm environment also accelerates the hardening reaction.
Air-lime mortar is more elastic than other mortars and can, to a certain extent, compensate for slight movements in the substrate, which are caused, for example, by thermal stresses, swelling and shrinkage when exposed to moisture or settlement phenomena, without cracking. The strength of air-lime mortars increases slightly in the first few years because the carbonation usually proceeds very slowly. In commercial use, pure air lime mortar has largely been replaced by mortars with the addition of hydraulic lime, cement or synthetic resins, since air lime has to be kept moist for a long time, the strength only develops very slowly and the mortar only hardens if the access of carbon dioxide is guaranteed, so that mortar inside thick walls has often not set after years. In addition, hydraulic limes also achieve weather resistance earlier
With the technical names of the materials, the lime cycle is shown in the following form:
Building lime products
Soaked lime paste or powdered white lime hydrate are diluted by adding water to lime sludge or further to lime milk . These building lime products are used for painting or as whitewash with a disinfectant effect.
Lime mortar can be made from a mixture of building limestone with water and a rock grain such as sand or possibly gravel. Lime mortar is one of the oldest known building materials. The lime acts as a binding agent between the grains of sand, which ensures high compressive strength. Lime mortar can be used both as masonry mortar and as plastering mortar. Air lime is also used to manufacture sand-lime bricks and aerated concrete. Building lime products are also used for soil improvement measures
Norms and standards
- DIN VEN 459-1 - building lime
- DIN 1060 -1
Individual evidence
- ↑ Balder Batran: Basic knowledge of construction . Handwerk und Technik Verlag, Stuttgart 2003, ISBN 3-582-03500-X , p. 111 and 112 .
- ^ Building material script (PDF; 568 kB) from the University of Technology, Economics and Culture, Leipzig
- ^ Hansjörg Frey: Structural engineering - specialist knowledge of construction . Europa-Lehrmittel Verlag, Haan-Gruiten 2003, ISBN 3-8085-4460-0 , p. 85 .
- ^ Lime mortar , by Elert, K .; Cazalla, O .; Rodriguez. C .; Hansen, E .; Sebastian, E .; Source: Restauro, 2002. ISSN 0933-4017