iron
properties | |||||||||||||||||||||||||||||||||||||||||||||||||||||||||||||
---|---|---|---|---|---|---|---|---|---|---|---|---|---|---|---|---|---|---|---|---|---|---|---|---|---|---|---|---|---|---|---|---|---|---|---|---|---|---|---|---|---|---|---|---|---|---|---|---|---|---|---|---|---|---|---|---|---|---|---|---|---|
General | |||||||||||||||||||||||||||||||||||||||||||||||||||||||||||||
Name , symbol , atomic number | Iron, Fe, 26 | ||||||||||||||||||||||||||||||||||||||||||||||||||||||||||||
Element category | Transition metals | ||||||||||||||||||||||||||||||||||||||||||||||||||||||||||||
Group , period , block | 8 , 4 , d | ||||||||||||||||||||||||||||||||||||||||||||||||||||||||||||
Appearance | shiny metallic with a grayish hue |
||||||||||||||||||||||||||||||||||||||||||||||||||||||||||||
CAS number | 7439-89-6 | ||||||||||||||||||||||||||||||||||||||||||||||||||||||||||||
EC number | 231-096-4 | ||||||||||||||||||||||||||||||||||||||||||||||||||||||||||||
ECHA InfoCard | 100.028.270 | ||||||||||||||||||||||||||||||||||||||||||||||||||||||||||||
Mass fraction of the earth's envelope | 4.7% | ||||||||||||||||||||||||||||||||||||||||||||||||||||||||||||
Atomic | |||||||||||||||||||||||||||||||||||||||||||||||||||||||||||||
Atomic mass | 55,845 (2) u | ||||||||||||||||||||||||||||||||||||||||||||||||||||||||||||
Atomic radius (calculated) | 140 (156) pm | ||||||||||||||||||||||||||||||||||||||||||||||||||||||||||||
Covalent radius | low-spin: 123 pm, high-spin: 152 pm | ||||||||||||||||||||||||||||||||||||||||||||||||||||||||||||
Electron configuration | [ Ar ] 3 d 6 4 s 2 | ||||||||||||||||||||||||||||||||||||||||||||||||||||||||||||
1. Ionization energy | 7th.902 468 1 (12) eV ≈ 762.47 kJ / mol | ||||||||||||||||||||||||||||||||||||||||||||||||||||||||||||
2. Ionization energy | 16.19920 (5) eV ≈ 1 562.98 kJ / mol | ||||||||||||||||||||||||||||||||||||||||||||||||||||||||||||
3. Ionization energy | 30th.651 (12) eV ≈ 2 957.4 kJ / mol | ||||||||||||||||||||||||||||||||||||||||||||||||||||||||||||
4. Ionization energy | 54.91 (4) eV ≈ 5 298 kJ / mol | ||||||||||||||||||||||||||||||||||||||||||||||||||||||||||||
5. Ionization energy | 75.00 (15) eV ≈ 7 236 kJ / mol | ||||||||||||||||||||||||||||||||||||||||||||||||||||||||||||
Physically | |||||||||||||||||||||||||||||||||||||||||||||||||||||||||||||
Physical state | firmly | ||||||||||||||||||||||||||||||||||||||||||||||||||||||||||||
Modifications | four | ||||||||||||||||||||||||||||||||||||||||||||||||||||||||||||
Crystal structure | α-iron: body-centered cubic
γ-iron: face-centered cubic |
||||||||||||||||||||||||||||||||||||||||||||||||||||||||||||
density | 7.874 g / cm 3 = 7874 kg / m 3 | ||||||||||||||||||||||||||||||||||||||||||||||||||||||||||||
Mohs hardness | 4.0 | ||||||||||||||||||||||||||||||||||||||||||||||||||||||||||||
magnetism | ferromagnetic | ||||||||||||||||||||||||||||||||||||||||||||||||||||||||||||
Melting point | 1811 K (1538 ° C) | ||||||||||||||||||||||||||||||||||||||||||||||||||||||||||||
boiling point | 3273 K (3000 ° C) | ||||||||||||||||||||||||||||||||||||||||||||||||||||||||||||
Molar volume | 7.09 · 10 −6 m 3 · mol −1 | ||||||||||||||||||||||||||||||||||||||||||||||||||||||||||||
Heat of evaporation | 354 kJ / mol | ||||||||||||||||||||||||||||||||||||||||||||||||||||||||||||
Heat of fusion | 13.8 kJ mol −1 | ||||||||||||||||||||||||||||||||||||||||||||||||||||||||||||
Speed of sound | 4910 m s −1 at 293.15 K. | ||||||||||||||||||||||||||||||||||||||||||||||||||||||||||||
Specific heat capacity | 449 J kg −1 K −1 | ||||||||||||||||||||||||||||||||||||||||||||||||||||||||||||
Work function | 4.5 eV | ||||||||||||||||||||||||||||||||||||||||||||||||||||||||||||
Electric conductivity | 11.7 · 10 6 A · V −1 · m −1 | ||||||||||||||||||||||||||||||||||||||||||||||||||||||||||||
Thermal conductivity | 80 W m −1 K −1 | ||||||||||||||||||||||||||||||||||||||||||||||||||||||||||||
Mechanically | |||||||||||||||||||||||||||||||||||||||||||||||||||||||||||||
Expansion coefficient | 11.8 · 10 −6 K −1 | ||||||||||||||||||||||||||||||||||||||||||||||||||||||||||||
Chemically | |||||||||||||||||||||||||||||||||||||||||||||||||||||||||||||
Oxidation states | 2, 3 , 4, 5, 6 | ||||||||||||||||||||||||||||||||||||||||||||||||||||||||||||
Normal potential | −0.44 V (Fe 2+ + 2 e - → Fe) | ||||||||||||||||||||||||||||||||||||||||||||||||||||||||||||
Electronegativity | 1.83 ( Pauling scale ) | ||||||||||||||||||||||||||||||||||||||||||||||||||||||||||||
Isotopes | |||||||||||||||||||||||||||||||||||||||||||||||||||||||||||||
|
|||||||||||||||||||||||||||||||||||||||||||||||||||||||||||||
For other isotopes see list of isotopes | |||||||||||||||||||||||||||||||||||||||||||||||||||||||||||||
NMR properties | |||||||||||||||||||||||||||||||||||||||||||||||||||||||||||||
|
|||||||||||||||||||||||||||||||||||||||||||||||||||||||||||||
safety instructions | |||||||||||||||||||||||||||||||||||||||||||||||||||||||||||||
|
|||||||||||||||||||||||||||||||||||||||||||||||||||||||||||||
As far as possible and customary, SI units are used. Unless otherwise noted, the data given apply to standard conditions . |
Iron is a chemical element with the symbol Fe ( Latin: ferrum , iron ) and the atomic number 26. It is one of the transition metals in the periodic table, the 8th subgroup ( iron-platinum group ), according to the new count, group 8 ( Iron group ). In terms of mass fraction ( ppmw ), iron is the fourth most common element in the earth's crust after oxygen , silicon and aluminum and the most common metal after aluminum .
Modern iron materials with a mass fraction of carbon of up to 2% are referred to as steel , with a higher content than cast iron . The distinction is based on the fact that cast iron cannot be plastically deformed, in particular it cannot be forged, while steel is deformable, i.e. forgeable. Older materials (before around 1870) with low carbon content are known as wrought iron and have greater impurities because they were manufactured differently than modern steel.
history
Evidence for the use of iron in various cultures through archaeological finds is relatively rare compared to the findings of bronze . On one hand, iron was used in the earliest periods of history only to a small extent, on the other hand tends iron in moist air, in the water and in the wet earth to corrosion remained, so many items not received. Only special circumstances or large dimensions of the object prevented the loss of such pieces.
etymology
In the past it was assumed that the Celtic and Germanic word for iron ( celt . * Isarnon , germ. * Isarna ) was borrowed from Illyrian . Because of the contrast to the softer bronze, a relationship between * isarnon and Latin ira = "anger, violence" was represented. The New High German word iron (from Middle High German īsen , and from īsīn "iron") is transformed into ahd. Īsa (r) n , from urgerm. * īsarnan , and this from gall. * īsarnon derived; an Illyrian origin, however, is now considered unlikely. * Isarnan and isarnon are used in German iron as well as in the other Germanic languages (Eng. iron , nordfries . joorn , westfries. izer , ndl. IJzer ,) as well as in Celtic (Bret. houarn , kymr. haearn , Irish and Scottish Gaelic iarann , Manx yiarn ).
In addition to its outstanding importance as a material, iron was used in alchemy , where it was associated with the symbol for Mars / masculinity ♂ .
Earliest use of meteorite iron
Before people in different cultures learned to extract iron from ore , they used the meteorite iron or meteorite iron , which was known before the actual " Iron Age " and is recognizable by its specific nickel content of around 5 to 18% . Due to its rarity, this "sky iron" ( ancient Egyptian : bj-n-pt = "iron of heaven") was correspondingly valuable and was mainly processed into cult objects and jewelry. In ancient Egypt, for example, jewelry pearls made of meteor iron with a nickel content of approx. 7.5%, dating back to around 3200 BC , were found in two graves from pre-dynastic times . Are dated. It was also possible to confirm the assumption made early on that a dagger found on the mummy of Pharaoh Tutankhamun was made from meteor iron. The oldest known finds from meteoric iron come from Mesopotamia , which the Sumerians living there called “urudu-an-bar” (= copper of the sky ). Among other things, a dagger with a blade made of meteor iron (10.8% Ni) and a gold-coated handle was discovered in the city of Ur , the manufacture of which dates back to around 3100 BC. Is dated.
Iron production from ore
For the beginnings of iron smelting see
Mediterranean and Asia Minor
The use of nickel-free, i.e. terrestrial iron must also have taken place early in Mesopotamia, as evidenced by a nickel-free iron dagger with a bronze handle from the period between 3000 and 2700 BC. BC, which was found in the ruins of Ešnunna near Tell Asmar in what is now Iraq. The records of the Hittites in the archives of Boğazkale (formerly Boğazköy ) in Central Anatolia show that iron was already known at the time of King Anitta (approx. 1800 BC) and that iron was smelted at least from approx. 1300 BC. Between 1600 and 1200 BC. Iron production remained largely a monopoly of the Hittite Empire and was a factor in its rise. From 1200 BC In the Levant, steel was produced by increasing the carbon content. The Hittites made mainly jewelry from iron, which was initially weighed up to eight times its weight in gold. In the late Hittite period, iron was so common that it was no longer listed in inventory lists with the precious metals, but with copper. However, there can be no question of a monopoly of the Hittites: Unique pieces made of terrestrial iron from the Middle and Late Bronze Age were also found in Greece and Cyprus, in Jordan, Lebanon, Israel and Egypt.
The Iron Age is generally believed to have started in the Middle East around 1200 BC. BC - not because iron played a significant role from this point on, but because the cultures of the Bronze Age collapsed within a very short time. The first centuries of the Iron Age are a " dark age " in this region , in which many cities were destroyed, long-distance trade collapsed and metal production almost fell asleep. Only from around 700 BC When cultures recovered from collapse, iron became more common again. Since 1200 BC In this region there is also known Damascus steel or melted damask , named after the city of Damascus , which has a very high carbon content of around 1.5% and a characteristic pattern when polished. This material is not only known in the Middle East, but also earlier in other regions, for example in South India, where it has been used since 300 BC at the latest. Is manufactured.
In ancient Egypt, iron was only smelted in the 6th century BC. Proven. Meteorite irons have been used since the Old Kingdom . This was referred to in later texts as bj3 n pt ("Iron of Heaven") and was mainly used to make amulets and model tools for the mouth opening ritual . A well-known find is a dagger blade as a burial object from Tutankhamun from approx. 1350 BC. BC, which, according to recent studies, very likely consists of meteoric iron. Another iron find in a grave near Abydos from the 6th dynasty (2347-2216 BC) could be determined as nickel-free and thus of terrestrial origin, but its earlier use could not be determined because the piece was completely rusted. An iron knife found in the joints of the Great Pyramid in 1837, which was initially dated to the 4th Dynasty, turned out to be a modern piece.
Furthermore, the Chalyber belonged to the peoples of the Mediterranean and Asia Minor who had already gained a good knowledge of the use of iron as a metallurgical material. Her name lived on in the Greek word for steel ( chalybs ), in contrast to common iron ( sideros ). The earliest traces of iron smelting on Greek territory were found in the form of iron slag from around 2000 BC. In Agia Triada on Crete.
In ancient Egypt and in Gerar (Palestine), iron smelting began around 1000 BC. Known for Gerar (evidenced by iron smelting furnaces and locally produced agricultural implements) and in China at least since the Han dynasty (206 BC to 222 AD).
Europe

The iron tents and spears that Count Gozzadini discovered in Etruscan tombs near Bologna in 1853 are among the oldest European pieces . They date from the 9th to 10th centuries BC. In Central Europe in general, the pre-Roman Iron Age is usually divided into the Hallstatt Period (800–450 BC) and the Latène Period (from 450 BC), with the first iron objects already appearing in the Late Bronze Age.
One of the oldest known iron finds in Germany is an iron rivet as a connection between a bronze lance tip and a wooden shaft, which was found in Helle (Ostprignitz) and dates from around 800 BC. BC. In the German-speaking countries, however, the La Tène period, which only began around 300 years later in the entire Celtic culture, marked a first high culture with numerous iron smelting sites and iron finds (e.g. in Siegerland and Teltow ). The Bronze Age cultures persisted in Northern Germany during the Hallstatt Period. South of the Alps, on the other hand, there was a high culture, the Etruscans, who produced large quantities of bronze and iron and whose products also reached Central Europe. Among other things, they mined an iron skarn on Elba .
Racing furnaces or racing works with associated forges were widespread in Europe until the 18th century . Until the late Middle Ages, they were the only method of making malleable iron. From this point on, “ freshening ” allowed a reduction in the carbon content in raw or cast iron. Liquid pig iron was not produced with this process, however, as a racing furnace could only reach temperatures between 1000 and 1200 ° C, but the melting point of pure iron is 1538 ° C (melting point of pure cementite , Fe 3 C: 1250 ° C). The development of blast furnaces and thus cast iron did not take place until later in Europe. The earliest cast iron pieces were discovered in Sweden ( Lapphyttan and Vinarhyttan ) and dated to 1150-1300 . With the cast cannonball (from 1400), cast iron processing spread like the military campaigns across Europe.
When the dwindling forests in Europe could no longer meet the growing need for charcoal for iron production, alternatives were sought. In 1709, Abraham Darby in Great Britain was the first to use coal (more precisely the coal product coke ) as an alternative. In Germany it was not possible to operate a blast furnace with coke until 1796. This change, together with the invention of the steam engine, is considered to be the beginning of the industrial revolution . The smelting works produced cast iron and wrought iron . With the introduction of the puddling process around 1784, it was possible to replace the previously common charcoal with the cheaper hard coal.
Iron use and finds outside Europe and Asia Minor
There was also a very old tradition of iron production in Africa, which began around 3,000 years ago. The African metallurgists were very eager to experiment and innovative, the construction methods and shapes of the furnaces show a variety that cannot be found on other continents. With a few exceptions - namely Mauritania and Niger - there was no Copper or Bronze Age at most of the sites south of the Sahara that preceded iron smelting: the Neolithic was immediately followed by the Iron Age. Archaeologists dated the oldest known smelting furnace in Africa, which was discovered in the Termite massif in Niger , to 800 BC. Other sites for iron processing were discovered, for example, in Walalde in Senegal , in the Central African Republic, in Rwanda , in Taruga , the region around Nsukka and on the northern edge of the Mandara Mountains in the border area between Nigeria and Cameroon .
From the 7th century BC In addition to the cultures in the Middle East and parts of Europe, iron was also known in many other regions: for example in India and Sri Lanka, in China, in Eastern Europe with the Scythians and also south of the Sahara in Africa. In Colchis , today's Western Georgia, in the 7th century was an important iron producer. About 400 ovens have been found there in which hematite and magnetite were smelted.
In China, the first experience with iron was gained from meteorite iron. The first archaeological traces of wrought iron can be found in the northwest, near Xinjiang , from the 8th century BC. It is believed that these products, created using Middle Eastern methods, came to China through trade. That changed in the late Zhou period in the 5th century BC. With a massive production of cast iron in blast furnaces. China continuously developed the technology and remained a very innovative center of metallurgy.
Iron objects and larger iron stores in the ruins of Khorsabad were found in the tombs of Turan , a region that stretched across eastern Iran, southern Afghanistan and southwest Pakistan . Were discovered by Victor Place along with about 160,000 kg iron bars rings and chain parts. Layard found iron weapons such as helmets, spears and daggers during his excavations in Nimrud . Famous is the Iron Column in Delhi, a seven meter high wrought iron pillar from the 4th / 5th. Century.
In Australia and the surrounding populated islands of Polynesia, however, the use of iron was unknown until it was discovered by European researchers. Even in the otherwise high-ranking culture of the Incas and Aztecs of Central and South America, gold, silver, copper and bronze of good quality and great craftsmanship were processed, but iron only in small quantities and only meteoric iron.
Occurrence
Iron is in ninth place in the series of relative abundance of elements related to silicon in the universe with 8.7 · 10 5 atoms per 1 · 10 6 silicon atoms. The fusion of elements in stars ends with iron, since during the fusion of higher elements no more energy is released but has to be expended (see nucleosynthesis ). Heavier elements are created endothermically in supernova explosions , which are also responsible for the scattering of the matter created in the star.
In the sequence of the element abundance according to the mass fraction, iron is in 2nd place in the entire earth (28.8%), 4th in the earth's envelope (4.70%) and 4th in the continental crust (5, 63%); in sea water it is only contained to 0.002 mg / L. Iron, along with nickel, is probably the main component of the earth's core . Presumably driven by thermal forces, convection currents of liquid iron in the outer core create the earth's magnetic field .
Most of the iron in the earth's crust is associated with various other elements and forms several hundred different iron minerals. An important and economically significant class are the iron oxide minerals such as hematite (Fe 2 O 3 ), magnetite (Fe 3 O 4 ) and siderite (FeCO 3 ), limonite (Fe 2 O 3 · n H 2 O) and goethite (FeO · OH ), which are the main ores of iron. Many igneous rocks also contain the sulfide mineral pyrrhotite and the nickel-iron mineral pentlandite, which is intergrown with it . During weathering , iron tends to leach from sulfide deposits as sulfate and from silicate deposits as hydrogen carbonate . Both are oxidized in aqueous solution and precipitate in the form of iron (III) oxide at a slightly increased pH value .
Large deposits of iron are ribbon ores , a type of rock made up of repeated thin layers of iron oxides that alternate with ribbons of low-iron shale and chert . The ribbon ores were mainly deposited between 3700 million years ago and 1800 million years ago (the most recent were formed 350 million years ago) by the reaction of iron with the oxygen produced by cyanobacterial photosynthesis .
Materials that contain finely ground iron (III) oxides or oxide hydroxides such as ocher have been used as yellow (ocher), red (hematite), brown (umber) and black (magnetite) pigments since prehistoric times . They also contribute to the color of various rocks and clays , including entire geological formations such as the Painted Hills in Oregon and the red sandstone . By iron sandstone in Germany and Bath Stone UK iron compounds for the yellowish color of many historical buildings and sculptures are responsible. The proverbial red color of the surface of Mars comes from a regolith rich in iron oxide .
The iron sulfide mineral pyrite ( FeS 2 ) contains considerable amounts of iron. However, it is mainly used for the production of sulfuric acid , whereby the gravel burns that occur during production have a high iron content. However, it is only possible to use these for iron production with modern methods, since residues of the sulfur have to be removed, which make the iron brittle. In fact, iron is so widespread that production generally focuses only on ores with very high iron content.
Iron in ores
The first deposits to be mined were turf iron stone and exposed ores. Today mainly magnetite ( Fe 3 O 4 ), hematite and siderite are mined. The largest iron ore deposits are found in the so-called Banded Iron Formations (BIF, banded iron ore or band ore ), which are also known as taconite or itabirite and contain iron mainly in the minerals hematite and magnetite.
Iron as a mineral
Rare iron in nature and dignified before, usually in the form of small bubbles or bulges in the surrounding rock, as well as massive mineral aggregates up to 25 tonnes in weight, and therefore as a mineral recognized. The International Mineralogical Association (IMA) lists it according to the systematics of minerals according to Strunz (9th edition) under the system no. "1.AE.05" (elements - metals and intermetallic compounds - iron-chromium family) ( 8th edition : I / A.07-10 ). The systematics of minerals according to Dana , which is also common in English-speaking countries , leads the element mineral under the system no. "1.1.11.0".
So far (as of 2010), solid iron has been found at 120 sites worldwide, although the vast majority consists of meteoritic iron finds of the Kamacite variety .
Iron crystallizes in the cubic crystal system , has a Mohs hardness between 4 and 5 and a steel-gray to black color ( iron black ) , depending on the formation conditions and degree of purity . The line color is also gray.
Because of the reaction with water and oxygen ( rusting ), solid iron is not stable. Therefore, there occurs alloy with nickel either as Kamacite (4 to 7.5% Ni) or taenite (20 to 50% Ni) only in iron meteorites on and in basalts , in which there is sometimes a reduction comes from iron-containing minerals. Iron with a lower nickel content is a variety of the same and is known under the name Josephinite , but this name is also a synonym for the mineral Awaruit (Ni 3 Fe).
Iron ores, on the other hand, are found comparatively frequently; Important examples are the minerals magnetite ( magnetic iron ore Fe 3 O 4 ), hematite ( hematite , Fe 2 O 3 ), pyrrhotite ( pyrrhotite , FeS), pyrite ( iron pyrite , FeS 2 ), siderite ( siderite , FeCO 3 ) and as rock applicable limonite ( limonite , Fe 2 O 3 · n H 2 O). The sedimentary rock iron oolite , sometimes referred to as iron stone, consists of iron hydroxide minerals, cemented with clayey or calcareous binders. The minerals chlorite , glauconite and pyrite are of less industrial interest, but are found fairly frequently in nature . A total of 1424 iron minerals are currently (as of 2010) known.
Iron in foods
Many foods contain traces of iron. For example, oats (peeled) contain 58 mg / kg, barley (peeled) and rye 28 mg / kg, wheat 33 mg / kg, cocoa (slightly de-oiled) 125 mg / kg, spinach 38 mg / kg, potatoes 5 mg / kg, Parsley 55 mg / kg, apple 2 to 9 mg / kg, beef 21 mg / kg, beef liver 70 mg / kg, beef kidney 11 mg / kg, pig liver 154 mg / kg, pork 18 mg / kg, pig kidney 100 mg / kg, Pig blood 550 mg / l, bovine blood 500 mg / l, cow's milk 0.5 mg / l and egg yolk 60 to 120 mg / l.
advancement
The People's Republic of China is 711 million tons (60 percent) in 2017, the most important by far Country of pig iron, followed by Japan 78 million tonnes (6.6 percent), India 66 million tonnes (5.6 percent) and Russia 52 million Tons (4.4 percent). The four states together had a share of 77.5 percent in world production of 1170 million tons. In Europe, other important producers were the Ukraine , Germany and France .
Around 2.4 billion tons of iron ore were mined worldwide in 2017. The most important iron ore suppliers were Australia , followed by Brazil , the People's Republic of China, India and Russia. Together they had a share of 80.8 percent of world production. In addition, new iron is made from scrap.
rank | country | Production (in million t ) |
rank | country | Production (in million t) |
|
---|---|---|---|---|---|---|
1 | People's Republic of China | 700.7 | 11 | Taiwan | 14.9 | |
2 | Japan | 80.2 | 12 | Turkey | 12.5 | |
3 | India | 77.3 | 13 | France | 9.7 | |
4th | Russia | 51.9 | 14th | Canada | 7.6 | |
5 | South Korea | 46.3 | 15th | United Kingdom | 6.1 | |
6th | Brazil | 35.0 | 16 | Netherlands | 6.1 | |
7th | Germany | 27.3 | 17th | Italy | 6.0 | |
8th | United States | 22.3 | 18th | Austria | 5.6 | |
9 | Ukraine | 21.9 | 19th | Mexico | 5.2 | |
10 | Iran | 18.3 | 20th | South Africa | 5.0 |
Development of global iron ore production (in millions of tons) ![]() |
Development of worldwide pig iron production (in millions of tons) ![]() |
Extraction and presentation

Ore mining and processing
Iron ore is mainly extracted in open-cast mining and less often in civil engineering ( underground mining , as in the Kiruna iron ore mine ). Where the iron ore deposits recognized as being worthy of mining are openly exposed, the ore can be extracted in less laborious open-cast mining. Most of the iron ore is mined in Brazil, Australia, China, India, the USA and Russia.
In recent years, these countries have displaced the originally most important iron ore producing countries such as France, Sweden and Germany, whose last iron ore mine in Upper Palatinate was closed in 1987.
For technological and economic reasons, the ores used for processing in blast furnaces should have uniform properties from a chemical and physical point of view. Accordingly, the coarse ores obtained during mining have to be broken, ground and sieved and the ores that are too fine have to be made lumpy. This is known as ore preparation. Irregularities in the ores of one or several mining sites are compensated for by mixing the ores on so-called mixed beds. Only a small part of the ores can be used as lump ore directly in the blast furnace . The main part of the iron ore is present as fine ore and must be made lumpy for use in the blast furnace, since the fine ore would greatly impair or even prevent the air supply (wind) in the blast furnace. The most important processes for this are sintering and pelleting . In Germany ores are mainly made into pieces by sintering. In other countries, for example in the USA, more pellets are used, whereby the grain size resulting from processing is decisive for the selection of the process. Sintering requires a grain size of more than 2 mm, while ores that are even more finely ground are pelletized.
In the sintering plants, coarser ore grains are sorted according to their size and sintered. For this purpose, small ore grains, together with lime aggregates, have to be placed on gas-fired, motor-driven traveling grids (grate conveyor belts) and melted through intense heating and thereby "baked" (sintered). Very fine ore is ground into a fine powder, which is often necessary to separate gangue. Then it is intensively mixed with limestone, fine-grain coke (coke breeze) and water and placed on a motor-driven traveling grate. Gases are extracted from below through the traveling grate. It is lit from above and a burning front moves from top to bottom through the mixture, which is briefly melted (sintered). When pelletizing, binders, aggregates and water are used to create a mixture, which is then rolled onto pelletizing plates to form small balls (green pellets) with a diameter of 8 to 18 mm. These are burned into pellets with gas firing at 1000 ° C on a traveling grate, in shaft ovens or rotary kilns. Sinter is not easy to transport and is therefore produced in the iron and steel works, pellet plants are mostly operated near the ore mines.
Iron production in the blast furnace

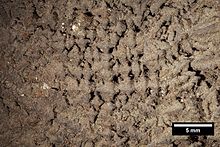
The iron is obtained by chemical reduction of the iron oxide of the oxidic iron ores (or sulfidic iron ores after their roasting with atmospheric oxygen) and carbon (coke). Pig iron is produced almost exclusively in tall blower shaft furnaces (blast furnaces). Only in countries with cheap hydropower plants and expensive coal does generation in electric ovens play a limited role. Coke and ore are poured into the furnace alternately in layers at the top of the furnace. For this purpose, two bunkers are usually arranged above the furnace vessel, which serve as gas locks between the furnace vessel and the environment. At the very top there is a rotary chute within the furnace vessel, with which the material is distributed over the loading surface in a spiral shape. The layers of coke in the lower area of the furnace, when the ore becomes plastic, maintain that process gas can flow through the bed (coke window).
The insert sinks in the furnace shaft and is dried, heated, the iron oxides reduced and finally melted ( redox reaction ) by the rising process gas , which is made up of carbon monoxide and nitrogen and has a temperature of around 1600 to 2200 ° C (at the injection point ). The process gas is generated by blowing air preheated to around 900 to 1300 ° C into the furnace through blow molding (water-cooled copper nozzles) . The oxygen in the air burns with coke to form carbon monoxide. The entire process takes about eight hours.
The so-called "indirect reduction" takes place in the temperature zone between 500 and 900 ° C. The various iron oxides react with carbon monoxide or hydrogen in three stages , until finally metallic iron is present:
or.
The more ferrous magnetite is formed from hematite .
or.
Of magnetite produced wustite .
or.
Metallic iron is made from wüstite and accumulates in the blast furnace below.
In the temperature range from 900 to 1600 ° C, there is also a "direct reduction" with carbon:
The furnace gas coming out of the blast furnace is freed from the dust and is used to operate the wind heaters, fans, pumps, lighting, gas cleaning and transport devices required for the blast furnace process. The surplus is used for steel mill operations or other industrial purposes.
In addition to the liquid iron, the furnace also produces liquid slag . Since the melting point of a mixture of SiO 2 and Al 2 O 3 is too high to form a slag that is liquid at 1450 ° C, aggregates are used to produce more easily meltable calcium aluminum silicates to lower the melting point . Is it z. B. to alumina and silicic acid-containing gangues, which is usually the case, one suggests accordingly calcareous, d. H. basic components (e.g. limestone , dolomite ). In the case of calcareous gaits, conversely, alumina and silicic acid-containing, i.e. H. acidic aggregates (e.g. feldspar , clay slate ) are added. The iron and the slag are mixed together in the blast furnace, have a temperature of about 1450 ° C and are drawn off through a tap hole that is opened about every two hours by drilling and closed after about an hour by plugging with a ceramic mass. Iron and slag are separated outside the furnace. The iron is filled in transport pans and brought to the steelworks .
The iron is liquid at 1450 ° C because the carbon dissolved in the iron lowers the melting point . The slag is atomized with water. It solidifies as a fine-grained glass (slag sand) due to the quenching . This slag sand is finely ground and used as a concrete additive (filler) . A blast furnace produces around 200 to 300 kg of slag per ton of iron.
Ore and coke contain silicon dioxide ( quartz sand , silicates ) SiO 2 and aluminum oxide Al 2 O 3 as the main impurities . A small part of the silica is reduced to silicon , which is dissolved in the iron. The rest together with the aluminum oxide form the slag (calcium aluminum silicates ).
The iron in the blast furnace ( pig iron ) only has an iron content of around 95%. It contains 0.5 to 6% manganese, as well as too much carbon (2.5 to 4%), sulfur (0.01 to 0.05%), silicon (0.5 to 3%) and phosphorus for most applications (0 to 2%). Usually, therefore , desulphurisation is first carried out in the steelworks by blowing in calcium carbide , magnesium or quicklime , whereby optimal desulphurisation is a prerequisite for the production of spheroidal graphite cast iron . If pig iron is cooled very slowly, e.g. B. in sand molds (“ingot beds”), the dissolved carbon separates out as graphite and “gray pig iron” is obtained (gray fracture surface, melting temperature around 1200 ° C). Another condition for this is that the silicon content predominates over the manganese content (> 2% Si; <0.2% Mn). With faster cooling, z. B. in iron shells ("chill molds"), the carbon remains as iron carbide in the pig iron, so that a "white pig iron" (white fracture surface, melting temperature around 1100 ° C, mainly used for the production of steel) is created. A predominance of the manganese content (<0.5% Si;> 4% Mn), which counteracts the precipitation of graphite, is also essential here.
Iron production without a blast furnace
Blast furnaces have a large material and energy requirement, which cannot always be provided if the raw material and energy conditions are unfavorable. Because of this and because of environmental concerns, alternative methods of processing iron have been developed. In these, the existing iron ores are to be reduced with little or no use of coke or, alternatively, with hard coal , lignite , crude oil or natural gas . In the majority of the processes referred to as "direct iron reduction", the pig iron produced is obtained in solid, porous form, which is referred to as sponge iron or "direct" iron and is suitable for steel production.
Two main reactions include the direct reduction process : When methane ( natural gas ) and oxygen (alternatively water vapor or carbon dioxide) are used, this is partially oxidized (with heat and a catalyst ):
The iron ore is then treated with these gases in a furnace , resulting in solid sponge iron :
Silica is removed by adding a limestone flux as described above.
Well-known direct reduction processes, sorted according to the respective reduction vessel, include:
- Iron production in the shaft furnace :
- Wiberg process , developed around 1918 in Sweden
- Purofer process , developed in Oberhausen
- Midland Ross Process / Midrex Process developed by Midland Ross Corporation in Cleveland , Ohio
- All three processes use a more or less short shaft furnace and, as input materials, iron-rich lump ores, sinter or pellets, which are preheated and introduced at the furnace head. A 1000 ° C hot reducing gas mixture of carbon monoxide (CO), hydrogen (H 2 ), carbon dioxide (CO 2 ), water (H 2 O) and, if necessary, methane (CH 4 ) is blown into the furnace base . The sponge iron produced has a purity of 85 to 95%.
- Corex process
- Iron production in the retort :
- Höganäs process , developed in 1908 by E. Sieurin in Höganäs , Sweden
- HyL process , developed in 1957 by the company H ojalata- y - L amina SA in Monterry , Mexico
- Very rich iron ore concentrates are placed here in ceramic retorts or muffles and reduced either with fine-grain coal, coke breeze and limestone or with natural gas. The sponge iron produced has a purity of 80 to 95% and is used either for the production of special steels or as iron powder for powder metallurgy .
- Iron production in a rotating vessel:
- Krupp sponge iron process
- RN process , developed by the R ePublic Steel Corporation and the N ational Lead Corporation
- SL process , developed by the S teel Company of Canada and the L urgi Society for Chemistry and Metallurgy
- Lump ore or pellets are introduced here together with limestone or dolomite in rotary kilns up to 110 m long , which are heated to up to 1050 ° C with lignite, coke oven gas or heating oil. Sponge iron is produced with a purity of 85 to over 90%.
- Dored process (Domnarf reduction process), developed at Stora Kopparbergs bergslag in Sweden
- Preheated iron ore is brought into a rotary kiln with coal or coke on a pig iron sump. By blowing in pure oxygen , the carbon monoxide contained in the reducing gas is burned to carbon dioxide and the rotary kiln is heated to approx. 1300 to 1350 ° C. Liquid pig iron is produced.
- Iron production in the fluidized bed reactor
- H-Iron process , developed by Hydrocarbon Research Inc. (USA)
- FIOR (Fluid Iron Ore Reduction) process developed by Standard Oil Company , New York
- Sponge iron is produced from fine-grain iron ores, which are whirled up and reduced either with injected hydrogen, natural gas or refinery residual gas .
- Finex process
- Iron production in the electric furnace
- The Tysland Hole process and the Demag process manage without preheating and pre-reduction of the input materials .
- Elektrokemisk processes and Strategic Udy processes , on the other hand, require preheating and prereduction of the ore using rotary kilns.
- However, iron production in electric furnaces is only worthwhile if electricity can be provided in sufficient quantities and at low cost. Depending on the quality of iron ore and carbon carriers, the energy consumption is between 2000 and 2500 kWh per ton of pig iron.
Thermite reaction
The ignition of a mixture of aluminum powder and iron (III) oxide produces liquid metallic iron via the thermite reaction:
The reaction is of no importance for the production of iron from ore, among other things because the aluminum required requires a considerable amount of electrical energy for its production. The aluminothermic welding uses the remaining energy of the liquid iron after the reduction of the iron oxide by means of aluminum for fusion welding and the like. a. of railroad tracks .
Steel production
In the γ-iron, carbon is up to 2.06% soluble, steel contains 0 to 2% of carbon, it is malleable and rollable, but only from 0.5% carbon it is curable . If the value is lower, it is non-hardenable steel or wrought iron.
For steelmaking different were procedures developed, including Pfützenöfen , Bessemer converter , stoves with open fireplace, Sauerstoffbasisöfen and arc furnaces . In all cases the goal is to oxidize some or all of the carbon along with other impurities . On the other hand, other metals can be added to make alloy steels.
Depending on the process, any desulphurisation slag that may have arisen is drawn off or tapped and the pig iron is then used to produce steel in a converter ( oxygen blowing process , wind-freshening process such as the Thomas process , stove-cooling process such as the Siemens-Martin process ) with the addition of quicklime and blowing in air or blow oxygen in an oxidizing manner. In this process, silicon is burned to silicon dioxide and carbon to carbon dioxide. The phosphorus is bound as calcium phosphate . The liquid iron then has a temperature of around 1600 ° C. It contains so much oxygen that carbon monoxide bubbles form from remaining carbon when it solidifies. This is undesirable with the continuous casting that is mostly used today . When the steel is tapped from the converter into the ladle, aluminum is therefore added in order to bind the oxygen as aluminum oxide. If there are high demands on the quality of the steel, the converter process is followed by further process steps, such as B. a vacuum treatment ( secondary metallurgy ).
Alternatively, pig iron can also be processed into steel (with up to 2% carbon ) by cementation using other methods such as the puddling process or tempering, as well as wrought iron (commercially available pure iron) .
properties
Physical Properties



Chemically pure iron is a silvery white, relatively soft, ductile, very reactive metal with a density of 7.873 g / cm 3 , which melts at 1535 ° C and boils at 3070 ° C.
The average iron atom has about 56 times the mass of a hydrogen atom . The atomic nucleus of the iron isotope 56 Fe has one of the largest mass defects and thus one of the highest binding energies per nucleon of all atomic nuclei. That is why it is considered to be the final stage in the production of energy by nuclear fusion in the stars . However, the absolute highest mass defect has 62 Ni , followed by 58 Fe, and only in third place follows 56 Fe.
At room temperature, the allotropic modification of pure iron is ferrite or α-iron. This modification crystallizes in a body-centered cubic crystal structure ( tungsten type) in the space group Im 3 m (space group no. 229) with the lattice parameter a = 286.6 pm and two formula units per unit cell . This modification is stable below 910 ° C. Above this temperature it transforms into the γ-modification or austenite . This has a face-centered cubic structure ( copper type) with the space group Fm 3 m (no. 225) and the lattice parameter a = 364.7 pm. A third structural change takes place at 1390 ° C, above this temperature up to the melting point at 1535 ° C, the body-centered cubic δ-ferrite is stable again. Phase transitions also take place at high pressure : at pressures of more than about 10 to 15 GPa and temperatures of at most a few hundred degrees Celsius, α-iron is converted into ε-iron, the crystal lattice of which is a hexagonal close packing of spheres (hcp); At higher temperatures up to the melting point, a corresponding conversion of γ-iron to ε-iron takes place, the pressure of the phase transition increasing with temperature. In addition, there may be another phase transition from ε-iron to β-iron, which is around 50 GPa and more than 1500 K; however, the existence of this β phase is controversial, and there are also various findings on its crystal structure, including: a. an orthorhombic or a double hcp structure. These transformations are also called the "polymorphism of iron".
The lack of a β-phase in the standard nomenclature of the iron allotropes is due to the fact that it was previously assumed that the change in magnetism at the Curie point at 766 ° C from ferro- to paramagnetism is accompanied by a structural change and thus a further modification between 766 and 910 ° C exists, which has been referred to as β-modification or β-iron. However, after more precise measurements, this turned out to be wrong.
The solubility of carbon in α-iron is very low and is a maximum of 0.018% at 738 ° C, as can be seen from the iron-carbon diagram . Much more carbon (up to 2.1% at 1153 ° C) can dissolve in γ-iron. In molten iron, the solubility of carbon at 1153 ° C is about 4.3%, although this increases with increasing temperature.
The melting point of iron is only well determined experimentally for pressures up to about 50 GPa. At higher pressures, different experimental techniques give very different results. Various studies localize the γ-ε triple point at pressures that differ by several dozen gigapascals, and at the melting temperatures under high pressure they are 1000 K and more apart. In general, molecular dynamic model calculations and shock experiments result in higher temperatures and steeper melting curves than static experiments in diamond anvil cells.
The spectrum of iron shows spectral lines in all spectral ranges. In astronomy, more precisely in X-ray astronomy, the strong emission lines of neutral iron in the X-ray range are of great interest. Astronomers observe them in active galactic nuclei , X-ray binary stars , supernovae and black holes .
Magnetic properties

1. steel sheet , the second magnetic steel sheet ,
the third cast steel , 4th tungsten steel ,
the fifth magnetic steel , 6. Cast iron , 7th nickel , 8. Cobalt , 9. magnetite
Below its Curie point of 770 ° C, α-iron changes from paramagnetic to ferromagnetic : The spins of the two unpaired electrons in each atom generally align themselves with the spins of its neighbors, creating an overall magnetic field. This happens because the orbitals of these two electrons (d z 2 and d x 2 - y 2 ) do not point to neighboring atoms in the lattice and are therefore not involved in the metal bond .
In the absence of an external source of magnetic field, the atoms will spontaneously split into magnetic domains about 10 microns in diameter so that the atoms in each domain have parallel spins but other domains have a different orientation. Thus, a macroscopic piece of iron has a total magnetic field close to zero.
The application of an external magnetic field causes the domains magnetized in the same general direction to grow at the expense of neighboring domains facing in other directions, thereby increasing the external field. This effect is used in electrical devices that have to channel magnetic fields, such as B. electrical transformers , magnetic recording heads and electric motors . Impurities, lattice defects or grain and particle boundaries can "fix" the domains at the new positions, so that the effect persists even after the external field has been removed and the iron object thus becomes a permanent magnet .
Some iron compounds, such as ferrites and the mineral magnetite , a crystalline form of mixed iron (II, III) oxide, show a similar behavior (although the atomic mechanism, ferrimagnetism, is somewhat different). Magnetite pieces with natural permanent magnetization ( magnetic iron stones ) were the earliest compasses for navigation. Magnetite particles were used extensively in magnetic recording media such as core memories , magnetic tapes , floppy disks, and disks until they were replaced by cobalt-based material .
Chemical properties
Oxidation states of iron | |
---|---|
−2 | [Fe (CO) 4 ] 2− , [Fe (CO) 2 (NO) 2 ] |
−1 | [Fe 2 (CO) 8 ] 2− |
0 | Fe (CO) 5 , Fe 2 (CO) 9 , Fe 3 (CO) 12 |
+1 | [Fe (H 2 O) 5 NO] 2+ |
+2 | FeCl 2 , FeSO 4 , FeO , Fe (OH) 2 , ferrocene |
+3 | FeCl 3 , Fe 2 O 3 , Fe (NO 3 ) 3 , FeO (OH) |
+4 | Li 2 FeO 3 , BaFeO 3 |
+5 | FeO 4 3− |
+6 | K 2 FeO 4 , BaFeO 4 |
Iron is resistant to dry air, to dry chlorine as well as to concentrated sulfuric acid , concentrated nitric acid and basic agents (except hot sodium hydroxide solution ) with a pH value greater than 9. This resistance is due to the presence of a continuous oxide protective skin. In non-oxidizing acids such as hydrochloric acid and dilute sulfuric or nitric acid, iron dissolves rapidly with the development of hydrogen .
It is also decomposed by water above 500 ° C and by hot alkalis in a reversible reaction:
Concentrated sodium hydroxide solution attacks iron even in the absence of air, this goes into solution with hydroxoferrate (II) formation. In humid air and in water that contains oxygen or carbon dioxide, iron is easily oxidized to form iron oxide hydrate ( rust ). Since the resulting oxide layer is soft and porous, the rusting process can proceed unhindered. Seawater containing electrolytes or water containing SO 2 is particularly aggressive in industrial areas. If iron is heated in dry air, a thin layer of iron (II, III) oxide (Fe 3 O 4 , hammer blow ) is formed, which is strongly colored ( tempering ). Very finely divided, pyrophoric iron reacts with oxygen from the air at room temperature, causing a fire. Burning steel wool reacts vigorously in moist chlorine gas to form brown iron (III) chloride vapors. If a mixture of iron and sulfur powder (in a weight ratio of 7: 4) is heated, mainly iron (II) sulfide is formed . Iron also forms phosphides , silicides , sulfides or carbides with other non-metals such as phosphorus , silicon , sulfur and carbon at elevated temperatures .
Smell of iron
Pure iron is odorless. The typical smell, classified as metallic, when you touch iron objects, is caused by a chemical reaction of substances from sweat and the fat of the skin with the divalent iron ions that are formed.
One of the most important fragrance carriers is 1-octen-3-one , which, even when diluted, has a mushroom-like metallic smell. This makes up about a third of the odor. The rest are other aldehydes and ketones. The preliminary stage of odorous substances are lipid peroxides. These occur when skin oils are oxidized by certain enzymes or non-enzymatic processes (e.g. the UV component of light). These lipid peroxides are then broken down by the divalent iron ions, forming the fragrances. The divalent iron ions result from corrosion of the iron when it comes into contact with hand perspiration , which contains corrosive organic acids and chlorides.
When blood is rubbed on the skin, a similar odor develops, as blood also contains iron (II) ions and these form odorous substances through similar reactions.
Heavily rusted objects (including the formation of iron (III) compounds) do not emit a metallic odor when they are touched, as everyday experience teaches. In agreement with this is the observation that the decomposition of lipid peroxides is not catalyzed by iron (III) ions.
Isotopes
Iron has 27 isotopes and two core isomers , four of which are naturally occurring, stable isotopes . They have the relative frequencies: 54 Fe (5.8%), 56 Fe (91.7%), 57 Fe (2.2%) and 58 Fe (0.3%). The isotope 60 Fe has a half-life of 2.62 million years, 55 Fe of 2.737 years and the isotope 59 Fe one of 44.495 days. The remaining isotopes and the two core isomers have half-lives between less than 150 ns and 8.275 hours. The existence of 60 Fe at the beginning of the formation of the planetary system was confirmed by the evidence of a correlation between the abundances of 60 Ni , the decay product of 60 Fe, and the abundances of the stable Fe isotopes in some phases of some meteorites (for example in the meteorites Semarkona and Chervony Kut ). It is possible that the energy released during the radioactive decay of 60 Fe, in addition to the atomic decay energy of the radioactive 26 Al , also played a role in the melting and differentiation of the asteroids immediately after their formation about 4.6 billion years ago. Today the originally present 60 Fe has decayed into 60 Ni. The distribution of nickel and iron isotopes in meteorites makes it possible to measure the abundance of isotopes and elements during the formation of the solar system and to identify the conditions prevailing before and during the formation of the solar system.
Of the stable iron isotopes, only 57 Fe has a nuclear spin other than zero . It is therefore suitable for Mössbauer spectroscopy .
use
In contrast to carbon-containing iron, chemically pure iron has only a subordinate technical importance and is used as a material for catalysts and the like. a. the Haber-Bosch process or the Fischer-Tropsch synthesis .
Most of the iron produced is the main component of steel and cast iron . With 95 percent by weight of metals used, iron is the most widely used worldwide. The reason for this lies in its wide availability, which makes it quite inexpensive, and in the fact that steel achieves excellent strength and toughness when it forms alloys with other metals such as chromium, molybdenum and nickel, which make it one for many areas of technology Make base material. It is used in the manufacture of land vehicles, ships and in the entire construction sector ( reinforced concrete construction , steel construction ). Other areas of application are packaging ( cans , bundles, containers, buckets, strips), pipelines, pressure vessels, gas bottles and springs . Various steels are used industrially; in Germany around 7,500 varieties are standardized.
Iron is used as a material in the following forms:
- Pig iron contains four to five percent carbon and various proportions of sulfur , phosphorus and silicon . It is an intermediate product in the manufacture of cast iron and steel.
- Cast iron contains over 2.06% carbon and other alloying elements , such as silicon and manganese , which improve castability . Cast iron is very hard and brittle. It usually cannot be plastically deformed (forged), but it can be poured very well because of its comparatively low melting point and the low viscosity of the melt.
- Steel contains a maximum of 2.06% carbon. In contrast to cast iron, it is forgeable . The mechanical properties of the steel can be varied within wide limits by alloying and a suitable combination of thermal treatment (see hardening ) and plastic forming ( cold rolling ).
Iron (along with cobalt and nickel ) is one of those three ferromagnetic metals which, with their properties, allow the large-scale use of electromagnetism and the like. a. in generators , transformers , chokes , relays and electric motors . It will be pure or u. a. Alloyed with silicon, aluminum, cobalt or nickel (see Mu-Metal ) and serves as a soft magnetic core material for guiding magnetic fields, for shielding magnetic fields or for increasing inductance. It is produced in bulk and in the form of sheet metal and powder ( powder cores ).
Iron powder is also used in chemistry (for example as a catalyst in ammonia synthesis ) and is used in appropriate types of tape for magnetic data recording. Iron wire was used to record data in the wire tone device and is u. a. used to manufacture wire ropes .
In medicine, iron-containing preparations are used as anti-anemics , causally in the treatment of iron deficiency anemia and additively in the treatment of anemia caused by other causes .
Biological importance
Part of living beings
Iron is an essential trace element for almost all living things, especially for blood formation in animals.
In plant organisms it influences photosynthesis as well as the formation of chlorophyll and carbohydrates , since in plants iron-containing enzymes are involved in photosynthesis, chlorophyll and carbohydrate formation. In plants, iron occurs almost exclusively in the form of free inorganic iron ions. In the nitrogenase (nitrogen fixation) iron is also included (as well as the element molybdenum ). There are plants that make iron ions bioavailable from calcareous soils through phyto- siderophores (iron-complexing compounds) in combination with the local release of hydrogen ions, during which Fe 3+ is reduced to Fe 2+ and then complexed. In plants, iron, like in the liver, is bound to phytoferritins. In plants it is absolutely necessary for chlorophyll synthesis. If the iron content in plants falls below a critical minimum, the green parts of the plant become pale and yellow ( chlorosis ).
In fungi (such as Ferrichrome , a siderophore with growth-promoting properties), bacteria (in Streptomyces is ferrioxamine B formed) and sea worms in them (and in Lingula the non-heme iron protein comes Hemerythrin ago) play iron compounds play an important role.
In the body of humans and animals it is oxidized as iron 2+ and iron 3+ . As the central atom of the cofactor heme b in hemoglobin and myoglobin and in cytochromes , it is responsible for oxygen transport and storage as well as electron transfer in many animals and humans. In these proteins it is surrounded by a planar porphyrin ring.
Iron is also a component of iron-sulfur complexes (so-called iron-sulfur clusters ) in many enzymes , for example nitrogenases , hydrogenases or the complexes of the respiratory chain . A third important class of iron enzymes known as are non-heme iron enzymes to name, for example, methane monooxygenase , ribonucleotide reductase and Hemerythrin . These proteins perform tasks in various organisms: oxygen activation, oxygen transport , redox reactions and hydrolysis . Trivalent iron is just as important as the central ion in the enzyme catalase , which breaks down the cell toxin hydrogen peroxide, which is produced during the metabolism, in the peroxisomes of the cells.
The iron is stored intracellularly in the enzyme ferritin (20% iron content) and its breakdown product hemosiderin (37% iron content). Iron is transported through transferrin .
Humans contain 2.5 to 4 g of iron, of which 60% (2.0 to 2.5 g) is found in the hemoglobin of the erythrocytes, about 1 g in the liver and bone marrow (storage proteins ferritin and hemosiderin), about 10% to 15% % in myoglobin (approx. 400 mg iron), 250 mg in enzyme systems 0.1 to 0.2% iron in transport proteins (e.g. sulfur, iron proteins, cytochromes) (cytochrome: 0.1% of total iron).
External electron donor and acceptor
Some bacteria use Fe (III) as an electron acceptor for the respiratory chain. You thus reduce it to Fe (II), which means that iron is mobilized, since most Fe (III) compounds are sparingly water-soluble, but most Fe (II) compounds are readily soluble in water. Some phototrophic bacteria use Fe (II) as an electron donor for the reduction of CO 2 .
Medical importance
Iron need and iron deficiency
Iron in the Fe 2+ and Fe 3+ oxidation states is essential for all organisms. The daily requirement is 1 mg for men and 2 mg for women. Due to the inefficient absorption, the dietary intake must be around 5 to 9 mg for men and 14 to 18 mg for women. Iron deficiency is most likely to occur in pregnant women and athletes. An infant can absorb approx. 50% of the iron from breast milk, and only 20% from cow's milk.
Pre- menopausal women in particular are often iron deficient , the reason for this being menstruation . You should be consuming about 15 milligrams of iron per day, while the daily requirement of an adult male is only about 10 milligrams. In addition, women lose around 1000 milligrams of iron when giving birth to a child. By taking vitamin C at the same time, the absorption rate of iron is significantly increased. Iron is particularly rich in black pudding, liver, legumes and whole-grain bread and only slightly in (muscle) meat. However, simultaneous consumption of dairy products, coffee or black tea inhibits iron absorption.
Toxicity and iron overload
People
Iron is an important trace element for humans, but can also be harmful if overdosed. This particularly affects people who suffer from hemochromatosis , a regulatory disorder of iron absorption in the intestine. The iron accumulates in the liver in the course of the disease and leads to siderosis and further organ damage.
Iron is also suspected of causing infectious diseases, e.g. B. to promote tuberculosis , as the pathogens also need iron to multiply. An oversupply of iron leads to an increased susceptibility to infectious diseases (tuberculosis, salmonellosis , AIDS , yersiniosis ). In addition, some neurodegenerative diseases such as Parkinson's or Alzheimer's disease cause iron deposits in certain areas of the brain. It is currently unclear whether this is a cause or a consequence of the disease.
Therefore, iron supplements, like other food supplements, are only recommended if there is a medically diagnosed iron deficiency .
plants
Iron is also an essential trace element in plant organisms . It affects photosynthesis and the formation of chlorophyll and carbohydrates. However, iron overload can manifest itself in the form of iron toxicity . In soils it is present as Fe (OH) 3 at normal pH values . If the oxygen content of the soil is low, iron (III) is reduced to iron (II) through reduction. This brings the iron into a soluble form that is available to plants. If this availability increases too much under anaerobic conditions, for example due to soil compaction , damage to plants can occur due to iron toxicity, a phenomenon which is particularly known in rice-growing areas.
proof
There are a number of detection methods for iron. In addition to spectral analytical methods (iron provides a very rich spectrum), diverse chemical detection methods are also known. In the detection reaction for iron ions, a distinction is first made between the two cations Fe 2+ and Fe 3+ .
Detection of iron with thioglycolic acid
Fe 2+ and Fe 3+ ions can be detected with thioglycolic acid :
The presence of Fe 2+ or Fe 3+ ions produces an intense red color.
Iron detection with hexacyanoferrates
The Fe 2+ ions can be detected with red blood liquor salt :
Fe 3+ ions can be detected with yellow blood liquor salt :
Both detection reactions produce deep blue Berlin blue , an important dye. There is no complex formation reaction , only a cation exchange.
Both pigments are largely identical because there is a chemical equilibrium between them. Fe 3+ changes into Fe 2+ and vice versa:
The particularly intense blue color of the complex is created by metal-to-metal charge transfers between the iron ions. It is noteworthy that this known iron detection reagent itself contains iron, which is chemically well masked by the cyanide ions ( inner orbital complex ) and thus shows the limits of chemical analysis.
Detection of iron with thiocyanates
Alternatively, iron (III) salts with thiocyanates (rhodanides) can be detected. These react with iron (III) ions to form iron (III) thiocyanate:
The deep red iron (III) thiocyanate (Fe (SCN) 3 ) forms, which remains in solution. However, some accompaniments interfere with this proof (e.g. Co 2+ , Mo 3+ , Hg 2+ , excess of mineral acids ), so that u. U. a cation separation must be carried out.
links
In its chemical compounds, iron occurs mainly with the oxidation states +2 (e.g. iron (II) chloride ), +3 (e.g. iron (III) fluoride ), and also +6 (e.g. barium ferrate ( VI) ), but there are also compounds with the oxidation states -2, -1 and 0 (e.g. iron pentacarbonyl ) as well as +1, +4 and +5. In no compound does iron appear in the oxidation state corresponding to its subgroup number VIII. Even compounds with iron in the +7 oxidation state are unknown.
Oxides
Iron forms divalent and trivalent oxides with oxygen:
- Iron (III) oxide (Fe 2 O 3 ) is a red to brown substance and results from the oxidation of iron in excess oxygen. In nature it occurs in the form of the minerals hematite and maghemite .
- Iron (II, III) oxide (Fe 3 O 4 ) is produced naturally through volcanic processes or wheniron is burned directly, e.g. B. with the cutting torch as a hammer blow and is referred to as a mineral as magnetite .
- Iron (II) oxide (FeO) is formed only at the cautious decomposition of iron (II) oxalate FeC 2 O 4 in the vacuum . It is black and unstable up to 560 ° C. As a mineral wüstite , it usually arises from the transformation of magnetite at high temperatures.
Another iron oxide, FeO 2, is also known.
Since these oxides do not form a solid protective layer, an iron body exposed to the atmosphere oxidizes completely. The porous oxide layer slows down the oxidation process, but cannot prevent it, which is why burnishing serves as poor protection against corrosion . When iron body before the final rusting collected and the recycling are fed, are rusted iron and rusted steel in the steel production in electric smelting furnace a desirable and valuable oxygen carrier. This oxygen in scrap iron acts as an oxidizing agent during "steel boiling" in order to oxidize undesired quality-reducing impurities (e.g. light metals ).
Iron (III) hydroxide oxide (FeO (OH)) belongs to the group of iron hydroxides or iron (III) oxide hydrates, which differ in their degree of hydration . When heated, iron (III) oxide hydroxide changes into iron (III) oxide. The α-form occurs in nature as needle iron ore or goethite . The y-shape occurs naturally as ruby mica or lepidocrocite . In the α-form it has an orthorhombic crystal structure , space group Pbnm (space group no. 62, position 3) .
Iron oxides and iron hydroxides are used as food additives (E 172).
Salts
Iron forms divalent and trivalent salts:
- Iron (II) chloride (FeCl 2 · 6 H 2 O) is applied to the precipitation of sulfides , Faulgasentschwefelung , biogas desulphurisation , chromate and phosphate elimination ; this includes simultaneous felling . It has a crystal structure of the cadmium (II) chloride type with the space group R 3 m (space group no. 166).
- In its pure state, iron (II) fluoride is a white solid that is sparingly soluble in water. It has a crystal structure of the rutile type, space group P 4 2 / mnm (space group no. 136).
- Iron (II) bromide and iron (II) iodide are crystalline, hygroscopic solids which have a trigonal crystal structure of the cadmium (II) hydroxide type with the space group P 3 m 1 (space group no. 164).
- Iron (II) sulphate (FeSO 4 · 7 H 2 O) is also called green salt because of its color, as the mineral melanterite. Applications such as iron (II) chloride and dried iron (II) sulfate as a chromate reducer, especially in cement against chromate allergy .
- Iron (III) chloride (FeCl 3 · 6 H 2 O) canoxidize and dissolve copper ; therefore you can use aqueous iron (III) chloride solutions for the gentle etching of printed circuit boards .
- Anhydrous iron (III) chloride is a black substance with a slightly pungent odor of hydrochloric acid . As an anhydrous compound, it is extremely hygroscopic, i.e. it removes water from the air. The hygroscopic nature decreases with increasing water content and the color changes from red-brownish to yellowish. Iron (III) chloride has a trigonal crystal structure with the space group R 3 (space group no. 148) .
- Iron (III) nitrate is used for tanning . In the textile industry , it is used as a mordant for cotton fabrics and to the black dyeing silk by deposition of iron (III) hydroxide . It has also been used as a corrosion inhibitor for a long time. More recently, it has been used, not always successfully, to reduce the hydrogen sulfide concentration in pressurized sewage pipes.
- Iron (III) sulfate is used in large sewage treatment plants for deodorization and for the precipitation of phosphate ( e.g. in drinking water treatment and industrial water disposal ) and in the iron and steel industry as a pickling agent (e.g. for aluminum and steel ). In the medicine one is hemostatic and astringent effect known.
- Iron (III) chloride sulfate (FeClSO 4 )
All iron salts are used inter alia as a flocculant and to eliminate phosphate, including the pre-precipitation , simultaneous precipitation , post-precipitation and flakes filtration and the precipitation of sulfides , Faulgasentschwefelung and biogas desulphurisation .
Other iron compounds
Individual iron compounds:
- Iron carbide (Fe 3 C)
- Iron pentacarbonyl (Fe (CO) 5 ), also called IPC (from en: iron pentacarbonyl ), is created under pressure from iron and carbon monoxide and, after its decomposition, forms a particularly pure iron powder, carbonyl iron, in addition to carbon monoxide. Further iron carbonyls are Fe 2 (CO) 9 and Fe 3 (CO) 12 .
- Ferrocene (Fe (C 5 H 5 ) 2 ), a ( sandwich compound ) from the group of metallocenes .
- Prussian blue (Fe 4 [Fe (CN) 6 ] 3 ) is a lightfast, deep blue, inorganic pigment . It is made from a solution of iron (III) salt and yellow blood liquor salt and is used as a paint and for wallpaper printing and as an antidote to poisoning with radioactive cesium or thallium . Due to its fine grain and the resulting glazing ability, as well as its great color strength, it is still used today for watercolor , oil and printing inks .
literature
- Wilhelm Baer: The iron: its history, extraction and processing. Manual for iron foundries, machine builders, tradespeople, manufacturers and builders . Leipzig 1862 ( digitized version ).
- Ludwig Beck : The history of iron in technical and cultural-historical relation. Volume 1–5, Vieweg, Braunschweig 1884–1903.
- Harry H. Binder: Lexicon of the chemical elements - the periodic table in facts, figures and data. S. Hirzel Verlag, Stuttgart 1999, ISBN 3-7776-0736-3 .
- Vagn Fabritius Buchwald : Iron and steel in ancient times. Kong. Danske Videnskab. Selskab, Copenhagen 2005, ISBN 87-7304-308-7 .
- AF Holleman , E. Wiberg , N. Wiberg : Textbook of Inorganic Chemistry . 102nd edition. Walter de Gruyter, Berlin 2007, ISBN 978-3-11-017770-1 , pp. 1636-1666.
- Otto Johannsen (on behalf of the Association of German Ironworkers): History of the iron. 3rd edition, Verlag Stahleisen, Düsseldorf, 1953.
- Otto Johannsen: History of Iron. Düsseldorf 1925 ( digitized version ).
- Hans Schoppa: What the blast furnace operator needs to know about his work . Verlag Stahleisen, Düsseldorf 1992, ISBN 3-514-00443-9 .
- Association of German Ironworkers: General representation of the ironworking industry. 17th edition, Stahleisen, Düsseldorf 1970/71.
Web links
- Mineral Atlas: Iron in the Mineral Atlas
- Mineral atlas: Mineral portrait / iron in the mineral atlas
- Iron production in Roman times at die-roemer-online.de
- Iron extraction in prehistoric times on the website of the Obermain Landscape Museum
Individual evidence
- ↑ a b c Harry H. Binder: Lexicon of chemical elements , S. Hirzel Verlag, Stuttgart 1999, ISBN 3-7776-0736-3 .
- ↑ The values for the properties (info box) are taken from www.webelements.com (iron) , unless otherwise stated .
- ↑ CIAAW, Standard Atomic Weights Revised 2013 .
- ↑ a b c d e entry on iron in Kramida, A., Ralchenko, Yu., Reader, J. and NIST ASD Team (2019): NIST Atomic Spectra Database (ver. 5.7.1) . Ed .: NIST , Gaithersburg, MD. doi : 10.18434 / T4W30F ( https://physics.nist.gov/asd ). Retrieved June 11, 2020.
- ↑ a b c d e entry on iron at WebElements, https://www.webelements.com , accessed on June 11, 2020.
- ↑ a b K. Schubert: A model for the crystal structures of the chemical elements . In: Acta Crystallographica . 1974, B30, pp. 193-204 ( doi: 10.1107 / S0567740874002469 ).
- ↑ a b Yiming Zhang, Julian RG Evans, Shoufeng Yang: Corrected Values for Boiling Points and Enthalpies of Vaporization of Elements in Handbooks. In: Journal of Chemical & Engineering Data . 56, 2011, pp. 328-337 ( doi: 10.1021 / je1011086 ).
- ↑ Ludwig Bergmann, Clemens Schaefer, Rainer Kassing: Textbook of Experimental Physics , Volume 6: Solid. 2nd edition, Walter de Gruyter, 2005, ISBN 3-11-017485-5 , p. 361.
- ↑ https://www.seilnacht.com/Lexikon/leitf.htm
- ^ A b William M. Haynes: CRC Handbook of Chemistry and Physics . 92nd edition. Taylor & Francis, 2011, ISBN 978-1-4398-5511-9 ( hbcpnetbase.com ).
- ^ A b G. Rugel, T. Faestermann, K. Knie, G. Korschinek, M. Poutivtsev, D. Schumann, N. Kivel, I. Günther-Leopold, R. Weinreich, M. Wohlmuther: New Measurement of the 60 Fe Half-Life. In: Physical Review Letters . 103, 2009, p. 072502, doi: 10.1103 / PhysRevLett.103.072502 .
- ↑ a b Entry on iron, powder in the GESTIS substance database of the IFA , accessed on April 26, 2017(JavaScript required) .
- ↑ a b c d e f g h i j k Florian Neukirchen: From the Stone Age to the Rare Earths - A Brief History of Metals . Springer-Verlag, 2016, ISBN 978-3-662-49347-2 , pp. 65 ( limited preview in Google Book search).
- ↑ Kluge: Etymological Dictionary of the German Language , 21st edition, pp. 160–161.
- ↑ Julius Pokorny : Origin and etymology of the word iron. In: Journal for Comparative Linguistic Research 46, 1914, pp. 128–150.
- ^ Pfeifer : Etymological Dictionary of German , 212th edition 1993.
- ↑ Karin Figala: Alchemy Lexicon of a Hermetic Science . CH Beck, 1998, ISBN 978-3-406-44106-6 , pp. 123 ( limited preview in Google Book search).
- ↑ Otto Johannsen: History of the iron. 3rd edition, Verlag Stahleisen, Düsseldorf, 1953, p. 6.
- ↑ a b Otto Johannsen: History of the iron. 3rd edition, Verlag Stahleisen, Düsseldorf, 1953, p. 38.
- ↑ Rehren, Thilo & Belgya, Tamas & Jambon, Albert & Káli, György & Kasztovszky, Zs & Kis, Zoltan & Kovács, Imre & Maróti, Boglarka & Martinon-Torres, Marcos & Miniaci, Gianluca & Pigott, Vincent & Radivojević, Miljana & Rosta, L. & Szentmiklósi, László & Szőkefalvi-Nagy, Z .. (2013). 5,000 years old Egyptian iron beads made from hammered meteoritic iron. Journal of Archaeological Science. 40, 4785-4792. doi: 10.1016 / j.jas.2013.06.002 .
- ↑ a b Meteoritics & Planetary Science , The meteoritic origin of Tutankhamun's iron dagger blade, May 20, 2016.
- ↑ a b Otto Johannsen: History of the iron. 3rd edition, Verlag Stahleisen, Düsseldorf, 1953, p. 40.
- ↑ Otto Johannsen: History of the iron. 3rd edition, Verlag Stahleisen, Düsseldorf, 1953, p. 44.
- ^ A b Charles Burney: Historical Dictionary of the Hittites. Historical Dictionaries of Ancient Civilizations and Historical Eras. Scarecrow Press, 2004. ISBN 978-0-8108-6564-8 , pp. 135-136.
- ^ Richard A. Gabriel: The Great Armies of Antiquity . Greenwood Publishing Group, 2002. ISBN 978-0-275-97809-9 , p. 75.
- ^ Wolfgang Helck : Iron. In: Wolfgang Helck, Eberhard Otto (Hrsg.): Lexikon der Ägyptologie. Volume 1, Harrassowitz, Wiesbaden 1975, columns 1209-1210.
- ↑ Howard Vyse: Operations Carried on at the Pyramids of Giza in 1837. Volume 1, Fraser, London 1840, pp 275-276.
- ^ Alfred Lucas, John R. Lucas: Ancient Egyptian Materials and Industries. 4th ed., Arnold, London 1962, p. 237.
- ^ A b c Association of German Ironworkers: Common representation of the ironworking industry. 17th edition, Stahleisen, Düsseldorf 1970/71, p. 5.
- ↑ Otto Johannsen: History of the iron. 3rd edition, Verlag Stahleisen, Düsseldorf, 1953, p. 45.
- ↑ Mineralienatlas: Mineralienportrait / Eisen .
- ↑ Sophus Müller: Iron Age . Walter de Gruyter GmbH & Co KG, 2019, ISBN 978-3-11-144101-6 , p. 9 ( limited preview in Google Book search).
- ↑ Legends: 2000 years of Varus Battle history - archeology - legends . Walter de Gruyter, 2012, ISBN 978-3-11-028251-1 , p. 154 ( limited preview in Google Book search).
- ↑ Myrstener, Erik & Lidberg, William & Segerström, Ulf & Biester, Harald & Damell, David & Bindler, Richard. (2016). Was Moshyttan the earliest iron blast furnace in Sweden? The sediment record as an archeological toolbox. Journal of Archaeological Science: Reports. 5. 35-44. doi: 10.1016 / j.jasrep.2015.10.040 .
- ^ Hans Berns, Werner Theisen: Iron materials - steel and cast iron . Springer-Verlag, 2008, ISBN 978-3-540-79957-3 , pp. 396 ( limited preview in Google Book search).
- ↑ Klaus Urban: Material science and material technology A ride on the razor blade . Springer-Verlag, 2015, ISBN 978-3-662-46237-9 , pp. 28 ( limited preview in Google Book search).
- ^ Bernhard Neumann: The metals . Рипол Классик, 1904, ISBN 978-5-87731-632-4 , p. 8 ( limited preview in Google Book search).
- ^ David Stronach: Metal Objects from the 1957 Excavations at Nimrud. In: Iraq. 20, 1958, pp. 169-181, doi: 10.2307 / 4199639 .
- ^ Richard Kieffer, Werner Hotop: Sintereisen and Sinterstahl . Springer-Verlag, 2013, ISBN 978-3-7091-3951-6 , pp. 4 ( limited preview in Google Book search).
- ↑ Otto Johannsen: History of the iron. 3rd edition, Verlag Stahleisen, Düsseldorf, 1953, pp. 9-11.
- ↑ Lodders, Katharina. “ Solar System Abundances of the Elements. "Principles and Perspectives in Cosmochemistry (2010): 379-417. Crossref. Web.
- ^ Claude Allègre, Gérard Manhès, Éric Lewin: Chemical composition of the Earth and the volatility control on planetary genetics. In: Earth and Planetary Science Letters . 185, 2001, pp. 49-69; doi: 10.1016 / S0012-821X (00) 00359-9 .
- ↑ David R. Lide (Ed.): CRC Handbook of Chemistry and Physics . 85th edition. CRC Press, Boca Raton, Florida, 2005. Section 14, Geophysics, Astronomy, and Acoustics; Abundance of Elements in the Earth's Crust and in the Sea.
- ^ John Grotzinger, Thomas Jordan: Press / Siever General Geology . Springer-Verlag, 2016, ISBN 978-3-662-48342-8 , pp. 11 ( limited preview in Google Book search).
- ↑ Werner Gocht: Handbook of the metal markets ore deposits, metal extraction, metal use, pricing, trade regulations . Springer-Verlag, 2013, ISBN 978-3-642-86964-8 , p. 31 ( limited preview in Google Book search).
- ^ Slobodan Jankovic: Economic geology of ores . Springer-Verlag, 2013, ISBN 978-3-7091-5100-6 , pp. 96 ( limited preview in Google Book search).
- ^ Gregor Markl: Minerals and Rocks Mineralogy - Petrology - Geochemistry . Springer-Verlag, 2014, ISBN 978-3-662-44628-7 ( limited preview in Google book search).
- ↑ Walter Kölle: Water analyzes - correctly assessed basics, parameters, water types, ingredients, limit values according to the Drinking Water Ordinance and the EU Drinking Water Directive . John Wiley & Sons, 2012, ISBN 3-527-65984-6 , pp. 84 ( limited preview in Google Book search).
- ↑ Lexicon of Geosciences: Banded Iron Formation , accessed on October 5, 2019.
- ^ A b c Martin Bertau, Armin Müller, Peter Fröhlich, Michael Katzberg: Industrial Inorganic Chemistry . John Wiley & Sons, 2013, ISBN 978-3-527-33019-5 , pp. 696, 252 ( limited preview in Google Book search).
- ↑ Ellen Morris Bishop, John Eliot Allen: Hiking Oregon's geology . Mountaineers, 1996, p. 200 ( limited preview in Google Book Search).
- ^ Walter Hähnel, Werner Buggisch, Christian Buggisch: Minerals and rocks . TESSLOFF Verlag, 1994, ISBN 978-3-7886-2850-5 , p. 35 ( limited preview in Google Book search).
- ^ FJ Berry: Chemical Bonding and Spectroscopy in Mineral Chemistry . Springer Science & Business Media, 2012, ISBN 978-94-009-4838-9 , pp. 92 ( limited preview in Google Book search).
- ↑ Martin Okrusch, Siegfried Matthes: Mineralogie An introduction to special mineralogy, petrology and deposit science . Springer-Verlag, 2010, ISBN 978-3-540-78201-8 , pp. 70 ( limited preview in Google Book search).
- ^ Rudolf Winderlich: Textbook of Chemistry for Higher Educational Institutions Standard edition for lower and upper grades . Springer-Verlag, 2013, ISBN 978-3-663-04370-6 , pp. 75 ( limited preview in Google Book search).
- ↑ Geology for Investors: Iron Deposits - Banded Iron Formations (BIF) | Geology for Investors , accessed October 7, 2019.
- ↑ Handbook of Mineralogy - Iron (English, 57 kB; PDF).
- ↑ IMA / CNMNC List of Mineral Names - Iron (English, PDF 1.8 MB; p. 137).
- ↑ Mindat - Localities for Iron .
- ↑ Martin Okrusch, Siegfried Matthes: Mineralogie: An introduction to special mineralogy, petrology and deposit science . 7th edition. Springer Verlag, Berlin, Heidelberg, New York 2005, ISBN 3-540-23812-3 , pp. 22 .
- ^ William Jervis Jones: Historical Lexicon of German Color Designations . tape 1 . Akademie Verlag, Berlin 2013, ISBN 978-3-05-005953-2 , pp. 835 ( limited preview in Google Book search).
- ↑ Stefan Weiß: The large Lapis mineral directory . 5th edition. Christian Weise Verlag, Munich 2008, ISBN 978-3-921656-17-4 .
- ↑ Mineral Atlas: Josephinite .
- ↑ Webmineral - Mineral Species sorted by the element Fe (Iron) .
- ↑ a b c d e f g h i j W. Ternes: Biochemistry of the elements: Inorganic chemistry of biological processes . Springer-Verlag, 2012, ISBN 978-3-8274-3020-5 , pp. 108,127 ( limited preview in Google Book Search).
- ↑ Iron and Steel Statistics and Information: Iron and Steel 2019 Statistics and Information , accessed October 8, 2019.
- ↑ Iron Ore Statistics and Information: Iron Ore Statistics and Information 2019 , accessed October 8, 2019.
- ↑ United States Geological Survey: World Production (PDF; 298 kB).
- ↑ World Steel in Figures 2020. (PDF) World Steel Association , archived from the original on July 3, 2020 ; accessed on July 3, 2020 (English).
- ↑ Worldsteel: FACT SHEET - Steel and raw materials 2019 , accessed October 9, 2019.
- ↑ Luossavaara-Kiirunavaara AB: Mining , accessed October 9, 2019.
- ↑ Günther Schwemmer: The history of iron production in the central Upper Palatinate in the 19th and 20th centuries . diplom.de, 2001, ISBN 978-3-8324-4262-0 , p. 129 ( limited preview in Google Book search).
- ↑ The Fischer World Almanac 2001 . Fischer Taschenbuch Verlag, 2000, ISBN 978-3-596-72001-9 , pp. 1157 ( limited preview in Google Book search).
- ^ A b c Heinz M. Hiersig : VDI-Lexikon Maschinenbau . Springer-Verlag, 2013, ISBN 978-3-642-57850-2 , p. 520 ( limited preview in Google Book Search).
- ^ A b H. Berns, L. Scheer: What is steel - a steel customer for everyone . Springer-Verlag, 2013, ISBN 978-3-642-61846-8 , pp. 100 ( limited preview in Google Book search).
- ^ A b Wolfgang Bleck, Elvira Moeller: Handbook of steel selection, processing, application . Carl Hanser Verlag GmbH Co KG, 2017, ISBN 978-3-446-44962-6 , pp. 78,386 ( limited preview in Google Book Search).
- ↑ a b c d e f g h i j k l m n o p q r s t u v A. F. Holleman , E. Wiberg , N. Wiberg : Textbook of Inorganic Chemistry . 102nd edition. Walter de Gruyter, Berlin 2007, ISBN 978-3-11-017770-1 , pp. 1637-1642.
- ↑ Heinz Brauer: Handbook of environmental protection and environmental protection technology Volume 2: Production and product-integrated environmental protection . Springer-Verlag, 2013, ISBN 978-3-642-60943-5 , p. 340 ( limited preview in Google Book search).
- ↑ M. Shamsuddin: Physical Chemistry of Metallurgical Processes . John Wiley & Sons, 2016, ISBN 978-1-119-07833-3 , pp. 237 ( limited preview in Google Book search).
- ↑ Ludwig von Bogdandy, H.-J. Engell: The reduction of iron ores Scientific basis and technical implementation . Springer-Verlag, 2013, ISBN 978-3-642-92935-9 , pp. 33 ( limited preview in Google Book search).
- ^ Simone Franke: Giesserei-Lexikon 2019 . Schiele & Schoen, 2019, ISBN 978-3-7949-0916-2 , pp. 181 ( limited preview in Google Book search).
- ↑ Jürgen Ruge: Technology of materials for students of mechanical engineering and process engineering from the 1st semester . Springer-Verlag, 2013, ISBN 978-3-322-84025-7 , pp. 75 ( limited preview in Google Book search).
- ^ Verne Biddle, Gregory Parker: Chemistry, Precision and Design . A Beka Book, Inc.,.
- ↑ Association of German Eisenhüttenleute: Gemeinfassliche representation of ironmongery. 17th edition, Stahleisen, Düsseldorf 1970/71, pp. 103-118.
- ↑ Martin Bertau, Armin Müller, Peter Fröhlich, Michael Katzberg, Karl Heinz Büchel, Hans-Heinrich Moretto, Dietmar Werner: Industrial Inorganic Chemistry . John Wiley & Sons, 2013, ISBN 978-3-527-64958-7 , pp. 252 ( limited preview in Google Book search).
- ↑ MP Fewell: The atomic nuclide with the highest mean binding energy . In: American Journal of Physics . 63, No. 7, 1995, pp. 653-658. doi : 10.1119 / 1.17828 .
- ↑ G. Audi, O. Bersillon, J. Blachot, AH Wapstra: The NUBASE evaluation of nuclear and decay properties. In: Nuclear Physics. Volume A 729, 2003, pp. 3-128. doi : 10.1016 / j.nuclphysa.2003.11.001 . ( PDF ; 1.0 MB).
- ^ François Cardarelli: Materials Handbook A Concise Desktop Reference . Springer Science & Business Media, 2008, ISBN 978-1-84628-669-8 , pp. 65 ( limited preview in Google Book search).
- ↑ Reinhard Boehler: High-pressure experiments and the phase diagram of lower mantle and core materials . In: American Geophysical Union (Ed.): Review of Geophysics . 38, 2000, pp. 221-245. doi : 10.1029 / 1998RG000053 .
- ^ Reinhard Boehler, M. Ross: Mineral Physics . Ed .: Elsevier (= Treatise on Geophysics . Volume 2 ). 2007, Properties of Rocks and Minerals - High-Pressure Melting, p. 527-541 .
- ↑ The chemical composition undeveloped stars of spectral types A and F . S. 32, 55 ( limited preview in Google Book search).
- ↑ Lexicon of Astronomy: Iron Line - Lexicon of Astronomy , accessed on February 11, 2018.
- ^ Charles Steinmetz: Theory and Calculation of Electric Circuits . Editor: McGraw-Hill. 1917, Fig. 42 .
- ↑ a b B. D. Cullity, CD Graham: Introduction to Magnetic Materials, 2nd . Wiley – IEEE, New York 2008, ISBN 0-471-47741-9 , p. 116.
- ↑ Greenwood and Earnshaw, pp. 1075-1079.
- ↑ BL Bramfitt, Arlan O. Benscoter: The Iron Carbon Phase Diagram . In: [ limited preview in the Google book search Metallographer's guide: practice and procedures for irons and steels] . ASM International, 2002, ISBN 978-0-87170-748-2 , pp. 24-28.
- ↑ a b Wissenschaft-Online-Lexika: Entry on iron in the Lexikon der Chemie , accessed on November 14, 2019.
- ↑ a b c Entry on iron. In: Römpp Online . Georg Thieme Verlag, accessed on May 26, 2014.
- ↑ D. Glindemann, A. Dietrich, H.-J. Staerk and P. Kuschk The two smells of iron when touched and when exposed to acids - (skin) carbonyl compounds and organophosphines , Angewandte Chemie , 118 (42), (2006), pp. 7163–7166 ( doi: 10.1002 / anie.200602100 ) .
- ↑ a b c d Wolfgang Mücke, Christa Lemmen: Fragrance and smell, effects and health significance of odorous substances . ecomed-Storck GmbH, 2010, ISBN 978-3-609-16436-6 , p. 76 ( limited preview in Google Book search).
- ↑ G. Audi, FG Kondev, Meng Wang, WJ Huang, S. Naimi: The NUBASE2016 evaluation of nuclear properties. In: Chinese Physics C. 41, 2017, S. 030001, doi: 10.1088 / 1674-1137 / 41/3/030001 ( full text ).
- ^ Schuh-Renner, Anna & Fritsch, Adam & Heim, M. & Shore, A. & Thoennessen, M .. (2010). Discovery of the Iron Isotopes. Atomic Data and Nuclear Data Tables. 96.817-823. doi : 10.1016 / j.adt.2010.06.003 .
- ^ Alan P. Dickin: Radiogenic Isotope Geology . Cambridge University Press, 2018, ISBN 978-1-107-09944-9 , pp. 422 ( limited preview in Google Book search).
- ^ Heinrich D. Holland, Karl K. Turekian: Radioactive Geochronometry A derivative of the Treatise on Geochemistry . Academic Press, 2010, ISBN 978-0-08-096708-0 , pp. 50 ( limited preview in Google Book search).
- ↑ Harry Y. McSween, Jr, Gary R. Huss: Cosmochemistry . Cambridge University Press, 2010, ISBN 1-139-48946-1 , pp. 290 ( limited preview in Google Book Search).
- ↑ Gero Vogl: Wandering without a goal From atomic diffusion to the spread of living beings and ideas . Springer-Verlag, 2007, ISBN 978-3-540-71064-6 , pp. 86 ( limited preview in Google Book search).
- ^ Karl H. Koch: Industrial process analysis . Springer-Verlag, 2013, ISBN 978-3-662-01083-9 , pp. 102 ( limited preview in Google Book search).
- ^ Erwin Riedel, Hans-Jürgen Meyer: General and Inorganic Chemistry . Walter de Gruyter, 2013, ISBN 978-3-11-027013-6 , p. 341 ( limited preview in Google Book search).
- ^ Stephan Hasse: Structure of the cast iron alloys . Fachverlag Schiele & Schoen, 2007, p. 55 ( limited preview in Google Book search).
- ↑ a b Hermann Sicius: iron group: Elements of the eighth subgroup A journey through the periodic table . Springer-Verlag, 2016, ISBN 978-3-658-15561-2 , pp. 20.22 ( limited preview in Google Book Search).
- ↑ Erhard Hornbogen, Hans Warlimont: Metallkunde, structure and properties of metals and alloys . Springer-Verlag, 2013, ISBN 978-3-662-08697-1 , p. 292 ( limited preview in Google Book search).
- ↑ Franz Zach: Power Electronics A Handbook Volume 1 / . Springer-Verlag, 2015, ISBN 978-3-658-04899-0 , pp. 1828 ( limited preview in Google Book search).
- ^ Karl A. Hofmann: Inorganic Chemistry . Springer-Verlag, 2013, ISBN 978-3-663-14240-9 , pp. 667 ( limited preview in Google Book search).
- ↑ Aaron Foisi Nmungwun: Video Recording Technology Its Impact on Media and Home Entertainment . Routledge, 2012, ISBN 978-0-8058-0360-0 , pp. 38 ( limited preview in Google Book search).
- ↑ Ulrich Schwabe, Dieter Paffrath: Drug Ordinance Report 2016 . Springer-Verlag, 2016, ISBN 978-3-662-50351-5 , p. 265 ( limited preview in Google Book search).
- ↑ Helmut Plattner, Joachim Hentschel: Cell Biology . Georg Thieme Verlag, 2006, ISBN 978-3-13-106513-1 , p. 277 ( limited preview in Google Book search).
- ↑ Entry on ferritin. In: Römpp Online . Georg Thieme Verlag, accessed on May 26, 2014.
- ↑ F. Widdel, S. Schnell, S. Heising, A. Ehrenreich, B. Assmus, B. Schink: Ferrous iron oxidation by anoxygenic phototrophic bacteria . In: Nature Vol. 362, 1993, pp. 834-836; Abstract .
- ↑ Eberhard J. Wormer : Iron. The life element. Kopp, Rottenburg 2016.
- ↑ Y. Kohgo, K. Ikuta, T. Ohtake, Y. Torimoto, J. Kato: Body iron metabolism and pathophysiology of iron overload. In: International Journal of Hematology . Volume 88, Number 1, July 2008, pp. 7-15, doi: 10.1007 / s12185-008-0120-5 . PMID 18594779 . PMC 2516548 (free full text).
- ^ M. Auerbach, H. Ballard: Clinical use of intravenous iron: administration, efficacy, and safety. In: Hematology / the Education Program of the American Society of Hematology. American Society of Hematology. Education Program. Volume 2010, 2010, pp. 338–347, doi: 10.1182 / asheducation-2010.1.338 . PMID 21239816 .
- ↑ JM McDermid, B. Lönnerdal: Iron. In: Advances in nutrition (Bethesda, Md.). Volume 3, number 4, July 2012, pp. 532-533, doi: 10.3945 / an.112.002261 . PMID 22797989 . PMC 3649722 (free full text).
- ↑ Schaible UE, Kaufmann SH: Iron and microbial infection . In: Nat. Rev. Microbiol. . 2, No. 12, December 2004, pp. 946-953. doi : 10.1038 / nrmicro1046 . PMID 15550940 .
- ↑ Medicine - Communication: DEGUM: recognize Parkinson's disease before it breaks out. Working Group of Scientific Medical Societies, press release from July 6, 2006 at Informationsdienst Wissenschaft (idw-online.de), accessed on December 20, 2014.
- ^ Günter Fellenberg: Chemistry of environmental pollution , 3rd edition, Verlag BG Teubner, Stuttgart 1997, ISBN 3-519-23510-2 , p. 158.
- ↑ Barbara Grüttner, Wilhelm Fresenius, H. Hahn, Gerhart Jander: Elements of the eighth subgroup iron · cobalt · nickel . Springer-Verlag, 2013, ISBN 978-3-662-36753-7 , p. 128 ( limited preview in Google Book search).
- ^ AF Holleman , E. Wiberg , N. Wiberg : Textbook of Inorganic Chemistry . 102nd edition. Walter de Gruyter, Berlin 2007, ISBN 978-3-11-017770-1 , p. 1650.
- ↑ Jander, Blasius: Textbook of analytical and preparative inorganic chemistry , 12th edition, S. Hirzel Verlag, Stuttgart 1983, p. 221.
- ↑ Ehlers: Analytics I , 8th edition.
- ^ E. Schweda: Jander / Blasius: Inorganic Chemistry I - Introduction & Qualitative Analysis. 17th edition, Hirzel, Stuttgart 2012, ISBN 978-3-7776-2134-0 , p. 337.
- ↑ Detlef Schroeder, Andreas Fiedler u. a .: Generation and Characterization of the Anionic, Neutral, and Cationic Iron-Dioxygen Adducts [FeO2] in the Gas Phase. In: Inorganic Chemistry. 33, 1994, p. 5094, doi : 10.1021 / ic00100a039 .
- ↑ Chemie für Ingenieure, Pearson Deutschland GmbH, 2008, ISBN 3-8273-7267-4 , p. 256 ( limited preview in the Google book search).
- ↑ Georg Brauer (ed.) U. a .: Handbook of Preparative Inorganic Chemistry. 3rd, revised edition. Volume III, Ferdinand Enke, Stuttgart 1981, ISBN 3-432-87823-0 , p. 1648.
- ↑ Patent specification: Process for the production of an aqueous iron (III) sulfate solution and its use as a water treatment reagent
- ↑ Prussian Blue , Colourlex.