bronze

The collective term bronzes refers to alloys with at least 60% copper , unless they can be assigned to the brass due to the main alloy addition zinc .
In terms of metallurgy, the term is only used today together with the preceding main alloy additive; one speaks correctly about a antimony and arsenic bronze , aluminum bronze , lead bronze , manganese bronze or phosphor bronze . In historical contexts, such as the Bronze Age and bronze sculptures , “bronze” (sometimes spoken without the ending -e in Austria) is used on its own and mostly for a tin bronze .
etymology
The current name for the alloy was first borrowed from the Italian bronzo in the 17th century , later also from the French bronze . The prehistory is etymologically unclear. The word was first adopted into Italian from the Orient in the 14th century. A connection with the Persian word birindsch ( pirinğ or birinğ ) for copper can not be ruled out , from which Middle Latin bronzium and Italian bronzo could be derived.
Mineral foundations
Among the early time discovered in Central Europe include the copper ore Fahlerze : tetrahedrite ( Antimonfahlerz ) Tennantit ( Arsenfahlerz ) Freibergit , germanite , Colusit , Schwazit ( Quecksilberfahlerz ) Hermesit , Annivit ; or Wolfsbergite ( copper antimony luster ) - in which the copper contained is accompanied by antimony , arsenic , sulfur , lead and iron , elements whose clean separation requires basic metallurgical skills. Tin ores were found in particular as cassiterite ( tin stone ) and stannite ( tin grit ).
Composition / properties
Tin bronzes
In the bronze area of the copper- tin system, the melt forms three different mixed crystals with different compositions: The α mixed crystal corresponds to that of pure copper, which forms a face-centered cubic lattice. The melting point of pure copper is 1083 ° C. At around 24% tin, the β mixed crystal is present, which has a body-centered cubic lattice, at around 30% tin and above that, the body-centered cubic γ mixed crystal. A peritectic subsystem is formed between the mixed crystals α and β and between β and γ . The technically relevant peritectic α / β is 22% tin and 798 ° C. At 586 ° C there is a eutectoid disintegration of the β mixed crystals into α and γ mixed crystals. Depending on the alloy composition, two intermetallic compounds can form from the γ mixed crystals when they cool: The δ phase corresponds to Cu 31 Sn 8 and thus approx. 32.5% tin. It forms an enormous, face-centered cubic unit cell with 416 atoms and is very hard. The orthorhombic ε phase corresponds to Cu 3 Sn and is therefore about 38.4% tin. In the technically relevant area, the δ phase arises at 520 ° C when the γ mixed crystals disintegrate into a eutectoid structure of α and δ mixed crystals with 27% tin. Another eutectoid disintegration of the δ mixed crystals into α and ε mixed crystals at approx. 350 ° C no longer takes place under real technical conditions, since the diffusion is too much impeded. Cold forming and annealing for several months would be required to achieve equilibrium.
The structures that actually arise are mainly determined by the great diffusion inertia of tin, which prevents the equilibrium from being established during crystallization from the melt. This means that tin bronze has a structure consisting exclusively of α mixed crystals only with tin contents below 5–6%; with higher contents it consists of soft α mixed crystals and the hard α / δ eutectoid.
The addition of tin increases the strength of the alloy and reaches a maximum between 10 and 15% tin. The yield strength increases almost linearly, being multiplied compared to pure copper, and reaches a maximum at around 20 percent. The elongation at break begins, starting from the high values of the copper, rapidly decrease beyond 5% tin and approaches approximately exponentially to the zero line, which is practically measured between 20 and 25%. The hardness increases steadily, which increases with higher tin content. The density decreases by 0.1 g / cm³ for every 6% tin added. With 8% tin it is 8.79 g / cm³.
Alloys and alloy additives

Tin bronzes are standardized as copper-tin alloys and, due to the fundamentally different requirements and properties, are divided into wrought alloys (max. 9% tin), which are suitable for metal forming, and cast alloys (9% to 13% tin). In addition, so-called bell bronzes come with about 20%, max. but 22% tin is used.
- Phosphorus reduces copper oxide and thus also liquefies the melt. Tin oxide is not reduced, but can more easily rise into the slag in the deoxidized melt. When adding phosphorus as a deoxidizing agent, usually as pre-alloyed phosphorus copper with 10 or 15% phosphorus content, the dosage must be such that at least 0.01% phosphorus excess remains in the melt after deoxidation. Casting jet oxidation is avoided, and castability and physical properties in the cast are improved. Phosphorus only has a negative effect on electrical conductivity. At contents of more than 0.1%, Cu 3 P occurs in the structure. In the case of bearing materials, this may be desirable; in the case of conductive copper, phosphorus as a deoxidizing agent must be replaced by manganese copper or another phosphorus-free master alloy.
- Nickel, which creates an additional ϑ mixed crystal in the range of 9% tin, increases the toughness and reduces the wall thickness influence on the strength. It is therefore only used for cast alloys with a share of up to 2.5%.
- Lead forms its own phase and is finely distributed in the structure. It improves machinability and sliding properties, but increases hot brittleness. It is therefore used with 2% in cast alloys for bearing materials, in wrought alloys with 4% only in the special case of continuous, strip and wire casting, where subsequent hot forming is no longer necessary and the product should be machinable.
- Under certain circumstances, zinc can replace half the amount of tin; it is used for economic reasons. It has a deoxidizing effect, so that there is no need to add phosphorus. This will u. a. used in alloys for contact materials.
The welding consumables and hard solders based on copper-tin are subject to their own standardization .
More bronzes
If alloys contain little or no tin, they are often called “special bronzes”. Their names are derived from the alloy additive: aluminum bronze, manganese bronze, nickel bronze etc. (see overview table below). Beryllium bronze is a special copper material for spark-free tools that contains only 2-3% beryllium and a small amount of cobalt .
Lead bronze (also copper-tin-lead-bronze) is a bearing alloy with 5–22% lead.
Gunmetal is not a tin bronze, so it is not "bronze" in the narrower sense, although it is sometimes referred to as "machine bronze", "cannon bronze" and the like. It is a copper-based alloy whose properties are determined less by the addition of tin than by zinc , lead and nickel .
Table overview of the bronze alloys
Alloy name | Components to copper | properties | use |
---|---|---|---|
Cast tin bronze | up to 22% tin, mainly 10–12% tin, density about 8.8024 kg / dm³ | elastic, tough, corrosion-resistant | Mainly as cast, up to 6% tin can be cold-rolled to sheet metal and stamping material (medals, coins), wire drawing up to 10% tin. Bell casting ( bell bronze : around 20–24% tin), cannon bronze is historical, as are sound instruments. Statue bronze for art casting (small bronzes, monuments) |
Aluminum bronze | 5-10% aluminum | seawater-resistant, wear-resistant, elastic, slightly magnetic, gold-colored | Spring plate, balance beam, ship propeller , chemical industry |
Lead bronze | up to 26% lead | corrosion-resistant, good sliding properties | Bearing metal, composite and cast materials, antique coin bronze often contained lead, from which not all of the silver was removed |
Manganese bronze | 12% manganese | corrosion-resistant, heat-resistant | electrical resistances (in the USA referred to as manganese bronze despite the zinc content of 20-40% contained in some alloys , for example in some materials manufactured by Ampco) |
Silicon bronze | 1-2% silicon | mechanically and chemically highly stressable, high conductivity | Overhead lines, sliding contacts, chemical industry |
Beryllium copper (beryllium bronze) | 2% beryllium | hard, elastic, poisonous | Springs, clocks, non-sparking tools |
Phosphor bronze | 7% tin, 0.5% phosphorus | high density and strength | tough machine parts, axle bearings, guitar strings |
Conductive bronze | Magnesium , cadmium , zinc (total 3%) | electrical properties similar to copper, but with more tensile strength | Overhead lines , power systems |
Gunmetal | Tin, zinc, lead (total 10-20%) | corrosion-resistant, good sliding properties and castability | Plain bearings, fittings, worm wheels, art |
Corinthian ore (Corinthium aes) | 1–3% gold , 1–3% silver , sometimes a few percent arsenic, tin or iron |
Can be colored black by patination | historical material for statues and luxury items (antiquity) |
Potin | French name for alloys based on copper. Potin gris can be described as a bronze alloy. Potin jaune is cast brass made from old brass. Term also for Celtic coin bronze |
Statue bronze
The Meyers of 1905 named 89% copper, 8.2% tin and 1.5% lead for the alloy of a weather-resistant bronze.
The composition of modern bronze statues was named in 1905:
statue | copper | zinc | tin | lead |
---|---|---|---|---|
Friedrich Wilhelm IV., Cologne | 89.55 | 7.46 | 2.99 | - |
Lion fighters, Berlin | 88.88 | 9.72 | 1.40 | - |
Amazone, Berlin | 90.00 | 6.00 | 4.00 | 1.00 |
Blücher, Berlin | 90.10 | 5.30 | 4.60 | - |
Friedrich II., Berlin | 88.30 | 9.50 | 1.40 | 0.07 |
Great Elector, Berlin | 89.09 | 1.64 | 5.82 | 2.26 |
87.91 | 1.38 | 7.45 | 2.65 |
According to Meyers in 1905, they had beautiful green patina :
statue | copper | zinc | tin | lead | iron | nickel |
---|---|---|---|---|---|---|
Shepherd at the pond, Potsdam | 89.20 | 1.12 | 8.86 | 0.51 | 0.18 | - |
Bronze from the 16th century | 89.40 | - | 8.17 | 1.05 | 0.34 | 0.19 |
Diana, Munich | 77.30 | 19.12 | 0.91 | 2.29 | 0.12 | 0.43 |
Mars and Venus, Munich 1575 | 94.12 | 0.30 | 4.77 | 0.67 | - | 0.48 |
history


Tin bronze is from the middle of the 4th millennium BC. Between the middle Danube and the Caspian Sea. B. from the 3rd millennium BC BC in the Balkans, as well as for the Kura-Araxes culture (Transcaucasia).
The term, already known in Greek, is also associated with Brundisium , the Latin name of today's southern Italian Brindisi , which in ancient times , belonging to New Greece, was a kind of center of bronze processing and the bronze trade.
The commercial production of bronze is thought to have been between 2500 and 2000 BC. Started in the Middle East ; in Mohenjo-Daro the small figure of a girl (dancer) was found. In China , the use is also in the 3rd millennium BC. BC, documented at the latest during the Xia period .
Bronze is therefore considered to be one of the first alloys made and used by humans, harder than pure copper, but in comparison with a lower melting point, a finding that already required a basic metallurgical knowledge. The composition of the earliest bronzes, however, was often still dependent on the ores used; Alloys with arsenic resulted, whose negative influence on the mechanical properties is known today. Bronzes containing lead and - due to the ore processed - those with antimony were also processed.
The Bronze Age , as the successor to the Copper Age , which in turn replaced the New Stone Age , brought bronze weapons , tools and jewelry (bronze brooches) to the Aunjetitz culture and the Alpine Bronze Age. It was gradually replaced by the early Iron Age ( Urnfield culture , Lusatian culture ), and finally, with the Hallstatt culture, antiquity was introduced. Depending on the task at hand, bronze and iron were still used side by side. However, through trial and error, low carbon wrought iron was found. As a result, bronze increasingly lost its importance for the manufacture of hand weapons. With the Greeks and Romans, weapon technology experienced a quality never seen before and developed in the building industry. Bronze monuments also attest to the great experience in antiquity. The early Middle Ages gave a new impetus, bell and piece casters supported ecclesiastical and secular rule for several centuries, until iron smelting and iron casting replaced bronze.
use
The traditional uses of bronzes
- Bells and comparable sound instruments from non-Christian religions, statues from life-size to oversized and since the invention of gunpowder, guns. During World War II, numerous bells were dropped to use copper and tin for armor. A “ bell cemetery ” in Hamburg served as temporary storage in front of the melting furnace. At the end of the war there were still numerous bells there that could be returned to their communities.
- Works of art ( art casting ). Historical bronze doors are known, such as the Bernward door in Hildesheim Cathedral
- Small bronzes, memorial plaques and cast or embossed medals (bronze medals in sporting competitions).
- powerful musical instruments such as drum cymbals and hi- hats
- Forming nozzles for pasta production
- ancient to modern coins, for example As .
Bronzes and bronze alloys as part of modern techniques
Copper-tin alloys for different techniques are also adapted to the requirements with equally different alloying elements. The addition of nickel increases the toughness of cast alloys, the strength of wrought alloys, lead is an indispensable component of all bearing alloys, separated in the structure as metallic lead, it supports the emergency running property that is important for bearings .
A wide area of application for copper-tin alloys is mechanical engineering and tool construction, but also for spring and contact elements in electrical engineering and electronics, e.g. B. in circuit sockets with gold-plated spring bronze. The chemical and food industries make use of the corrosion and wear resistance.
Classic tin bronzes are not suitable for the production of propellers and ship screws for seagoing ships; instead, multi-material aluminum bronzes are used, which are resistant to cavitation and corrosion in contact with seawater .
Just as fine and ultra-fine granulates are produced from other metals and alloys - commonly referred to as "metal powder" (copper powder, aluminum powder) - also from bronze. Pyrophoric properties make all metal powders a component of fireworks, but what is more important is that they enable the technique of powder flame spraying to produce three-dimensional objects. With additional hot isostatic pressing ( sintering ), properties of a metal model are achieved, thus saving time and money in the production of prototypes and small series.
gallery
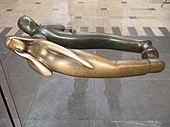
Bronze sculpture (patinated), placed at the Apothekerbrunnen in Ilmenau
Snöklockan ( Snowdrop ), Paris 1881, by Per Hasselberg . Copy in bronze from 1953, cast by C & A Nicci (Rome / Italy) and placed in Rottneros Park near Sunne in Värmland (Sweden).
Bavaria and Bavarian Lion. Bronze cast (copper-tin alloy, in sand), 87.36 tons
Artificial bronze casting of a mortar , unsigned series item
literature
- Lexicon of metal technology. Manual for all tradespeople and artists in the metallurgical field. Edited by J. Bersch. A. Hartlebens Verlag, Vienna / Pest / Leipzig, no year.
- Bronze - an indispensable material of the modern age. German Copper Institute (DKI), Düsseldorf 2003.
- Tobias L. Kienlin: Early Metal in the Northern Alpine Region: An investigation into technological and cognitive aspects of early metallurgy based on the structure of early Bronze Age axes . In: Archaeological Information . tape 27 , 2004, p. 187–194 , doi : 10.11588 / ai.2004.1.16825 ( journals.ub.uni-heidelberg.de [PDF; 5.9 MB ; accessed on March 24, 2020]).
- Information prints i15 and i25 of the German Copper Institute (DKI), Düsseldorf 2004.
- Cast from copper alloys. From the American by Ernst Brunhuber, Schiele & Schön, Berlin 1986, ISBN 3-7949-0444-3 .
Web links
German Copper Institute (DKI) :
- Information prints:
- BRONZE - an indispensable material of modernity (PDF; 596 kB)
- Wrought copper-tin alloys (tin bronzes) (PDF; 998 kB)
- Copper-tin and copper-tin-zinc cast alloys (tin bronzes) (PDF; 1.8 MB)
- Web pages:
Individual evidence
- ↑ Ernst Pernicka: "The spread of tin bronze in the 3rd millennium." In: Bernhard Hänsel (Ed.): "Man and the environment in the bronze age of Europe." Oetker Voges Verlag, Kiel 1998, ISBN 978-3-98043-222- 1 , pp. 135–147 ( [1] on archiv.ub.uni-heidelberg.de)
- ↑ Spelling and pronunciation of the word bronze. In: duden.de. Duden , accessed on March 24, 2020 .
- ↑ Etymology . In: The Great Duden . tape 7 . Bibliografische Institut AG, Mannheim 1963.
- ^ Martin Löpelmann: Etymological dictionary of the Basque language . tape 1 . Walter de Gruyter, Berlin 1968, p. 231 ( limited preview in Google Book search).
- ^ Friedrich Kluge , Alfred Götze : Etymological dictionary of the German language . Ed .: Walther Mitzka . 20th edition. De Gruyter, Berlin, New York 1967, ISBN 3-11-005709-3 , pp. 102 (reprint (“21st unchanged edition”) ibid 1975).
- ↑ Karl Lokotsch : Etymological dictionary of European (Germanic, Romanic and Slavic) words of oriental origin (= Indo-European library. Division 1: Collection of Indo-European text and handbooks. Series 2: Dictionaries. Volume 3 ). Winter, 1927, ZDB -ID 843768-3 , p. 132 f .
- ↑ DIN CEN / TS 13388; DIN SPEC 9700: 2015-08 - Copper and copper alloys - Overview of compositions and products. In: din.de. DIN, accessed on March 24, 2020 .
- ↑ a b c bronze. at Zeno.org, p. 454 ff.
- ↑ Tobias L. Kienlin, E. Bischoff, H. Opielka: Copper and Bronze During the Eneolithic and Early Bronze Age: a Metallographic Examination of Axes from the Northalpine Region . In: Archaeometry . tape 48 , no. 3 , 2006, p. 453–468 , doi : 10.1111 / j.1475-4754.2006.00266.x (English, analyzes of early bronzes).
- ↑ Copper-tin and copper-tin-zinc cast alloys (tin bronzes). (PDF 1930 kB) In: kupferinstitut.de. Deutsches Kupfer Institut, December 2004, accessed on March 24, 2020 .