Haber-Bosch process
The Haber-Bosch process is a large-scale industrial chemical process for the synthesis of ammonia . It is named after the German chemists Fritz Haber and Carl Bosch who developed the process at the beginning of the 20th century. The central step of the process, the ammonia synthesis from atmospheric nitrogen and hydrogen , is carried out on an iron-containing catalyst at pressures of around 150 to 350 bar and temperatures of around 400 to 500 ° C. As a major chemical process with a production output of more than 150 million tons in 2017, it covers more than 99% of the world's ammonia production.
Ammonia is a chemical substance that is mainly used for the production of urea , ammonium nitrate , ammonium sulfate and ammonium phosphates . These substances are used as fertilizers and contribute to the nutrition of a large part of the world's population. Ammonia is also used to manufacture explosives and chemicals containing nitrogen. The selective catalytic reduction using ammonia in the flue gas denitrification for conversion of harmful nitrogen oxides into nitrogen and water. Ammonia has also been used as an environmentally friendly and energy-efficient refrigerant since 1876 .
The scientific achievements for the realization of this process were on the one hand the investigation of the underlying chemical reaction by Fritz Haber and Walther Nernst , on the other hand the systematic search for suitable catalysts by Alwin Mittasch and the clarification of fundamental process problems for high pressure processes by Carl Bosch. In connection with the Haber-Bosch process, the Nobel Foundation awarded the Nobel Prize for Chemistry to Fritz Haber in 1918 , to Carl Bosch in 1931 and to Gerhard Ertl in 2007 , who found the complete theoretical explanation of the mechanism of ammonia formation.
If ammonia is produced from natural gas without the use of renewable energies, around 1.5 tons of the greenhouse gas carbon dioxide are produced per ton of ammonia produced . However, hydrogen can also be produced in a climate-neutral manner via electrolysis using renewable energies. The Haber-Bosch process described here should also be climate-neutral with renewable energies.
The production of ammonia is widespread, currently around 2–3% of the total commercial energy requirement worldwide is expected to be used for this.
history
Bread made of air
From the work of Justus von Liebig, it has been known since the middle of the 19th century that the uptake of nitrogen is a basis for the growth of crops. The necessary nitrogen was supplied to the arable land in the form of manure, compost or a specific crop rotation . Due to the rapid growth of the world population in the 19th century, the associated high demand for nitrogen fertilizers could no longer be met by natural occurrences of guano or Chile's nitrate, for example, or by technical sources such as coke oven gas . To draw attention to this fact, the British chemist William Crookes gave a widely acclaimed speech to the British Association for the Advancement of Science in Bristol in June 1898 . In it he stated that by 1918 the demand for nitrogen would far exceed the supply and the western world was threatened with a famine of unimagined proportions. He also stated that the only solution to this problem was to chemically fix the nitrogen in the air. He called the technical implementation of this process one of the great challenges for the chemists of his time. The attempt to bind atmospheric nitrogen in a chemical that plants can absorb, known under the catchphrase “Bread from Air”, then advanced to become one of the focal points of chemical research at that time.
Early developments

A first breakthrough in the fixation of atmospheric nitrogen came in 1898 with the preparation of calcium cyanamide according to the Frank-Caro method , in which calcium carbide absorbs atmospheric nitrogen at high temperatures and thus fixes it. The hydrolysis of calcium cyanamide provides ammonia and calcium carbonate . Although large capacities were built up for the production of calcium cyanamide, the process was not competitive in the long term because of the high energy requirement of around 190 gigajoules per ton of ammonia.
In 1900, Wilhelm Ostwald registered a patent for the “production of ammonia and ammonia compounds from free nitrogen and hydrogen” because he had apparently succeeded in producing ammonia catalytically from the elements. As early as 1903, the Rottweiler explosives manufacturer Max Duttenhofer published Ostwald's warning of a saltpeter embargo in the event of war in the "Swabian Mercury". Ostwald withdrew his patent after Bosch had proven that the ammonia produced came from the iron nitride of the catalyst used.
The Birkeland-Eyde process , which was developed by the Norwegian scientist Kristian Birkeland and his business partner Sam Eyde and put into operation in 1903, fixed the nitrogen in the air by oxidizing it directly to nitric oxide using an electric arc . Upon cooling and further oxidation, nitrous oxide was formed , which reacted to nitric acid by absorption in water. The low energy efficiency soon led to the displacement of the process.
Basic work
In 1904 Fritz Haber, who at that time was working as an associate professor for technical chemistry in Karlsruhe , began to deal with the chemical principles of ammonia synthesis. The equilibrium constant found for the synthesis of ammonia from the elements nitrogen and hydrogen corresponded to a yield of less than 0.01 percent at a temperature of 1000 ° C and normal pressure and was therefore too low to implement a technical process. Haber was aware that higher pressures would lead to better yields, but due to the anticipated technical problems, he temporarily stopped his research in this area. It was only after a scientific discussion with Walther Nernst about the equilibrium constant of ammonia synthesis based on the Nernst theorem that Haber was able to continue his work. As a result of further research, he believed that the transfer to technology would only be possible at temperatures below 300 ° C and only with a suitable catalyst . Shortly afterwards he was able to put it into practice with the help of an osmium- based catalyst.
On October 13, 1908, Haber applied to the Imperial Patent Office in Berlin for patent protection for a “method for the synthetic preparation of ammonia from the elements”, which was granted on June 8, 1911 with patent no. 235,421. Since he was now working with BASF , he gave the company the patent for commercial use.
technical realization
The provision of the raw material hydrogen in particular, which until then was only available in larger quantities in chlor-alkali electrolysis , required completely new processes. Until then, there were also no technical references for the construction of the chemical reactors required for ammonia synthesis , in which hydrogen could be controlled at high pressures and temperatures. Carl Bosch and Fritz Haber then developed new solutions in many areas of technical chemistry and reactor construction.
Due to the large number of specialists required to implement production on an industrial scale, Bosch set up an interdisciplinary chemical engineering division in which mechanical engineers and chemists worked together. Since the steels initially used for reactor construction were eroded by atomically diffused hydrogen, one of the tasks of the new work area was to research material damage caused by decarburization of carbon steels . This ultimately led to the development of high-alloy chromium-nickel steels that withstand hydrogen attack at the required reaction temperatures and pressures. In particular, the Schierenbeck winding process developed by Julius Schierenbeck , in which several layers of a hot metal strip were shrunk onto a chemically resistant central tube, enabled the construction of larger and safer high-pressure reactors. At the same time, Alwin Mittasch developed and tested around 3000 different catalysts based on iron oxide with various conversion-accelerating substances, which he called activators or promoters , in 20,000 experiments . The catalyst used in 2015 largely corresponded to that developed by Mittasch.
In 1913, BASF commissioned a plant based on the Haber-Bosch process at the Ludwigshafen-Oppau plant for the first time . The capacity of the plant was initially 30 tons per day. As early as 1914, the German Chief of Staff Erich von Falkenhayn pushed the further development of the process up to its large-scale industrial applicability , whereupon Bosch made the so-called saltpeter promise. This was a contract for the delivery of nitrates with purchase guarantees and with financial support from the Reich for the construction of appropriate plants. This should enable ammonium nitrate as a basis for military explosives to be produced in sufficient quantities without the naturally occurring saltpetre that is otherwise used. Shortly afterwards, the Haber-Bosch process succeeded in producing correspondingly large quantities of the war-relevant material. This enabled the German Reich, which was cut off from nitrogen sources such as Chile's nitrate by the British naval blockade, to maintain its ammunition and fertilizer production during the First World War and to avert economic collapse. In addition to the large-scale plant in Oppau near Ludwigshafen , others in Leuna and Bitterfeld were operated by BASF and, after the merger in the large German corporation, by IG Farben .
After the First World War
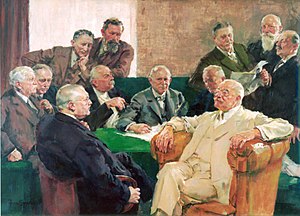
After the war, the victorious power of France obliged BASF to hand over all patents and experience relating to the process and to support the construction of a corresponding factory in Toulouse . Further ammonia plants were built in England, Italy and other countries at the same time. This construction project was based either on a license from BASF or on a process variant with modified process parameters, including the Casale process and the Mont-Cenis process with modified catalyst.
IG Farben was founded between the two world wars, with Carl Bosch as its first chairman of the board. As early as 1926, the company's market capitalization , which now has 100,000 employees, was around 1.4 billion Reichsmarks . The global economic crisis that began with the New York stock market crash of October 1929 reduced the demand for synthetic ammonia considerably. Production in Germany, which had already reached an annual volume of over 800,000 tons, then fell to below 500,000 tons and IG Farben's income was halved. Nevertheless, IG Farben remained the world's largest manufacturer of ammonia until 1930; Ammonia synthesis accounted for 65 percent of the total profit.
The import embargo for nitrogen fertilizers issued by the Brüning cabinet allowed IG Farben to raise the prices for synthetic fertilizers again. After the seizure of power of Hitler the Nazi regime took control of the IG Farben. In 1935 , under pressure from the Nazi regime, Bosch resigned his position on the board, which fell to NSDAP member and military economics leader Hermann Schmitz . In 1940 ammonia production in Germany reached one million tons per year. As a result of the steadily increasing demand for ammonia and its secondary products, ever more powerful reactors were created.
After the Second World War
The increasing availability of inexpensive crude oil and cost-reducing gasification processes through, for example, the partial oxidation of crude oil fractions made it possible to build Haber-Bosch plants all over the world after the Second World War. The partial oxidation originally developed by IG Farben was improved by the company Imperial Chemical Industries (ICI) and expanded to include the oxidation of naphtha , which made the raw materials of the process cheaper in the 1950s and 1960s.
Engineering companies such as MW Kellogg subsequently developed more energy-efficient and thus more cost-effective large-scale plants with only one reactor, which led to a worldwide increase in plant capacity . Increasing competition and high cost pressure finally paved the way for the LCA process from ICI and the KAAP process from Kellogg, Brown & Root , in which a ruthenium catalyst was used for the first time .
raw materials
Ammonia is created in an equilibrium reaction from the elements hydrogen and nitrogen according to the equation
- ,
where the required nitrogen is taken from the ambient air. The oxygen, which is also contained in the air but is undesirable, was first converted into water by reduction with hydrogen and thus separated; the Fauser process used the nitrogen, which was not converted during ammonia combustion with air, as a raw material. Later, nitrogen production by air separation using the Linde process proved to be more economical.
The largest part of the production costs is caused by the procurement of hydrogen, which was initially obtained from the cost-intensive chlor-alkali electrolysis . With natural gas, crude oil, coal and the electrolysis products of water, further sources for the production of hydrogen were added later.
BASF used water gas based on the coal gasification of lignite using a Winkler generator as the primary source. The hydrogen is obtained by reacting steam with glowing coke. The air supplied is dosed in such a way that the oxygen is completely converted into carbon monoxide . The nitrogen required for the subsequent ammonia synthesis remained in the water gas. The carbon monoxide was then converted into easily removable carbon dioxide or used in a water gas shift reaction to provide additional hydrogen. In 2008, about 18 percent of the hydrogen produced worldwide was produced from coal as a raw material.
Although natural gas was not yet available to BASF as a raw material for the production of hydrogen in the 1920s, Carl Bosch initiated the development of the steam reforming of methane , which would later become an important part of the process. Georg Schiller achieved a breakthrough for IG Farben, who succeeded in steam reforming methane using a nickel oxide catalyst. The Standard Oil of New Jersey was granted a license to the hydrogen production by steam reforming at its plant in 1931 Baton Rouge in Louisiana began. The steam reforming of natural gas accounted for around 48 percent of global hydrogen production in 2014, around 60 percent of which used the Haber-Bosch process.
Another possible method of producing hydrogen is partial oxidation . In this case, natural gas or petroleum origin are hydrocarbons gasified with oxygen and steam in an open reactor without a catalyst at about 1100 ° C and the synthesis gas further processed as in the steam reforming. The higher hydrocarbons from petroleum contributed 30 percent to the annual production of hydrogen in 2008.
Hydrogen can also be obtained by electrolysis of water. This uses electrical energy to break down water into hydrogen (H 2 ) and oxygen (O 2 ). This process is only economical if inexpensive electrical energy, for example from hydropower, is available. In 2008, electrolysis accounted for around four percent of hydrogen production.
With the advent of platforming capacities in the United States in the mid-1950s, a petrochemical hydrogen source became available that in 1956 provided about eleven percent of the hydrogen required for ammonia synthesis in the United States. Other refinery processes such as hydrodesulfurization and hydrocracking later used the hydrogen produced.
catalyst
To lower the activation energy and the associated increase in the reaction rate , an additional substance, the catalyst , is used in many chemical processes , which is not consumed during the reaction. If the physical state of the catalyst differs from that of the actual substances that react with one another, then it is a heterogeneous catalyst. This is also the case with the Haber-Bosch process, in which finely divided iron on an iron oxide carrier in solid form serves as a catalyst within a reacting gas mixture. This heterogeneous catalyst, also known as “contact”, arises during the reaction from another material previously introduced into the reactor, the “catalyst precursor” or “ precursor contact ”.
Iron catalyst

The heterogeneous iron catalyst is a catalytically very active form of body-centered cubic α-iron and is produced by chemical reduction from a special form of oxidized iron, magnetite (Fe 3 O 4 ). The effect of the catalyst is enhanced by oxidic promoters that have been added to the magnetite beforehand. In the case of ammonia synthesis, these include, for example, aluminum oxide , potassium oxide , calcium oxide and magnesium oxide .
The production of the required magnetite contact requires a special melting process in which the raw materials used must be free of catalyst poisons and the promoter surcharges must be evenly distributed in the magnetite melt. Rapid cooling of the magnetite melt, which has a temperature of around 3500 ° C., forms the desired catalyst with high activity , which reduces its abrasion resistance. In spite of this disadvantage, the rapid cooling method is often preferred in practice.
The reduction of the catalyst precursor magnetite to α-iron is carried out with synthesis gas directly in the production plant. The reduction of magnetite initially takes place via the level of wüstite (FeO), so that contact is formed with a core made of magnetite, which is surrounded by a shell made of wüstite. The further reduction of the magnetite and wustite phase leads to the formation of α-iron, which together with the promoters forms the outer shell. The processes involved are complex and depend on the reduction temperature. As disproportionated wustite at lower temperatures in an iron and a magnetite phase, at higher temperatures is the reduction of magnetite to the iron Wüstit- and the dominant process.
The α-iron forms primary crystallites with a diameter of about 30 nanometers . These form a bimodal pore system with pore diameters of around 10 nanometers, which result from the reduction of the magnetite phase, or from 25 to 50 nanometers, which result from the reduction of the wüstite phase. With the exception of cobalt oxide, the promoters are not reduced.
When iron oxide is reduced with synthesis gas, water vapor is produced as a by-product. This water vapor must be taken into account for optimum catalyst quality. If this comes into contact with the finely divided iron, this leads, especially in connection with high temperatures, to premature aging of the catalyst due to recrystallization . For this reason, the vapor pressure of the water in the gas mixture formed during catalyst formation is kept as low as possible, with values below 3 gm −3 being aimed for. For this reason, the reduction is carried out at high gas exchange , low pressure and low temperatures. The exothermic nature of the ammonia formation ensures a gradual increase in temperature.
The reduction of fresh, fully oxidized catalyst or precursor until full capacity is reached takes four to ten days. The wüstite phase is faster than the magnetite phase (Fe 3 O 4 ) and is reduced at lower temperatures. After detailed kinetic, microscopic and X-ray spectroscopic investigations, it could be demonstrated that wüstite is the first to convert to metallic iron. This leads to a density inhomogeneity (gradient) of the iron (II) ions , as a result of which they diffuse from the magnetite through the wustite to the interface and precipitate there as iron nuclei.
In technical practice, pre-reduced, stabilized catalysts have gained a significant market share . They already have the fully developed pore structure , but have been oxidized again on the surface after production and are therefore no longer pyrophoric . The reactivation of such prereduced catalysts only takes 30 to 40 hours instead of the usual periods of several days. In addition to the short start-up time, they have other advantages with their higher water resistance and lower weight.
Composition of a contact | % Iron | % Potassium | % Aluminum | % Calcium | % Oxygen |
---|---|---|---|---|---|
Volume composition | 40.5 | 0.35 | 2.0 | 1.7 | 53.2 |
Surface composition before reduction | 8.6 | 36.1 | 10.7 | 4.7 | 40.0 |
Surface composition after reduction | 11.0 | 27.0 | 17.0 | 4.0 | 41.0 |
Catalysts other than iron
Since the industrial introduction of the Haber-Bosch process, many efforts have been made to improve it, resulting in significant advances. In the improvement of the ammonia synthesis catalyst, however, there has been no significant progress for a long time since the 1920s.
As part of the search for suitable catalysts, many metals were tested intensively: The prerequisite for suitability is the dissociative adsorption of the nitrogen (the nitrogen molecule must therefore be split into two nitrogen atoms during adsorption). At the same time, the bond between the nitrogen atoms must not be too strong, otherwise the catalytic capabilities would be reduced (i.e. self-poisoning ). The metals in the periodic table of the elements to the left of the iron group show such a strong bond to nitrogen. The associated formation of volume or surface nitrides , for example , makes chromium catalysts ineffective, they poison themselves. Metals to the right of the iron group, on the other hand, adsorb nitrogen to a small extent to be able to activate sufficient nitrogen for ammonia synthesis. Haber himself initially used osmium and uranium as catalysts. During catalysis, uranium reacts to form nitride and osmium oxide is very rare, volatile and highly toxic.
Because of its comparatively low price, great availability, ease of processing, lifespan and activity, iron was ultimately chosen as the catalyst. For a production capacity of 1800 tons per day, for example, a pressure of at least 130 bar , temperatures of 400 to 500 ° C and a reactor volume of at least 100 m³ are required. Theoretical and practical studies have shown that the scope for further improvement of the pure iron catalyst is limited. It was not until 1984 that the iron catalyst was modified by cobalt that it noticeably increased its activity.
Second generation catalysts
Catalysts based on ruthenium show a higher activity at comparable pressures and lower temperatures and are therefore referred to as second generation catalysts. Their activity is strongly dependent on the catalyst support and the promoters. A large number of substances can be used as carriers; in addition to carbon , these are magnesium oxide, aluminum oxide, zeolites , spinels and boron nitride .
Ruthenium activated carbon catalysts have been used industrially since 1992 in the “KBR Advanced Ammonia Process” (KAAP, German about the more advanced ammonia process according to Kellogg, Brown and Root ). The carbon carrier is partially broken down into methane , which can be reduced by a special treatment of the carbon at 1500 ° C and thus helps to extend the lifespan. In addition, the finely dispersed carbon poses a risk of explosion . For these reasons and because of its low acidity , magnesium oxide has proven to be a good alternative. Carriers with acidic properties remove electrons from ruthenium, make it less reactive and undesirably bind ammonia to the surface.
Catalyst poisons
Catalyst poisons reduce the activity of the catalyst. They are either part of the synthesis gas or come from impurities in the catalyst itself, whereby the latter does not play a major role. Water, carbon monoxide, carbon dioxide and oxygen are temporary catalyst poisons. Sulfur - phosphorus - arsenic - and chlorine - connections are permanent poisons.
Chemically inert components of the synthesis gas mixture such as noble gases or methane are not actually catalyst poisons, but they accumulate through the cyclization of the process gases and thus reduce the partial pressure of the reactants , which in turn has a negative effect on the catalytic conversion.
Reaction engineering
Synthesis conditions
Temperature (° C) | K eq |
---|---|
300 | 4.34 × 10 −3 |
400 | 1.64 × 10 −4 |
450 | 4.51 × 10 −5 |
500 | 1.45 × 10 −5 |
550 | 5.38 × 10 −6 |
600 | 2.25 × 10 −6 |
The ammonia synthesis takes place at a nitrogen to hydrogen ratio of 1 to 3, a pressure of 250 to 350 bar, a temperature of 450 to 550 ° C and using α-iron as a catalyst according to the following equation:
The reaction is an exothermic equilibrium reaction that takes place with a reduction in volume, the mass action constant K eq of which results from the following equation:
- .
Since the reaction is exothermic, the equilibrium of the reaction shifts to the side of the ammonia at lower temperatures. Furthermore, four parts by volume of the raw materials produce two parts by volume of ammonia. In accordance with the principle of least constraint , high pressure therefore also favors the formation of ammonia. A high pressure is also necessary in order to ensure that the surface of the catalyst is adequately covered with nitrogen.
The ferrite (α-Fe) catalyst is created in the reactor by reducing magnetite with hydrogen. This is optimally effective from temperatures of around 400 to 500 ° C. The activation barrier for the cleavage of the triple bond of the nitrogen molecule is greatly reduced by the catalyst , but high temperatures are necessary for an adequate reaction rate. At the chosen reaction temperature, the optimum lies between the decomposition of ammonia into the starting materials and the effectiveness of the catalyst. The ammonia formed is continuously removed from the reaction system. The volume fraction of ammonia in the gas mixture is around 20%.
The inert components, especially the noble gases such as argon , must not exceed a certain level in order not to lower the partial pressure of the reactants too much. To remove the inert gas components, part of the gas is drawn off and the argon is separated out in a gas separation system . The extraction of pure argon from the cycle gas is possible using the Linde process.
Large-scale implementation
Modern ammonia plants produce more than 3000 tons per day in one production line. The following diagram shows the structure of a Haber-Bosch system.
Depending on the origin of the synthesis gas, it must first be freed of impurities such as hydrogen sulfide or organic sulfur compounds, which act as catalyst poisons. High concentrations of hydrogen sulphide, which occur in synthesis gas from smoldering cokes , are removed in a wet cleaning stage such as the Sulphosolvan process , while low concentrations are removed by adsorption on activated carbon . Organosulfur compounds are separated by pressure swing adsorption together with carbon dioxide after the CO conversion.
To produce hydrogen by means of steam reforming, methane reacts with water vapor with the aid of a nickel oxide- aluminum oxide catalyst in the primary reformer to form carbon monoxide and hydrogen . The energy required for this, the enthalpy Δ H , is 206 kJ / mol.
The methane gas is only partially converted in the primary reformer. In order to increase the yield of hydrogen and to keep the content of inert components as low as possible, in a second step the remaining methane gas is converted with oxygen into carbon monoxide and hydrogen. For this purpose, the secondary reformer is charged with air, with the nitrogen required for the subsequent ammonia synthesis also entering the gas mixture.
In a third step, the carbon monoxide is oxidized to carbon dioxide, which is referred to as a CO conversion or a water gas shift reaction .
Carbon monoxide and carbon dioxide combine with ammonia to form carbamates which, as solids , would quickly clog pipes and apparatus . In the following process step, the carbon dioxide must therefore be removed from the gas mixture. In contrast to carbon monoxide, carbon dioxide can easily be removed from the gas mixture by gas scrubbing with triethanolamine . The gas mixture then also contains noble gases such as argon and methane, which are inert .
The gas mixture is then compressed to the required operating pressure by means of turbo compressors. The resulting compression heat is dissipated by means of heat exchangers ; it is used to preheat raw gases.
The actual production of ammonia takes place in the ammonia reactor, whereby the first reactors burst under the high pressure, as the atomic hydrogen in carbon steel partially recombined to methane and cracked the steel. That is why Bosch developed tubular reactors, consisting of a pressure-bearing steel tube in which a casing made of low-carbon iron was inserted, into which the catalyst was filled. Hydrogen diffusing through the inner steel tube escaped to the outside through thin bores in the outer steel jacket, the so-called Bosch holes. The development of hydrogen-resistant chromium-molybdenum steels made it possible to construct single-walled tubes. A disadvantage of the tubular reactors was the relatively high pressure loss that had to be reapplied by compression .
Modern ammonia reactors are designed as floor reactors with a low pressure loss, in which the contacts are distributed as beds on about ten floors located one above the other. The gas mixture flows through them one after the other from top to bottom. Cold gas is injected from the side for cooling. A disadvantage of this type of reactor is the incomplete conversion of the cold gas mixture in the last catalyst bed.
Alternatively, the reaction mixture is cooled between the catalyst layers by means of heat exchangers, the hydrogen-nitrogen mixture being preheated to the reaction temperature. Reactors of this type have three catalyst beds. In addition to good temperature control, this type of reactor has the advantage of better conversion of the raw material gases compared to reactors with cold gas feed.
The reaction product is continually removed for maximum yield. For this purpose, the gas mixture is cooled from 450 ° C in a heat exchanger using water, freshly supplied gases and other process flows. The ammonia also condenses and is separated in a pressure separator. The as yet unconverted reactants nitrogen and hydrogen are compressed again to reaction pressure by means of a circulating gas compressor, supplemented with fresh gas and fed to the reactor. The ammonia is purified in a subsequent distillation.
Products
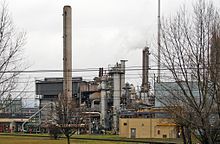
Most of the ammonia required annually is produced using the Haber-Bosch process. Annual production was around 150 million tons in 2017 with China , India and Russia as the largest producers. Due to the high energy requirements in the production of the pure hydrogen required, the Haber-Bosch process accounts for around 1.4 percent of the world's energy requirements . The resulting carbon dioxide emissions amount to around three to five percent of global emissions, some of which is used to generate urea. Today, around 40 percent of the nitrogen contained in the human body, at least among the population of industrialized nations, has already taken part in the Haber-Bosch synthesis.
About 80 percent of the primary product ammonia is processed into fertilizer, 20 percent is used for other products. The most important ammonia-based nitrogen fertilizers , in addition to gaseous and aqueous solutions of ammonia, are ammonium nitrate and urea .
The production of urea in a high pressure process goes back to Carl Bosch and Wilhelm Meiser and was first put into operation by BASF in 1922. In 2010 the production volume was 130 million tons. The entire world production of nitric acid takes place by catalytic combustion according to the Ostwald process . The process goes back to a lecture experiment in which a glowing platinum wire is immersed in a mixture of ammonia and air to generate nitrous gases . The world annual production amounted to 80 million tons in the year 2009. The most frequently produced by-product of nitric acid is ammonium nitrate ; the annual production in 2002 was about 39 million tons, of which about 80 percent is processed into fertilizers and 20 percent into explosives. Other secondary products such as potassium nitrate , phosphates partially or completely neutralized with ammonia such as mono- , di- and ammonium polyphosphates , ammonium sulfate and ammonium nitrate-urea solution are frequently used fertilizers.
About five percent of ammonia production is used to make explosives. The nitro and nitrate groups found in many explosives are ultimately based on ammonia, which was obtained using the Haber-Bosch process, including important explosives such as trinitrotoluene and nitroglycerin . About ten percent of ammonia production is used to make nitrogen-containing compounds such as nitriles , amines, and amides . The range of secondary products is extremely diverse and ranges from urea resins , sulfonamides to nitrobenzene and its secondary product aniline in polyurethane and dye chemistry, caprolactam for the production of polymers and through to rocket fuels such as hydrazine .
mechanism
Elementary steps
The mechanism of ammonia synthesis is divided into the following seven steps:
- Transport of the starting materials from the gas phase through the boundary layer to the surface of the contact
- Pore diffusion to the reaction center
- Adsorption of the reactants
- reaction
- Desorption of the products
- Return of the products through the pore system to the surface
- Return to the gas volume.
Because of the shell structure of the catalyst, the first and last two steps are fast compared to adsorption, reaction and desorption. Exchange reactions between hydrogen and deuterium on Haber-Bosch catalysts take place at a measurable rate even at temperatures of −196 ° C; The exchange between deuterium and hydrogen on the ammonia molecule also takes place at room temperature . Since both steps are fast, they cannot determine the rate of ammonia synthesis. It is known from various studies that the rate-determining step in ammonia synthesis is the dissociation of nitrogen.
The adsorption of nitrogen on the catalyst surface depends not only on the reaction conditions but also on the microscopic structure of the catalyst surface. Iron has different crystal faces , the reactivity of which is very different. The Fe (111) and Fe (211) surfaces have by far the highest activity. The explanation for this is that only these surfaces have so-called C7 sites - these are iron atoms with seven closest neighbors.
The dissociative adsorption of nitrogen on the surface follows the following scheme, where S * means an iron atom on the surface of the catalyst:
- N 2 → S * –N 2 (γ species) → S * –N 2 –S * (α species) → 2 S * –N (β species, surface nitride )
The adsorption of nitrogen is similar to the chemisorption of carbon monoxide. On an Fe (111) surface, the adsorption of nitrogen initially leads to an adsorbed γ-species with an adsorption energy of 24 kJmol −1 and an NN stretching vibration of 2100 cm −1 . Since nitrogen is isoelectronic with carbon monoxide , it adsorbs in an on-end configuration in which the molecule is bound via a nitrogen atom perpendicular to the metal surface. This was confirmed by photoelectron spectroscopy .
Ab initio - MO calculations have shown that in addition to the σ-Hinbindung the lone pair of the nitrogen to the metal a π back-donation from the d-orbitals is present the metal into the π * orbitals of the nitrogen containing the iron-nitrogen Bond strengthens. The nitrogen in the α state is more strongly bound with 31 kJmol −1 . The resulting weakening of the NN bond could be demonstrated experimentally by reducing the wave number of the NN stretching vibration to 1490 cm −1 .
Further warming of the Fe (111) surface, which is covered by α-N 2 , leads to both desorption and the appearance of a new band at 450 cm −1 . This represents a metal-N oscillation, the β-state. A comparison with the vibrational spectra of complex compounds allows the conclusion that the N 2 molecule is bound “side-on”, with an N atom in contact with a C7 site. This structure is known as "surface nitride". The surface nitride is very strongly bound to the surface. Hydrogen atoms (H ads ), which are very mobile on the catalyst surface , quickly add to this.
Surface imides (NH ad ), surface amides (NH 2, ad ) and surface ammoniaates (NH 3, ad ) that have been detected by infrared spectroscopy are formed , the latter disintegrating with release of NH 3 (desorption). The individual molecules were identified or assigned using X-ray photoelectron spectroscopy (XPS), high-resolution electron energy loss spectroscopy (HREELS) and IR spectroscopy.
On the basis of these experimental results, a reaction scheme can be created that consists of the following individual steps:
- H 2 + S * ⇌ 2 H ad
- N 2 + S * ⇌N 2, ad
- N 2, ad ⇌ 2 N ad
- N ad + H ad ⇌ NH ad
- NH ad + H ad ⇌ NH 2, ad
- NH 2, ad + H ad ⇌ NH 3, ad
- NH 3, ad ⇌ NH 3 + S *
As with every Haber-Bosch catalyst, the rate-determining step in ruthenium-activated carbon catalysts is nitrogen dissociation. The active center for ruthenium is a so-called B 5 site, a 5-fold coordinated position on the Ru (0001) surface, at which two ruthenium atoms form a step edge with three ruthenium atoms on the Ru (0001) surface . The number of B 5 positions depends on the size and shape of the ruthenium particles, the ruthenium precursor and the amount of ruthenium used. The reinforcing effect of the basic carrier has the same effect as the promoter effect of alkali metals , which is just as important here as with the iron catalyst.
Energy diagram
With the knowledge of the reaction enthalpy of the individual steps, an energy diagram can be created. With the help of the energy diagram, homogeneous and heterogeneous reactions can be compared: Due to the high activation energy of the dissociation of nitrogen, the homogeneous gas phase reaction cannot be carried out. The catalyst avoids this problem, as the energy gain resulting from the binding of nitrogen atoms to the catalyst surface overcompensates for the necessary dissociation energy, so that the reaction is ultimately exothermic . Nevertheless, the dissociative adsorption of nitrogen remains the rate-determining step: not because of the activation energy, but mainly because of the unfavorable pre-exponential factor of the rate constant. The hydrogenation is endothermic, but this energy can easily be applied by the reaction temperature (about 700 K).
Process variants
Since the introduction of the Haber-Bosch process, the synthesis of ammonia from atmospheric nitrogen has become one of the world's most important chemical manufacturing processes. The development of process variants at the beginning of the 20th century often served to circumvent BASF's patent claims. Since the process requires significant energy consumption , later developments focused on energy efficiency . The average energy consumption per ton of ammonia in 2000 was around 37.4 GJ, while the thermodynamically determined minimum is 22.4 gigajoules per ton.
Casale method
The Casale process was developed by Luigi Casale in the early 1920s . The process uses an iron catalyst, but works in contrast to the Haber-Bosch process with a pressure of around 800 to 1000 bar. This made the reactor smaller and allowed good temperature control thanks to an internal, central heat exchanger and the axial injection of cold gas.
The high operating pressure allowed the direct condensation of ammonia without absorption in water. By 1923 Casale had built 15 plants in Europe and the United States with a capacity of around 80,000 tons of ammonia per year; in 1927 the installed capacity was already 320,000 tons per year. At that time, Casale was BASF's only competitor. A total of more than 200 ammonia plants based on Casale's first generation of technology have been built worldwide.
Fauser method
The Fauser process, named after the Italian electrical engineer Giacomo Fauser , largely corresponded to the Haber-Bosch process, but used the electrolysis of water as a hydrogen source. The Fauser cell used 27% potassium hydroxide as the electrolyte and anodes and cathodes enclosed in asbestos , which ensured good separation of the gases produced. The process was introduced by Montecatini in the early 1920s .
Mont Cenis method
The Mont Cenis process was developed by Friedrich Uhde and first put into operation in 1926 at the Mont Cenis colliery . The process, also known as the low-pressure process, works at pressures of 80 to 90 bar and a temperature of 430 ° C. The catalyst used was an iron cyanide-alumina catalyst, which was more active than the catalyst developed by Mittasch. The milder process conditions made it possible to use cheaper steels for the construction of the reactors.
AMV procedure
Imperial Chemical Industries developed the AMV process in 1982 with a highly active iron-cobalt catalyst that works at a reaction pressure of 100 bar and a temperature of 380 ° C. Cobalt itself is hardly catalytically active, but serves to stabilize the contact through the formation of spinel phases with the aluminum oxide. In addition, when the contact is reduced, smaller iron crystallites of higher activity are formed.
A further development of the process is the LCA process (Leading Concept Ammonia) developed by ICI in 1988, which is designed for lower throughputs with the same energy input. The carbon dioxide, which is produced in a single-stage water-gas shift reaction, is removed by pressure swing adsorption .
Kellogg Advanced Ammonia Process
In 1992 MW Kellog developed a ruthenium-on-activated carbon catalyst that works at lower pressures and temperatures under the name Kellogg-Advanced-Ammonia-Process (KAAP). Due to the more active, but more expensive ruthenium catalyst, the pressure required is only about 40 bar. Alkali or alkaline earth metals such as cesium and barium are used as promoters . The catalyst is said to be about 10 to 20 times as active as the conventional iron catalyst.
Solid State Ammonia Synthesis
The direct electrolytic synthesis of ammonia from water and nitrogen using electrical energy circumvents the detour via hydrogen production from water. This increases the efficiency. The formation of ammonia takes place electrochemically according to the following equation:
The gross equation of the reaction is:
Since ammonia is a high-energy substance, a lot of electrical energy is required. This process is therefore only economical if very cheap electrical energy is available.
Web links
literature
- Gerhard Ertl : Elementary steps in heterogeneous catalysis. In: Angewandte Chemie . 102, No. 11, 1990, pp. 1258-1266, doi: 10.1002 / ange.19901021108 .
- Hans-Erhard Lessing : Bread for the World, Death to the Enemy. in: Stephan Leibfried et al. (Hg): Berlin's Wilde Energies - portraits from the history of the Leibniz Science Academy. de Gruyter, Berlin, 2015, ISBN 978-3-11-037598-5
- Sandro Fehr: The “nitrogen question” in the German war economy of the First World War and the role of neutral Switzerland . Nordhausen 2009, DNB 993295185 .
- Alwin Mittasch : History of the ammonia synthesis. Verlag Chemie, Weinheim 1951, DNB 453395902 .
- Robert Schlögl : Catalytic ammonia synthesis - a “neverending story”? In: Angewandte Chemie. 115, No. 18, 2003, pp. 2050-2055, doi: 10.1002 / anie.200301553 .
- Gerhard Ertl, Jens Soentgen : N: Nitrogen - an element makes world history. oekom Verlag, 2015, ISBN 978-3-86581-736-5 .
- Max Appl: Ammonia. Principles and Industrial Practice. Wiley-VCH, Weinheim 1999, ISBN 3-527-29593-3 .
- Dietrich Stoltzenberg: Fritz Haber, Carl Bosch and Friedrich Bergius - protagonists of high pressure synthesis . In: Chemistry in Our Time . tape 33 , no. 6 , 1999, p. 359-364 , doi : 10.1002 / ciuz.19990330607 .
Individual evidence
- ↑ a b Nitrogen (Fixed) - Ammonia. US Geological Survey, Mineral Commodity Summaries, January 2018.
- ^ Vaclav Smil: Nitrogen cycle and world food production. (PDF) World Agriculture 2. 9-1., 2011, accessed on February 20, 2019 (English).
- ↑ a b Peter H. Pfromm: Towards sustainable agriculture: Fossil-free ammonia. In: Journal of Renewable and Sustainable Energy. 9, 2017, p. 034702, doi: 10.1063 / 1.4985090 .
- ^ Fritz Haber: Memorial speech on Justus von Liebig. In: Journal for Applied Chemistry. 41, 1928, pp. 891-897, doi: 10.1002 / anie.19280413302 .
- ↑ a b c d e f g h Max Appl: Ammonia. In: Ullmann's Encyclopedia of Industrial Chemistry. Wiley-VCH Verlag, 2006, pp. 11-13, doi: 10.1002 / 14356007.a02 143.pub2
- ^ William Crookes: Address of the President before the British Association for the Advancement of Science, Bristol, 1898. In: Science. 1898, pp. 561-575, doi: 10.1126 / science.8.200.561
- ^ William Crookes: The Wheat Problem. Longmans, Green, and Co., London / New York / Bombay / Calcutta 1917.
- ↑ a b A. Hermann: Haber and Bosch: Bread from Air - The ammonia synthesis. In: Physics Journal. 21, 1965, pp. 168-171, doi: 10.1002 / phbl.19650210403
- ^ Nicodem Caro: Industries of calcium cyanamide and related processes. In: Journal for Applied Chemistry. 22, 1909, pp. 1178-1182, doi: 10.1002 / anie.19090222404
- ↑ John R. Anderson: Catalysis: Science and Technology. Verlag Springer, 1990, ISBN 3-642-64666-2 , p. 48.
- ↑ Hans-Erhard Lessing: Bread for the world, death to the enemy. in S. Leibfried (Hg): Berlins Wilde Energien de Gruyter, Berlin, 2015 p. 349
- ^ Thomas Hager: The Alchemy of Air: A Jewish Genius, a Doomed Tycoon, and the Scientific Discovery That Fed the World but Fueled the Rise of Hitler. Publisher Crown, 2008, ISBN 978-0-307-35178-4 , p. 96.
- ↑ Kristian Birkeland: On the oxidation of atmospheric nitrogen in electric arcs. In: Transactions of the Faraday Society. 2, 1906, pp. 98-116, doi: 10.1039 / tf9060200098
- ↑ Fritz Haber, G. van Oordt: About the formation of ammonia in the elements. In: Journal of Inorganic Chemistry. 44, 1905, pp. 341-378, doi: 10.1002 / zaac.19050440122
- ↑ Patent US971501 : Production of ammonia. Published September 27, 1910 , inventors: Fritz Haber, Robert Le Rossignol.
- ↑ Patent DE235421A : Process for the synthetic preparation of ammonia from the elements. Published October 13, 1908 .
- ^ A b c d Carl Bosch: The Development of the Chemical High Pressure Method During the Establishment of the New Ammonia Industry. Speech on the award of the Nobel Prize on May 21, 1932.
- ↑ Armin Hermann, Charlotte Schönbeck (ed.): Technology and science (technology and culture). Springer, 1991, ISBN 3-540-62259-4 , pp. 441-442.
- ↑ Manfred Baerns, Arno Behr, Axel Brehm: Technical chemistry. Textbook . Wiley-VCH, 2006, ISBN 3-527-31000-2 , p. 623.
- ^ A b Alwin Mittasch: Comments on catalysis. In: Reports of the German Chemical Society (A and B Series). 59, 1926, pp. 13-36, doi: 10.1002 / cber.19260590103
- ↑ Werner Abelshauser, Wolfgang von Hippel, Jeffrey Alan Johnson: The BASF. From 1865 to the present. CH Beck Verlag, 2002, ISBN 3-406-49526-5 , p. 171.
- ↑ David Turnock: The Eastern European Economy, 1800-1989: Stages of Transformation in a peripheral region. Routledge Chapman & Hall, 2005, ISBN 1-4039-3287-5 , p. 197.
- ^ Harm G. Schröter: The international nitrogen cartel 1929-1939. In: Harm G. Schröter, Clemens A. Wurm (eds.): Politics, economics and international relations, studies on their relationship in the period between the world wars . Mainz 1991, ISBN 3-8053-1255-5 , pp. 129-130.
- ^ A b Vaclav Smil: Enriching the Earth: Fritz Haber, Carl Bosch, and the Transformation of World Food Production. MIT Press, 2001, ISBN 0-262-69313-5 , p. 242.
- ↑ Wolfgang Zollitsch: Workers between the World Economic Crisis and National Socialism: a contribution to the social history of the years 1928 to 1936. Vandenhoeck & Ruprecht, 1990, ISBN 3-525-35751-6 , pp. 22-24.
- ↑ Hans-Erhard Lessing: Robert Bosch. Rowohlt, Reinbek near Hamburg, 2007, ISBN 978-3-499-50594-2 , p. 142.
- ^ Nitrogen (Fixed) - Ammonia - Supply-Demand Statistics. US Geological Survey, Historical Statistics for Mineral and Material Commodities in the United States, Data Series 140, 2015.
- ↑ a b c d Roman J. Press u. a .: Introduction to hydrogen technology . John Wiley & Sons, 2008, ISBN 978-0-471-77985-8 , pp. 99-125.
- ↑ Patent US2083795 : Production of hydrogen. Published on June 15, 1937 , inventors: Georg Schiller, Gustav Wietzel.
- ↑ Vaclav Smil: Enriching the Earth: Fritz Haber, Carl Bosch, and the Transformation of World Food Production. MIT Press, 2001, ISBN 0-262-69313-5 , p. 113.
- ↑ Fangming Jin (Ed.): Application of Hydrothermal Reactions to Biomass Conversion. Springer, 2014, ISBN 978-3-642-54457-6 , p. 221.
- ↑ Friedrich Asinger: Introduction to Petrochemistry . Akademie-Verlag, Berlin 1959, p. 138.
- ↑ a b c d e f g h i Max Appl: Ammonia. Principles and industrial practice . Wiley-VCH, Weinheim et al. 1999, ISBN 3-527-29593-3 , pp. 17–64 ( limited preview in Google Book Search).
- ^ WK Jozwiak, E. Kaczmarek u. a .: Reduction behavior of iron oxides in hydrogen and carbon monoxide atmospheres. In: Applied Catalysis A: General. 326, 2007, pp. 17-27, doi: 10.1016 / j.apcata.2007.03.021
- ↑ Gerhard Ertl: To the mechanism of ammonia synthesis. In: News from chemistry, technology and the laboratory. 31, 1983, pp. 178-182, doi: 10.1002 / nadc.19830310307
- ↑ Michael Bowker: PhD in Ammonia Synthesis . In: DA King, DP Woodruff (Eds.): The Chemical Physics of Solid Surfaces . Volume 6: Coadsorption, promoters and poisons . Elsevier, 1993, ISBN 0-444-81468-X , Chapter 7, pp. 225-268 .
- ↑ a b c d Zhixiong You, Koji Inazu, Ken-ichi Aika, Toshihide Baba: Electronic and structural promotion of barium hexaaluminate as a ruthenium catalyst support for ammonia synthesis . In: Journal of Catalysis . tape 251 , no. October 2 , 2007, doi : 10.1016 / j.jcat.2007.08.006 .
- ↑ F. Rosowski, A. Hornung, O. Hinrichsen, D. Herein, M. Muhler: Ruthenium catalysts for ammonia synthesis at high pressures: Preparation, characterization, and power-law kinetics . In: Applied Catalysis A: General . tape 151 , no. April 2 , 1997, doi : 10.1016 / S0926-860X (96) 00304-3 .
- ↑ a b Jürgen Falbe: Römpp-Lexikon Chemie (H – L) , Georg Thieme Verlag, 1997, ISBN 3-13-107830-8 , pp. 1644–1646.
- ↑ Theodore L. Brown, H. Eugene LeMay, Bruce Edward Bursten, Linda Sue Brunauer (Eds.): Chemistry the Central Science. 9th edition. Prentice Hall, Upper Saddle River, NJ 2003, ISBN 0-13-038168-3 .
- ^ A b c A. F. Holleman , E. Wiberg , N. Wiberg : Textbook of Inorganic Chemistry . 102nd edition. Walter de Gruyter, Berlin 2007, ISBN 978-3-11-017770-1 , pp. 662-665.
- ^ Boy Cornils, Wolfgang A. Herrmann, M. Muhler, C. Wong: Catalysis from A to Z: A Concise Encyclopedia. Verlag Wiley-VCH, 2007, ISBN 978-3-527-31438-6 , p. 31.
- ↑ Focus on chemistry, upper level, introductory phase. Cornelsen-Verlag, Berlin 2010, ISBN 978-3-06-013953-8 , p. 79.
- ↑ P. Häussinger u. a .: Noble Gases. In: Ullmann's Encyclopedia of Industrial Chemistry. Wiley-VCH, Weinheim 2006, doi : 10.1002 / 14356007.a17_485
- ↑ E. Leibnitz, H. Koch, A. Götze: About the pressureless processing of lignite coke oven gas to strong gas according to the Girbotol process. In: Journal for Practical Chemistry. 13, 1961, pp. 215-236, doi: 10.1002 / prac.19610130315
- ↑ a b Dirk Steinborn: Fundamentals of organometallic complex catalysis. Teubner, Wiesbaden 2007, ISBN 978-3-8351-0088-6 , pp. 319-321.
- ^ A b c Detlef Forst, Maximillian Kolb, Helmut Roßwag: Chemistry for engineers. Springer Verlag, 1993, ISBN 3-662-00655-3 , pp. 234-238.
- ↑ Patrick Heffer, Michel Prud'homme: Fertilizer outlook 2010–2014. In: 78th IFA Annual Conference, Paris. 31, 2010, p. 6.
- ↑ Celeste LeCompte: Fertilizer plants spring up to take advantage of US's cheap natural gas. In: Scientific American. 2013. (online)
- ↑ TE Crews, MB Peoples: Legume versus fertilizer sources of nitrogen: ecological tradeoffs and human needs. In: Agriculture, Ecosystems & Environment. 102, 2004, pp. 279-297, doi: 10.1016 / j.agee.2003.09.018 .
- ↑ Jan Willem Erisman, Mark A. Sutton, James Galloway, Zbigniew Klimont, Wilfried Winiwarter: How a century of ammonia synthesis changed the world. In: Nature Geoscience. 1, 2008, pp. 636-639, doi: 10.1038 / ngeo325
- ↑ Patent US1429483 : Process of manufacturing urea. Published on September 19, 1922 , inventors: Carl Bosch, Wilhelm Meiser.
- ↑ a b c d e M. Bertau, A. Müller, P. Fröhlich, M. Katzberg: Industrielle Inorganische Chemie , 2013, Wiley-VCH, ISBN 978-3-527-33019-5 , pp. 31-37.
- ↑ Dirk Steinborn: Fundamentals of organometallic complex catalysis. Teubner, Wiesbaden 2007, ISBN 978-3-8351-0088-6 , p. 7.
- ↑ Allen V. Barker, David J. Pilbeam (Eds.): Handbook of Plant Nutrition . CRC Press, 2006, ISBN 0-8247-5904-4 , p. 40.
- ↑ Jacqueline Akhavan: Chemistry of Explosives . Royal Society of Chemistry, 2011, ISBN 978-1-84973-330-4 , pp. 44-46.
- ^ AF Holleman , E. Wiberg , N. Wiberg : Textbook of Inorganic Chemistry . 102nd edition. Walter de Gruyter, Berlin 2007, ISBN 978-3-11-017770-1 , pp. 675-680.
- ^ Walter J. Moore, Dieter O. Hummel: Physikalische Chemie . Walter de Gruyter, Berlin 1983, ISBN 3-11-008554-2 , p. 604.
- ↑ G. Ertl, SB Lee, M. Weiss: Kinetics of nitrogen adsorption on Fe (111). In: Surface Science. 114, 1982, pp. 515-526, doi: 10.1016 / 0039-6028 (82) 90702-6 .
- ↑ a b SB Lee, M. Weiss: Adsorption of nitrogen on potassium promoted Fe (111) and (100) surfaces . In: Surface Science . tape 114 , no. 2-3 , February 1982, pp. 527-545 , doi : 10.1016 / 0039-6028 (82) 90703-8 .
- ↑ a b Gerhard Ertl: Reactions at Solid Surfaces . John Wiley & Sons, 2010, ISBN 978-0-470-26101-9 , pp. 123 ( limited preview in Google Book search).
- ↑ Jeppe Gavnholt, Jakob Schiøtz: Structure and reactivity of ruthenium nanoparticles. In: Physical Review B. 77, 2008, doi: 10.1103 / PhysRevB.77.035404 .
- ^ J. Ruddock, TD Short, K. Brudenell: Energy integration in ammonia production. In: WIT Transactions on Ecology and the Environment. 62, 1970, doi: 10.2495 / EENV030251 .
- ↑ James A. Kent (Ed.): Kent and Riegel's Handbook of Industrial Chemistry and Biotechnology . Verlag Springer, 2007, ISBN 978-0-387-27842-1 , pp. 998-999.
- ↑ Patent US1478550 : Catalytic apparatus for the synthesis of ammonia. Published December 25, 1923 , inventor: Luigi Casale.
- ^ A b Casale SA: Ammonia - The development of technology. Retrieved June 27, 2016.
- ↑ Patent US1495681 : Electrolyzer for producing hydrogen and oxygen. Published May 27, 1924 , inventor: Giacomo Fauser.
- ^ Jean Billiter: The technical electrolysis of non-metals. Verlag Springer, 1954, ISBN 978-3-7091-5728-2 , pp. 42-44.
- ↑ Bernhard Neumann (Ed.): Textbook of chemical technology and metallurgy: I Fuels Inorganic branches of industry. Verlag Julius Springer, 1939, ISBN 978-3-642-92056-1 , pp. 408-409.
- ↑ Huazhang Liu: Ammonia Synthesis Catalysts: Innovation and Practice . World Scientific Pub., 2013, ISBN 978-981-4355-77-3 , pp. 739-740.
- ^ JR Jennings: Catalytic Ammonia Synthesis. Fundamentals and Practice. Springer Science and Business Media, 1991, ISBN 1-4757-9594-7 , p. 353.
- ^ Gary Maxwell: Synthetic Nitrogen Products: A Practical Guide to the Products and Processes. Verlag Springer, 2004, ISBN 0-306-48225-8 , pp. 181-182.
- ^ Anne K. Rhodes: New ammonia process, catalyst proven in Canadian plant. In: Oil and Gas Journal. 47, 1996 (online)
- ↑ Hubert Bielawa, Olaf Hinrichsen, Alexander Birkner, Martin Muhler: The Ammonia-Synthesis Catalyst of the Next Generation: Barium-Promoted Oxide-Supported Ruthenium. In: Angewandte Chemie International Edition. 40, 2001, pp. 1061-1063, doi : 10.1002 / 1521-3773 (20010316) 40: 6 <1061 :: AID-ANIE10610> 3.0.CO; 2-B .
- ↑ Rong Lan, John TS Irvine, Shanwen Tao: Synthesis of ammonia directly from air and water at ambient temperature and pressure. In: Scientific Reports. 3, 2013, doi: 10.1038 / srep01145 .