steel

Steel is a material that consists largely of iron . Steel can be hot or cold formed , so it can be rolled , bent , drawn and forged .
Frequently steel as the iron is carbon - alloy with a carbon mass fraction defined by a maximum of 2%. Iron-carbon alloys with a higher carbon content are called cast iron and cannot be plastically deformed, so they cannot be forged or rolled. In addition to carbon, steel always contains residues of undesired phosphorus , sulfur and some other impurities. Some types of steel also contain other elements that have been specifically alloyed to improve the properties of the steel. The proportions of accompanying and subsequently added alloying elements as well as the heat treatment condition are decisive for the properties of the steel .
Steel is one of the most versatile construction materials and can be recycled almost indefinitely . Its production (in 2016: 1629 million tons) exceeds the amount of all other metallic materials combined by more than ten times. Steel is available in large quantities and at low cost. Its properties can be varied over a wide range by alloying and heat treatment .
Steel can be processed by casting and above all by rolling, forging, milling and welding and has a high strength (simple steel between 180 and 350 N / mm², high-strength steel up to well over 1200 N / mm²), good hardenability , rigidity ( Modulus of elasticity ) and elongation at break .
Coal and steel ( mining industry ) have long been the main pillars of heavy industry and the basis for the political power of a state.
Word origin
The word “steel” developed from the Middle High German stahel, stāl, the Old High German word stahal , the Middle Low German stāl, the Middle Dutch stael and the an. stál; next to it the j-formation as. stehli 'ax' and ae. stīle.
Terms
DIN EN 10020 - Definitions for the classification of steels
![]() |
DIN EN 10020 |
---|---|
Area | Materials |
title | Definitions for the classification of steels |
Brief description: | Steel, definitions |
Latest edition | 2000-07 |
ISO |
In DIN EN 10020: 2000–07 definitions of terms for the classification of steels , the following is stated under point 2.1:
“[Steel is a] material whose mass fraction of iron is greater than that of any other element, whose carbon content is generally less than 2%, and which contains other elements. A limited number of chrome steels can contain more than 2% carbon, but 2% is the usual limit between steel and cast iron . "
The limit carbon content of 2% is derived directly from the iron-carbon diagram . The material can be in the form of austenite up to a content of 2.06%, which can be easily formed.
Specialist literature
The definitions used in the specialist literature are based on DIN EN 10020 and all contain the definition as ferrous material with a carbon content of less than 2%. In addition, however, it is always emphasized that steels are formable, i.e. can be processed by forging, rolling and similar processes .
Use of terms in the history of technology
This general definition, which has been in use since the early 20th century, also includes the term steel , wrought iron , which was hardly produced at that time and which has a low carbon content of usually less than 0.3%. It is then not hardenable and has a different area of application. Despite its similar composition to steel, it is not identical to steel due to various impurities. When "steel" is used in a historical context in modern works (from the 20th century), it usually means "wrought iron". Even in works on the history of technology , the term steel is used for earlier forgeable iron materials. The term wrought iron was used in antiquity to differentiate it from pig iron , which was still very heavily contaminated, and from the Middle Ages onwards also from non-forgeable cast iron .
history
Simple forgeable iron materials were already produced by the Hittites around 3500 years ago. B. for weapons . The early smelting of iron ore dates back to the 2nd millennium BC. In the then Hittite Empire, where also around the middle of the 1st millennium BC. BC a simple hardenable steel was probably made for the first time. Iron gradually displaced the previously used copper materials ( bronze ), because as steel it is hardenable and at the same time tougher. Iron was mainly used for weapons and armor as well as for tools, less in agriculture. Iron ores could be found almost everywhere, while the metals copper and tin required for bronze production were rare and did not occur in the same places. Charcoal , which could be obtained from wood, was needed to extract iron .
Antiquity
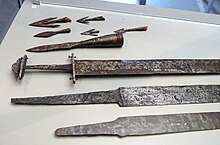
In ancient times and in the Middle Ages , the ore was smelted in charcoal- heated racing furnaces at temperatures of around 1250 ° C. The iron ore was converted into semi-solid iron and liquid slag , which contains various undesirable constituents of the ores. The furnace was pierced at the bottom so that the slag could run out (hence the name racing furnace, from rinnen ). The product was porous, solid pig iron that still contained slag residues that were removed by forging. Afterwards it was called wrought iron, which contained almost no carbon and came very close to today's steel, but was obtained in a different way and was therefore more heavily contaminated with accompanying elements. Aristotle differed in any case already in the Meteorologica the pig iron from wrought iron , which contains no more slag residues. Since the low-carbon iron is too soft for tools and weapons, it was annealed on charcoal, which consists mainly of carbon, whereby it absorbed the element carbon mainly in the outer layers. Also, the hardening by quenching in water or oil has been known and used by Plutarch explained (45-125 n. Chr.) Correctly by the rapid cooling. Before that, Pliny the Elder (24–79 AD) was of the opinion that the water quality had the decisive influence.
Blacksmiths and fine smiths emerged as new professions that now used iron, in contrast to coppersmiths . Other blacksmiths specialized in certain products or product groups. These include the tool , knife , sickle, nail, sword , helmet, lance or arrow blacksmith and locksmith. In ancient times, the necessary work was often done by slaves.
middle Ages
In the early Middle Ages, village handicrafts produced scythes , sickles and plows for agriculture . Hammer mills and bellows powered by windmills or water mills were developed. In the 14th century AD, the charcoal blast furnace (piece furnace) was developed in Europe . It reached higher temperatures and needed less coal. The iron ore reacted with the carbon in the charcoal. Thanks to the carbon content, the melting temperature was now below the blast furnace temperature, so that liquid pig iron was produced for the first time, which, however, was not malleable due to the high carbon content of around 4%. It was similar to today's cast iron and was also cast in molds. In order to obtain forgeable iron, the pig iron from the blast furnace was melted again in a fresh fire . The properties of iron could be specifically influenced by tempering , carburizing , quenching and annealing . The Benedictine monk Theophilus Presbyter described the hardening of files in the 11th century: First ox horn was burned and mixed with salt and sprinkled over the files, which were then annealed in the oven. They were then quenched in water and tempered in the oven. Wire was originally twisted and forged as in ancient times. In the Middle Ages, wire drawing with a drawing iron was used in order to manufacture the large quantities of wire that were mainly needed for ring armor ("chain mail").
At the beginning of the Middle Ages, there was little division of labor . Blacksmiths and fine blacksmiths often worked in the same forge. Later, the division of labor was similar to that in antiquity, to which new professions such as blacksmith, pan, plow and tong smith as well as file cutter contributed. In addition to the professional division of labor, there were also regional differences. In the area around Solingen there were numerous hammer mills driven by water mills on tributaries of the Wupper , on which blades were forged. The grinding mills for the blades required more energy for finishing and were therefore located directly on the Wupper. However, these separate production stages required the transport of the forged blades from the secondary runs to the Wupper, which meant that up to an hour's walk had to be spent on transport.
industrialization

The production of usable iron from ores took place in several steps:
- Smelt the ores in the blast furnace into pig iron,
- Refining the pig iron to reduce the carbon content and then
- Forging and rolling into bars, rails or sheets.
What was new was the technical implementation of these processes, which was now based primarily on hard coal and therefore made ferrous materials cheaper and increased production volumes. In production engineering, iron or steel could now be used as a construction material for machine tools, making them more precise and efficient. Most of the iron, however, was used for steam locomotives and rails, as well as bridges.
For the smelting of the ores in the blast furnace, it was necessary that the ore came into contact with coal, as the carbon was required for chemical reactions. This was not a problem with charcoal, which consists almost entirely of carbon, but the cheaper hard coal was heavily contaminated with sulfur and other elements that made the product worse. Abraham Darby came up with the idea of coking hard coal. The main product was coke , which could be used for smelting the ores, and tar as a by-product . As the tar pits near the ironworks continued to fill up, chemists became aware of this and found methods of making tar paints and medicines from them. A significantly lower coal / coke consumption was possible with the hot air blowing from James Beaumont Neilson . The air supplied to the furnace was heated, which resulted in higher temperatures and better steel.
There were two different methods of freshening with coal to shield the iron from the sulfur in the coal. From 1740 developed Benjamin Huntsman the crucible steel in the steel in crucibles given several days and was heated in a coal fire long. The result was a homogeneous steel of excellent quality. Because of its relatively high hardness, it was preferred for cutting tools, but also for anvils, hammers and other tools. However, it was very expensive and could only be produced in small quantities.
The more important method was puddling , which was invented by Henry Cort in 1784 . When puddling, the pig iron was placed in large crucibles on a stove under which coal was burned. The liquid pig iron was stirred manually with iron rods (= puddling ), came into contact with the oxygen in the air and burned the carbon contained in the iron. Since the low-carbon iron has a higher melting point, lumps, which finally formed Luppen anwuchsen and were taken out of the oven. To ensure that all parts of the melt came into uniform contact with oxygen, workers had to constantly stir the melt vigorously, which required a lot of experience. The quality of the steel produced thus crucially depended on the puddlers. The puddling while enabling greater production volumes as above, but was a manual procedure, which could not be mechanized, and formed in the bottleneck of the whole process chain from ore to finished product.
The iron, which was refined by puddling, was then worked under the forge hammer to remove the slag residue and make the material more homogeneous. This forging process also had a major impact on the quality of the steel. Only then was it rolled into sheets or rails.
Friedrich Krupp founded the first German cast steel factory in Essen in 1811. The impetus for the sudden increase in steel production came about in the middle of the 19th century through the simultaneous application of several technical inventions: the steam engine provided the industry with a powerful and flexible workforce, in the coking plants the coal was processed into coke and the development the railways and steam shipping promoted the accessibility of new, large sales markets for steel.
The steel industry was of enormous political importance in all countries, regardless of economic considerations, since it was not only an indicator of technical and economic development and its importance for the armaments industry, but also a question of national prestige. The importance of steel for that time is symbolized by the Eiffel Tower (still made of puddle iron because of the high demands on break resistance ), which was built from steel as a monument to technical progress on the occasion of the Paris World Exhibition in 1889 .
High industrialization and mass steel processes
High industrialization is part of the first wave of industrialization in which the leading states finally changed from an agricultural to an industrial state. There are various definitions and delimitations of what exactly is meant by high industrialization : in part, it means high industrialization in Germany between 1870 and 1914, and in part it also means the second industrial revolution . The most important innovations concern the development of processes for the mass production of cheap and at the same time high-quality steel and the rationalization movement, which went hand in hand with more economical production.
The bottleneck in steel production was still freshening in the puddle furnace. Pig iron could be melted in good quality and in sufficient quantities in the steadily growing blast furnaces. The further processing of the puddle iron in mechanized rolling mills also happened quickly. In order to meet the great demand from the railway industry, some attempts were made to mechanize puddling as well, but this was unsuccessful. The experience of the puddlers could not simply be translated into machines. This was remedied by three competing processes: the two bottom blowing or wind-freshening processes by Bessemer and Thomas and stove freshening by Siemens and Martin.
Bessemer method
In the 1850s, Henry Bessemer came up with the idea of putting the liquid pig iron into a converter and blowing air through nozzles in the ground. The oxygen contained in the air burned the carbon and other undesirable accompanying elements in just 20 minutes and at the same time heated the pig iron, so that the refurbished steel was now liquid and could be cast for the first time. The process of blowing air through pig iron is also known as wind freshening. With the Bessemer process , it was only possible to generate and maintain the highest temperatures in the metallurgy system up to that point with air, and in doing so did not consume fuel as in the past, but also generated heat. The process was therefore significantly cheaper. In addition, the Bessemer steel was of very good quality: It was very pure and homogeneous and, thanks to its great hardness, withstood the loads to which it was exposed as a rail material. Puddle iron rails, on the other hand, usually had to be replaced after 10 years. In the USA in particular, numerous Bessemer systems were built in the late 1860s and early 1870s. However, the process had two disadvantages. It was only suitable for low-phosphorus ores, which were rare in Germany in particular, and the chemically neutral nitrogen in the air dissolved in the structure of the steel and made it hard but also brittle. In addition, almost all of the carbon was burned during the refining process, so Bessemer steel was not particularly strong.
Thomas method
The Thomas process by Sidney Thomas and Percy Gilchrist has been a variant of the Bessemer process since 1878, which was suitable for ores rich in phosphorus and was therefore used primarily in regions on the Rhine and Ruhr , in Belgium , Luxembourg and Lorraine . However, it also required a certain minimum content of phosphorus, so that there was little interest in it in England and America, as corresponding ores were not found here. Thomas steel was even harder and more brittle than Bessemer steel and was more suitable for less stressed cases such as wire or pipes and less for bridge or ship building.
Siemens-Martin process
An alternative to the two bottom-blowing or wind-freshening processes was the Siemens-Martin process, which is counted as stove freshening and is named after the three brothers of the famous Werner von Siemens , Friedrich , Otto and Wilhelm, and the French ironworker Pierre Martin . The process was based on a special oven in which the air supplied was heated strongly before it was ignited. Instead of heating the stove with this hot air, one heated another stream of air, which was now even hotter than the first. In this way, temperatures could now be permanently maintained that were above the melting temperature of steel. After several hours the steel was freed from the accompanying elements. Due to the slower process, the desired carbon content could be set very precisely. In addition, no nitrogen dissolved in the steel, so that the Siemens-Martin process resulted in a higher quality steel, which, however, was somewhat more expensive due to the more complex process. Most of the steel, however, was produced using this process until 1960, as it was also excellent for recycling scrap.
Elimination of forging
The forging of the rounds after puddling in order to homogenize the material could be dispensed with with the new processes, as they all produced liquid steel, which was already much more homogeneous than puddle iron could ever be. However, steelmakers were reluctant to give up forging, as a thorough forging process was the hallmark of good steel. For a long time, customers in particular could not believe that a better product was possible with less effort. Krupp was the last industrialist in Germany to give up forging, but forbade his representatives to reveal that Krupp steel, which was known for its high quality, was only rolled.
Fast operation
A rationalization movement gradually established itself in America at the end of the 19th century , which culminated in the early 20th century. At that time, rationalization was primarily understood to mean increasing the economic efficiency of production. The aim was to produce as much as possible with the existing workers and equipment or to produce a certain amount of production at the lowest possible cost. Only with the organizational principles that resulted from this was the real potential of the new technologies fully exploited - not only in the steel industry, but in all trades.
Although the steel in a converter in the Bessemer works was refined after only 20 minutes, only five to six batches could be produced per day. The converter was idle for the rest of the time. This was mainly due to the high need for repairs to the converter floors, which were worn out after six batches at the latest and had to be repaired for around 10 hours. In Europe people tried to use new materials that are more heat resistant. In America, where there was a very great need for steel, they didn't dwell on it for long. You simply changed the entire floor in a few minutes and then continued production. As a result, the output per converter rose to 48 per day within a few years and later to 72 on peak days. The cost of the soil, on the other hand, did not play a major role. American steelworks now produced around the clock and thus for the first time both fast and well, which particularly impressed observers from Europe. Because up to now, producing well meant producing slowly and thoroughly. This production method in the steel industry was called English hard driving in America and fast operation in Germany .
20th century

Electric current enabled the production of so-called electric steel with the arc furnaces, which were new at the time . These steel mills were excellent scrap recyclers, but played only a subordinate role in the overall market. As before, three different processes were in competition here: the Bessemer and Thomas processes with the somewhat cheaper steel and the Siemens-Martin process with the better quality steel. In the Bessemer and Thomashütten they tried to improve the quality and thus to achieve the longed for "Siemens-Martin equality", but this did not succeed. However, all processes were extremely productive, so that there was overcapacity for the first time. So far, attempts have been made to optimize the costs of individual systems; the production volume was a resultant quantity. Now, like the market price, it was determined by cartelization , group formation , protective tariffs and other economic influences. In the vertically integrated steel groups, with their ore mines, blast furnaces, Bessemer or Siemens-Martin smelters and the rolling mills, it was now a matter of minimizing costs for the entire company.
Integrated smelting works
In order to increase efficiency, integrated smelting works were soon created to recycle by-products. In the blast furnace, for example, what is known as blast furnace gas is produced , which has long been used to heat the blast furnace wind. However, only about 20% of the gas was used. Now attempts were made to use it further: First, it was burned in the steam engines of the rolling mill drives. This created a rigid technical link between the number of blast furnaces and the number of rolling mills. When the company switched to electric drives, it was used to drive generators instead: the gas was "converted into electricity". In addition, the liquid pig iron from the blast furnace began to be fed directly into the converters (Bessemer and Thomas processes) or Siemens-Martin furnaces without remelting it, which is more energy-efficient. The refined iron was allowed to cool just enough to set and then rolled. In the ideal case, the heat generated in the blast furnace was sufficient for the entire process, which was known as “ rolling in one heat ”. The slag, which had always been falling off, was now processed into sand, stone and cement. The slag from the Thomas works was particularly popular because it contains a high proportion of phosphates and can therefore be processed into fertilizer . The Thomas works were even among the largest fertilizer manufacturers. This Thomas credit contributed significantly to the cost advantages of the procedure, since the Thomasstahl was cheaper by this credit.
Chrome-nickel steel
In the chemical industry, some processes, such as the Haber-Bosch process for the production of ammonia, which was new at the time, required very high pressures and temperatures of up to 330 bar and 550 ° C. The hydrogen involved in the process diffused into the steel of the reactor walls, dissolved the carbon it contained and thereby reduced the strength of the steel, which led to reactor explosions. As a result, high-alloy steels were developed that do not get their strength from carbon but from other alloying elements and are therefore more chemically resistant. The most important representative is the austenitic , rustproof chrome-nickel steel . The new steels and chemical processes thus helped each other to achieve an industrial breakthrough.
Economical meaning
For the German National Socialists, who had launched an extensive armaments program in 1935, steel was an important material for the war effort. The Norwegian campaign was aimed, among other things, at securing supplies of Swedish iron ore, which was an indispensable raw material for steel production at the time. The Allies bombed the Ruhr area, the largest steel-producing region in Europe. At the end of the war, the air raids had destroyed around 20% of the production capacity. It was not until 1957 that the pre-war level was reached again with crude steel production of 16 million tons.
The demilitarization of the German Reich decided at the Potsdam Conference also included dismantling the steel industry. Some of the dismantled factories went to the Soviet Union , which needed them to rebuild the country destroyed by the war. Resistance to dismantling soon arose in the western occupation zones, and so the Allies stopped dismantling as early as 1949. Another measure taken by the allied control authority was the so-called "unbundling" of the steel industry. This should prevent the renewed emergence of dominant company mergers such as the " United Steel Works ".
To ensure joint control of coal and steel production, was 1952 French initiative, the ECSC founded. The European Union then gradually developed from the coal and steel union . As a result, the steel industry in the Federal Republic of Germany experienced a great boom. In 1961, 420,568 employees produced 33 million tons of crude steel, which was a peak in the number of employees. The West German steel industry set a production record in 1974 when it produced over 53 million tons of steel. Today the steel industry in reunified Germany needs around 76,500 employees to produce around 46 million tons of steel (as of 2008). This enormous increase in productivity was only possible through significant technical innovations.
According to expectations of the steel industry, the demand for steel in the automotive industry will increase by 4.2 million t by 2050 due to the emergence of electric mobility.
Areas of application and competing materials
Steel is the standard material in mechanical engineering and an important building material in construction. The sub-discipline of civil engineering that deals with the special features of steel structures is steel construction . Of the steel used in Germany, 35% is used in the construction industry , 26% in the automotive industry , 12% in metal goods , 11% in mechanical engineering and 9% in pipes (as of 2017).
Steel is used for numerous different machines , including pumps , cranes , conveyor systems , turbines or milling machines , for steel cables , bridges and building construction , in reinforced concrete , for weapons and tools of all kinds, for pipes and chemical apparatus , pressure vessels , rails , ships , cars and motorcycles .
In branches of industry where emphasis is placed on lightweight construction (in particular vehicle and aircraft construction as a whole), lower- density materials such as titanium , aluminum , magnesium , plastics and fiber composites can be used instead of steel . However, since the other metallic materials often have a lower strength and hardness compared to steel, the weight advantage can be compensated for by the targeted use of high-strength steels and structural measures - such as the processing of thinner sheet metal with recesses and beads . Fiber composite materials sometimes have significantly higher strength and rigidity in the direction of the fibers, but construction and processing differ significantly from metallic materials and, above all, are significantly more complex.
Production quantities
1629 million tons of steel were produced worldwide in 2016. That is more than ten times all other metallic materials put together. Of aluminum, the second most important metallic material, only 115 million tons were produced in 2016. By far the most important manufacturing country was the People's Republic of China with a share of 50 percent. The largest producer after China is Japan with 6.4%. 10 % of world production is produced in the EU and 6.8% in North America ( NAFTA ). See also steel / tables and graphics .
In Germany, around 43 million tons of crude steel were produced in 2014 with 87,000 employees.
For a long time, steel production was at a relatively low level: According to estimates, between 20,000 t and 30,000 t of steel were produced annually in the German-speaking countries in the Middle Ages. Around 1950 world production exceeded 200 million tons for the first time, until the mid-1970s it rose further to 700 million tons and remained at this level with minor fluctuations until the turn of the millennium. Since then, it has increased further to over 1,000 million tons, with the increase being almost exclusively due to China.
Manufacturing, recycling and ecology
Manufacturing
Of iron ore is pig iron produced by it along with coke (degassed carbon) in a blast furnace is given. On the one hand, the coke heats the ore through combustion and, on the other hand, serves as a reducing agent for the ore, which chemically consists of iron oxide. The resulting pig iron serves as the raw material for steel production. It contains around 4% carbon and various impurities.
The process in which the content of carbon and other elements in the pig iron is reduced is called refining , which means nothing other than that the undesirable accompanying elements silicon , manganese , sulfur and phosphorus are burned by adding oxygen . Today relatively insignificant fresh processes are the Siemens-Martin , Bessemer and Thomas processes , in which the oxidation takes place through air. They were widespread in the mid-19th century through the 1960s. Before that, the puddling process was used. Technically widespread (72% of world production) is the Linz-Donawitz process (LD process). In this case, the liquid pig iron from the blast furnace is poured into a large, swiveling container. This container, the converter, holds around 300 tons of liquid pig iron. The reaction that leads to the conversion of pig iron into steel is exothermic . To ensure that the converter is not damaged by excessively high temperatures, it must be cooled. For this purpose, iron or steel scrap is added to the pig iron . The energy required to melt the iron or steel scrap removes part of the heat from the process. Nevertheless, the temperatures in the converter rise from approx. 1250 ° C to approx. 1600 ° C.
The process of crude steel production starts when a water-cooled oxygen lance is inserted into the melt. Pure oxygen is blown into the melt through this lance at a pressure of around 10 bar. It oxidizes the accompanying elements, the resulting gaseous oxides (carbon monoxide, carbon dioxide and sulfur dioxide) escape through the converter opening into the exhaust stack. Solid or liquid oxides are deposited on the surface of the melt where, together with previously added limestone, they form what is known as slag . After about half an hour, the content of foreign elements in the melt has dropped significantly. The slag and molten steel (now called crude steel ) are poured separately from the converter into transport buckets.
The second important steelmaking process is the electric steel process . With graphite electrodes, temperatures of up to 3500 ° C are generated in the arc furnace . Since these temperatures only arise locally at the tips of the graphite electrodes, oxygen can be blown in with lances to accelerate the homogenization of the temperature distribution. This significantly accelerates the melting process and around 100 tons of steel scrap can be melted in about an hour. For the smelting, the own scrap, which comes from the steel production, as well as foreign scrap, z. B. automotive scrap used. Alloying agents can be added to the steel melt during melting. The refined setting of the desired chemical analysis is carried out in the alloy furnace after the steel melt has been brought into the so-called alloy state.
In addition, the quality of the steel can be increased by subjecting it to deoxidation. Ferrosilicon and aluminum , which bind the oxygen in the melt, are added to the steel melt. This prevents oxygen inclusions and thus increases the strength of the steel. During the deoxidation process, i.e. the solidification (cooling) of the steel, the edge zone is temperature-controlled in the same way as the core of the steel block. This reduces the tension energy in the structure of the steel, thus the steel acquires a uniform structure. Depending on the degree of deoxidation, a distinction is made between killed steels and fully killed steels.
For smaller amounts or in foundries find induction furnaces frequently use.
Ecology and recycling

Iron, the main component of steel, is non-toxic to the environment, animals, humans and plants, even if it is corroded or thrown away. Steel production is a large consumer of energy. In 2013 the iron and steel sector accounted for around 18% of total global industrial final energy consumption. In the life cycle assessment of steel, two production routes have to be distinguished:
- Primary generation : When producing one kilogram of crude steel via the blast furnace route , the best blast furnaces in Europe emit around 1.475 kg of CO 2 equivalent , which is close to the theoretical limit of 1.371 kg of CO 2 . Accordingly, larger emissions reductions can only be achieved through completely new production methods. On the blast furnace route, too, around 20% recycling material ( scrap ) is used in what is known as the converter .
- Steel recycling : With the recycling route in the electric steelworks , the chemical energy from coal used to reduce iron ore can be saved compared to the blast furnace route . Recycling steel requires 60 to 75 percent less energy than primary production. This results in approx. 0.75 kg of CO 2 per kg of steel; the exact CO 2 balance depends on the electricity generation used. Problems with recycling pose individual foreign substances such as B. is copper that comes from electrical appliances.
In practice, steel is first made from ore and then often recycled several times (one-time primary production and several steel recycling). This results in an average CO 2 emission of around 1 kg CO 2 per kg of hot strip steel produced. For comparison: The production of 1 kg of raw aluminum releases 10 kg of CO 2 (using an average energy mix). An iron fraction can be recovered from shredded mixed scrap using magnetic separators . Alloying elements can, but need not, be removed during recycling. Accordingly, high-alloy steels are specially recorded and remunerated by metal buyers. In contrast, the recycling of thin-walled, coated, completely empty containers (can scrap) is sometimes referred to as downcycling.
With 500 million tons per year, steel is the most recycled industrial material in the world. The recycling rate of steel is 70%, that of individual steel applications z. T. at well over 90%.
For the protection of iron and steel against corrosion, substances are used that interfere with recycling, are lost or, as environmentally relevant substances, escape or have to be retained. These include in particular the alloying elements chrome and nickel as well as paints, tin ( tinplate ) and zinc as coatings . In Europe, the steel mill dust is therefore recycled in order to recover the zinc it contains.
Types of steels and steel products
In 2017, the register of European steels lists over 2,400 types of steel .
Steel is differentiated, for example
- according to function or use: tool steel , structural steel , electrical steel , armor steel , steel for lightweight construction , offshore steel , shipbuilding steel
- according to the end product: spring steel , chain steel , plastic mold steel , steel for pressure vessels , valve steel , roller bearing steel, shaped steel (for steel profiles )
- by forming process: steel for cold rolling , steel for deep drawing
- after the intended heat treatment : case- hardening steel , nitriding steel , heat- treatable steel
- by alloy: carbon steel , AHSS steel, unalloyed steel
- according to quality class: stainless steel , basic steel, quality steel
- according to special properties: heat-resistant steel, stainless steel , weatherproof steel, scaling-resistant steel, acid-resistant steel , weatherproof structural steel
- according to temperature resistance: cold work steel , hot work steel , high speed steel
- Special versions: Corten steel , dual-phase steel , duplex steel
Classification according to quality classes (EN 10020)
According to EN 10020: 2000, a distinction is made between three main quality classes:
- Unalloyed steels ( unalloyed quality steels , unalloyed stainless steels ). Carbon steels (in product often colloquially carbon steel ( AHSS ), carbon steel or carbon steel called) as an additive predominantly carbon, and only small amounts of chromium , copper , nickel , lead , manganese or silicon . They are divided into steel materials for subsequent heat treatment and those that are not intended for heat treatment.
- Stainless steels , d. H. Steels with a mass fraction of at least 10.5% chromium and no more than 1.2% carbon
- Other alloy steels and alloy stainless steels
The short names of the steels are specified in EN 10027 . Today around 2500 different types of steel are produced, of which around 2000 were only developed in the last ten years.
The steel materials are divided into groups according to the alloying elements , the structural components and the mechanical properties.
Classification according to areas of application
Other important properties for the user are the areas of application and possible uses of the steels. It is therefore useful to have a label showing this:
- Structural steel - Structural steels make up over half of global steel production. They are the standard type, which is mainly used for the construction of buildings and machines, unless there are special requirements in terms of strength, corrosion resistance or other properties. There are unalloyed (general / normal strength) structural steels and alloyed structural steels. Structural steels often have very low carbon contents.
- Case hardening steel - Intended for case hardening of the surface layers of the finished workpiece. This increases the carbon content, which was previously only 0.1 and 0.2%, in the edge area to up to 0.8%. The core of the workpiece remains tough and break-proof, as only the outer layer is hardened and thus becomes brittle. Case-hardening steels are particularly frequently used for small parts and wear-resistant components with dynamic stress.
- Quenched and tempered steel - The carbon content is between 0.1 and 0.6%. These steels are well suited for tempering , a special heat treatment for hardening or complete hardening of the steel. This production method is used for gears. but also for highly stressed components such as B. Hydropower turbines.
- Nitriding steel is intended for hardening by nitriding . The carbon content is around 0.3%. Application for parts subject to wear and tear.
- Tool steel - Used to make tools , dies, and molds , and is characterized by greater hardness.
- Stainless steel - These are available as ferritic, austenitic , martensitic and duplex steel . The former is produced by alloying at least 10.5 percent chromium . In austenitic stainless steels, nickel is also alloyed. Austenitic steels are not magnetic at room temperature.
- Acid-resistant steel - Acid and alkali-resistant from a chromium content of at least 17%; Use: e.g. B. Filling systems for cleaning agents.
Classification according to DIN EN 10079 - definition of steel products
DIN EN 10079 (definition of steel products) differentiates steel products into liquid steel, solid crude steel and semi-finished products , flat products , long products and other products.
Flat products have a rectangular cross-section, the width of which is significantly greater than its thickness. They are divided into
- hot-rolled wide flats, sheet and strip without surface treatment, produced by hot rolling of semi-finished products
- Cold-rolled sheets and strips without surface finishing, produced by cold rolling (the cross-section reduction is generally more than 25%), with special shapes
- Electrical steel sheets and strips with defined magnetic properties ( grain-oriented or non-grain-oriented)
- Packaging sheets and strips made of soft unalloyed steel (cold-rolled once or twice; as a sheet or roll; e.g. thin sheet , tinplate , special chrome-plated sheet with 0.17-0.49 mm and tin-plated sheet with over 0.5 mm thickness)
- Flat products with surface finishing, hot or cold rolled, e.g. B. with coating as
- metallic coatings by hot dipping ( hot-dip galvanizing or hot-dip aluminizing) or electrolytic metal deposition (with zinc or nickel)
- organic coatings ( paints , powder coatings, etc.)
- inorganic coatings ( enamel )
- composite products (clad sheets and strips, sandwich sheets and elements).
According to the material thickness, flat products are divided into thin sheet and strip up to 3 mm thick and heavy plate and strip from 3 mm thick.
properties
General physical properties
The density of steel is 7.85-7.87 g / cm³ (7850-7870 kg / m³).
The melting point of pure iron is 1536 ° C, the addition of alloying elements usually reduces the melting point of steel and with 2% carbon is only 1400 ° C. As can be seen from the iron-carbon diagram, steel, like most alloys, does not have an exact melting point: At temperatures above the liquidus line (top line in the diagram) the material is completely liquid, while it is partially between the liquidus and solidus line (second line from the top ) liquid and solid. Only solid material is present only when the solidus line is undershot.
The electrical conductivity of steel is slightly lower than that of pure iron with 10 · 10 6 A / (V · m). Thus steel C15 (with 0.15% carbon) 9.3 x 10 6 A / (V · m), steel C35 8.6 x 10 6 A / (V · m) and steel C60 7.9 x 10 6 A / (V · m). The conductivity drops noticeably with an increasing proportion of carbon, but remains clearly above that of stainless steel with 1 · 10 6 A / (V · m).
Mechanical properties

Steel is considered to be a very strong, but also "soft" material, while the cast iron used is considered hard and brittle. Strength is the force related to the cross-section that the material can withstand before it fails (tearing, breaking, etc.). Components made of steel can therefore transmit high forces. Steel is considered to be “soft”, ie malleable: before steel breaks, it deforms, although this deformation can be very large in steel. Cast iron, on the other hand, breaks without being deformed beforehand. Steel therefore has large safety reserves against breakage, which is why it is used in important vehicle parts (steering, chassis, drive).
The strength of the most frequently used steels, unalloyed structural steels , is between 180 and 350 N / mm². It increases with the increasing content of carbon and other alloy elements. The deformation behavior of materials is recorded in stress-strain diagrams . The force on a material sample is slowly increased and the change in length is measured. In the diagram, the mechanical stress (force divided by cross-sectional area) and the strain (change in length relative to the initial length) are plotted. Structural steels have a pronounced yield point: the stress initially increases proportionally to the elongation and then suddenly drops slightly. The maximum of the straight line in the diagram is the yield point up to which steels should be used when in use. For processing by rolling and forging, it must be exceeded.
High-strength steels can achieve strengths of over 1000 N / mm². Some special grades, such as those for piano strings , even reach over 1800 N / mm². Steel is therefore much stronger than wood, concrete and stone. The strength related to the density, the specific strength , is very high in steel compared to these materials. Structures made of steel are therefore lighter for a given load-bearing capacity. Steel is only surpassed by a few light metals such as aluminum , magnesium or titanium . Of all known materials, steels are among those with the highest strength. In addition to aluminum, magnesium and titanium alloys, CFRPs , plastics reinforced with carbon fibers, achieve similar but lower values .
The elongation at break, i.e. the elongation at break (end of the curve in the stress-elongation diagram), can be 50% for deep-drawing steel with low strength, whereas higher-strength steels ( AHSS ) generally have lower elongations at break; Structural steels therefore stretch very far before they break. In contrast, cast iron and ceramics break if their strength is exceeded without prior plastic deformation.
The modulus of elasticity of common ferritic steels is 210 GPa (2.1 · 10 5 N / mm²). In the stress-strain diagram, it can be seen as the slope of the straight line. The modulus of elasticity is thus slightly higher than that of cast iron (170 GPa) and significantly higher than that of aluminum alloys (70 GPa). Only a few materials outperform steel, including hard metals (approx. 500 GPa) and diamond (900 GPa).
The hardness of steel can vary widely and can reach Vickers hardnesses between 80 and 940 HV. Soft-annealed quenched and tempered steels achieve hardnesses of 150 to 320 HV (150 to 300 Brinell , 1 to 33 Rockwell), quenched and tempered (hardened) quenched and tempered steels are around 210 to 650 HV. In the hardened state, tool steel reaches up to 840 HV. In comparison, copper and aluminum materials are between 40 and 190 HV, while hard metals reach 780 to 1760 HV. Typical ceramics are even harder.
Technological properties
Technological properties relate to machining and processing. In detail, it concerns the castability, forgeability, machinability and weldability. With the exception of the pourability, they are good to very good for the varieties that are frequently used.
Castability
Castability is the suitability of a material to be processed by casting . This refers above all here casting , in which the forms already included the shape of the final products later, not casting into ingots.
Steel is comparatively difficult to cast, which is why it has a low mass fraction of all materials used in the foundry and is clearly surpassed by both cast iron and aluminum , since both are much easier to cast. In 2011, around 220,000 tons of steel were used in foundries in Germany, while it was around 4.2 million tons for cast iron and 840,000 tons for aluminum.
Special types of steel for foundries are called cast steel . It tends to develop hot cracks , which can only be controlled with experience in casting. In addition, the melting point is very high at 1580 ° C to 1680 ° C (cast iron 1100 ° C, aluminum casting alloys around 600 ° C), which leads to a high energy requirement during melting and high thermal loads on the molds and systems. Steel tends to burn the surface of the mold when it is cast and large feeders are necessary to compensate for the loss of volume during cooling in the mold. After solidification, the feeders are difficult to separate again. Cast workpieces made of steel are about three times more expensive than those made of cast iron because of the high manufacturing costs, although less material is required because of the higher strength.
Forgeability and formability
Formability is the suitability of a material to be processed by the processes of forming technology . By far the most important process of the group is forging , which is why it is also referred to as forgeability. The group also includes bending , rolling , deep drawing , extrusion and many more.
The formability is better, the lower the forces required and the more the material can be deformed without breaking or tearing. The force required for deformation is usually related to the cross-sectional area and specified as the flow stress . The maximum elongation that a material can endure is the elongation at break .
With simple structural steels, the yield stress is comparatively low and the elongation at break is very high. In the case of high-strength steels, the yield stress is naturally higher, but significantly stronger materials are also forged, including titanium, nickel and cobalt alloys. The elongation at break is usually smaller the stronger a steel is. TRIP steels with low to medium yield stress and high elongation at break are an exception . For most types of steel, the yield stress is classified as low. In addition to structural steels, these include hot-work and free-cutting steels. Aluminum and magnesium alloys are in a similar range. The elongation at break, however, can fluctuate more: It is very low for free-cutting steels, and almost as good for hot-work steels as for structural steels.
With cold forming , the flow stress and thus also the necessary force increases the higher the degree of deformation (the deformation). The effect is called work hardening and can be used to forge particularly strong workpieces. The exact relationship between yield stress and degree of deformation is recorded in flow curves . At higher temperatures, both the yield stress and the work hardening decrease in almost all steels. With hot forming , the yield stress no longer increases even at low degrees of deformation. In the case of steels, this occurs at temperatures of around 1100 ° C.
Machinability
Machinability is the suitability of a material to be machined by machining ( milling , drilling , grinding ). It depends on the carbon content, the other alloy elements and the state of heat treatment. Steels with a very low carbon content have a tendency to stick to the cutting edge and form long strip chips that can get caught in the machine. However, they lead to low cutting forces, but also to poor surfaces. With medium carbon contents (0.2% to 0.6%) there are no problems with sticking. The cutting forces increase, the surfaces become better and the chips shorter. In return, the wear on the tools increases. Steels with a high carbon content lead to high forces and temperatures as well as high wear. However, the surface quality and chip breaking are good. Elements such as phosphorus, lead and sulfur improve machinability, while strength-enhancing elements such as nickel reduce it. In the soft (normalized) condition, most steels can be machined relatively easily, in the quenched and tempered or hardened condition, on the other hand, the wear is very high, which requires expensive tools made of cutting ceramics or boron nitride.
Weldability
The weldability indicates how well a material can be welded . In particular, the unalloyed and low-alloy structural steels can be welded very well, which is an important reason for their widespread use, since joining by welding is significantly more cost-effective than by other joining techniques such as screws or rivets. Higher alloy steels can be problematic when welding. As a rough estimate of whether a steel can be welded, the carbon equivalent can be used, which takes into account the different influence of the various alloying elements. Aluminum is usually much more difficult to weld than steel.
Structural structure
In steel, as in many other materials, the microstructure determines to a large extent the mechanical properties, especially hardness and strength. In addition to iron and carbon, most steels also consist of numerous other elements that are contained at least as impurities - the steel companions - or are intentionally added as alloy elements . The microstructure is therefore relatively complicated, but is essentially based on the structure of the pure iron-carbon alloys (especially in the case of unalloyed and low-alloy steel). Their structure is based on that of pure iron.
As with all metals, iron atoms are in a regular arrangement in the solid state. Below 911 ° C, the iron atoms are in the corners of an imaginary cube with another iron atom in the middle. This structure repeats itself theoretically as often as desired in all directions and is generally referred to as body-centered cubic , in the case of iron also as -iron. Above 911 ° C, iron is in the so-called face-centered cubic form, in which atoms are again located in the corners of an imaginary cube, but this time an additional one in the center of each cube surface, but none in the center of the cube. This variant is known as -iron. The main difference for steel is the different density: In the face-centered cubic form, the gaps between the iron atoms are larger; they can therefore be more easily occupied by atoms of the alloying elements.
In pure iron-carbon alloys, there is always carbon in the gaps between the iron atoms. -Iron with carbon atoms is generally used as - mixed crystal referred to, often than steel ferrite (from Latin ferrum , while the quantity of iron) -iron with carbon than is called solid solution with steel and austenite is named after William Austen . Depending on the temperature, austenite can contain a great deal of carbon, a maximum of 2.06 percent by mass , while ferrite can only contain a maximum of 0.03% carbon. The temperature at which austenite transforms into ferrite depends on the carbon content and can be taken from the iron-carbon diagram . In both cases there is solid solution strengthening, i.e. an increase in strength. In addition to the iron mixed crystal, carbon can also be present in two other forms, especially if more carbon is present than can be absorbed in the mixed crystal: graphite and cementite . Areas that consist only of carbon are referred to as graphite, while cementite is a chemical compound of iron and carbon with the formula Fe 3 C. Graphite is mainly formed when it cools slowly after casting or annealing, while the hard and brittle cementite is formed when it cools down quickly. They do not lead to an increase in strength.
Other alloy elements can be present in steel in various forms:
- As mixed crystal: elements whose atoms are much smaller than those of iron (such as carbon, hydrogen or nitrogen) occupy the gaps between the iron atoms ( intercalated mixed crystal ). Larger atoms are located in the iron lattice ( exchange mixed crystal ) instead of an iron atom . These also increase the strength.
- They can form other chemical compounds, often together with carbon, the carbides , e.g. B. tungsten carbide or vanadium carbide , sometimes with each other. Simultaneous alloying of sulfur and manganese leads to the formation of manganese sulfide . Some elements also prefer to combine with iron. The effect of these compounds is very different in each individual case: Some are important for heat treatment, others increase hardness and wear resistance, others reduce strength and make the steel brittle.
- They can form small particles that only consist of the respective element. This only applies to a few elements, including lead, graphite and copper. They usually reduce the strength.
Heat treatment and modification of steel properties
The mechanical properties of steel (hardness, strength) can be changed in different ways:
- Cold forming : Forging, rolling, drawing and related processes increase the strength of all metals and alloys if the temperature is below a certain limit. The solidification can be desired and used in a targeted manner in order to produce particularly strong workpieces, but it can also be undesirable if excessive internal stresses arise during machining. Subsequent annealing can reduce the internal stresses and thus set the desired properties.
- Alloying : Alloying various elements generally increases the strength. Some elements such as phosphorus and sulfur embrittle the material. Lead has little effect at room temperature, but it lowers the strength at high temperatures. Chromium and nickel improve the corrosion resistance with certain minimum contents .
- Heat treatment : This allows hardness and strength to be changed in a variety of ways. Before machining, steel can be annealed to reduce the machining forces, then hardening is possible to increase wear resistance before use. The material can be hardened over the entire cross-section, whereby it also becomes more brittle, or only in the edge layers, while the inner areas remain tough and strong.
The heat treatment processes are divided into several groups:
- (purely) thermal processes: e.g. B. Annealing
- Thermochemical processes: The chemical composition of the steel is changed, typically only in the areas close to the surface
- Thermomechanical processes: They combine mechanical (rolling, forging) with thermal processing.
Thermal processes
Thermal processes change the microstructure through purely thermal influences, without additionally changing the chemical composition and without simultaneous mechanical processing.
-
Annealing : Annealing includes a number of processes in which the workpieces are first heated, kept at the annealing temperature for a certain period of time and then finally cooled. Process parameters are primarily the annealing temperature and duration, as well as the cooling rate. The exact results depend on the alloy composition and its exact condition. Previous heat treatments can have a greater impact on the result.
- Stress relief annealing, reduces or eliminates residual stresses caused by forming and is carried out at relatively low temperatures of 550 ° C to 660 ° C for 2 to four hours. Other property changes are avoided.
- Soft annealing , reduces the hardness, mainly to facilitate the subsequent machining . Lamellar cementite turns into a spherical shape.
- Normalizing (Normalization) produces a uniform, fine-grained microstructure. Changes in the structure due to previous processing are thus eliminated.
- Coarse grain annealing increases the grain size in the structure, which is associated with a decrease in strength. It is used before machining.
- Diffusion annealing reduces uneven distribution of the alloy components. By diffusion migrate atoms from areas of high concentration to areas of low concentration. This usually results in coarse grains that can be removed by hot forming (forging) or normalizing.
- Recrystallization annealing serves to remove strain hardening and thereby improves the formability of heavily deformed materials.
- Hardening is a process sequence consisting of austenitizing (around 800 ° C), quenching (rapid cooling) and tempering (heating to 180 to 300 ° C). Quenching makes the steel very hard, but also brittle. Subsequent tempering reduces the brittleness. Carbon content from 0.2%.
- Quenching and tempering is related to hardening. Tempering takes place at 450 to 650 ° C, carbon content between 0.3% and 0.8%.
- Bainitizing : Creation of bainite in the structure.
- Surface hardening : The surface layers are heated up quickly while the inner layers remain cold due to the limited thermal conductivity. Variants are flame hardening , induction hardening , laser beam hardening and electron beam hardening .
Thermochemical processes
They also change the steel chemically. The following procedures are used:
- Carburization increases the carbon content, especially in the surface layers, which increases hardness and strength.
- Carbonitriding increases the carbon and nitrogen content in the surface layer.
- Nitriding forms nitrides (nitrogen compounds) in the surface layer.
- Case hardening consists of carburizing, hardening and tempering. The corresponding steels are called case- hardening steel .
- Boriding is a hardening process based on the introduction of boron .
Thermomechanical processes
Thermomechanical processes are based on mechanical processing (forging, rolling) combined with heat treatment. The austenite form hardening , which serves to increase strength, is important.
literature
- Association of German Ironworkers (Ed.): Material Science Steel, Volume 1: Basics. Springer-Verlag , Berlin / Heidelberg / New York / Tokyo 1984, ISBN 3-540-12619-8 , and Verlag Stahleisen, Düsseldorf 1984.
- Association of German Ironworkers (Ed.): Material Science Steel, Volume 2: Applications. Springer-Verlag, Berlin / Heidelberg / New York / Tokyo 1985, ISBN 3-540-13084-5 , and Verlag Stahleisen, Düsseldorf 1985.
- Claus and Micah Wegst: Steel Keys - Key to Steel 2010 reference work. Verlag Stahlkey, 2010, ISBN 978-3-922599-26-5 .
- Industry association for massive forming: New steels for massive forming. Infor-series Massivumformung, Hagen 2012, ISBN 978-3-928726-28-3 .
- Theisen Berns: iron materials. 4th edition. Springer, 2013.
Web links
- Steel information center
- Steel side: Photographs of almost all processes in steel production and steel processing
- Transport Information Service: Specialized information on the transport of steel
- Hüttenwerke Krupp Mannesmann Flash animation "Paths of steel production"
- Best Available Techniques - (BAT). Download the BREFs and implementing decisions. ( Memento from July 17, 2013 in the Internet Archive ) At: Umweltbundesamt.de.
- Patrick Chudalla, Thomas Stahl: From iron ore to steel. On www.fh-muenster.de [1]
Individual evidence
- ↑ nssmc.com, Nippon Steel Technical Report No. 80, July 1999 (PDF, 333 kB)
- ↑ Kluge. Etymological dictionary of the German language . Edited by Elmar Seebold . 25th, revised and expanded edition. Walter de Gruyter, Berlin / Boston 2011, ISBN 978-3-11-022364-4 , p. 875.
-
↑ VDEh : Material Science Steel - Volume 1: Fundamentals , 1984, p. 21. “... which are generally suitable for hot forming.”
Dubbel , 24th edition, p. E34, “... represent iron materials that are i. General suitable for hot forming,… “
Böge: Handbuch Maschinenbau. 21st edition. P. E14, "Steel is malleable iron ..."
H. Czichos, B. Skrotzki, F.-G. Simon: Hut - The engineering knowledge: materials. 2014, p. 24, “Iron-carbon alloys with a carbon content in general. less than 2% by weight that are cold or hot formable (forgeable) ... “
B. Ilschner, RF Singer Material science and manufacturing technology: properties, processes, technologies. 5th edition. 2010, p. 431, "... referred to iron alloys that contain less than 2% carbon and that are suitable for hot forming."
Hans-Jürgen Bargel, Günter Schulz (Ed.): Material Science. 11th edition. 2012, p. 181, "Iron-carbon alloys that can be forged without further treatment are steels (C ≤ 2%)."
Erhard Hornbogen, Hans Warlimont Metals: Structure and properties of metals and alloys. 6th edition. 2016, p. 291, "Steels are practically all deformable technical alloys of iron." - ↑ Wolfgang König (ed.): Propylaea history of technology. Volume I, Propylaeen, Berlin 1997, pp. 419-421.
- ↑ Friedrich Cornelius : Spiritual History of the Early Period. Volume 1, Brill Archive Publishing House, 1960, p. 132.
-
↑ Wolfgang König (ed.): Propylaea history of technology. Volume 3, Propylaea, Berlin 1997, p. 98 f.
Günter Spur: About the change in the industrial world through machine tools. Carl Hanser Verlag, Munich / Vienna 1991, pp. 49–51. - ↑ Wolfgang König (ed.): Propylaea history of technology. Volume 3, Propylaea, Berlin 1997, p. 99 f.
- ↑ Günter Spur: On the change in the industrial world through machine tools. Carl Hanser Verlag, Munich / Vienna 1991, p. 57 f.
- ↑ Alex R. Furger: Ancient steel production. Evidence of the carburization of iron from Augusta Raurica. LIBRUM Publishers & Editors, Basel / Frankfurt am Main 2019, ISBN 978-3-906897-28-8
-
↑ Günter Spur: On the change in the industrial world through machine tools. Carl Hanser Verlag, Munich / Vienna 1991, pp. 67, 70 f., 77.
Wolfgang König (Ed.): Propylaea History of Technology. Propylaea, Berlin 1997:- Volume 1, pp. 346-408, 419-435.
- Volume 2, pp. 76-107.
-
↑ Günter Spur: On the change in the industrial world through machine tools. Carl Hanser Verlag, Munich / Vienna 1991, pp. 68, 79–81.
Wolfgang König (Hrsg.): Propylaea history of technology. Propylaea, Berlin 1997, Volume I, pp. 423-425 (Damast), Volume II 390 (cast iron). -
↑ Günter Spur: On the change in the industrial world through machine tools. Carl Hanser Verlag, Munich / Vienna 1991, pp. 69 f., 79-81.
Wolfgang König (Hrsg.): Propylaea history of technology. Volume 2, Propylaen, Berlin 1997, pp. 377, 391. - ↑ Günter Spur: On the change in the industrial world through machine tools. Carl Hanser Verlag, Munich / Vienna 1991, pp. 69, 85-88.
-
↑ Example Solingen: Günter Spur: On the change in the industrial world through machine tools. Carl Hanser Verlag, Munich / Vienna 1991, p. 76.
General regional distribution: Wolfgang König (Hrsg.): Propylaen Technikgeschichte. Volume 1, Propylaen, Berlin 1997, p. 426. - ↑ Wolfgang König (ed.): Propylaea history of technology. Volume 3, Propylaeen, Berlin 1997, p. 383.
- ↑ Wolfgang König (ed.): Propylaea history of technology. Volume 3, Propylaea, Berlin 1997, p. 330.
- ↑ Ulrich Wengenroth: Iron, steel and non-ferrous metals. In: Ulrich Wengenroth (ed.): Technology and economy. (= Technology and culture. Volume 8). VDI-Verlag, Düsseldorf 1993, p. 103.
- ↑ Wolfgang König (ed.): Propylaea history of technology. Volume 3, Propylaea, Berlin 1997, pp. 383 f., 397.
- ↑ Gottfried Pump: Chemical Industry. In: Ulrich Wengenroth (ed.): Technology and economy. (= Technology and culture. Volume 8). VDI-Verlag, Düsseldorf 1993, pp. 161-163.
-
↑ Günter Spur: On the change in the industrial world through machine tools. Carl Hanser Verlag, Munich / Vienna 1991, pp. 127–129.
Wolfgang König (Hrsg.): Propylaea history of technology. Volume 3, Propylaen, Berlin 1997, pp. 390-393, 395. -
↑ Günter Spur: On the change in the industrial world through machine tools. Carl Hanser Verlag, Munich / Vienna 1991, p. 129.
Wolfgang König (Ed.): Propylaea history of technology. Volume 3, Propylaen, Berlin 1997, p. 397. -
↑ Günter Spur: On the change in the industrial world through machine tools. Carl Hanser Verlag, Munich / Vienna 1991, p. 130.
Wolfgang König (Ed.): Propylaea history of technology. Volume 3, Propylaea, Berlin 1997, pp. 399 f., 406 f.
Ulrich Wengenroth: Iron, steel and non-ferrous metals. In: Ulrich Wengenroth (ed.): Technology and economy. (= Technology and culture. Volume 8). VDI-Verlag, Düsseldorf 1993, pp. 101-103. -
↑ Wolfgang König (ed.): Propylaea history of technology. Volume 3, Propylaea, Berlin 1997, p. 402 f.
Ulrich Wengenroth: Iron, steel and non-ferrous metals. In: Ulrich Wengenroth (ed.): Technology and economy. (= Technology and culture. Volume 8). VDI-Verlag, Düsseldorf 1993, pp. 100-103. - ↑ Ulrich Wengenroth: Iron, steel and non-ferrous metals. In: Ulrich Wengenroth (ed.): Technology and economy. (= Technology and culture. Volume 8). VDI-Verlag, Düsseldorf 1993, pp. 103-109.
- ↑ Lothar Gall (Ed.): Enzyklopädie Deutscher Geschichte. Volume 79, Christian Kleinschmidt: Technology and Economy in the 19th and 20th Centuries, p. 17f.
- ↑ Wolfgang König (ed.): Propylaea history of technology. Volume IV, Propylaen, Berlin 1997, pp. 71-78, 286f.
- ↑ Martina Heßler: Cultural history of technology. Campus Verlag, Frankfurt / New York, p. 47 f.
- ↑ Wolfgang König (ed.): Propylaea history of technology. Volume 4, Propylaen, Berlin 1997, pp. 288 f., 427-431.
- ↑ Ulrich Wengenroth: Iron, steel and non-ferrous metals. In: Ulrich Wengenroth (ed.): Technology and economy. (= Technology and culture. Volume 8). VDI-Verlag, Düsseldorf 1993, p. 111 f.
- ^ Lothar Gall (Ed.): Encyclopedia of German History - Volume 79. Christian Kleinschmidt: Technology and economy in the 19th and 20th centuries. Oldenbourg, 2007, pp. 18, 23.
- ↑ Ulrich Wengenroth: Iron, steel and non-ferrous metals. In: Ulrich Wengenroth (ed.): Technology and economy. (= Technology and culture. Volume 8). VDI-Verlag, Düsseldorf 1993, pp. 115-119.
- ^ Ulrich Wengenroth: Electric energy. In: Ulrich Wengenroth (ed.): Technology and economy. (= Technology and culture. Volume 8). VDI-Verlag, Düsseldorf 1993, p. 342.
- ↑ Ulrich Wengenroth: Iron, steel and non-ferrous metals. In: Ulrich Wengenroth (ed.): Technology and economy. (= Technology and culture. Volume 8). VDI-Verlag, Düsseldorf 1993, p. 118.
- ↑ Wolfgang König (ed.): Propylaea history of technology. Volume 5, Propylaea, Berlin, 1997, p. 46.
- ↑ stahl-online.de
- ↑ stahl-online.de
- ↑ Stahlinstitut VDEh (ed.): Stahlfibel , Verlag Stahleisen, 2007, p. 162.
- ↑ a b c stahl-online.de accessed on June 13, 2017.
- ↑ world-aluminium.org
- ↑ Steel and sustainability. (PDF) Accessed December 21, 2015 .
- ↑ Material Science Steel - Volume 1, p. 4 f.
- ↑ Stahlfibel, p. 2.
- ^ Eckhard Ignatowitz: Chemistry for school and work. A text and study book. 4th edition. Verlag Europa-Lehrmittel Nourney, Haan-Gruiten 1999, ISBN 3-8085-7054-7 , p. 142.
- ↑ Steel production: oxygen converter in front of an electric furnace. At: stahl-online.de.
- ^ Kun He, Li Wang: A review of energy use and energy-efficient technologies for the iron and steel industry . In: Renewable and Sustainable Energy Reviews . 2016, doi : 10.1016 / j.rser.2016.12.007 .
- ↑ Manfred Fischedick u. a .: Techno-economic evaluation of innovative steel production technologies. In: Journal of Cleaner Production . 84, 2014, pp. 563-580, p. 564, doi: 10.1016 / j.jclepro.2014.05.063 .
- ↑ Steel scrap balance 2014: The steel recycling industry had to cope with a decline in total shipments of 1.7 percent. ( Memento of April 2, 2015 in the Internet Archive ; PDF) bdsv.org, press release, March 23, 2015.
- ↑ https://www.sueddeutsche.de/wirtschaft/kreislaufwirtschaft-fuer-die-tonne-1.5004792
- ↑ Multireycling of steel. (PDF) At: stahl-online.de. (PDF; 1.03 MB).
- ↑ Life cycle assessment according to ISO 14040/44 for multi-recycling of steel. (PDF) At: stahl-online.de. (PDF; 1.3 MB).
- ↑ Is aluminum / tinplate recycling worthwhile? (PDF) At: kopytziok.de. (PDF; 92 kB).
- ^ Steels: Facts, Figures, Environment and Green Steels. At: dierk-raabe.com.
- ^ Recycling Rates of Metal. (PDF) At: unep.org. (PDF; 2.4 MB).
- ↑ Status report on steel recycling in construction. (PDF) University of Wuppertal (PDF).
- ↑ Tinplate recycling rate: 93.7%. On: stahl-online.de.
- ↑ Entry Stahl , BiBuch - Bilingual information portal for industry and technology; accessed in March 2019.
- ^ B. Ilschner, RF Singer: Materials science and manufacturing technology. 5th edition. Springer, 2010, pp. 438 f., 441-445.
- ^ Hans-Jürgen Bargel, Günter Schulz (Ed.): Material science. 11th edition. Springer, 2012, pp. 239–284.
- ↑ a b C-steel product data sheet ( Memento from December 17, 2010 in the Internet Archive ), ThyssenKrupp Steel Europe, accessed in July 2013.
- ↑ Dr.-Ing. Hans-Joachim Wieland: Information about product forms (PDF) p. 1, Stahl-Zentrum; In: stahl-online.de. Accessed October 2019
- ↑ Metallic materials - physical properties
- ↑ nssmc.com (PDF)
- ↑ H. Czichos, B. Skrotzki, F.-G. Simon: The engineering knowledge - materials. Springer, 2014, p. 66.
- ↑ google.com.pg
- ^ B. Ilschner, RF Singer: Material technology and production technology. Springer, 2010, p. 433 f.
- ↑ H. Czichos, B. Skrotzki, F.-G. Simon: The engineering knowledge - materials. Springer, 2014, p. 59.
- ^ Hans-Jürgen Bargel, Günter Schulz (Ed.): Material science. 11th edition. Springer, 2012, ISBN 978-3-642-17716-3 , pp. 241, 248.
- ↑ H. Czichos, B. Skrotzki, F.-G. Simon: The engineering knowledge - materials. Springer, 2014, p. 62.
- ↑ H. Czichos, B. Skrotzki, F.-G. Simon: The engineering knowledge - materials. Springer, 2014, p. 71.
- ↑ Günter Spur (Ed.): Handbuch Urformen. Hanser, 2014, p. 16.
- ^ Alfred Herbert Fritz, Günter Schulze (Ed.): Manufacturing technology. 11th edition. Springer, 2015, pp. 24, 34.
- ↑ Eckart Doege, Bernd-Arno Behrens: Handbook of forming technology. 2nd Edition. Springer, 2010, pp. 438-440.
- ↑ Hartmut Hoffmann, Reimund Neugebauer, Günter Spur (ed.): Handbook of forming. Hanser, 2012, p. 253.
- ↑ Material Science Steel - Volume 1: Fundamentals. 1984, pp. 564-615, especially 564 f., 567, 576.
- ^ B. Ilschner, RF Singer: Materials science and manufacturing technology. 5th edition. Springer, 2010, p. 387.
- ^ Hans Berns, Werner Theisen: Eisenwerkstoffe. 4th edition. Springer, 2013, pp. 3–15.
- ^ Alfred Böge (Ed.): Manual of mechanical engineering. 21st edition. Springer, 2013, pp. E35 – E40.
- ^ Alfred Böge (Ed.): Manual of mechanical engineering. 21st edition. Springer, 2013, pp. E40f.
- ^ Alfred Böge (Ed.): Manual of mechanical engineering. 21st edition. Springer, 2013, pp. E41f.