Molding
Mold casting is a casting process . Casting refers to the totality of technical possibilities to bring molten metals - either pure or as an alloy - into a shape determined by their future use. This includes modern techniques such as gradient casting and hybrid casting, which is related to manufacturing technology, but not the casting of blanks, which may indicate the later intended use, but must be further processed intensively (examples: drop forging , deep drawing ). The casting of plastics is usually carried out as injection molding of thermoplastics or with casting resin as the material.
history
The manufacture of metallic jewelry and utensils by pouring molten metal into a mold was already known in the early Bronze Age . Finds that already suggest small series show this and at the same time provide information about knowledge of mold production from different materials. The simplest form was used for the one-off casting of busts and statues and was separated from the cast part by smashing it after it had cooled down, a technique that has survived as a "lost form" in bell casting to this day. Another development was "stove casting" (the best-known example are the richly decorated iron stove plates from the 15th and 16th centuries), in which pouring was carried out in an open-topped mold that was created by simply pressing a casting template into the mold bed. The underside of the cast then showed the desired contouring . This molding technique, too, was only suitable for a cast, which, however, could be repeated after the mold bed was refreshed. A big step was the invention of the lost wax process known to this day. For this purpose, a model made of wax was used, a material that made it possible to work out any desired fineness of the model template. The wax model was then completely embedded in an adaptable yet stable clay mass, the wax was melted by heating and the liquefied metal or alloy was poured into the cavity that was created in its place. After cooling, the clay mold was knocked off. This technology was not very suitable for series production. As early as the 12th century BC Therefore, two-part bronze casting molds can be found, by means of which axes could be cast in series.
Casting only attained technical importance towards the end of the 18th century, when the cast iron era marked the beginning of the industrial age. Individual parts made of cast iron were mass-produced in sand molds and connected to structures. Some have been preserved as industrial monuments to this day.
Today, cast iron has to meet more diverse requirements. New developments even make it possible to compensate for the previous weight disadvantage compared to cast aluminum and to meet the requirements of modern engine technology with extremely thin walls ( ADI, austempered ductile iron ).
The current development in molding at the beginning of the 21st century is bionics , which is based on the human bone structure and its structures in terms of shape and stability. The aim is to combine good strength values with lightweight construction and weight savings.
In vehicle construction in particular, weight savings and the associated energy savings have become a determining factor in manufacturing processes. The choice of materials, design and manufacturing processes are subject to the overarching concept of "lightweight construction".
Model making as a historical prerequisite for mold production
In simple terms, every casting mold (also synonymous with casting mold) is a cavity that is filled with molten metal and reproduces it when it solidifies, taking into account the details given by its shape. This is done with the help of a model that corresponds as closely as possible to the later cast piece, taking into account the linear shrinkage during cooling from the casting to room temperature. A distinction must be made between lost and reusable models made of plaster of paris, wood, synthetic resin or metal.
The model is a technical specialty. In the past, the models were mostly made from wood (hence the old job title “model carpenter or cabinet maker”). Digitization, which has been expanding in its possibilities since the end of the 20th century, has had a strong influence on the profession, because the 3D process enables models to be produced quickly and easily changed. This is done by means of a computer that uses a CAD / CAM process to create a three-dimensional model from a drawing made either from thermally resistant plastic or metal powders. Even operational prototypes can be produced (rapid prototyping process). Larger sand molds can be built from a synthetic resin-free raw material, for example sand, to the inorganic binder, which enables thermal hardening, by means of the 3D process, dispensing with a model. The commissioning of the largest 3D printing system for molds is reported from the USA. Conversely, it is also possible to mill out a model from a solid. Since models can be easily produced and also changed using 3D technology from almost any material, they enable model changes to be made through evaluation of the results of the respective casting simulation up to their casting optimization and approval for series production.
For the production of thin-walled cast parts or those with different wall thicknesses, the three-dimensional simulation of the casting process is increasingly becoming the standard in model construction, not only for the flow behavior during mold filling, but also for its course and the processes during the solidification of the cast part in the mold . In this way, possible weak points, especially when filling the casting mold, such as solidification contraction and avoidance of voids , can be identified and quickly remedied by targeted changes to the model.
The material used in model making determines the number of shapes to be made with it. Injection molded metal models that are true to the casting can be used as prototypes to replace a casting. Small series for test purposes have been common up to now, with regular printed parts taking the place of cast parts in some cases.
Intricate castings, such as the engine block or the cylinder head of an automobile engine , require the necessary models to take into account the necessary internal cores made of metal, sand, salt or other mineral substances, which are removed after the casting, and then the technically required cavities in the casting reproduce. There are both single cores and “core packages” made up of interconnected single cores.
Molding material and mold making
A differentiating feature in molding relates to the molding material used , the material from which the mold is formed, regardless of the model technology.
Sand casting

Regardless of innovations, casting in sand molds that can be used once is still "state of the art" in the 21st century. However, innovations have been added, such as the lining of casting ladles, which is intended for one-time use and which limits the temperature drop in the casting metal when several molds are poured one after the other.
The molding sand can be clay-bound or chemically bound. Natural sand, which is mined in molding sand pits, is always clayey, a prerequisite for binding and malleability. Since natural sand can be exposed to fluctuations in its composition, pure quartz sand is preferred for high-quality sand casting , which is prepared with precisely dosed, swellable and binding additives based on the mineral bentonite in order to meet the main requirements of optimal compressive and shear strength (important for the stability of edges) to suffice.
The alternative to clay-bound sand is chemically bound sand. Grains of pure quartz sand are covered with a thin layer of synthetic resin , which is either self-hardening as a result of polymerisation or is subject to a thermal process when heated, which has a binding effect and ensures the strength of the mold.
Bentonite and cold or hot-setting synthetic resins are known as molding additives. The addition is between 0.3 and 3 to 5 percent, depending on the substance. In iron and heavy metal castings, hard coal dust is predominantly added as a lustrous carbon generator to achieve perfect cast surfaces, but other carbon carriers are also used. When casting magnesium or magnesium-rich aluminum alloys, boric acid is added to limit the reaction of the molding material.
Bentonite and synthetic resins are used in several techniques - including the use of silicate binders ( water glass ) - to produce the sand cores necessary to complete the shape. Since very few castings can be cast without cores, with cores merely being recesses in the later cast, core binders are a special field for research and further development. For the production of cores and core packages - which used to be time-consuming manual labor - outsourcing to specially appointed suppliers is not unusual. Particular emphasis is placed on the stability of the cores in relation to the melt flowing around them when the mold is filled, as well as on residue-free, easy removability of the used cores.
To remove the cores or their residues, sometimes simple methods are used, such as "shaking", but the core material mixtures must also be adapted to the requirement of easier removal after casting. Water-soluble salt cores have proven themselves in many cases. New is a system that uses shock wave technology to remove the core from complex cast parts, whereby the cast parts are subjected to a high-frequency shock wave lying in a water bath.
Sand molds are mostly made in two-part or multi-part molding boxes , or - with more advanced technology - "boxless". For large parts there is also the bottom molding process and the molding pit. In the case of the box molding process, the model is embedded in the so-called lower box, the lower half of the molding box, in less coarse model sand that defines the contours of the casting, after which the molding material is compacted while simultaneously being filled with “filler sand”. With the second half, processes, gates and sprues are formed, finally the model is “excavated” and the two halves are put together. Today, the mass production of sand molds is done by molding machines, the technology of which ranges from manual control to fully automatic machines.
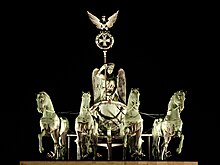
The production of the molds and cores by hand is only used in exceptional cases today because of the labor time involved. This applies particularly to single pieces and small series, as well as using specially fine molding sand mixtures for artisanal cast . The monument casting is also to be assigned to the artificial casting. The created objects can be people, figures or symbols in a design ranging from miniaturized to oversized. If objects up to natural size are to be cast, a possible method is hollow casting, which is technically related to the formation of church bells : The basic model, the ball, which is usually made of sand, is in a contoured shape. The cavity is filled with melt. After they have solidified, the sand of the ball is removed from an opening in the floor surface. Larger monuments ( Bavaria in Munich , Germania near Rüdesheim , Berlin Quadriga ) are, contrary to popular belief, not cast as a whole, but rather in parts, which are then attached to an inner support frame and soldered together ( hard solder ).
For the production of utility casts , the finished forms are either poured "wet" ("wet casting"), as is the case with aluminum , maintaining a natural or previously set water content, or dried before casting ("dry casting") Process that is preferred for parts made of copper alloys because there is no gas-forming reaction between liquid metal and mold material. In the iron and steel foundry and the larger castings that are customary there, pouring is done in dry molds because they are more stable than wet molds.
When casting larger and thick-walled pieces, it is established practice to favorably influence the solidification time and thus the structure of the cast parts by installing cooling irons in the sand mold at the appropriate points. To supplement and to supply slowly solidifying areas with liquid metal for as long as possible, "feeders" are placed. Often these - including the pouring funnel - still have an exothermic, aluminothermic heat-generating lining. It is intended to prevent premature freezing of the replenishment of the casting, which is subject to a volume reduction during solidification, which is indispensable for sealing feed, i.e. freedom from voids. Depending on the circumstances, exothermic, powdery mixtures are also added to the pouring funnel and feeder heads.
For very large castings, the mold is made in a pit according to the specifications of the model. The molding material is a sand for iron casting that is made bondable by adding synthetic resin ( furan resin ). A size and weight limit results solely from the technical possibilities of the respective foundry. The world's heaviest part made of spherulitic cast iron up to July 2010 weighs 283 tons unmachined and, after machining, becomes part of a forging press operated by ALCOA. To do this, 283 tons of liquid melt at a temperature of 1350 ° C must be provided in five ladles and poured within 120 seconds. The molding can only be done after a cooling time of 14 days. This is followed by milling, which is set to 0.1 to 0.2 millimeters, on one of the world's largest portal milling machines .
Since all sand molds are only used for a single casting, the sand that accumulates after the molding boxes are emptied sooner or later ends up in a dump as "used sand". Multiple use (recycling) enables a simple treatment process: The cooled used sand is sieved, removing lumps, metal splashes and residues of the core material ("core supports"); The moisture content is determined using simple test procedures, missing moisture and binding agents are added and the whole thing is mixed again. Synthetic resin- bound molding sands are processed in a thermal process, which leads to pure quartz sand as the end product, which is again mixed with synthetic resin.
The mechanized production of sand molds for large series, for example in engine casting, is still considered to be the "state of the art". A "Ductalalucast" (protected process and name) combines the advantages of mechanized production of sand casting molds, especially multiple for small parts, with the advantage of increasing mold filling in the low-pressure casting process (see permanent metal molds). Proven improvements in the mechanical values for the alloy EN AC-AlSi7Mg0.3 compared to conventional sand casting are 30 percent for tensile strength and up to 100 percent for elongation and fatigue strength.
An alternative to sand casting already existed in the Bronze Age, when the first permanent molds were invented for simple tasks, the requirement of which, however, was to be made of a material resistant to the heat of the molten metal. The melting temperature of the permanent mold had to be significantly higher than that of the metal to be cast. After all, it was already possible at that time to manufacture copper hatchets "in series" in a bronze form presumably coated with protective clay.
Other molding materials and molding processes (investment casting, 3D printing)
The generic term of the lost form, which applies to sand casting, as opposed to the permanent form , historically also includes open forms made of clay and cow dung, sandstone , baked clay, plaster of paris , synthetic resin (Croning compound) and other materials that are only resistant to a casting . Tin figures and implements can even be cast in chlorinated rubber molds that are resistant at a given temperature . So-called false bronzes were often made from a zinc alloy. The finished castings were then bronzed or blackened.
Investment casting has become technically significant in the production of precision small parts , but it is in strong competition with the 3D printing process, which has been known for a long time, but is constantly being further developed in its possibilities.
In the investment casting process, titanium alloys as well as steel and copper alloys are cast. The shaping is mostly done using the lost wax process, similar to bell casting, or using burn-out plastics for modeling (see under model technology). Any number of wax models can be produced using simple molds. Ceramic compounds , which are placed around the wax model as a bowl or block, are used as molding material for casting . These bowls - put together in the form of grapes - are attached to a metal inlet. In the next step, the wax is melted out with simultaneous hardening of the molding material and the contoured mold cavities are filled with melt. After it has cooled, the shell mold is knocked off.
Originally only intended for small parts, larger parts were also manufactured in investment casting because of their cost advantages compared to sand casting. According to its own statements, one of the largest foundries specializing in investment casting produces 1 million cast parts made of steel, aluminum and copper alloys with a total weight of 4,000 tons per year.
With an increasing number of specialist publications, the 3D printing process, which was originally reserved for “rapid prototyping”, has increasingly been used for parts since the beginning of the 20th century. which were previously reserved for investment casting, or which had to be milled from solid material or assembled from parts due to technical difficulties in terms of shape. This "tool-free" production is not only used for small parts and small series because of its economic advantages, it is also possible to print larger or geometrically complex parts, even those with printed sand cores. According to publications in 2019, a density of the parts of up to 99.8% of the possible is achieved with printed parts made of metal or alloy powders. Further developments in the 3D process are even based on traditional mold production. Sand molds for parts made of non-ferrous alloys can be printed as well as combined as molded parts with parts from "classic" sand mold production.

The art foundry originally used the investment casting process for individual pieces and series made of iron, bronze and zinc.
As a classic investment casting process, investment casting was already used to manufacture steel parts, but these were limited in size and the shaping was associated with considerable costs. The more recent development leaves the "classic" investment casting and provides for the production of thin-walled (> 2 mm) steel castings in the low-pressure casting process in appropriately developed sand molds. The 3D printing process is ideal for this.
As a process related to investment casting, “full-mold casting” can be seen because it also works with lost models. The models are made from polystyrene and molded using various techniques. When the mold is filled, the model is converted into a gas phase without residue.
Gradient casting is assigned to the newer casting processes for light metals . Here a sand mold is filled with two melts, the less stressed parts of the casting with magnesium alloy, the rest with aluminum alloy.
In terms of manufacturing technology, hybrid casting is used in the manufacture of crankcases. Here, a prefabricated “insert” made of an over eutectic aluminum-silicon alloy, which is also coated with AlSi12 alloy, is inserted into the mold for thermally stressed zones of the casting and then encapsulated with a magnesium alloy. The achievable weight reduction of the crankcase can be 25 percent.
Metallic permanent forms
Notwithstanding these early discoveries, the sand shape has remained predominant until recent times. With a share of just under 20 percent for light metal castings, this is no longer the case, but - now highly mechanized - it is indispensable for intricate and core-rich cast parts. A first loss of importance is already around 400 BC. To be recorded. They used permanent metallic molds made of cast iron, which had proven to be the more heat-resistant material than bronze. In the 20th century, cast iron was mostly replaced by special steels whose milled cavities, which are also equipped with metallic cores at key points, correspond to the desired cast piece and offer manufacturing advantages in large series.
The "classic" permanent molding process is considered to be the industrially insignificant lintel casting, which was used in the production of hollow bodies made of zinc alloy: A cast iron mold was filled with melt, waited for the first solidification phase that started from the mold wall, the mold tilted and let the not yet solidified residual metal flow back into the melt. After opening the mold, you got an open jug, vase, or urn.

A permanent metallic form, which also enables castings that require one or more cores made of steel for this purpose, is used by gravity die-cast (also known as "gravity die-cast", see also die casting process ). The mold , which is lined with a “coating” that is gentle on the mold and directs solidification, is filled with a manually operated or automated pouring spoon. After complete solidification in the mold, the steel cores are pulled with the so-called "Knippeisen", the cast part is removed and the mold is prepared for the next casting. This also includes checking the arbitration, which is heavily stressed by the temperature change and, if necessary, has to be improved by hand, using a spray device or fully automatically. For aluminum chill casting, insulating, rough coatings have proven their worth, the durability of which can be extended considerably if they are coated with a thin nanoceramic film.
A variant designed for the production of high-quality cast parts in large numbers is "low-pressure chill casting". Within a closed system, which is formed by a furnace with a melt ready to be poured and the riser pipe that leads to the mold - usually even a multiple mold - the opening of a compressed air or inert gas supply causes the melt to be pressurized, which then leads to the mold via the riser pipe ( n) and fills it under sustained pressure that counteracts any shrinkage or pore formation. After the metal has solidified in the mold, a clock control releases the pressure, releases the solidified cast parts and lets the metal still in the riser run back into the holding furnace. A new bar can begin.

Not only metallic cores made of sand or other compressible materials but also bound with inorganic additives or synthetic resins are used in permanent mold casting and this where a metal core is not technically possible. A well-known part made using this technology is the water meter .
Between sand casting and permanent mold casting, there is a mold production technique in which the solidification of the outer walls of the casting is determined by an adapted permanent mold, while that of the inside of the mold, with its dedicated cavities, is determined by a sand core solidified by a binding agent. This can be a single core, but in practice core packages composed of single cores are the rule here as well. The more intricate the core structure of a casting, the more important it is to remove the cores easily after the mold has been poured. There are various methods that are based on water glass as a binding agent for the core sand mixture. The finished kernels are showered with carbonic acid and hardened with it.
Salt cores are widely used as an alternative. They are primarily used in the manufacture of diesel pistons. After the piston blank has cooled down, the salt core is washed out of the cast part without leaving any residue. In general, a distinction must be made between cores cast from molten salt and cores pressed from granules. Salt cores made of sodium chloride ( table salt) and simple, chemical additives are created from a melt using the lost foam process , with a high level of complexity and strength, which is particularly popular in die casting, in relation to the requirements of the casting process. Even just pressed or sintered salt cores consist of table salt. The somewhat lower strength properties, however, do not rule out case-related use in die casting.
The parts that are only suitable for economical mass production using the die casting process include numerous pieces of equipment that were previously soldered together from sheet metal, such as the carburetor of gasoline engines.
Although it has been modernized in many respects and is still common today for the production of high-strength parts in vehicle construction, the process has proven to be time-consuming for the production of very large series. This costly circumstance gave rise to the development of a more productive casting technique in permanent molds after the First World War . After a hesitant start around 1920, starting with zinc alloys, the technique of permanent mold filling with metal injected under high pressure has become so popular in aluminum and magnesium castings within a century that more alloys are processed using the " die-casting process " than in any other way. In its early years, the technology was mainly used for smaller parts, for which machines with a clamping force of 250–500 kN were sufficient, today machines with clamping forces of 4,000 kN and more are capable of producing large, thin-walled parts such as doors, engine hoods and trunk lids for automobiles. The relevant mechanical engineering sector contributed to this “quantum leap”. This includes the provision of a casting cell that was specially designed for the production of extremely complex, thin-walled, but highly resilient structural components, primarily for the automotive industry that is required to save weight. At the beginning of the 21st century, die casting is the most automated variant of die casting. A casting technique that has been improved for the production of resilient cast parts, in which the mold is evacuated before filling, produces pore-free and inclusion-free castings at high pressures, as is necessary for high-performance diesel engines, and also makes die-cast parts accessible to heat treatment that greatly improves the mechanical values. In many cases they can be installed without any post-processing, especially if there is a particularly critical check for porosity using computed tomography. The proportion of the total cast of light metals (according to figures from 2005 about 700,000 t) increased to over 65 percent as a result of the new technologies. Although lower in terms of quantity - around 70,000 t in Germany in 2014 - zinc alloys standardized under EN 1774 with the addition of aluminum and copper have opened up numerous areas of application
Format cast
The form casting discussed here, i.e. the shaping defined for small to large series with at the same time either “lost” or, within predetermined limits, “permanent” form, is related to the quantitatively more significant format casting , also called format casting / semi-finished casting , only to the extent that liquid metal is used in a Further processing is brought favorable form.
Shaping takes place in the continuous casting process using round, rectangular or square (collar) molds, which, regardless of the special casting technique, can still be assigned to the permanent metal molds and enable the production of round billets or right-angled rolling bars.
Formateguss comes from both the iron and steel foundries (cast-houses), which are connected to the primary smelters that produce primary aluminum from alumina , but also from recycling or secondary smelters that deal with the recovery of scrap aluminum and aluminum waste.
The cast bars and, depending on the alloy, either stored at room temperature or "tempered" in specially designed furnaces are, as "unfinished semi-finished products", only input material for the final processing by drawing , rolling , pressing , forging and the end products of these processes in the form of sheets , Profiles, wires , foils, cans and others.
Strip casting is determined by the requirements for further processing - fewer rolling passes for thin sheet production. The collar mold of the continuous casting is replaced by two water-cooled rollers whose speed of rotation is controlled. They leave a gap between them, into which the melt flows and is released again in the course of the rotation to the band.
Economic importance (production quantities)
With regard to the amount (in kg) of cast products, cast iron leads by a clear margin over non-ferrous metal castings , which in turn are dominated by light metal castings. In terms of quantity, light metal casting ranks second, although the weight differences determined by the physical density must be taken into account. In this respect, one kilogram of cast aluminum is equivalent to three kilograms of cast iron for statistics of the cast volume. The worldwide amount of light metal castings given for 2012 as 14.3 million tons would correspond to 43 million tons of gray cast iron, which is roughly equivalent to its world production in 2012. The total amount of other cast iron and steel cast in the world is, however, another approx. 38 million tons, including almost 25 million tons of nodular cast iron and approx. 11 million tons of cast steel.
The statistics of world casting production for 2012 state - with a few minor inaccuracies in the time recording - a production volume of over 101 million tons of all types of castings for all participating countries.
Germany's share is 5.214 million t of castings. In addition to the majority of iron (and steel), non-ferrous metals make up around 22 (mass) percent. This includes 802501 t aluminum, 77390 t copper, 16444 t magnesium, 34772 t zinc, including their respective alloys, and only 9 t “other non-ferrous metals”. In terms of volume, Germany increased by 12% in the reporting period, compared to a global decline of 6%, which was particularly influenced by China and India.
Reference and further reading
- Heinz Wübbenhorst: 5000 years of casting metals. Foundry publishing house, Düsseldorf 1984, ISBN 3-87260-060-5 .
- Foundry glossary. 17th edition. Schiele and Schön, Berlin 1997, ISBN 3-7949-0606-3 .
- Josef Bersch: Lexicon of metal technology. Handbook for all traders and artists in the metallurgical field. Hartleben, Vienna around 1899.
- Roland Irmann : Aluminum casting in sand and mold. 5th edition. Aluminum headquarters, Düsseldorf 1952 (chapter sand casting and chill casting).
- Foundry review. 58, No. 7/8, 2010 (technical and economic special articles).
- Paul-Georg Custodis: The Sayner hut. (= Historic landmarks of civil engineering in Germany. Volume 5). Federal Chamber of Engineers, Berlin 2010, ISBN 978-3-941867-05-5 .
References and footnotes
- ^ H. Wübbenhorst: 5000 years of casting metals. Foundry publishing house, Düsseldorf 1984, p. 11 f.
- ↑ One of them is the Sayner Hütte casting hall, which was completed around 1828 (detailed articles on this in Even a cold memorial needs more than warm words. In: Frankfurter Allgemeine Zeitung. No. 197, August 26, 2010 and in A Gothic church served as a model. In: Frankfurter Allgemeine Zeitung. No. 207, September 7, 2010 p. T6.). A comparable object is the bridge over the British River Sewern, inaugurated in 1799 and still accessible today.
- ↑ Leopold Kniewallner, Guido Rau: Bionics and casting - a good combination. In: Giesserei-Rundschau. 56, No. 9/10, 2009, p. 158 f.
- ↑ Anton Stich: Resource efficiency and lightweight construction with cast from the perspective of a premium manufacturer. Lecture, given on February 5, 2013 in Magdeburg, at the 7th VDI conference "Casting Technology in Engine Construction", see also reports of the same name in VDI-Verlag, Düsseldorf 2013, (pp. 51–60)
- ↑ Lost wax process, full mold process
- ↑ Press release from April 25, 2016, Erzmetall 3/2016, p. 138, there W. Volk and colleagues: Process development for 3D printing with inorganic molding material systems. Lecture on the occasion of the VÖG conference 2014 in Bad Ischl, printed in VÖG Giesserei-Rundschau. Vol 61, issue 5/6, p. 152.
- ↑ ALCOA reports in a press release dated April 7, 2016 about the planned use of Airbus parts based on titanium. Erzmetall 3/2016, p. 136.
- ↑ FOSECO Kaltek system
- ↑ Numerous literature, just as an example V. Bechny: Future challenges to Giessereisande. In: Giesserei Rundschau. Vol. 59, issue 3/4 2012, p. 81.
- ↑ When synthetic resin is used as a binding agent, a distinction is made between hotbox and coldbox processes , whereby the “box” (also known as the core box (core shape)) is used to strengthen the core with or without heat (hotbox).
- ↑ AC TECH press release of June 26, 2013. In: Erzmetall. 4.2013, under "Technology", p. 199.
- ↑ Cooling iron, also called heat sink, chill or shock plate
- ↑ According to a press release from the specialized Krefeld company Siempelkamp (May 22, 2014), this has now been surpassed for a 50,000 t press delivered to China in 2014.
- ↑ This includes kneading a ball of sand by hand and checking whether hand lines are reproduced, as well as resisting breaking or dropping it from different heights
- ↑ Press release of "Eurotech Aluminum Castings", Venlo, NL, from November 17, 2009, reproduced in Erzmetall. 63, No. 1, 2010, p. 44.
- ↑ Tail rotor housing for helicopters according to press release of April 21, 2009 in Erzmetall. 62, No. 3, 2009, p. 186.
- ↑ Innovative investment casting from Riedlingen. In: VDG current. No. 1, 2011, p. 8.
- ↑ Ingo Ederer: 3D printing, turbo for casting processes of all kinds. In: Foundry Rundschau. Volume 62, Issue 7/8, 2015, p. 178 f.
- ↑ On this also Martina Pall: Iron art castings from Austria and the monarchy. In: Foundry review. 11/12 61, vol, p. 356.
- ↑ Klaus Eigenfeldt: Foundations for the foundry industry - foundations for the future. In: Foundry review. 58, No. 5/6, 2010, p. 80 (lecture given on April 23, 2010 at the 54th Austrian Foundry Conference in Leoben).
- ↑ Full- mold casting process. In: Giesserei Lexikon.
- ↑ Technological properties and potential of magnesium alloys. In: Giesserei-Rundschau. No. 7/8, 2009, p. 114 (Report on a conference lecture of February 12, 2009 on magnesium in vehicle construction.)
- ↑ Black sizing dissipates heat and accelerates solidification, white sizing has a heat insulating effect and delays solidification
- ↑ More detailed under low-pressure mold casting. In: Foundry Lexicon. 17th edition. Schiele & Schön, Berlin 1997, ISBN 3-7949-0606-3 .
- ↑ Casting of cylinder blocks for water-cooled engines is typical for this.
- ↑ N. Erhard, Slabjan Babic: Modern die casting - today and fit for the future with innovations. In: Giesserei Rundschau. Trade journal of the Austrian Foundry Associations. Vol. 60, issue 7/8, 2013. Also ore metal. 6/2013, p. 324, press release Fraunhofer IFAM from November 13, 2013.
- ↑ On the occasion of Euroguss 2010, a door frame for the Porsche Panamera was awarded. Source: GF, Schaffhausen, press release from January 19, 2010.
- ↑ Manuel Callegari: Structural system for the class leader from Switzerland. In: Giesserei-Rundschau. 58, No. 3/4 2011, p. 62.
- ↑ Wolfgang Schöffmenn: High-performance diesel crankcase development in aluminum. In: Giesserei-Rundschau. 58, p. 70.
- ↑ See also under further literature
- ↑ Die- cast zinc - versatile in use and innovative in casting technology. Lecture at the 16th International German Die Casting Day 2016. In: Giesserei-Rundschau. Volume 63, issue 3/4, 2016, p. 69 f.
- ↑ The numbers in this section come from the “47. Survey on world casting production ”, published in VÖG Giesserei-Rundschau. Jhg. 61, issue 1/2, 2014.
- ↑ Survey of world casting production according to VÖG Giesserei-Rundschau. as above . 61, No. 1/2, 2014, p. 46.