Coking plant

In a coking plant , coke and raw gas are produced from coal using a dry distillation process. The volatile components in the coal are pyrolyzed by heating to a temperature of 900 ° C and 1400 ° C , released and sucked off. For around 70 years, regenerative firing, in which the released components are used to fire the coke ovens, has been established. A layer of ash is created on the finished coke. The degassing of the coal forms a porous coke that contains almost exclusively carbon . The raw gas is broken down into the carbon materials tar , sulfuric acid , ammonia , naphthalene , benzene and coke oven gas by fractional condensation , which are further processed in chemical plants . There are currently five coking plants in operation in Germany (2017).
Coke is needed in the blast furnace to produce pig iron (steel production). That is the main use today. The sulfur content is significantly reduced through gasification, so less sulfur is released when the coke is burned . Sulfur is undesirable when used in blast furnaces because it significantly reduces the quality of the iron melt. The mineral ash components of the coke remain unchanged compared to the raw coal.
History and basics
In the early days of iron production , only charcoal was used to smelt ore . Untreated fossil coal (brown and bituminous coal) or uncarburized wood are not suitable for this purpose, as the necessary high temperatures cannot be reached and, due to the lower purity of the fuels, insufficient pig iron quality cannot be achieved. Due to the need for wood, which was converted into charcoal in a very similar process as in the case of coal coking , entire areas of land changed their appearance through the deforestation of huge trees. It was not until the 18th century that coal coking was developed, which uses fossil coal as a raw material. The newly created fuel replaced charcoal and made today's mass production of pig iron possible .
By heating coal in the absence of air, the fuel coke is produced, which is specifically richer in carbon , purer and of more uniform quality than the raw material coal.
Due to the controlled conditions in the coking process, the product coke can be adapted to certain requirements depending on the intended use, such as
- Water content,
- Ash content,
- Sulfur content,
- Grain size,
- Strength,
- Abrasion.
The most common end products today are blast furnace and foundry coke. One of the important properties of blast furnace coke is its strength even at high temperatures. In addition to serving as fuel, the coke in the blast furnace supports the entire column of ore and aggregates . Coal in its place would baked and make it difficult to aerate the mixture.
Operational flow
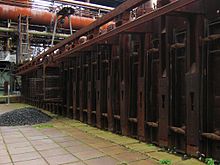
- Delivery, mixing, grinding and bunkering of the raw coal
- Picking up an oven filling with the loading cart on the oven roof
- Open the filling openings on the furnace roof
- The process of pouring the coal into a single coke oven
- The coal is stuffed depending on the furnace principle and coal quality
- Airtight sealing of the oven
- Heat
- This is followed by outgassing and the achievement of the correct porosity
- Open the front and rear oven doors
- Express
- Extinguishing and at the same time refilling the furnace
After a furnace has been filled, the loading carriage drives back to the coal bunker and the process starts all over with another furnace. The operational processes are coordinated in such a way that a pressing process can take place every few minutes. The furnace walls are continuously heated with the gas produced during the coking process. Depending on the target properties of the coke and the size of the oven, the baking time is between 15 and over 30 hours.
Required staff / jobs
For the smooth operation of the black side , the following jobs must at least be filled:
- Filler - drives the filling truck
- Einfeger - closes and sheds the filling lids, sweeps the ceiling clean; at least one, often even two employees
- Door actuator machine side (MS) - operates the "door opener" on the push machine and cleans the master aisle
- Spinning machine operator - drives and operates the spinning machine
- Door plate coke side (KS) - drives and operates the KKF wagon; cleans the corridor in front of the ovens
- Fire truck driver (with wet extinguishing, less common today) - operates the fire truck; cleans the extinguishing tower as far as possible at ground level
- Ramp puller - operates the coke ramp, i.e. This means that the coke from the extinguishing car is directed onto a conveyor belt that leads to the screening plant
- Foreman - directs and coordinates the battery operations as instructed by the coke or gas master
- Coke / gas master - responsible supervisor for at least one coke oven battery
The black side
The actual production of the coke takes place on the so-called black side of a coking plant. During the work in this area, dust and exhaust gases are generated, which led to the name being given.
Coke oven
The coke oven is the central component of a coking plant. The mostly used horizontal ovens (direction of movement when pushing out coke) are usually several meters high and deep, but only about ½ m wide. The most modern furnace chambers have a volume of up to 100 m³ (e.g. 0.5 × 6 × 32 m). As a rule, these chambers are combined into what is known as a furnace battery , with the furnace chambers always being arranged between heating flues in which gases are burned at 1200 to 1400 ° C and thus heat the furnace walls. The heating gas comes from the gas cleaning system, which is also the secondary recovery system. If there is a blast furnace in the vicinity, the furnace gas with the low calorific value is used, with coke gas with a high calorific value then added. The underfiring changes back and forth between the machine side and the discharge side about every half an hour, so that the chambers are heated more or less evenly.
After the first firing phase of around three months when a coking plant is put into operation, the heating process takes place continuously. Too fast heating or immediate switching off of the lighting of a battery inevitably leads to strong thermal stresses, which irreparably destroy the system.
Like a blast furnace, the inside of the coke ovens is lined with heat-resistant fireclay or silica bricks. Each furnace has three openings that are important for its operation, the front and rear doors on the front sides, which are as wide as the chambers, and at least one filling opening on the furnace roof for charging the furnace with coal, but usually four to five around the coal Bring as evenly as possible into the oven and distribute. The brought in coal is smoothed out with a leveling bar. This leveling bar is located on the spinning machine and is set in motion by this.
Oven roof
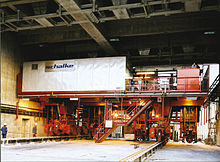
The oven roof is not just the roof of a coke oven battery. On the top of the furnace, the charging trolley moves back and forth between the individual filling openings of the coke ovens and one or more coal bunkers . The workplace on the furnace ceiling is not without danger. Heat, dust, gases and flames make work difficult.
Coal bunker
Depending on the type of system, there are one or more coal bunkers on the furnace roof or at one of the ends of a battery. A bunker contains the coal supplies that are brought into the furnaces by the charging trucks. Bunker coal is a mixture of different types of coal that has been matched to the target properties of the coke and that has already been given a certain grain size through sieving or grinding.
Machine side
The machine side is the side of a coke oven battery on which the spinning machine (also known as the "push locomotive") runs (drives). The task of the spinning machine is to squeeze out the finished coke cake (the coking coal cooked in the absence of air) for further processing. For this purpose, a rod is used, which is very often divided into two or three parts, in order to be able to travel the entire length of the furnace. The push head is located at the front end of this rod. The passage in front of the ovens on the machine side is called the master passage. This aisle on the machine side is so wide that not only the “door operator” can go about his work here, but also the “coke master” (also known as the “gas master”).
Coke expressing machine from the Schwelgern coking plant, Schalke Eisenhütte
Mobile stage of the Prosper coking plant
Coke side
The coke side is that side of a coke oven battery on which the cooked coke falls out of the oven and, with the help of a transfer machine, gets into the fire fighting vehicle. So that this can happen without any problems, the “coke cake guide carriage”, also known as the KKF, drives here. A machinist (door operator) operates the machine and drives to the corresponding furnace. When all safety signals are green, the door is opened with the KKF. The KKF then moves the "tub" into position. In modern coking plants, this process is controlled fully automatically. This tub is only the guide for the coke cake, from the oven via the aisle to the fire fighting vehicle.
Transfer machine of the Schwelgern coking plant, Schalker Eisenhütte
Coke extinguishing
A distinguishing feature of the process management is the type of coke extinguishing. As soon as contact with atmospheric oxygen is established by opening, the coke begins to burn at the temperatures that are still present. To prevent this, it must be quickly extinguished and cooled down.
This cooling can be done in the following ways:
Wet coke cooling
- Approx. 2 m³ of water are required per ton of coke for extinguishing.
- Thermal energy is lost.
- approx. one third of the extinguishing water evaporates.
- Problematic cleaning of the water vapor, which is mainly contaminated with dust, water gas and hydrogen sulfide
In 1986 the measured values for a wet coke cooling process were between 200 and 2000 g of dust per ton of coke. In the modern CSQ (Coke Stabilizing Quenching) process , only 10 to 15 g / t are expected.
Dry coke cooling
(mostly with nitrogen as inert gas )
- enables energy recovery (heat, power generation)
- no water consumption
- less dust generation
- higher coke quality due to lower water content
- expensive to build and maintain
Dry cooling pays for itself after 3 to 5 years.
The white side
Main article: Carbon recycling plant
In the middle of the 19th century, valuable raw materials for the chemical industry began to be extracted from the coke oven gases . The system components that take on the task of gas scrubbing and the separation of various substances are usually built on the machine side and supplied with the coke oven gas through thick pipes in the gas receiver. Normally there is no dust or other visible contamination, hence the name "white" side or carbon recycling plant . A blower known as a gas suction device is used to extract the raw gas from the gas reservoir and then convey it through the auxiliary recovery systems. It is crucial here to keep the gas supply under a slight excess pressure (around 2 mbar to 5 mbar). A negative pressure would promote the penetration of atmospheric oxygen and thus cause an explosion risk. If the gas suction device is disturbed, it is flared.
First the raw coke oven gas is cooled down and then washed in so-called gas washers. Subsequently, the individual washed out components of the further processing for the production of the following by-products are fed to the respective production processes:
Byproducts
- tar
- benzene
- sulfur
- ammonia
- Ammonium sulfate (fertilizer), less often ammonium nitrate (also as a fertilizer)
- sulfuric acid
- Phenolate liquor
Current coking plant (2005)
The world market price for coke fluctuates strongly. From 2002 to 2004 the world market price for Chinese coke rose in the wake of the global steel boom from around 80 US dollars to around 350 US dollars, more than quadrupling the price, three times as much as the increase in steel prices over the same period.
At the same time, the Chinese in the Ruhr area dismantled the modern Kaiserstuhl coking plant in Dortmund . The last plant in Germany with dry coke cooling was missing guaranteed sales after the Thyssenkrupp group had stopped its pig iron and steel production in Dortmund and concentrated it in Duisburg .
The three remaining coking plants in the Ruhr area , the Bottrop plant Prosper coking plant , the Schwelgern coking plant and the coking plant of Hüttenwerke Krupp Mannesmann , have been working at their capacity limit for three years. For the coking plant of Hüttenwerke Krupp Mannesmann in the south of Duisburg ( Huckingen ), an application for approval for the expansion of a further battery was submitted to the Düsseldorf district government on June 3, 2005. Approval was granted on January 13, 2006. On March 29, 2014, the first coke was pressed and the extension of the coking plant was put into operation.
In December 2005, the restructuring of the central coking plant Saar GmbH, Dillingen was decided. The concept envisages the construction of a new third battery. After commissioning, the old battery no. 1 is heated up and rebuilt. The second old battery then goes out of service.
Industrial policy
As a result of the sharp rise in coke prices, some coal proponents believe that it is now economically viable again to mine coal in Germany and dig new shafts. There are plans for a new mine to the north of Hamm , supposedly free of subsidies , but their realization is considered unlikely due to the high investment costs. Skeptics are already seeing economic follow-up costs from the next sales crisis when investing in the current economic cycle. In addition, it is still open whether the promotion will be possible without subsidies.
Related articles
literature
- Handbook of the gas industry , especially Volume 1 “ Gas Generating Furnaces”, Dr.-Ing. Horst Brückner u. a., Verlag R.Oldenbourg Munich / Berlin 1938
- Walter Buschman: Collieries and coking plants in the Rhenish coal industry. Aachen district and western Ruhr area . Mann, Berlin 1998, ISBN 3-7861-1963-5
- Dietmar Osses: coal, coke, culture. The coking plants of the Zollverein colliery . Foundation for the preservation of industrial monuments and history culture , Dortmund approx. 2002, ISBN 3-935783-09-4
- Franz Michael Ress: history of coking technology . Glückauf, Essen 1957
- Fritz Schreiber: Development and current status of the coking industry in Lower Silesia . Springer, Berlin 1911 ( digitized version )
- Michael Farrenkopf (Ed.): Koks. The history of a resource , 2 volumes. German Mining Museum, Bochum 2003.
Individual evidence
- ↑ Uhde: Competence and know-how by tradition - A new dimension in cokemaking technology ( page no longer available , search in web archives ) Info: The link was automatically marked as defective. Please check the link according to the instructions and then remove this notice. (PDF; 3.9 MB)
- ↑ Rolf Peter Sieferle : The underground forest. Energy crisis and industrial revolution. Munich 1982
- ↑ Case Study of Technology Transfer between Japan and China in iron / steel industry ( Memento from May 12, 2006 in the Internet Archive ) (in English; PDF; 3.3 MB)
- ↑ Theo Payer, Wilhelm Baum: Gas cleaning and by-product extraction ( Memento from January 28, 2016 in the Internet Archive ) (PDF; 5.0 MB)
- ↑ Stefan Willeke: "Mr. Mo fetches the factory - the most modern coking plant in the world is moving from Dortmund to China" In: DIE ZEIT No. 40 of September 23, 2004
- ↑ wa.de: Plans for a Donar production site are finally a thing of the past , February 7, 2013.
Web links
- Pictures of coking plants in Europe and North America
- Schwelgern coking plant - interactive panorama - also in large image formats
- Photographs of coking plants
- August Thyssen coking plant - detailed description, numerous photos and illustrations
- Video of a push