cement

Cement ( Latin caementum "quarry stone", "building block") is an inorganic and non-metallic building material . It is finely ground and therefore counts as a bulk material . Due to its properties, it is manufactured in cement works as a building material and used to manufacture components and structures. Cement is one of the binders within building materials . It hardens through the chemical reaction with water ( hydration ) and then remains solid. For the production of building materials such as mortar and concrete , so-called additional water (formerly “mixing water”) and other substances are added to the cement as additives . Due to the worldwide availability of raw materials and the strength and durability of concrete, cement is one of the most important binders worldwide. With a world production of 4.1 billion tons in 2017, cement is the most widely used material .
Cement is produced in cement works. The natural raw materials limestone and clay are used for its production , which are often present as a natural mixture and are then referred to as marl . If necessary, quartz sand and materials containing iron oxide are added as correction materials for better sintering . The raw materials are ground into raw meal and then heated to around 1,450 ° C until they partially fuse together at the grain boundaries ( sintering ) and what is known as cement clinker is formed. The now spherical material is cooled and ground to the end product cement. In order to obtain cement types with certain properties, blast furnace slag , fly ash , limestone and gypsum can be added in different dosages and grinding fineness before grinding .
history
The German word cement goes back to the Latin name opus caementitium . The opus caementitium , which was known to the Romans over 2000 years ago, was not, however, cement as it is today, but a concrete-like masonry. It can be seen as the forerunner of today's concrete and consisted of burnt limestone as a binding agent and stones , sand and pozzolans as an aggregate. Since the opus caementitium was resistant to water, it was used for the construction of water pipes and harbor moles , but also for foundations and for structures such as the Colosseum and the Pantheon .
Later cementum , cimentum , cäment and cement were used to denote aggregates such as volcanic ash, pozzolans and brick dust, which were added to the quick lime in order to obtain a hydraulic binder ( hydraulic lime , water lime). The importance of the clay content for the hydraulic properties of cement ( Roman cement ) was discovered by the Englishman John Smeaton (1724–1792). Since then, cement no longer stands for the aggregate, but the binding agent.
The French Louis-Joseph Vicat (1786–1861) laid the foundations for the development of cement and lime mortar with the rediscovery of "Roman cement" and the invention of artificial hydraulic lime .
The Englishman Joseph Aspdin (1778–1855) is considered to be the real inventor of Portland cement . In 1824 he received the Patent An Improvement in the Mode of Producing an Artificial Stone ; in the patent he used the term "Portland cement". The name was based on the Portland stone , a limestone that was quarried on the Portland peninsula on the English Channel coast and was similar in color to the artificial products made from Portland cement.
This "Portland cement" was not yet cement in the current sense, but an artificial novel cement : Isaac Charles Johnson (1811–1911) was the first to recognize the importance of sintering in 1844 and, with his improved process, to use the "real", overburned Portland cement introduced the construction industry, where it quickly ousted Roman cement due to its superior hardness.
In 1838 the Ulm pharmacist Gustav Ernst Leube and his brothers founded the first German cement works in Ulm . The first German Portland cement based on the English model was produced in Uetersen . The basis for the production of Portland cement in Germany was laid by Hermann Bleibtreu (1821–1881), who also built two cement works in Züllchow near Stettin (1855) and in Oberkassel near Bonn . Wilhelm Michaëlis (1840–1911) had a decisive influence on further development . In his book entitled Die hydraulic Mörtel , published in 1868 , he was the first to provide precise information about the most favorable composition of the raw material mixture. One of the oldest existing structures to have been executed in Portland cement is the old forge, built by Berliner Cement AG from 1871 at Spittastraße 40 in Berlin-Lichtenberg.
In 1877 all 23 existing German Portland cement manufacturers joined together to form the Association of German Portland Cement Manufacturers in order to “clarify all technical and scientific questions that are important for the cement industry in joint work”. Together with the elaboration of a uniform test method and the establishment of regulations for the requirements to be placed on the quality of cement and in conjunction with the architects' associations, the Berlin hardware store, which the German Association for the manufacture of bricks, pottery, lime and cement began in 1876 and the brick industry, the first Prussian standards for testing Portland cement were issued in 1878, and were immediately prescribed for all state buildings.
Manufacturing process
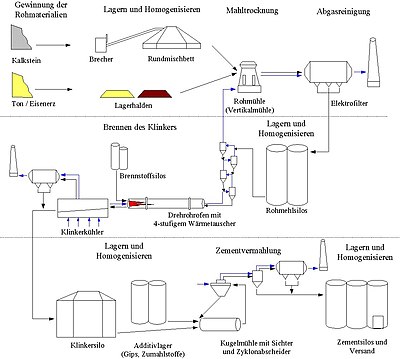
The raw material for cement is mainly made from natural raw materials, ground and mixed in a dry process , then burned, cooled and re-ground in a continuous process in rotary kilns . Typical throughputs of the rotary kilns are 3,000 to 10,000 tons of clinker per day.
The predecessors of the dry process for grinding raw materials were wet and semi-wet processes, in which the raw materials were ground and mixed while wet. However, because of the high energy consumption in the subsequent drying, these processes are usually no longer competitive today.
The raw materials are limestone (calcium carbonate as a source of calcium oxide ), clay (for silicon dioxide and aluminum oxide ), sand (for silicon dioxide) and iron ore (iron (III) oxide). By adding additives such as B. blast furnace slag , pozzolan or fly ash , cements with different chemical and physical properties can be produced. Gypsum or anhydrite is added to the end product.
The raw materials are mined in quarries or opencast mines , pre-crushed in crushers and transported to the cement works. In a vertical mill or raw mill, all raw materials are ground together and dried at the same time. The resulting raw meal is then burned in a rotary kiln at temperatures of approx. 1,400–1,450 ° C to form what is known as cement clinker . When burning, the carbon dioxide bound in the lime is released. After cooling to a temperature below 200 ° C, the gray-brown granules are then ground in a ball mill together with plaster of paris to form the finished product, cement.
See also: Technical lime cycle # Burning of lime .
Classification and characteristics
By grinding in materials such as blast furnace slag , pozzolan , fly ash or limestone , cements with special chemical and physical properties are obtained. For example:
- Low rate of hydration, low heat of hydration cement, LH
- Cement with high sulphate resistance, SR ,
- Low Alkali Effective Cement, NA
In addition to the chemical and mineralogical composition, the fineness of a cement is also decisive for its properties. In principle, it can be said that a cement that is finer also develops a higher strength. The specific surface area (also known as Blaine ) serves as a measure of the fineness and is normally between 2,500 and 5,000 cm² / g.
Types, strength and use according to EN 197 and DIN 1164
designation | Compressive strength [N / mm²] | Identification color | |||
---|---|---|---|---|---|
after 2 days | after 7 days | after 28 days | Sack color | Inscription color | |
32.5 L | - | ≥ 12.0 | 32.5-52.5 | light brown | |
32.5 N | - | ≥ 16.0 | black | ||
32.5 r | ≥ 10.0 | - | red | ||
42.5 L | - | ≥ 16.0 | 42.5-62.5 | green | |
42.5 N | ≥ 10.0 | - | black | ||
42.5 r | ≥ 20.0 | - | red | ||
52.5 L | ≥ 10.0 | - | ≥ 52.5 | red | |
52.5 N | ≥ 20.0 | - | black | ||
52.5 r | ≥ 30.0 | - | White |
The strength of cements in Europe is regulated by the European standard EN 197. A distinction is made between three different strength classes, with standard strengths of 32.5, 42.5 and 52.5 N / mm² after 28 days of hardening. Depending on the initial strength of a cement, it is also referred to within a strength class as slow (L), normal (N) or faster curing (R, from English rapid ). In order to prevent mix-ups, especially on the construction site, the cements in Germany are assigned color codes on the paper of the cement sacks and the imprint. The assignment takes place in DIN 1164. The European standard dispenses with such markings.
In addition to strength, EN 197-1 also classifies cements according to their composition. Five different types are defined in the standard:
- CEM I - Portland cement
- CEM II - Portland composite cement
- CEM III - blast furnace cement
- CEM IV - pozzolan cement
- CEM V - composite cement
In addition, 27 types of normal cement are generally defined using the percentage by weight of the starting materials. Other cements are called special cements . A description regulation regulates the designation of these cements, for which no precise composition is defined in the standard.
In addition to EN 197-1, DIN 1164 in Germany specifies the intended areas of application for the individual types of cement. Depending on the expected environmental influences and installation situations, DIN 1164 defines “exposure classes” and names the types of cement that are suitable in each case (e.g. cements containing slag are suitable for the production of underwater concrete).
Portland cement


Portland cement is produced by grinding cement clinker and lime or anhydrite . From a chemical point of view, it consists of approx. 58 to 66% calcium oxide (CaO), 18 to 26% silicon dioxide (SiO 2 ), 4 to 10% aluminum oxide (Al 2 O 3 ) and 2 to 5% iron oxide (Fe 2 O 3 ).
From a share of 36% slag sand , the cement is called blast furnace cement .
In dentistry, a modified form of Portland cement called Mineral Trioxide Aggregate (MTA) is used for the retrograde closure of root canals .
Special cements
- Trass cement
- Trass cement is made with the addition of the natural pozzolan trass and results in a more waterproof mortar than Portland cement. It is used for bricking up natural stones because it shows less efflorescence .
- Alumina cement
- Similar to Portland cement, but with a high aluminum content . As a result, little calcium hydroxide is formed during hardening , which ensures an alkaline environment and protects the reinforcing steel from corrosion. In Germany therefore not approved for load-bearing structures.
- Rapid cement
- Fast-setting cement, usually a mixture of Portland and high alumina cement
- Spray cement
- Spray cements or spray binders are fast-setting binders that guarantee rapid strength development even without the addition of setting accelerators in the manufacture of sprayed concrete . During the production of the cement, raw plaster of paris is not ground into the clinker, which provides the generally desired delay in setting time for cement. Robert Keller from Vils in Tirol first used this type of cement for the production of shotcrete in 1983, which is now also used in Austria and Germany in tunnel construction .
- Fiber cement
- White cement
- Cement is usually a gray powder. In addition, white cement called Dyckerhoff white is also produced, which, like white lime hydrate, serves both as a pigment and a binding agent . White cements are made from raw materials that are very low in iron ( Fe 2 O 3 content <0.1%) and are mainly used for terrazzo , exposed concrete and colored (precious) plaster . White cement is not only suitable for light-colored preparations, but can also be colored more easily with color pigments than ordinary gray Portland cement, so that it is used for the production of cement tiles and terrazzo tiles .
Special cements
- Thurament
- is a special cement made from blast furnace slag or blast furnace slag with a proportion of gypsum, which is produced in Thuringia.
- Celitement
- is a special cement that, in contrast to conventional cement, has a significantly more favorable material and energy balance. Celitement is produced at temperatures below 500 degrees Celsius, just as robust and strong as conventional cement. This brings considerable ecological and economic advantages.
composition
During the burning process in the rotary kiln, after the calcination of the lime (CaCO 3 ) to calcium oxide , which releases CO 2 , these main constituents are partially sintered to form minerals that are of crucial importance for the special properties of cement. The most important of these connections are:
- Tricalcium silicate (alite), C 3 S for short (general chemical formula 3 CaO SiO 2 )
- Dicalcium silicate (belite), short C 2 S (2 CaO SiO 2 )
- Tricalcium aluminate, short C 3 A (3 CaO Al 2 O 3 )
- Tetracalcium aluminate ferrite, short C 4 AF or C 4 (A, F) (4 CaO · Al 2 O 3 · Fe 2 O 3 ) and C2 (A, F).
When cement hardens with water ( hydration ), calcium silicate hydrate fibers, CSH or C 3 S 2 H 3 (3 CaO 2 SiO 2 3 H 2 O) for short, grow on the one hand , and portlandite , CH ( Ca (OH ) for short ) is formed on the other ) 2 ), which gives the end product a high alkalinity with a pH value of 12-14.
Hydration and strength development
In contrast to (air) lime mortar , cement is a hydraulic binding agent. Substances that harden in the air as well as under water and are also resistant are regarded as hydraulic . It does not harden like air lime by absorbing carbon dioxide from the air, but reacts with water to form insoluble, stable compounds. These compounds, the calcium silicate hydrates, form fine needle-shaped crystals, which interlock with each other and thus lead to the high strength of a cement mortar or concrete.
Side reactions of hydration are for example
- Alkali-silica reaction . When it increases in volume, it can cause concrete to crack.
- Pozzolanic reaction . It causes an increase in strength within several months.
- Formation of wollastonite (calcium silicate).
The setting and hardening of the cement is based on the formation of water-containing compounds, which arise during the reaction between the cement components and the added water. In general, cement is used in relatively water-poor, plastic mixtures with water-cement values between about 0.3 and 0.6. The reaction is called hydration, the reaction products are called hydrates or hydrate phases. One consequence of the reactions that start immediately is a stiffening of the cement paste, which is still very slight at the beginning, but increases over time. If the setting of the cement paste reaches a certain level, one speaks of the start of setting . The subsequent further solidification of the cement paste is considered to be solidification, the subsequent solidification is called hardening .
The cause of stiffening, solidification and hardening is the formation of a more or less rigid structure of hydration products that fills the water-filled space between the solid particles of the cement paste, mortar or concrete. The time course, but not the type of hydration products, therefore depends to a very large extent on the size of the gap, i.e. H. of the water-cement value. The strength-building hydration products of silicate cements are primarily calcium silicate hydrates and calcium aluminate hydrates for high-alumina cement . Further hydration products are calcium hydroxide , calcium ferrite hydrates, sulfate-containing hydrates and related compounds such as hydro garnet and gehlenite hydrate .
Silicatic cements consist of more than 70 mass% of calcium silicates or silicate components. The hydration of these compounds and the properties of the resulting calcium silicate hydrates are therefore of particular importance. Since the calcium silicate hydrates are lower in CaO than the calcium silicates in cement clinker, calcium hydroxide is also formed when the Portland cement is hydrated. All cements also contain aluminum and iron oxides as well as sulphates as essential components , which is why calcium aluminate hydrates, calcium ferrite hydrates and sulphate-containing compounds as well as more complex hydration products are formed. The pH value of the pore solution takes on comparatively high values and is of particular importance for most hydration reactions.
Shortly after contact with water, a brief, intensive hydration sets in (pre-induction period), calcium sulfates partially and alkali sulfates almost completely dissolve. The reaction of calcium and sulfate ions with tricalcium aluminate forms short, hexagonal columnar ettringite crystals on the surfaces of the clinker particles . In addition, starting from tricalcium silicate, the first calcium silicate hydrates (CSH) are formed in colloidal form. With the formation of a thin layer of hydration products on the clinker particles, this first period of hydration subsides and the period of rest or induction begins, during which virtually no further hydration takes place. The first hydration products are still too small to bridge the space between the cement particles and build up a solid structure. This means that the cement particles can still move against each other - that means that the consistency of the cement paste has only become a little stiffer. The cement paste begins to set after about one to three hours, when the first, still very fine, calcium silicate hydrate crystals form on the clinker particles. After the rest period has ended, the clinker phases begin to rehydrate intensively. This third period (acceleration period) begins after about four hours and ends after 12 to 24 hours. A basic structure is built up, consisting of CSH fiber tufts or CSH leaf structures, platy calcium hydroxide and ettringite crystals that grow in length. The spaces between the cement particles are bridged by the larger crystals. In the further course of hydration, the solidification increases steadily, but at a reduced rate of hydration. The structure condenses and the pores are increasingly filled.
The chemical reactions of the clinker phases with the mixing water can be represented as a chemical reaction equation:
- C3S:
- C2S:
- C3A:
- C4AF:
The hydration products do not form at the same time, but according to their reactivity at different speeds and after different times. The transition from solidification to hardening takes place "fluently".
Environmental aspects
Until the 1960s, cement works were considered to be "polluters", which released a large amount of dust and exhaust gases into the environment. Although cement works still release four times as much CO 2 as global air traffic combined, environmental protection in cement production improved significantly afterwards, as more modern filter systems reduced dust emissions just as drastically as the further development of rotary kilns and firing technology reduced energy consumption and the emission of harmful exhaust gases such as sulfur dioxide (SO 2 ), carbon dioxide (CO 2 ) and nitrogen oxides (NO x ). The latter are removed from the exhaust gases using so-called “SNCR processes” ( selective non-catalytic reduction ).
Particular attention is paid to the emission of volatile trace elements and heavy metals such as mercury , cadmium or thallium , while all non-volatile and non-volatile trace elements are adsorptively bound by the freshly deacidified limestone (principle of dry sorption). Soluble chromates contained in cement can trigger an allergy, so-called mason itch , whereby the high alkaline pH of the aqueous solution also contributes.
So-called secondary or substitute fuels are sometimes used to save fossil fuels such as coal , natural gas and crude oil . These alternative liquid and solid fuels such as waste oil or solvents, as well as processed household and commercial waste, car tires , animal meal , waste wood or other biomasses become harmful in the rotary kiln due to the oxidizing conditions and extremely high temperatures (flame temperature> 2,000 ° C) without any additional damage Burned exhaust gases. The emissions are subject to the standards of the EU co-incineration directive 76 / 2000EC, compliance with which the approving authorities monitor electronically. In Switzerland, these alternative fuels make up more than 50%. In all of Western Europe, efforts are also being made to bring the proportion of so-called secondary fuels in the cement works up to around 70%. This disposal option through co-incineration, also in emerging countries, is used as a tried and tested means of developing inexpensive waste disposal infrastructures and ensuring sustainable local disposal under high environmental protection standards. For more than 30 years, whole car and truck tires (without prior shredding ) have been used thermally and - because of the iron carcass - materially in the kiln inlet of the rotary kiln.
A feared emission of dioxins or furans has not yet been scientifically proven, as the high basic calcium content, the exhaust gas atmosphere and the unfavorable temperature conditions in the closed system prevent the so-called de novo synthesis .
Since a large part of the cements produced today are so-called composite cements, in which clinker is replaced to a certain extent by other additives, natural raw materials are conserved. In addition, these additives, for example blast furnace slag and fly ash, are residues and waste materials from other branches of industry. The thermal energy balance has also improved enormously through the intensive use of waste heat from the rotary kiln, for example for grinding drying and preheating the raw meal. Environmental protection guidelines and the associated statutory emission limit values have led to these factors being increasingly taken into account in modern cement works.
A problem that increases with the increasing greenhouse effect , however, is the high level of carbon dioxide emissions. The cement industry is one of the main emitters of greenhouse gases that cause global warming . Worldwide, 4.1 billion tons of cement are produced annually, which contains around 60% CaO on average. The release of the carbon dioxide bound in the lime results in emissions of at least three billion tons of CO 2 or around 6 to 8% of the annual CO 2 emissions, even with optimal process management. If the global cement industry were a country, it would be the third largest emitter in the world - after the People's Republic of China and the United States. In order to meet the requirements of the Paris Climate Agreement , the annual emissions of the cement industry would have to decrease by at least 16 percent by 2030. Accordingly, considerations are being made to produce cement using more environmentally friendly methods. There are approaches for new manufacturing processes that release significantly less CO 2 .
The extraction of raw materials for cement production leads in several cases to considerable negative consequences for the regions concerned: through the displacement of people, or through the loss of their livelihoods and through the destruction of valuable landscapes.
Processing precautions
safety instructions | ||||||||
---|---|---|---|---|---|---|---|---|
Surname |
cement |
|||||||
CAS number |
65997-15-1 |
|||||||
EC number |
266-043-4 |
|||||||
|
Under the influence of water, an alkali with a high pH value of up to 13 is formed in the cement, which can lead to severe burns and necrosis on the skin or eyes (cement burn). Since the symptoms often take hours to appear, the danger is often recognized too late. Therefore, glasses and gloves should be worn when processing cement. If clothing or gloves are soaked through the cement liquor when processing cement , they should be changed.
economic aspects
Cement industry in Germany
The cement industry in Germany is divided into 22 companies which together operate 55 cement plants. With around 7,900 employees, the German cement works produced around 32 million tonnes of cement in 2014 and achieved sales of around 2.5 billion euros. 1.2 million tons of cement were imported in 2014, mainly from neighboring European countries. At the same time, German manufacturers exported around 6.1 million tons of cement. The manufacturers' investment quota was around 6.5 percent.
consumer
The People's Republic of China has the greatest demand for cement . Around 45% of global production is built there. In the years 2012–2014, the same amount of cement was used as in the entire 20th century in the USA. Not only the construction boom in China but also the quality of the construction play a role here, as buildings are often considered to be dilapidated within a few decades.
The annual consumption of cement is an important parameter for the intensity of construction activity in a region. In countries like Indonesia , only around 15 to 20 kg per inhabitant are required annually; in countries like Singapore or the Arab countries, consumption can exceed 2,000 kg per inhabitant per year. Consumption in Germany is around 350 kg per inhabitant per year.
Producers
rank | country | Production (in million t ) |
rank | country | Production (in million t) |
---|---|---|---|---|---|
1 |
![]() |
2,400.0 | 10 |
![]() |
58.0 |
2 |
![]() |
280.0 | 11 |
![]() |
56.0 |
3 |
![]() |
86.3 | 12 |
![]() |
54.0 |
4th |
![]() |
78.0 | 13 |
![]() |
53.0 |
5 |
![]() |
77.0 | 14th |
![]() |
35.0 |
6th |
![]() |
66.0 | 15th |
![]() |
35.0 |
7th |
![]() |
63.0 | 16 |
![]() |
32.0 |
8th |
![]() |
59.0 | 17th |
![]() |
32.0 |
9 |
![]() |
58.0 | 18th |
![]() |
23.0 |
In Switzerland around 4.8 million tonnes of cement are produced annually and consumed.
literature
- Lothar Müller: Portland cement . In: Chemistry in Our Time . tape 7 , no. 1 , 1973, p. 19-24 , doi : 10.1002 / ciuz.19730070104 .
- Friedrich W. Locher: Cement: Basics of production and use. Verlag Bau + Technik, Düsseldorf 2000, ISBN 3-7640-0400-2 .
- Association of German cement works: Zement-Taschenbuch 2002, 50th edition. Verlag Bau + Technik, Düsseldorf 2002, ISBN 3-7640-0427-4 .
- Wilhelm Scholz, Wolfram Hiese: Knowledge of building materials. Werner Verlag, Cologne 2007, ISBN 978-3-8041-5227-4 .
- Georges Spicher, Hugo Marfurt, Nicolas Stoll: Nothing works without cement. History of the Swiss cement industry. NZZ Libro, Zurich 2013, ISBN 978-3-03823-835-5 .
Footnotes and individual references
- ↑ Statista: cement production by the most important countries worldwide in 2017
- ↑ Florian Riepl: The economic and technological development of the cement industry with special consideration of the merits of Hans Hauenschild . Vienna June 2008, The history of cement development from the early beginnings to the invention of Portland cement - 3.6 The development of Portland cement, p. 23 ff . ( pdf , othes.univie.ac.at - diploma thesis).
- ↑ http://www.stadtentwicklung.berlin.de/staedtebau/foerderprogramme/denkmalschutz/de/foerdervorhaben/kaskelstrasse/index.shtml
- ^ Fritz Becker : The industrialization in reinforced concrete construction . Karlsruhe: Dissertation TH Karlsruhe 1930, p. 9
- ↑ Karl-Eugen Kurrer : 100 years of standards in reinforced concrete construction , in: Beton- und Stahlbetonbau 98 (2003), no. 12, pp. 794–808, p. 795
- ↑ Cement properties - compressive strength. (No longer available online.) HeidelbergCement, archived from the original on August 8, 2013 ; accessed on July 15, 2018 .
- ↑ Celitement: Energy-efficient building materials - Binding promise to the environment ( Memento from October 20, 2012 in the Internet Archive )
- ↑ New cement protects the climate and resources: Partners sign the founding contract for Celitement GmbH. on: chemie.de , February 23, 2009.
- ^ A b Hipp, Dietmar: Short process. Der Spiegel , August 2, 2010, accessed October 11, 2013 .
- ^ Daniel Bütler: Schweizer Zementwerke: Officially approved poison slingshots. In: observer.ch . July 4, 2019, accessed August 1, 2019 .
- ↑ Chatham House Report: Making Concrete Change: Innovation in Low-carbon Cement and Concrete. Chatham House , June 13, 2018, accessed May 19, 2019 .
- ^ Mineral Commodities Summary. (PDF) USGS, accessed June 12, 2018 (English).
- ↑ Lucy Rodgers: Climate change: The massive CO2 emitter you may not know about. BBC News, December 17, 2018, accessed May 19, 2019 .
- ↑ https://www.n-tv.de/wissen/Neue-Hoffnung-fuer-Klimakiller-Beton-article21279697.html
- ↑ https://www.cleanthinking.de/zement-ohne-klinker-franzoesisches-startup-mit-bahnbrechender-technologie/
- ↑ Indigenous Community Sedulur Sikep and their fight against HeidelbergCement honored with human rights award. Retrieved November 15, 2019 .
- ↑ Anett Keller: Environmental Destruction in Indonesia: Farmers Against Cement Works . In: The daily newspaper: taz . December 17, 2012, ISSN 0931-9085 ( taz.de [accessed November 15, 2019]).
- ↑ a b Entry on cement in the GESTIS substance database of the IFA , accessed on March 28, 2019 (JavaScript required)
- ↑ Cement firing: After the screed, to the dermatology clinic. In: Doctors newspaper online. August 28, 2012, accessed April 19, 2015 .
- ↑ Health risks for do-it-yourselfers. (No longer available online.) ERGO Insurance Group , March 20, 2013, archived from the original on February 4, 2015 ; accessed on July 15, 2018 .
- ↑ Figures and data - Cement Industry in Germany 2015. Association of German Cement Works , June 8, 2015, accessed on June 8, 2015 .
- ↑ Global cement production top countries 2017 | Statistic. Retrieved July 2, 2018 .
- ↑ Erich Aschwanden: Cement: Federal Council wants to know how big reserves are. In: nzz.ch . January 18, 2020, accessed January 20, 2020 .
See also
Web links
- Cements and their production (PDF file; 309 kB)
- Zement-Taschenbuch, 50th edition 2002 (PDF file; 7.3 MB)
- Initiative for sustainability in the German cement industry
- Virtual cement factory
- German cement museum in Hemmoor an der Oste
- The development of German cement , Der Architekt , 1895