Terrazzo
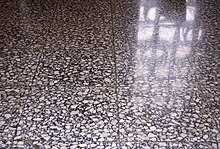
Terrazzo is the name of a floor covering that has been known since ancient times , which by directly applying decorative, often colored aggregates to a mostly cement-bonded screed base, forms a unit with it and, after drying, by sanding and polishing its final, shiny surface receives.
The manufacture of terrazzo floors in Germany is regulated by DIN 18353.
"Terrazzo plates" is a colloquial term for concrete stones that made the format plate with finished ground surface in plants and on site as a whole or in accordance with the conditions circumcised in a mortar bed to be laid. This rational way of producing a terrazzo floor is the most common today.
To distinguish it and to make it clearer, a terrazzo that is traditionally produced "on site", i.e. seamlessly poured, as it was common until the middle of the 20th century, is called "Ortsterrazzo", colloquially also called "Cast Terrazzo".
history


Terrazzo floors already existed in Greek and Roman antiquity , possibly even earlier. This type of flooring flourished during the Roman Empire . Terrazzo floors were used universally in some regions. They were found in excellent artistic execution as well as in simple design in the towns and villages as well as in the country estates of the provinces. In addition, the Roman army also relied on the durability of this floor covering and sometimes even used it in small military posts along the borders.
The aggregates almost always consisted of marble , limestone , dolomite etc. However, harder materials such as granite chippings , moraine or river gravel were also used in the past for heavily loaded soils . A renewed flourished terrazzo in Italy of the Renaissance , as exemplified in the palaces of Venice . In Italy it was previously called “composto terrazzo marmorino”. Today terrazzo is generally called "Terrazzo alla veneziana" because it was often historically built in the area of Venice and Trieste .
Terrazzo once again found its way into Central Europe through the construction of churches in the Mediterranean region and over time it was also used in other public buildings as a resilient, functional and decorative element.
Terrazzo floors were most widespread in the founding period and around the turn of the century , not only in residential buildings, but also in public buildings such as churches and train stations. Different colored surfaces were often combined with each other and ornaments or inscriptions made of mosaic stones were also inserted. In contrast, later floors were designed in a single color, but in the first half of the 20th century they were often used in high- traffic areas of residential construction, for example in stairwells, kitchens and bathrooms. During the post-war German reconstruction , terrazzo floors were very often laid, but now also in the form of so-called "terrazzo panels". Terrazzo was not only used for flat floor surfaces, but also for stairs that were either poured or built from finished terrazzo steps. Sinks and table tops were also made from the decorative material.
From the 1960s, cheaper, industrially manufactured products such as ceramic tiles , carpeting and PVC increasingly pushed terrazzo floors out of the mass market. In some places existing terrazzo floors were even covered with "modern" coverings, also because the knowledge about the possibility of repairing damage had been lost. More recently, terrazzo has been rediscovered for high quality living areas. By using purely mineral substances, there is no risk of vapors. In many historical buildings, terrazzo floors are still preserved and in good condition, which proves their durability.
However, surfaces that are damaged or later covered with other coverings can also be restored. For example, residues of glue and mortar, such as those found in e.g. B. left behind by glued PVC floors or tiles, sanded and the surface re-polished. The addition of imperfections requires a certain amount of experience, as the correct selection of colors and additives must ensure that the old covering looks as precisely as possible. With the appropriate knowledge, however, it is quite possible to inconspicuously add even large imperfections or to create new floor areas to match the existing ones, as is the case with B. may be necessary when changing the floor plan of a building. Apart from the requirements of the monument protection, the great durability, easy maintenance and the appearance of terrazzo, which is appreciated again today, make the repair appear worthwhile.
properties
Terrazzo usually has advantages over other coverings in terms of load-bearing capacity , usability and, above all, service life . It consists of mineral materials, hardly absorbs water and the visible top layer is relatively thick. The choice of material influences hardness and resistance in individual cases. In addition, there is - similar to solid parquet - the option of refurbishing the surface by sanding and polishing.
Manufacturing
Traditionally, terrazzo is dry mixed on site from binding agents and aggregates (mostly from 5 mm grain size), mixed with water and hydraulic lime or cement . The color of the floor can be influenced by adding pigments and different colored additives .
Stone powder , sand and gravel or chippings with grain sizes up to 8 or 16 mm are used as aggregates . Rock powder in particular also influences the color of the matrix, while coarser aggregates of different colors become visible as dots after grinding. In the past, soft aggregates such as crushed sand and chippings from limestone were mostly used to simplify the grinding of the floor.
Earlier terrazzo was generally considered topping applied directly to the substrate. Today terrazzo floors are also laid on thermal and impact sound insulation as well as on underfloor heating and are also offered as prefabricated panels that are laid like floor tiles .
In the case of more elaborately worked floors, further granulates can then be sprinkled on the homogeneous surface or mosaic stones can be added. The applied layer is compacted with rollers . By grinding, the grains of the aggregates become visible and thus determine the appearance of the floor.
A setting and resting time is required before the first sanding. In the past, air lime was sometimes used as a binding agent, which meant that it could take more than six months for it to fully harden .
Before the final treatment of the surface, indentations and imperfections can be leveled out with filler . To refine and strengthen the gloss effect, additional fillings and sanding are possible.
Terrazzo floors can be made electrically conductive by adding corrosion-resistant metal chips or adding graphite . This method is used nowadays in operating theaters, for example, to avoid electrostatic charges. The charge is dissipated through an integrated, earthed metal mesh mat.
Bituminous terrazzo
As with mastic asphalt , hard bitumen can also be used as a binding agent instead of lime and cement . Thanks to the plasticity and tensile strength of bitumen, the thickness of the terrazzo layer can often be reduced to 3 to 4 centimeters, even on elastic intermediate layers. Depending on the aggregate, mastic asphalt is waterproof and practically gas and water vapor tight. Since bitumen-bound screed is poured in liquid form at a temperature of approx. 240 ° C, adjacent components or built-in parts must be correspondingly temperature-resistant. After about four hours the screed has cooled down enough to be walked on. Mastic asphalt can also be laid seamlessly in large areas with integrated underfloor heating (as long as no structural joints need to be taken into account).
Mastic asphalt is insensitive to smoldering tobacco products, welding sparks and the like and can be briefly exposed to boiling water.
Mastic asphalt screed is usually produced with hardness class IC 10 for rooms with a constant room temperature of approx. 20 ° C. In rooms with temperatures below 5 ° C, the mastic asphalt screed should be adjusted accordingly softer. The penetration depth for a mastic asphalt screed of hardness class IC 10 at room temperature of 20 ° C under standardized load and defined test conditions is 10/10 mm. An IC 40, i.e. a softer set mastic asphalt , has a penetration depth of 40/10 mm.
Due to the plastic behavior of static loads, the contact areas are to be selected so that - depending on the hardness class - at room temperatures no surface pressures higher than 0.5 to 1.0 N / mm² occur. If necessary, punctiform loads are to be distributed over a larger area by placing slabs underneath. Floating mastic asphalt screeds, the permissible traffic load also depends on the load-bearing capacity of the insulation layer.
The improvement in footfall sound insulation is 14 dB for an approx. 3 cm thick mastic asphalt screed on the separating layer. Mastic asphalt has good internal damping properties. Its loss factor h for sound waves passing through is 0.18 at room temperature (concrete: 0.0063); the noise reduction reaches 3%.
The coefficient of thermal conductivity of 0.7 to 0.9 W / (m * K) is significantly lower than, for example, concrete with 2.10 W / (m * K). The bulk density is usually around 2.5 to / cbm. The fire behavior corresponds to building material class B1.
Surface treatment
One of the main criteria for choosing maintenance methods is the subsurface.
Classic methods
In ancient times, ground terrazzo floors were rubbed with a mixture of turpentine and beeswax . Turpentine or Canada balsam is obtained from fresh tree resin . After cutting the bark, the leaked resin was collected and roughly cleaned. Purified beeswax was then heated until a viscous mass was formed. This wax was slowly stirred into the turpentine until a pasty mass was formed, which cooled in closed vessels. This paste was applied to the floor several times by hand until it was saturated. This led to an intensification of the color of the floor, which after polishing with a brush had a silk-matt shine. This type of maintenance is often used in listed buildings.
Those who could n't afford expensive turpentine turned to linseed oil . It penetrates deeper into the pores. The terrazzo was soaked in the linseed oil until it did not absorb anything and the pores were "tight". The linseed oil polymerized and hardened. It was then repolished. Linseed oil can fade, so the color may change depending on the sunlight. To reduce this effect, the linseed oil had previously been spread out and exposed to sunlight for months, which led to thickening and bleaching. Then turpentine was added again as a solvent and the layer was applied as described. As with waxes, a stain-free basic cleaning can hardly be achieved. Maintenance cleaning can be used as before after hardening with wax-based agents.
Both of the aforementioned methods are still in use today, but are relatively expensive and can only be used for composite structures that have dried out. The odor nuisance should not be underestimated either. Although turpentine is of natural origin, it is still a harmful solvent.
Floors that are cared for in the classic way are best cleaned with a waxy cleaning agent, which can maintain and, under certain circumstances, even increase slip resistance when wet. The floor must then be polished up regularly with a dry natural bristle. On the other hand, polymer mop care products or alcohol cleaners usually lead to the formation of a fog and thus endanger the slip resistance in wet conditions. Basic cleaning of these old coverings is also problematic because old waxes cannot be removed from the pore spaces, even with highly alkaline products, and undesirable staining is possible.
industrialization
The electric grinding machines made terrazzo floors more and more popular and were no longer only used in upscale areas. The classic maintenance methods were usually too expensive and were simply cleaned with soap and brushed on after installation. In the ready-to-use soapy water, the minerals in the water create, among other things, poorly soluble compounds, which are also known as the "edge" of the sink. These "lime soaps" are soft and easy to polish up to a silky shine. In the past, an iron polishing block was used to polish the floor. The disadvantage of the soap is the permanent layering and a natural graying of the deposits. These disadvantages can be offset by regular thorough cleaning.
Post-war until today
In the time of the economic miracle , hard polymers were also applied to the floor, but they are very difficult to remove and not to be confused with soap. There are many known cases in which a thick layer of “gloss” had to be removed with a spatula before the terrazzo could be sanded. The abrasive would be added without removing this layer immediately. Normal floor cleaning can usually not improve the appearance, because soap generally smears on it.
In the 1950s and 1960s, it was a common method to clean the sanded floor with dilute acid and then soak it in with a wax fluid. The own production of the wax fluid by the terrazzo processors was hazardous to health if wax candles were dissolved cold in toxic trichlorethylene . Solvent-based wood care products often help to carry out thorough cleaning and post-processing. But even in these cases it is necessary to discuss the risks (smoothness, solvents , stains) with the client and record them in writing.
After the terrazzo was considered to be of inferior quality in post-war Germany, it has become more and more popular in recent years, also because of more modern substructures, through which no moisture can be drained "downwards". The surfaces have also changed. The trend is moving from the originally matt version to high gloss.
There are several approaches to "modern" maintenance in private areas, depending on the substructure. In general, the terrazzo should be completely dry before further treatment in order to avoid secondary damage. In addition, too early treatment can significantly change the hydration and carbonation of the surface, which can lead to increased abrasion or a blotchy "tiger skin look". In commercial properties, maintenance measures can lead to a drastic deterioration in the set slip resistance , which is why this should be clarified beforehand with the client and the responsible authorities.
Impregnate
On an absolutely dry and clean surface, z. B. a water-soluble stain protection can be applied according to the manufacturer's instructions. The advantage of this system is the easy removal of excess agents and the solvent-free composition. In most cases, this basic protection is fully effective after around three days, during which it should only be dry cleaned. A surface treated in this way can only be cleaned to a limited extent with classic soapy water. Due to the inadequate chaining of the care components to an impregnated surface, it is hardly possible to cover the signs of use. In this case, a residue-free cleaning system would be better. The dosage usually has to be set higher than for non-impregnated surfaces. The reason is the hydrophobic property of the impregnates. The sensitivity to stains decreases and the adhesion of dirt increases, especially with organic dirt such as soot from rubber soles.
Soap
Using a soap cleaner alone from day one is the safest method and can also be used on slightly damp floors. The disadvantage is that it can take a long time for an effective care film to form. Natural soap reacts with the hardness of the water. The softer the water, the longer it takes for a protective film to form.
To grow
The use of so-called “wax fluates” is still often used today and is not without its risks and disadvantages. The solvents alone , depending on the manufacturer, can trigger severe allergies . Uneven application of the wax fluates can lead to staining. Every cleaning professional knows the problem of so-called "streaking" caused by shoes on a waxed surface. Proper cleaning and care is only possible with solvent-based products that are also used on waxed parquet. Soaps or polymer wipes usually leave streaks on a waxed surface. This method is not recommended over underfloor heating .
Wet crystallization
Instead of fluorosilicate, “ clover salt ” is usually used as a polishing agent. This “salt”, which was used as a polishing agent in the past, forms a thin, shiny layer of calcium oxalates on the surface . It is also the standard method for polishing limestone and marble .
Coating
From building cleaning there is a large number of pore fillers and care products based on soft polymers that can be used as care products . As with soap, the advantage of these agents is that they are easy to remove. Disadvantages include the lower resistance to alcohol , which is found in glass cleaners, or the alkalis still present in the floor , which can attack the coating.
Fluorosilicate treatment with fluosilicate
In order to achieve a high-gloss surface, the soil can be "crystallized" after it has completely dried out. Using the classical crystallization procedure with ( Magnesiumhexa -) fluoro silicate a more closed normally and shinier surface can be achieved by in a pre-ground terrazzo with calcareous aggregates chemical reaction generated between the crystallization agent and the rock. In this process, the water-insoluble magnesium fluoride , calcium fluoride , silicate gel (no large quartz crystals) and the volatile carbon dioxide are formed according to the reaction equation:
MgSiF 6 + 2 CaCO 3 MgF 2 + 2 CaF 2 + SiO 2 + 2 CO 2
The resulting surface is composed of calcium fluoride (CaF 2 ), magnesium fluoride (MgF 2 ) and embedded quartz (SiO 2 ) and is usually slightly water-permeable. The achievable layer thickness varies greatly depending on the rock and care taken (max. 50 µm). This is done in combination with a machine heat supply with special pads made of stainless steel or plastic. The process does not work with hard stone, dolomite or dolomite marble aggregates. This procedure does not offer any basic protection. Careful cleaning usually leads to cleaning streaks.
literature
- Olivo Andream, Pim WA Metman: Het terrazzoboek. Vereniging Terrazzo en Vloerenbedrijven, The Hague, Netherlands 1989, ISBN 90-71860-01-9 .
- PK Balatjew: Concrete, tile and terrazzo work. Fachbuchverlag Leipzig, Leipzig 1954.
- Antonio Crovato: The Venetian Terrazzo orig. Title: I pavimenti alla veneziana . Edizioni Grafi, Resana (Treviso) Italy 2002, ISBN 88-900419-0-0 .
- Professional Association for Concrete Products and Related Industries for the State of Hessen V. (Ed.): Concrete stone. Wiesbaden 1955.
- Herbert Fahrenkrog: Natural stone in everyday life. Munich 2007, ISBN 978-3-7667-1729-0 .
- Association of the Federal College for Concrete Workers at the Ferdinand-von-Steinbeis-Schule e. V. (Hrsg.): Meisterklasse.Betonwerkstein.Info. Ulm 2008.
- AD Hellmuth Friesen: Concrete stone as a material and construction element in modern construction. Erasmus print Max Krause, Mainz 1956.
- Hans Issel: artificial stone u. Mortar industry. Your latest products by machine production on floor and wall panels, bricks, hollow blocks, steps, roof tiles, pipes and posts. The mortar mix ratios as well as the type of regenerative aggregates; in addition, the mortar calculation according to mass and cost expenditure. Published by Bernhard Friedrich Voigt, Leipzig 1922.
- Sigmund Lehner: The artificial stones. A description of the representation of artificial stone masses, the raw materials, devices and machines. A. Hartleben's publishing house , Vienna / Leipzig 1927.
- Karl Müller: Artificial stone construction, silent teacher for the entire artificial stone industry . Gommern 1905. (New edition: Reprint-Verlag-Leipzig, Holzminden 2003, ISBN 3-8262-1314-9 )
- Doretta Davanzo Poli: Applied & Decorative Art in Venice orig. Title: Le Arti Decorative a Venezia. Könemann Verlagsgesellschaft, Cologne 1999, ISBN 3-8290-2185-2 , pp. 58–73.
- Erich Probst: Handbook of the concrete block industry. Carl Marhold publishing house, Halle / Saale 1951.
- HF Rodlich: Practical instructions for the production of Venetian screeds. CH Platen, Berlin 1810.
- Robert Scherer: The artificial floor and wall coverings and ceiling coverings. With a detailed description of the production of stone wood (xylolite), linoleum, artificial marble and stucco. A. Hartleben's publishing house , Vienna / Leipzig 1922.
Further literature on the Fraunhofer Information Center for Space and Construction .
Web links
material archive: Terrazzo (lime) - extensive material information and images
Individual evidence
- ↑ DIN 18353 at the German Institute for Standardization e. V. accessed on October 25, 2011.
- ↑ DIN 18353 at www.baunormenlexikon.de, accessed on October 25, 2011.
- ^ History of Terrazzo ( Memento from September 14, 2017 in the Internet Archive ), accessed on February 4, 2020.
- ↑ Terrazzo from the Stone Age. In: The time . July 26, 1985, accessed on October 26, 2011 in the Zeit print archive.
- ^ Carl Friedrich von Wiebeking: Theoretical-practical bourgeois building history: Report and description enriched by history of the most remarkable architectural monuments and their precise description. Volume 4, Munich 1826 (online on Googlebooks)
- ↑ In Germany, terrazzo has been offered as Terrazzo alla Veneziana for marketing reasons for some time , although it is often an epoxy resin bonded compound .
- ↑ Plastics are advancing further. In: The time . May 17, 1956, accessed in the print archive of the time on October 26, 2011.
- ↑ a b c d e f Technical properties and material characteristics BituTerrazzo - Bitu-Terrazzo Verband e. V. , accessed on February 1, 2020.