ignition coil
The ignition coil is a component of the ignition system of a gasoline engine or a gas firing system. The structure corresponds to a transformer .
Basics

Ignition coils work like a spark inductor . When the ignition is switched on, current flows through the primary winding of the ignition coil, creating a magnetic field around the coil. This magnetic field is also transferred to the secondary winding through the common iron core of both windings. Opening the breaker in the primary circuit of the ignition coil induces a high-voltage pulse in the secondary circuit as the magnetic field collapses quickly. The high voltage passes through the ignition cable to the spark gap of a spark plug , for example in order to ignite the fuel-air mixture in the cylinder of a gasoline engine at the right time.
In Otto engines, it is used, together with the interrupter (now mostly electronic) and the capacitor connected in parallel to the interrupter, to generate a high voltage of approx. 15,000 to 30,000 V from the on-board 12 V voltage.
The capacitor parallel to the contact is intended on the one hand to reduce the formation of sparks at the interrupter contacts (increased burn-off) and on the other hand to form an oscillating circuit with the primary coil that has the same resonance frequency as the secondary coil. In this way, the energy transfer from the primary to the secondary circuit is optimized. With conventional ignition coils, the optimum is often 220 nF.
Ignition coils in gasoline engines
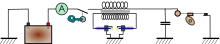
Vehicle ignition coils have three connections: The primary circuit receives voltage from the ignition lock at terminal 15 (DIN 72572) of the ignition coil, runs through the primary winding and the ignition interrupter (ignition contact) connected to terminal 1 to ground . The high voltage of the secondary circuit taken from terminal 4 is conducted via the ignition distributor to the spark plugs, which re-establish the connection to earth via the spark gap. Occasionally, ignition coils with 4 connections are also used: In addition to terminals 1 and 15 for the primary winding, the ground of the secondary winding is connected separately to terminal 4a. In order to prevent undesired misfire by switching on the magnetic field (single spark coil), a series connection of cascade diodes is installed on the secondary side . Together they achieve a reverse voltage of approx. 2000–5000 volts. However, this circuit makes a resistance test on the secondary side with commercially available measuring devices impossible (measurement result: open line).
In ignition coils for systems with wasted spark , the two ends of the secondary winding for one spark plug each are led to the outside, so they are not autotransformers but each have a separate primary and secondary winding.
To retrofit older vehicles, ignition coils with a higher secondary voltage are also available in stores. These usually have to be operated with a series resistor in order to avoid thermal overload. The series resistor can be bridged with the starter relay in order to compensate for the voltage drop in the on-board network during the starting phase.
In training for automotive electrician was into it taught until the 1970s nor the expensive (up) winding coils - a method that is easy to exchange through today's practice, such products has become superfluous, but in the restoration of classic cars is still practiced.
Fully electronic ignition (VEZ) with its "static ignition distribution" is mostly used in newer vehicles : an ignition module with its own ignition coil is located above each spark plug. This increases the reliability, since only one cylinder fails in the event of a fault. The complex ignition distributor with its mechanics is no longer necessary, as is the susceptible high-voltage cables. Since sparkover only occurs in the spark plug, radio interference is also kept to a minimum.
Developmental and functional features
Since the introduction of the Otto engine, ignition coils operating with mechanical breakers have been in use for around a century. However, the most recently produced technical versions could only be designed for contact or primary currents between 4 and 5 A. As a result, the ignition energy supplied to the spark plug, which is dependent on the main inductance of the ignition coil, its transmission ratio, the ohmic components in the secondary circuit (interference suppression), and in particular the engine speed and number of cylinders to be supplied, is limited to approx. 5 to 35 mJ . On the other hand, transistor-switched ignition coils can run significantly higher primary currents. Due to the increase in the glow discharge current made possible in this way, the ignition spark energy currently achieved in large-scale production is between approx. 50 and 100 mJ, with the ignition coil main inductance acting as a power source in the area of the glow discharge.
The high-voltage capacitor ignition, which was used for the original equipment of road vehicles (Porsche) until the 1980s, also provided a comparably high ignition energy compared to contact-controlled ignition systems, but with a significantly larger ignition voltage reserve and a considerably shorter voltage rise time, with the ignition coil essentially acting as an energy transmitter after reaching the ignition voltage serves. However, the spark service life, which is also determined by the capacitance of the primary circuit capacitor C, is not dependent on the main inductance of the ignition coil, but - because it is actually short-circuited by its leakage inductance - on this as well as on the overall effective ignition coil and interference suppression resistors, the latter not being one convert an insignificant part of the energy made available by the primary circuit capacitor into heat. The resulting significantly shorter spark duration per arc discharge is, on the one hand, more advantageous in terms of plasma physics than the glow discharge; on the other hand, the influence and effectiveness of a sufficiently high and long glow discharge current for igniting lean and / or inhomogeneous ignition mixtures must by no means be ignored. At present, passenger car gasoline engines manufactured in Europe and the USA are almost always equipped with fully electronic ignition controls in conjunction with individual cylinder ignition coils. As the illustrated exemplary embodiment for a 6-cylinder engine shows, the digital engine electronics ( DME , DCU for Digital Control Unit ) evaluate the level and timing of the spark current on a cylinder-specific basis and - among other things - as a parameter for the control or switching time of the Primary current of the ignition coil used.
Instead of a pre-spark gap built into the ignition coil, a high-voltage diode is usually used. This also prevents or shuts off the voltage induced on the spark plugs in the secondary circuit when the primary current is switched on - a few milliseconds before the ignition point - so that a possible sparkover on the spark plug electrodes under certain engine operating conditions is definitely excluded.
ISO 6518
In ISO 6518-1 (as of June 2002), chapter 4 contains technologically different types of ignition coils for ignition systems in road vehicles. This definition paper also specifies influences that can lead to uncontrolled ignition processes (Section 7). The related ISO 6518-2 (correction status September 1997) already refers in its introductory part (area of validity or scope ) to two methodological approaches to counter the problem of insufficient reproducibility of information on the output energy of ignition systems. While method A refers to the use of spark gaps (Section 5.3.1), which also includes high-voltage capacitor ignition, method B recommends replacing a spark gap with a zener diode as an alternative and explicitly for comparison measurements on and for ignition coils.
To determine the maximum high-voltage supply, ISO 6518-2 specifies, among other things, equivalent circuits for different load cases of an ignition coil: A spark plug connected directly to the high-voltage output, as is the case with ignition coils for spark plug well assembly, is switched by connecting a 1 MΩ resistor in parallel with a Simulated capacitor of 25 pF. With an ignition lead between these components, the value of this capacitor should be 50 pF.
Spark duration and energy of the glow discharge
After the ignition voltage on the spark plug electrodes has built up the field for the streamer charge developing in the so-called predischarge phase in less than a nanosecond, the breakdown phase takes place in the single-digit nanosecond range with a capacitive energy of usually approx . 1 mJ. In this discharge form a running microsecond arc (follows Arc phase ), which is also about 1 mJ in series technical ignition systems. This process, which is essentially formed from the discharge of the capacitive components in the high-voltage circuit, then changes into a glow discharge . Despite its comparatively highest proportion of thermal loss for the electrode area, this form of discharge has the significantly largest proportion of spark energy for the ignition of the mixture in conventional ignition systems based on TSZ. The current curve of the glow discharge in the case of interrupter and transistor-switched ignition coils is largely determined by the time behavior of the spark voltage as well as the inductive and ohmic values effective in the secondary circuit - those of the ignition coil and interference suppression resistors. In conventional contact-switched coil ignition systems, the glow discharge current is superimposed by a balancing oscillation, which is essentially co-determined by its mandatory primary circuit capacitor, which, in principle, does not affect the overall energy balance, but in the case of a transistor-controlled ignition coil - in the interests of a short high voltage rise time - kept as low as possible and here by the Switching transistor or its damper diode is largely suppressed.

Under engine operating conditions, the spark voltage is essentially dependent on the electrode gap and compression ratio, cylinder filling and ignition angle. A practical mean value for the measurement data and comparative evaluation of ignition coils is given by ISO 6518-2 with a constant voltage of 1 kV, which is to be simulated with a Zener diode line at its high-voltage outputs. This voltage can also be assumed to be a representative value on the basis of oscillogram analyzes on engines between idling and partial load operation, whereby in ignition systems with mechanical high-voltage distributors an implicitly measured voltage drop due to the interference suppression resistors on the cylinder side must be taken into account. For the time curve of the spark current, there follows an initially more or less curved sloping and essentially horizontal running voltage line. For load change processes or under turbulent mixture conditions in the electrode area, however, this burning voltage characteristic, also known as "spark tail" in the jargon of oscillogram analysis, can no longer be reliably quantified.
In the case of a breaker-contact and transistor-switched ignition coil, the drop in the discharge current is determined by the time constant . Since the energy flowing out of the inductance is not only consumed in the total ohmic resistance, but also in the burning voltage source fed by it, the exponentially decreasing current is prematurely terminated at time t F , when the current reaches zero and the glow discharge is irreversibly terminated is. The continuity of the course of time beyond this point in time, determined by the time constant - i.e. H. following the red curve - could only be maintained under the condition that an amount of current the size would subsequently feed this circle. In this case, only its ohmic resistance would have to be set for the discharge of the inductance, corresponding to the coil current curve during the switch-off process , whereby the instantaneous value for the time t F appears defined as follows:
This approach can be demonstrated, for example, with the Laplace transform . The circulation equation applies
As a Laplace transformation
or with
or rewritten
or for the inverse transformation
With the function pair equivalents
is
- (Compare above!)
The spark duration follows by setting to zero
The spark energy of glow discharge is fundamental
or in our case with and with regard to ISO 6518-2 (size definition according to method B )
or explicitly
At the point in time , the capacitive component parts in and on the ignition coil still carry the voltage , which results in a compensatory oscillation which is not relevant to the spark energy balance and which usually decays periodically.
Energy balances from the comparison of capacitive and inductive ignition systems
In contrast to inductive energy storage, in high-voltage capacitor ignition the storage capacitor connected to the ignition transformer with a direct voltage of several hundred volts and only the leakage inductance of the inductive transformer are responsible for the basic functional principle. The spark duration of the arc discharge occurring here is essentially determined by these two components in the form of a damped periodic oscillation, the period duration of which is dependent on the effective total capacitance in the primary and secondary circuit and, if applicable, on the real resistances contained therein (interference suppression of the high-voltage circuit). Accordingly, the spark current basically tends to have a sinusoidal curve, although after its first zero crossing the spark gap for reversing the charge carrier direction can hardly be maintained. In the partially modified series-production systems, the spark duration is between approx. 0.02 and 0.2 milliseconds.
According to ISO 6518-2, measuring method method A (without interference suppression resistor), two investigated high-voltage capacitor ignitions with the control units Bosch 0227300003 and 0227300004 in connection with the ignition coils 0221121005 and 0221121008 with an energy supplied on the input side between 148 mJ and 58 mJ deliver an ignition spark energy of at most approx. 3 mJ, whereby the approximately 50% thermal and radiation-relevant losses for the arc discharge in the electrode area are not taken into account here. With the DME and TSZ ignition coils shown in the diagram, the energy from their primary circuits is of the same order of magnitude (137 mJ red , 84 mJ blue ). After deducting plasma-physical losses of 70% here, effectively effective amounts of energy of 24 mJ (red) and approx. 14 mJ (blue) follow.
Characteristics of some ignition coils
Type designation | L 1 [mH] | L 2 [H] | R 1 [Ω] | R 2 [kΩ] | ü [n 2 : n 1 ] | C 2 [pF] |
---|---|---|---|---|---|---|
Bosch 0221122001 (TSZ) Bosch 0221122010 (TSZ) series resistors 0.4 Ω + 0.6 Ω |
2.8 | 71 | 0.4 | 9.3 | 160 | 23 |
Bosch 0221122005 (TSZ) series resistors 0.4 Ω + 0.6 Ω |
6.1 | 71 | 1.35 | 8.9 | 110 | 30th |
Bosch 0221122009 (TSZ) series resistors 0.4 Ω + 0.6 Ω only for control units without primary current control |
8.2 | 30th | 1.15 | 7.2 | 60 | 25th |
Bosch 0221118307 (EZ / TSZ) | 5.5 | 50 | 0.55 | 10.0 | 95 | 32 |
Bosch 0221118319 (TSZ) | 6.0 | 38 | 0.83 | 7.5 | 80 | 28 |
Bosch 0221118329 (EZ / TSZ) | 4.5 | 45 | 0.35 | 9.4 | 100 | 22nd |
Bosch 0221118335 Motronic ML 1.3 |
3.5 | 35 | 0.50 | 6.0 | 100 | 34 |
Bosch 0221119030 "KW12V" series resistor 1.8 Ω |
6.1 | 71 | 1.35 | 8.9 | 110 | 30th |
Bosch 0221119035 "K12V" | 9.7 | 62 | 3.1 | 11.3 | 80 | 22nd |
Bosch 0221504004 DME, single cylinder ignition coil |
4.5 | 36 | 0.3 | 4.0 | 90 | 12 |
Bosch 0221121005 (HKZ) L 2σ = 0.5 H |
0.38 | 3.8 | 0.1 | 0.46 | 100 | <3 |
Delco Remy DR502 series resistor 1.6–1.8 Ω |
6.3 | 63 | 1.3 | 5.8 | 100 | 14th |
EZ: "Electronic ignition system" DME: "Digital engine electronics" HKZ: "High-voltage capacitor ignition" TSZ: "Transistor coil ignition" Measuring equipment: PeakTech 2170 (RLC), Belco BR-8 ( g), measuring temperature 23 ° C. C 2 also referred to as "operating capacity". |
The strikingly high gear ratio of the first transistor ignition coil mass-produced by Bosch is explained by its initial use in conjunction with germanium switching transistors. Their permissible collector-emitter reverse voltage, which in this case determines the ignition voltage reserve, is considerably below the order of magnitude of silicon transistors currently in use.
The power-related coupling factor between the primary and secondary side, which must be observed in particular for a current transformation with as little loss as possible, is approx. 0.9 for ignition coils in traditional cylinder design. Designs with a sheath core allow coupling factors of around 0.96.
literature
- Rudolf Hüppen, Dieter Korp: Car electrics all types. Motorbuchverlag, Stuttgart 1968, ISBN 3-87943-059-4 .
- Jürgen Kasedorf, Richard Koch: Service primer for vehicle electrics. 14th, revised edition. Vogel Buchverlag, 2001, ISBN 3-8023-1881-1 .
- Karl-Heinz Dietsche, Thomas Jäger, Robert Bosch GmbH: Automotive pocket book. 25th edition. Friedr. Vieweg & Sohn Verlag, Wiesbaden 2003, ISBN 3-528-23876-3 .
Web links
Individual evidence
- ↑ Bosch Technical Reports. 1, No. 5, 1966, pp. 256-264.
- ↑ G. Söhner, H. Splitter: Conventional and electronic ignition systems. In: Electronics. 8, 1966, pp. 235-238.
- ↑ Archived copy ( memento of the original from June 12, 2015 in the Internet Archive ) Info: The archive link was inserted automatically and has not yet been checked. Please check the original and archive link according to the instructions and then remove this notice. accessed on June 11, 2015.
- ↑ Bosch Technical Reports. 1, No. 6, 1966, pp. 297-304, see p. 304 (4.1).
- ↑ H. Bertling, H. Schwarz: Requirements for ignition systems for igniting lean ignition mixtures. In: Automobiltechnische Zeitschrift. (ATZ) 80, 4, 1978, p. 157 (3.1).
- ↑ New knowledge about electrical ignition sparks and their suitability for igniting flammable mixtures. In: automotive industry. 4/77 & 3/78.
- ↑ Edward M. Bazelyan, Yuri P. Raizer: Spark Discharge. CRC Press LLC, 1998, for terminology p. 162.
- ↑ Colin R. Ferguson, Allan T. Kirkpatrick: Internal Combustion Engines: Applied Thermosciences. 3. Edition. John Wiley & Sons, 2015, ISBN 978-1-118-53331-4 , p. 198.
- ^ Richard van Basshuysen, Fred Schäfer (ed.): Handbook internal combustion engine. Springer Fachmedien, Wiesbaden 2015, p. 617.
- ↑ New knowledge about electrical ignition sparks and their suitability for igniting flammable mixtures. In: automotive industry. 4/77, p. 49. Richard van Basshuysen, Fred Schäfer (Hrsg.): Handbuch Internal Combustion Engine rightly complements the comparison and reference to series-technical ignition systems based on TSZ which are methodically omitted here . Springer Fachmedien, Wiesbaden 2015, pp. 617–618.
- ↑ M. Schäfer: The ignition spark. Dissertation. Institute for Physical Electronics, University of Stuttgart 1997.
- ↑ Bosch Technical Reports: Battery Ignition (SZ). 1st edition. 1976, p. 11.
-
↑ Assuming a constant operating voltage over time, Rolf Badenhausen's calculation method , but only with an exponential equation (without Laplace transformation), comes to the same result:
Rolf Badenhausen: "AutoScreen": Evaluation of oscillograms and measurement results in engine diagnostics . Spark Basics section . In: Elrad, edition 10/90 (pp. 94–95) - ↑ z. B. Bosch Technical Reports: Battery Ignition (SZ). 1st edition. 1976.
- ↑ Influence of electrical ignition on operating behavior and exhaust gas composition in gasoline engines. In: MTZ. 33, 1972, pp. 408-409.
- ↑ New knowledge about electrical ignition sparks and their suitability for igniting flammable mixtures. In: automotive industry. 4/77, p. 49.