Fatigue fracture
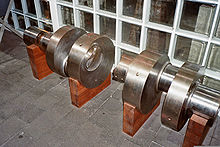

to a cast aluminum - bicycle crank ;
light: force or brittle fracture

The zones of the break can be seen in the fracture surface: left a crack that has existed for a long time (dark); towards the middle the area of the fatigue fracture progressing under alternating load with stop lines, from the right another fatigue fracture zone, in between the narrow force fracture zone
As a fatigue fracture , also known as fatigue failure or colloquially as permanent or fatigue fracture , is called the break under load cycling. Most of all breaks in mechanical engineering can be traced back to fatigue fractures. The fatigue of the component, at the end of which is the failure or breakage of the component, is primarily dependent on the duration of the load and the load intensity caused by a changing load. The fatigue fracture occurs earlier, the higher the frequency of the alternating load and the larger the oscillation amplitude. Qualitatively, the amount of stress can be derived from the ratio of the fatigue fracture area compared to the residual force fracture area . The larger the residual force fracture area, the higher the nominal stress acting on the material.
In contrast to forced rupture, the material is subject to stresses caused by swelling or oscillating loads that are below the yield point , in the elastic range. Under such alternating loads, changes in the microstructure of the material can be determined with a sufficient number of load changes, which are an indication of fatigue.
Latching lines on the fracture surface due to intermittent crack growth are the visible sign of a fatigue fracture. The microscopic counterpart to this are very finely structured furrows, which are known as vibrating strips. According to theory, a load change cycle can be determined based on the distance between two vibrating strips, but this is only very rarely possible in practice, since z. B. there is no completely equal vibration load. Vibrating stripes are an almost certain indication of cyclical stress; however, must not be confused with the breakage of a pearlitic structure. In most cases, locking lines and the type of fracture course are sufficient to demonstrate a fatigue fracture.
Actions to avoid
Since the cause of the fatigue fracture is ultimately the mechanical alternating stress, it is important to reduce this through design measures:
- Sufficient dimensioning of the component for dynamic stress, for example by dimensioning against component failure at the weakest point with the aid of Smith or Haigh diagrams , Wöhler line diagrams or through fatigue strength calculations or machine dynamic calculations
- Avoidance of additional alternating stresses due to natural vibrations
The natural vibrations that can be caused by the load case or an external excitation can be the sole cause of a fatigue failure. An example are high-standing, heavy-duty wired electronic components on circuit boards that are used, for example, in motor vehicles or on vibrating machines, or mudguards and their brackets on bicycles. In such cases, it makes sense to change the natural frequency of the vibratory system (preferably through greater rigidity) or to dampen the vibration. Wired, raised components are therefore often fixed on circuit boards with adhesive .
In addition to the dimensioning of the component, the risk of fatigue fracture in mechanical engineering is reduced by various measures, the common goal of which is to avoid a starting point for the breakage. Such a starting point is where there is high local tension , so the measures are particularly worthwhile at such locations:
- Creation of rounded transitions with changes in cross-section, avoidance of abrupt changes in cross-section
- Avoidance of notches, e.g. B. as a result of
- Damage
- constructive elements such as threads and grooves
- special manufacturing features such as unprocessed weld seams
- Create smooth surfaces
- Introduction of compressive residual stresses into the material surface, shot peening is common here , which scientifically verifiable brings compressive residual stresses into the material and extends the service life in the event of cyclical loading
- Treatment of weld seam transitions with High Frequency Impact Treatment (HiFIT for short) - a process for extending the service life of welded constructions by rounding out the geometric notch, surface smoothing, surface hardening and the introduction of residual compressive stresses up to a depth of 1.5 mm
- Avoiding manufacturing defects such as duplications and inclusions
- Use of suitable materials - it is assumed that e.g. B. cast iron with spheroidal graphite compared to lamellar cast causes a more favorable stress curve in the microstructure
- Corrosion protection, among other things to avoid stress corrosion cracking
Individual evidence
- ↑ according to VDI guideline 3822