Carrier
A hoisting machine is a mechanical device that is used in mining to drive the hoist baskets or buckets . It is used as a drive machine in shaft and inclined conveyor systems.
history

The original form of the hoisting machine is the hand reel , according to today's classification a muscle-powered single-drum machine set up above the shaft. As mining advanced into greater depths, more drive energy was required and this led to the construction and use of pedal bikes, horse paws and sweepers . Now the installation above the shaft was abandoned and these early hoisting machines were positioned to the side of it. In some cases, sweepers were also installed underground in wheelhouses, with the impact water being supplied through impact chutes and discharged through drainage chutes. With this arrangement, which was common in ore mining from the Middle Ages to the beginning of industrialization, the hoisting ropes were either guided through separate cable channels or through the shaft itself into the driving house and then diverted back into the shaft by pulleys . By arranging the guide vanes in two rings with opposite orientation, the rope cages could be driven in both directions.
The concept of the hoisting machine emerged with the introduction of the steam engine for shaft hoisting. Until the beginning of the 20th century, the winding machines were powered exclusively by steam. The first electric hoisting machines were set up at the beginning of the 20th century at the von Arnim coal works in Planitz near Zwickau ( Neuer Heinrichschacht 1899 and Neuer Alexanderschacht 1902). For a long time afterwards, both electric and steam-powered hoisting machines were used. With the shutdown of coal mine power stations in the 1950s and 1960s, the simple supply of steam was no longer necessary, so that a boiler house with steam boilers was only required for the steam supply to the hoisting machines. The steam-powered hoisting machines were gradually displaced after the Second World War. However, steam operation at the Lohberg colliery was only switched to electric drive in 1995.
construction
A hoisting machine essentially consists of the following 5 components:
- Rope carrier
- Drive (drive machine and, if applicable, gearbox)
- Braking devices
- Control and regulation devices
- Control stands
This also includes the necessary relocations and foundations.
Rope carrier
The term cable carrier emerged from the need to find a common generic term for cable baskets, drums, traction sheaves or reels. The cable carrier picks up the hoisting rope , which is connected to the conveying means or hoisting cage located in the shaft . By rotating the cable carrier, the conveying means located in the shaft is moved in an upward or downward direction via the hoisting rope. There are three different types of rope carriers:
Drums are used as rope carriers when pumping from particularly deep shafts.
Traction sheaves (also known as Koepe pulleys ) are the most frequently used cable carriers today.
The reel is used as a cable carrier for hoisting machines that are used to sink the shaft. Flat ropes are used as hoisting ropes.
drive
The drive consists mainly of the prime mover. In some specific hoisting machines, a gear is connected between the drive machine and the cable carrier . This is always necessary when the speed of the drive machine is too high and cannot be reduced enough. According to their drive energy, the following drive machines were used:
- Hydropower machines
- Pneumatic machines
- Steam engines
- Electric motors
Hydropower machines
In the case of the hoisting machines driven by water power, overshot water wheels were predominantly used. These sweeping wheels are divided into two halves by a central ring. The brake also engages on the central rim. The rope cages are mounted on the extended water wheel shaft. Turbines were sometimes used as drive machines. Since these machines have a higher speed, they are connected to the cable cage shaft via a back gear. Due to the required fall energy, the hydropower machines are usually installed underground in the shaft in such a way that the impact water can be diverted through the deepest tunnel. The contactors for the waterwheel control are also installed underground and are connected to the above-ground control station via rods. The ropes are directed to the surface pulleys.
Pneumatic machines
Single-cylinder machines and twin machines were used as compressed air machines in mining. The machines work at an overpressure of 3 to 5 bar . The machine attendant regulated the compressed air supply for the machines via a shut-off valve. The machines were mainly used as blind shaft machines or as devil reels. The basic structure of the machines is similar to that of steam engines. Since compressed air machines work with air as the drive medium and this air has a higher density than steam, the inlet and outlet openings in the valve body and cylinder are somewhat larger than in the steam engine. Single-cylinder machines are operated with a flywheel ; this is not necessary with the twin reel. Twin machines were often used in a double function for dewatering . Compressed air machines were used in the Westphalian hard coal mining and in Saar mining.
Steam engines
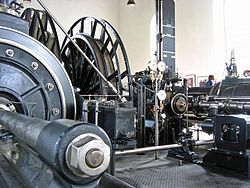
The first steam engines used as hoisting machines had an output of 8 to 20 hp. With these hoisting machines it was possible to convey a payload of one ton from a depth of 150 meters at a speed of 2 meters per second. Because of the strong vibrations, bobbins were used as rope carriers. More modern machines soon had outputs of 50 hp and more. They worked with a vapor pressure of 3 to 5 atmospheres. The pressure was able to escape unhindered from the outlet valves, as the machines usually did not have an expansion device installed. The expansion devices were not installed because they had proven to be disadvantageous when reversing. Disadvantages of these machines were the large dimensions of the slide and the associated manual mobility of the slide due to its size.
Some of the machines often had a dual function, they were used as a haulage machine and for drainage at the same time.
Each shaft system had to have a boiler house for the steam supply. Flame tube boilers were originally used as steam boilers , often in the form of a double flame tube boiler , which were operated at pressures of 10 to 16 bar. Most of the time, a so-called Roots storage facility was interposed between the steam generator and the steam engine. These storage tanks have a volume of several 10,000 l and are filled with boiling hot water. The steam from the steam boiler is introduced through nozzle pipes in the lower area of the storage tank. Since the steam engine is operated with a high overload when it starts up, considerable amounts of steam can be made available for a short time as a result of the re-evaporation from the large amount of water in the Roots reservoir.
- Examples of steam transporters
The 12 hp steam engine of the 125 m deep St. Lampertus shaft has been used to drive the cast-iron pump sets since 1876 and to drive the hoisting machine since 1880.
At the Zeche Fürst Leopold in Dorsten (most recently part of the Lippe mine , which was closed in 2008 ), the last twin steam engine operated in the Ruhr mining industry was located at shaft 2. The machine was shut down in mid-2008.
At the Oeynhausen 1 shaft of the Ibbenbüren mine there is a steam hoisting machine in the now rare design of a double drum hoisting machine. In some cases, the drive on dismantled conveyor systems with steam engines has been converted to compressed air (e.g. Malakow tower, shaft 1 of the Ewald colliery ).
Up until 2007, a total of three former steam hoisting machines were still in use at the Auguste Victoria mine in Marl. In 1966 these machines were converted to low pressure. The machines are from 1904 and 1907 (GHH Sterkrade) and 1911 (Isselburg). The shafts have since been closed and filled.
On the industrial monument Zeche Consolidation Schacht 9 in Gelsenkirchen, the largest steam hoisting machine in Europe, built in 1963 by Gutehoffnungshütte , stands . The two-cylinder twin steam engine has an output of 4100 hp, weighs 285 tons and lifted payloads of 12 tons at a speed of 18 m / s from the 1000 m deep shaft. The machine is demonstrated on the 1st Sunday of the month in the museum and runs on compressed air as in regular operation.
Carrier with electric motor
The requirements for hoisting machines, high torque with low speed at the same time as well as stepless control of the speed, could initially only be met by DC machines . These were supplied with the required direct current via a Leonard converter .
Modern hoisting machines are driven either by high-speed three-phase or direct-current motors with a downstream gearbox or low-speed, converter-controlled direct current or synchronous motors. Slow-running motors are coupled directly to the main shaft. High-speed motors up to 2 megawatts and slow-speed motors over 2 megawatts are used.
For drives with direct current motors, separately excited direct current motors with speed setting via the field or armature winding are used. The speed is set via differently switched converters . For three- phase drives , three-phase asynchronous motors with series resistors and step-by-step speed control or three-phase asynchronous motors with converter control or three-phase synchronous motors are used. For drives with three-phase synchronous motors, direct-converter-fed synchronous machines are used from a drive power of more than 1 megawatt. Carriers with an integrated motor have huge advantages.
Braking devices
A distinction is made between drum brakes and disc brakes when it comes to braking devices for hoisting machines. A distinction is made between drum brakes:
- Braking
- Double shoe brakes
- Internal shoe brakes
Mainly double-shoe brakes are used as drum brakes for hoisting machines. With these brakes, the braking force is transmitted through a brake linkage when the force is radial. Because the brake shoes are arranged on both sides, bending stress on the shaft is avoided. A distinction is made between two braking systems: the driving brake and the safety brake . In the case of the travel brake, braking takes place through an external energy supply, in the case of the safety brake braking takes place through an external energy dissipation.
With the disc brake, the force is generated by compression springs. The brake pads are pressed onto the brake disc by pretensioned and hydraulically controlled disc springs. When braking, the pressure is reduced and the associated energy dissipation occurs. Disc brakes have great advantages over drum brakes. They can withstand high thermal loads and the braking force is divided between several elements. Because they take up less space, they can be used to create multi-rope hoists better. With disc brakes, the individual braking elements respond to enable constant deceleration. In addition, it is easier to increase the braking force by installing additional braking elements.
Installation site
With regard to the location of the hoisting machine, a distinction is made between two options:
- Floor conveyors
- Tower hoists
In the case of floor conveyor systems, the hoisting machine is located at ground level at some distance from the headframe in a separate hoisting machine building. Sheaves in the headframe serve to divert the hoisting rope .
In a tower hoisting system, the entire hoisting machine is located in the hoisting tower, vertically above the shaft opening. This arrangement of the hoisting machine is very space-saving, since no further buildings are required on the mine site.
business
The carrier operator is responsible for operating the hoisting machine . The hoisting machine operator can determine the position of the basket using the depth indicator . The exact position is indicated by color markings on the rope. A lot of tact is required to operate the hoisting machine, especially for the precise positioning of the conveyor baskets with different loads. Operating the hoisting machine is a responsible task, especially when traveling by rope. The communication between the soles and the conveyor operator takes place via acoustic signals that are transmitted electrically. The so-called used to communicate with excavation work shaft hammer . The attacker is a person who monitors the operation of the shaft on the soles regularly hit by the basket. The attacker communicates with the haulage operator by means of the signal system (shaft hammer, ready-made signal system; formerly mechanical, now mostly electrical / electronic). At side shafts without regular rope travel, instructed miners can give the signal for the journey themselves (so-called self-propelled).
Performance data
The most important performance data for a shaft hoisting system are the payload that the hoisting machine can move and the conveying speed with which it can move this payload.
The world's largest and most powerful hoisting machine is currently located in the South Deep mine in South Africa. It is a two-cable, double-drum winder of the Blair type. The four hoisting ropes are each 3345 m long. The hoisting machine can move a payload of 31 t at a maximum conveying speed of 18 m / s from a depth of 3000 m. The electric motor of the hoisting machine has a drive power of 12.8 MW.
The most powerful traction sheave hoisting machine is installed in a blind shaft at the Gotthard Base Tunnel . The electric motor has a drive power of 4.2 MW. The hoisting machine can move payloads of 50.8 t at a conveying speed of 18 m / s from a depth of 800 m.
The largest traction sheave hoisting machine in Germany is the eight-rope system of the Zielitz I shaft with a payload of 50 t.
literature
- H. Hoffmann, C. Hoffmann: Textbook of mining machines (power and work machines). 3rd edition, Springer Verlag OHG, Berlin 1941.
- Julius, Ritter von Hauer: The conveyors of the mines. 2nd edition, published by Arthur Felix, Leipzig 1874.
- The technology of load handling then and now. Printed and published by R. Oldenbourg, Munich / Berlin 1907.
Individual evidence
- ^ Wilhelm Hermann, Gertrude Hermann: The old collieries on the Ruhr. 4th edition, Verlag Karl Robert Langewiesche, successor Hans Köster KG, Königstein i. Taunus, 1994, ISBN 978-3-7845-6994-9 .
- ^ Coal mining in the Zwickau district. Zwickau Coal Mining Association eV, Förster & Borries, Zwickau 2000, ISBN 3000062076 .
- ↑ Technical requirements for shaft and inclined conveyor systems (TAS). Verlag Hermann Bellmann, Dortmund 2005.
- ^ Walter Bischoff , Heinz Bramann, Westfälische Berggewerkschaftskasse Bochum: The small mining dictionary. 7th edition, Verlag Glückauf GmbH, Essen 1988, ISBN 3-7739-0501-7 .
- ^ Emil Stöhr, Emil Treptow : Basics of mining science including processing. Spielhagen & Schurich publishing bookstore, Vienna 1892.
- ↑ Albert Serlo: Guide to mining science. Second volume, 3rd edition, published by Julius Springer, Berlin 1878.
- ↑ Amadee Burat, Carl Hartmann: The material of hard coal mining. Published by August Schnee, Brussels / Leipzig 1861.
- ↑ Herbert Pforr: The Erzgebirge artificial ditch system and the water power machines for dewatering and shaft extraction in the historic Freiberg silver mining. In: Ring Deutscher Bergingenieure eV (Hrsg.): Mining. Makossa Druck und Medien GmbH, Gelsenkirchen 2007, pp. 502–505 Online ( Memento of the original dated October 4, 2013 in the Internet Archive ) Info: The archive link was inserted automatically and has not yet been checked. Please check the original and archive link according to the instructions and then remove this notice. (last accessed on October 30, 2012; PDF file; 646 kB).
- ↑ Freundeskreis Geologie und Bergbau eV Hohenstein-Ernstthal ( Memento of the original from October 4, 2013 in the Internet Archive ) Info: The archive link was inserted automatically and has not yet been checked. Please check the original and archive link according to the instructions and then remove this notice. (last accessed October 30, 2012).
- ↑ Steam conveyors on Fürst Leopold ( Memento of the original from June 19, 2012 in the Internet Archive ) Info: The archive link was inserted automatically and has not yet been checked. Please check the original and archive link according to the instructions and then remove this notice. (last accessed October 30, 2012).
- ^ Colliery Consolidation Shaft 9 in Gelsenkirchen (last accessed on October 30, 2012).
- ↑ Paul Burgwinkel: Drive technology in shaft conveyance. (PDF) RWTH, accessed on May 4, 2010 .
- ↑ Technical information on disc brakes for hoisting machines. Siemag Tecberg (accessed on September 10, 2012; PDF file; 581 kB)
- ↑ Horst Roschlau, Wolfram Heintze: Bergmaschinentechnik. VEB German publishing house for basic industry, Leipzig 1977, pp. 257-258.
- ↑ Steinkohlenportal article: Tempo im Schacht ( Memento from June 26, 2009 in the Internet Archive ) (accessed October 30, 2012).
- ^ Association for Mining and Social History Dorsten: Der Fördermaschinist ( Memento of the original from October 6, 2013 in the Internet Archive ) Info: The archive link has been inserted automatically and has not yet been checked. Please check the original and archive link according to the instructions and then remove this notice. (last accessed on October 30, 2012)
- ↑ Mining Ordinance for Shaft and Inclined Conveyor Systems (BVOS) § 24 Self-propelled ropeway (accessed on October 30, 2012).
- ↑ Siemag TECBERG: Drum Carriers Examples ( Memento of 14 August 2010 at the Internet Archive ) (accessed on 30 October 2012).
- ↑ a b Winfried Sindern, Olivier Gronau: Steel wire ropes - proven service providers of shaft hoisting systems . In: Ring Deutscher Bergingenieure eV (Hrsg.): Mining . 61st year, no. 4 . Makossa Druck und Medien GmbH, April 2010, ISSN 0342-5681 , p. 155-164 .
- ↑ Siemac Tecberg Koepe conveyor machine examples ( Memento from August 14, 2010 in the Internet Archive ) (accessed October 30, 2012)
Web links
- Koepe hoisting machine with electric motor (accessed October 30, 2012)
- Examples of conveyors (accessed June 10, 2016)