Die
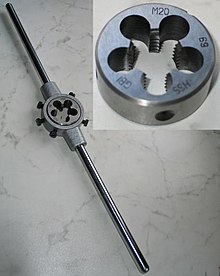
A die (cutting blade, also called filière in German-speaking Switzerland) is a metalworking tool for cutting external threads . It belongs to the machining tool and machining category . The corresponding tool for cutting internal threads is the tap .
Plant mechanics for sanitary, heating and air conditioning technology use cutting clips to produce threads on gas and water pipes .
Appearance and function
A cutting die is cylindrical and has three or more cutting edges on the inside, depending on its size . Hollow spaces in the form of bores are incorporated between the cutting edges , which roll and remove the chips . There are also hexagonal dies in order to be able to move the die in inaccessible places with a combination wrench or open-end wrench (especially for repair purposes) (see also thread cutting nut ).
The cutting edges are serrated and geometrically represent the nut thread. A chip is removed from each bolt to be machined.
The outer teeth are flattened. This on the one hand facilitates the first cut, on the other hand reduces wear and tear, and when cutting, each tooth takes a chip with approximately the same width. The inner teeth only serve to guide the die in the already cut part of the thread.
A cutting die is constructed symmetrically so that cutting is possible in both axial directions. On the outside of the cylinder there are three or four conical indentations with which the die can be secured against twisting by means of screws in a suitable holder. The sometimes existing groove is used for radial readjustment due to the inevitable tool wear . With an adjusting screw attached to the circumference of the die holder in addition to the retaining screws , a slotted die can be spread open in order to create an oversize thread for a more secure fit of the screw
Cutting dies are mostly made of high speed steel (HSS).
standardization
Die dies are standardized according to DIN EN 22568, formerly DIN 223.
Operation
Before the thread is cut, the workpiece must already have the correct nominal diameter . Small workpieces are clamped in a vice for fixation . The die is set at right angles and turned until the desired thread length is reached. In the case of tough materials, the die should be turned back a little after every half turn so that the chips break and do not clog the threads. A lubrication with cutting oil or another oil , z. B. rapeseed oil is strongly recommended. It reduces the effort required and increases the service life (service life) of the die.
In order to avoid tilting when attaching the die, the end of the blank should be chamfered at an angle of 45 ° . Clamping the workpiece and die in the chuck and vice or tailstock of a drilling or lathe can also ensure that the die is perpendicular to the longitudinal axis of the thread. In the case of tough materials, the chuck of the drill or lathe should be turned by hand in order to avoid breakage of the workpiece if the die jams. Alternatively, guide bushes can also be used in the die holder to prevent the die from tilting.
External threads (and internal threads with a large diameter) can in principle also be cut on a lathe with chisels or thread chasers and a special thread cutting device (lead screw / lock nut). However, especially with long and thin external threads, the workpiece can give way if no support is used (e.g. by means of rolling grains, rotating center point, etc.). Since the machine must first be set up, cutting individual threads on non-automated lathes is more time-consuming. Before unclamping, the thread should be checked using a thread gauge.