Hydraulic valve lifters
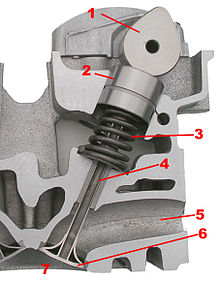
1. Camshaft cams
2. Bucket tappets with an annular gap for the oil supply to the HVAE
3. Valve spring
4. Valve stem
5. Gas duct to inlet (fresh gas) or outlet (exhaust gas)
6. Valve plate that presses the combustion chamber (7) against the Valve seat ring seals
7. Combustion chamber
Hydraulic valve lifters (also called hydraulic lifters) are lifters in the valve train of gasoline and diesel engines , which hydraulically compensate for valve clearance automatically . They were introduced by Cadillac in 1930 . In designs from around 1990, they are usually designed as bucket tappets and are therefore also called hydraulic bucket tappets . Hydraulic valve lifters are part of the hydraulic valve clearance compensation elements (HVAE).
Areas of application
Hydraulic valve lifters are widely used in automobile engines, but are rare in motorcycle engines . The motorcycles from Harley-Davidson and Buell are traditionally equipped with hydraulic valve clearance compensation , the Honda CB Sevenfifty , Yamaha MT-01 and the Kawasaki VN 1500 are new . Modern motorcycle engines often have very high rated speeds; Hydraulic valve lifters, however, are considerably heavier than rigid bucket lifters, which increases the moving masses of the valve train, which limits the maximum speed that can be achieved. In addition, hydraulic valve lifters require more installation space than normal bucket lifters, but this is often not available in the comparatively small motorcycle cylinder heads .
Layout and function
Hydraulic valve lifters make other elements for adjusting the valve clearance (adjusting screws, adjusting washers, plates of defined thickness) superfluous. There is also no need to check and readjust the game, which has reduced maintenance costs. The valve trains work almost free of play, which reduces wear and has a positive effect on engine noise, smoothness and efficiency of the engines, because the valve play and thus the valve timing (opening times of the inlet and outlet valve) can be observed better for all cylinders at all times.
Recently the trend has been going back to simple bucket tappets without valve clearance compensation. One of the reasons for this was that the hydraulic valve lifters wear out much faster than mechanical lifters. In addition, mechanical tappets allow higher speeds, more precise valve timing and are less dependent on the type of oil used. Thanks to modern manufacturing processes with low tolerances and more abrasion-resistant materials, mechanical valve tappets are also virtually maintenance-free. For example, with the introduction of the Focus in 1999 , Ford again used mechanical bucket tappets with adjusting plates for its Zetec 16V engines . The manufacturer plans to check the valve clearance for the first time at 150,000 km. However, the wear at this point is still so low that other setting plates are usually not necessary to compensate.
Hydraulic valve lifters are used - preferably as bucket lifters - in valve trains without rocker arms and rocker arms . In the valve train with rocker arms or rocker arms, instead, the lever abutments are usually designed as hydraulic lash adjuster elements (support elements). They are also called " hydrolifters "; however, rocker arms can also be provided together with hydraulic valve lifters (example: Ford CVH , Opel CIH ).
Working principle

The functional principle is always the same: A pressure bolt is guided with little play in a cylindrical cup and forms the working area with it. A backlash compensation spring (helical compression spring) inside presses on the bolt so that the lever or the tappet (with bucket tappets) always rests on the cam without play. There is a small hole in the pressure bolt that is closed by a ball valve ( check valve ) when the cam opens . This creates a rigid connection between the bolt and the cup in the oil-filled working space. The entire element behaves like a rigid body and presses on the valve stem (on the bucket tappet) or on the lever. In the rest position of the valve, the compensating spring presses on the pressure pin. A suction effect is created in the working space, which is enlarged as a result, the ball valve opens and oil flows in through the bolt bore from the storage or filling space above until the bolt is back against play. Temperature changes occurring during operation cause minor changes in size ( thermal expansion ) in the components of the valve train . These are compensated for by the so-called annular gap , which is formed by the slightly smaller diameter of the pressure bolt with the cup. It allows excess oil to escape in small quantities. The engine oil, which is fed to the valve train via the pressure circulating lubrication system, serves as the hydraulic fluid .
particularities
In the case of engines with hydraulic tappets, it is important to strictly adhere to the prescribed specifications, especially the viscosity of the engine oil and the oil change intervals, as otherwise malfunctions in the valve control can occur, which can lead to loss of performance and engine damage. When starting after the engine has been idle for a long time, typical rattling noises can occur if the hydraulic valve lifters are partially "idling". The noises usually disappear after a few seconds as soon as the tappets are completely filled with oil again. That is why leak-proof hydraulic valve lifters were developed, which were first used at BMW .
Advantages and disadvantages
The hydraulic valve clearance compensation in bucket tappets has some serious advantages for the consumer:
- The serviceability of the engines is increased by eliminating the valve clearance control.
- By eliminating the backlash during engine operation, the kinematically specified control times are maintained in all temperature ranges and during the entire engine life .
- The noise emissions are reduced due to the reduced shock excitation in the valve train.
But there are also disadvantages:
- Replacing the rigid tappet with the hydraulic valve means replacing a very rigid valve train component with a component that has a rigidity that is two orders of magnitude lower.
- After the engine has been switched off, the hydraulic compensation elements are shortened when the valves are open. This has a negative impact on the acoustic behavior after the next cold start.
- The constant contact of the tappet with the cam - even during the base circle phase - increases friction and thus fuel consumption.
literature
- Richard van Basshuysen, Fred Schäfer: Handbook Internal Combustion Engine Basics, Components, Systems, Perspectives. 3. Edition. Friedrich Vieweg & Sohn Verlag / GWV Fachverlage, Wiesbaden 2005, ISBN 3-528-23933-6 .
- Peter Gerigk, Detlev Bruhn, Dietmar Danner: Automotive engineering. 3. Edition. Westermann Schulbuchverlag, Braunschweig 2000, ISBN 3-14-221500-X .
Individual evidence
- ↑ G. Maas: Analysis of the dynamic operating behavior of valve trains with hydraulic valve lifters. Dissertation. RWTH Aachen University, 1987.