camshaft

A camshaft is a machine element in the form of a rod (= "the shaft ") on which at least one rounded protrusion (= "the cam") is attached. The shaft rotates around its own axis, and the cam (s) attached to it converts this rotary movement into a short longitudinal movement. In the standard design, the cam contours run parallel to the camshaft, but "angled cams" have also been implemented.
The camshaft is used in cam switches and controls, but mainly in reciprocating piston engines ( internal combustion engines ); here it is part of the valve train , it is used to open the inlet and outlet valves according to the design timing.
In older injection pumps , camshafts are also used to meter fuel to the individual intake manifolds or cylinders.
history
The technical device for converting rotating into linear movements was already known in ancient times. Since the 11th century, the camshaft has been used commercially in the form of cams or thumbs on elongated corrugated trees or axles on mill wheels . By the pressure of the cam could feed pounding , hammers , walking and lifting Pochstempel while they fell upon further rotation of the shaft and did their work. Bellows and saws were operated according to the same principle . At the beginning of the High Middle Ages, the camshaft played an important role in the mechanization of numerous trades.
Camshafts for valve control of reciprocating engines
On the camshafts of reciprocating engines such as the four-stroke engine there is usually an eccentric cam for each valve , which pushes the valve into the open position. When the cam is rotated further, the valve spring closes . The camshaft does not press exactly on the center of the valve, but somewhat laterally. As a result, the valve is always turned slightly and there are no irregular pressure marks from the cam. One cam can also operate several valves; Even the actuation of intake and exhaust valves by a single cam per cylinder has been implemented, but in such designs the timing for intake and exhaust cannot be selected independently of one another. A separate opening and closing cam per valve can be used for the unavoidable valve actuation . Camshafts have also been designed that do not rotate, but only reciprocate less than a full revolution.
Drive the camshaft
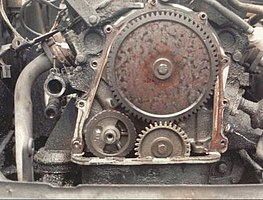
In standard four-stroke engines - with the exception of radial engines - the camshaft rotates at half the speed of the crankshaft , which is usually driven by a chain ( timing chain ) or a toothed belt , and more rarely by a vertical shaft with two bevel gears or a gear set .
The gear ratio of the timing gears is 2: 1 to cause the camshaft to rotate at half the speed of the crankshaft to control the four stroke cycle .
Arrangement & construction
Radial engines have a short cam drum or "large diameter cam disk" arranged coaxially to the crankshaft - it is sometimes also referred to as a "cam ring". Because all exhaust and intake cams of a cam drum actuate the exhaust and intake valves of a cylinder star, different speed and gear ratios result here, see cam drum .
In the standard design, camshafts are parallel to the crankshaft, but arrangements of camshafts that “stand” perpendicular to the crankshaft have also been implemented, for example in Chater Lea motorcycles and designs by Richard Küchen , for example for the Zündapp motorcycle prototype SS 600 . This arrangement often gives cause for confusion with vertical shafts .
In the pump-nozzle process for diesel engines, a further cam per cylinder actuates the piston of the injection pump. The advantage is the very high possible injection pressure and steep pressure increase compared to injection with a separate pump. Targeted pre-injections are also technically possible in pump-nozzle systems, but they are more complex to implement. Disadvantages, however, are the very high effort associated with high costs and the problematic package, so that the VW group, as the last advocate of the system in car engines, has switched to common rail injection. Advantages of the common rail system (originally introduced by Fiat at Alfa Romeo , meanwhile taken over by almost all major automobile manufacturers) are, however, the improvement of the combustion process and the engine running properties as well as the significantly lower particle emissions.
Either a tappet or a rocker arm or rocker arm is located between the cam and valve to keep the side forces away from the pushrod (if the camshafts are below) or the valve stem. With camshaft adjusters, the times for opening and closing the valves can be adapted to the power requirement during operation. This enables power and torque to be increased and consumption to be reduced in the partial load range. Camshaft adjusters turn the entire camshaft with respect to the crankshaft.
interpretation
All oscillating (back and forth moved) components have to be moved, cost performance and increase the inertia forces . If the camshaft is installed directly above the valves ( overhead camshaft ) and a separate camshaft is used for each row of valves (two overhead camshafts, DOHC), the number of oscillating components can be reduced, the inertia forces are lower and a higher speed is possible.
When calculating, designing and manufacturing cam controls, compromises have to be made: On the one hand, you want to open the valve wide for a good gas throughput; However, this increases the forces on the valve train that occur in circulation, and a collision of the valve with the piston must also be avoided. On the other hand, one would like to keep a valve open for a long time (over a large angle per cycle) for high gas throughput; on the other hand, there must still be an opportunity for consolidation.
All the mutual influences put tight limits on the variation of cam curves (construction, tuning or "regrinding") to increase performance. An engine with cam parameters that have been changed (“tuned”) towards higher output will need a higher idling speed, its maximum torque is shifted to higher speeds, it will run more restlessly and consume more fuel. The regrinding of the cam profiles, which was often practiced in the past, is no longer common; nowadays, a special camshaft is more likely to be procured for common engines to increase performance.
Camshaft adjustment
Camshaft adjustment is used for variable valve control , especially for realizing dynamically variable valve timing .
Manufacturing
The majority of camshafts for automobile engines is still in one piece of cast iron cast , in exceptional cases of steel forged and then machined edited and partially cured, for which usually the induction hardening process is used.
For some time now, so-called “built” camshafts made from different materials have been used. The advantages of built camshafts are lower costs, lower weight, higher-strength materials for the cams (hardened ball bearing steel, sintered steels), and greater flexibility in production. But new cam geometries such as negative cam radii are also easier to implement.
With a camshaft grinding machine, copies of a template can be made from a blank or a serial camshaft (using so-called raw master cams). For series production, the cam geometries are stored as parameters in the CNC programs. There is typically a link between the CAD data, the machining parameters ( CAM ) and the associated measuring programs ( CAQ ). Such series production is carried out on so-called pendulum grinding machines (orbital grinders).
The surfaces of the cams are hardened to a depth of approx. 0.2 mm and 1.5 mm . However, hardened cams are often used in assembled camshafts. The hardening of cams is more cost-effective and improves the material properties, since the hardness transition area in particular is avoided.
outlook
Fully variable valve controls are under development and in some cases already implemented (e.g. Valvetronic ). Although they have the mechanical drive via cam, but each valve is electro-hydraulic ( MultiAir - technology) or by a mechanical variable speed driven. It is common to all systems that a variable stroke and variable timing can be represented. The electro-hydraulic systems can also actuate the valve several times during the cam stroke. Their degrees of freedom are reminiscent of that of the injection valves, whose function (think of pump-nozzle) was basically taken over. The first electro-hydraulic concept from Fiat was first found in series production in the Alfa Romeo MiTo from mid-2009 . The mechanical Valvetronic system has been on the market since 2000. The fully variable electromagnetic systems that work entirely without camshafts are currently still too expensive, immature and difficult to integrate into current engine concepts (including high power requirements).
literature
- Richard van Basshuysen , Fred Schäfer (Ed.): Handbook Internal Combustion Engine Basics, Components, Systems, Perspectives. Friedrich Vieweg & Sohn Verlag / GWV Fachverlage GmbH, Wiesbaden 2005 (3rd revised edition), ISBN 3-528-23933-6 ( ATZ-MTZ reference book ).
- Hans Jörg Leyhausen: The master craftsman's examination in the automotive trade. Part 1: General principles, combustion engines, mixture formation, power transmission, chassis. Vogel Buchverlag, Würzburg 1991 (12th revised edition), ISBN 3-8023-0857-3 .
- Max Bohner, Richard Fischer, Rolf Gscheidle: Expertise in automotive technology. Verlag Europa-Lehrmittel, Haan-Gruiten 2001 (27th edition), ISBN 3-8085-2067-1 .
- Karl-Heinz Ludwig: The innovation of the camshaft in the transition from the early to the high Middle Ages. A sketch of European source problems with special consideration of the fulling mill . In: Technikgeschichte, 61. Vol. (1994), H. 3, pp. 227-238.