Radial engine
The radial engine is a type of reciprocating internal combustion engine in which several engine cylinders are arranged radially around the crankshaft in a star shape. Radial engines operated on the four-stroke - Otto process , but also diesel and two-stroke engines or combinations of these designs are possible. They are mainly used as aircraft engines . Fixed housing and a rotating crankshaft are common in these engines, but rotary engines have also been built in which the crankshaft is stationary and the cylinder star rotates.
technology
In a radial engine, the axes of all cylinders in a cylinder row are arranged radially around this axis at regular angular intervals in a plane perpendicular to the axis of rotation of the crankshaft.
Crank drive
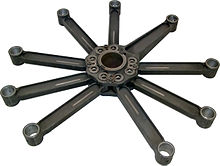
In contrast to other multi-cylinder engine concepts, each cylinder star only has a single cranked crankshaft. While in most other piston engines, each piston is directly connected to a crank pin of the crankshaft via its connecting rod, in the radial engine there is only a direct connection with one of the connecting rods, namely the main connecting rod (also known as the mother connecting rod ; in the animation above the lighter colored upper one Connecting rod). At the base of the main connecting rod on the crankshaft side there are spherical bearings arranged in a ring around the connecting rod eye running on the pin; the remaining connecting rods ( called secondary connecting rods ) are connected to the main connecting rod via these spherical bearings. This design ensures that all pistons in a cylinder plane can act on a single crank pin via the respective connecting rod without any longitudinal offset. As with all main / secondary connecting rods, the line of force of the secondary connecting rods - depending on the crankshaft position - is not always exactly in a straight line between the piston pin and the center of the crank pin, but sometimes slightly buckled at the eccentric pivot point of the spherical bearing. This results in slightly different piston strokes of the secondary connecting rod pistons compared to the main connecting rod piston (in the millimeter range). Since the complex connecting rod foot of the main connecting rod, which is highly stressed by the spherical bearings, is usually not divisible for assembly, ie it can only be manufactured without a removable connecting rod cover, a crankshaft that can be divided at the crank pin is usually used in return.
Since the oscillation of all movable components takes place in exactly one plane, there are no free moments of mass. The rotating inertia forces of the connecting rods and pistons can - generally in engines with an even number of cylinders or in engines with an odd number of cylinders from five cylinders - be almost completely balanced by the counterweights on the crank webs, which results in low-vibration operation.
Valve control
Four-stroke radial engines usually have an OHV valve control with push rods and rocker arms in the cylinder heads. In the simplest case, the valves are controlled by a step-down cam drum arranged in the crankcase . However, constructions with one camshaft per cylinder or valve are also possible. During the Second World War , large numbers of valveless four-stroke slide engines were used on the British side , in which the gas exchange was controlled through alternately released openings in the cylinder liner .
Housing structure
As a rule, in the front part of the compact crankcase in the direction of flight, a propeller gear is integrated in many models , in the rear part there is usually a central radial charger driven by the rear crankshaft stub for engine charging and the auxiliary units such as fuel pumps, alternators, starters and the mixture preparation .
Engine lubrication
Since the construction without a pronounced structural top or bottom makes it impossible to use an oil pan at the lowest point of the oil circuit, dry sump lubrication is usually used , often even with several return pumps.
Number of cylinders
In a radial engine, all pistons of a star reach top dead center one after the other for each crankshaft revolution .
Since with the four-stroke process there is only one working stroke every second crankshaft rotation, the engine needs two rotations (720 ° crank angle) to ignite all cylinders. In order to evenly distribute the work cycles of all cylinders over this 720 ° crank angle = two crankshaft revolutions, every second cylinder that reaches top dead center fires continuously; the cylinder in between is always in the top dead center of the gas exchange cycle (end of pushing out / beginning of suction). In the case of a seven-cylinder radial engine, for example, this results in an ignition time sequence in the order 1-3-5-7-2-4-6 . The number of cylinders in a cylinder star is always odd in four-stroke engines, as this consistently even firing sequence with the same crank angle intervals - which is necessary for low-vibration torque output - can only be achieved with an odd number of cylinders. Otherwise, at the end of the complete cycle of all four cycles of all cylinders, deviating from the regular cycle, two adjacent cylinders would have to fire immediately one after the other, which would disrupt the uniform sequence of the working cycles with regard to the crank angle.
A further advantage of an odd number of cylinders is the better stability and rigidity of the crankcase, which results from the fact that with an odd number of cylinders there is an area without a housing breakthrough compared to each cylinder bore. The resulting overlap offers structural advantages. Without additional measures, the housing becomes significantly stiffer than with an even number of cylinders.
With practical engine designs in terms of bore / stroke ratio, connecting rod length and overall diameter, up to nine cylinders per cylinder plane can be arranged around the housing. However, up to eleven cylinders were also used in rotary engines (e.g. Siemens & Halske Sh.III ), and up to twelve cylinders in stationary engines ( Nordberg Radial Engines ).
Two-stroke star engines can also be manufactured with an even number of cylinders, for example, in 1940, Adolf Schnürle built an 8-cylinder two-stroke diesel star engine and around 10 years later Ludwig Elsbett built a 4-cylinder two-stroke diesel engine in his car - Prototype used.
Designs
Originally radial engines were only designed in a single row . When more power was required, for which it was not possible to arrange enough cylinders next to one another, two-row radial engines (also called double radial engines ) were developed: two cylinder stars were arranged one behind the other. With further increasing performance requirements, four-row radial engines were also produced, such as the Pratt & Whitney Wasp Major with 28 cylinders in four rows.
Two or more cylinder stars are staggered in air-cooled engines so that the cylinders of the rear star come to stand behind the spaces in the front star. The advantage of this arrangement is a better flow of cooling air over all cylinders. In addition, the ignition interval is somewhat more even. In the case of water-cooled engines, the stars were not shifted, this is called a radial engine .
Water-cooled radial engines have been built relatively rarely. Applications were, for example, the construction of engines for tropical climates that could be cooled more reliably with water, or later the construction of compact multi-row radial engines such as the Jumo 222 , a four-fold radial engine without cylinder offset , which is a hybrid of the in-line radial engine.
Radial motors can also be implemented as rotary motors . In aircraft engines from World War I , the crankshaft was fixed while the cylinders rotated with the propeller attached to them . The carburetor sat on the (hollow) bearing journal of the crankshaft. Standing radial engines were only used in large numbers after the war. The Megola motorcycle (1921) also had a rotary engine in the front wheel. The housing rotated at wheel speed, the crankshaft rotated backwards at five times the wheel speed. The housing of the planetary gear in between was firmly connected to the front fork.
advantages and disadvantages
advantages
In the early days of aircraft engine development, radial engines proved to be superior to conventional in-line engines. Radial engines were lighter than comparable in-line engines. The short overall length was beneficial to the aircraft designers in the development of manoeuvrable fighter aircraft, thanks to the good mass balance, little vibrations were transmitted to the filigree airframes.
In the military sector, the lower sensitivity of air-cooled radial engines to bombardment was seen as an advantage, since there is no risk of damaging a liquid cooling circuit and thus of losing coolant; a loss of coolant always results in engine failure within a very short time. Since air-cooled radial engines do not require any corrosion-sensitive coolers, their sensitivity to saltwater corrosion was assessed to be lower when using the carrier , which led the US Navy to use only models with radial engines for their aircraft used on aircraft carriers (until the introduction of jet aircraft ).
disadvantage
Compared to other designs, radial engines have a larger frontal area and therefore a higher air resistance. The development of the low- resistance NACA hood improved the situation compared to the previously common free-standing cylinders, the Townend ring or tight-fitting fairings, but could not completely compensate for the disadvantage compared to in- line and V-engines . In double and multiple radial engines, the drag disadvantage is less pronounced due to the arrangement of several cylinder stars with the same face.
The usual air cooling is also less favorable in terms of air resistance and, due to asymmetries in the cooling air flow, inevitably means that not all cylinders or cylinder areas always work at the same temperature and that individual cylinders can run the risk of overheating or undercooling.
The cylinder arrangement - especially in multi-row engines - makes the routing of the individual exhaust and intake lines from and to all cylinder heads more complex compared to in-line or V-engines, in which only a few collecting lines can connect all cylinders of a bank.
As some of the cylinders are designed to hang down, it is possible that when the engine is switched off, engine oil will seep past the piston skirt and piston rings into the combustion chamber; this leads to increased oil consumption and brief smoke formation when starting the engine. In the worst case, when starting the engine, too much oil that has seeped in can lead to a hydraulic blockage of a cylinder and thus to damage or destruction of the engine.
history
The first rotary radial engines were built by Félix Théodore Millet in 1889 and by Stephen Balzer in 1899 . The first radial engines with an upright crankcase followed at the beginning of the 20th century and were used as aircraft engines by aviation pioneers such as Louis Blériot . Until the end of the First World War, rotary engines were the predominant design of radial engines. Star-shaped stationary motors did not gain acceptance until after the First World War, but then completely replaced the uneconomical rotary motors.
Although radial engines were primarily used in aviation, there were other applications in boats and land vehicles. The Megola motorcycle with a 5-cylinder rotary engine in the front wheel became very popular due to its performance and unusual design. The M4A1 variant of the American Sherman tank used in World War II was powered by a converted Wright J-5 Whirlwind aircraft engine in a star design. The “Volkswagen” prototype developed by Porsche for Zündapp was also powered by a 5-cylinder radial engine.
Because of its large frontal area for a given number of cylinders, the single-row radial engine was unsuitable for high-speed flight; and with the introduction of low-flow monoplane in military aviation in the 1930s, water-cooled V-engines proved to be superior to air-cooled radial engines. Only with the introduction of double radial engines with twice the number of cylinders with the same face area did radial engines become competitive again.
In the case of larger aircraft such as the American long-range bombers in World War II, which were all equipped with radial engines, the larger frontal area of the engine was hardly significant compared to the overall size of the aircraft. The massive use of radial engines in the USAAF brought American radial engines to a very high level of development. Air-cooled radial engines became the predominant engine type in civil aviation after World War II.
In 1954 the engineer Heinz Gartmann described the radial engine as the result of an optimization process:
- “The aircraft engines started with a cylinder. [Later] several cylinders were put in a row, four, eight, even twenty-four. The engines became very long. Therefore, two rows of cylinders were now placed side by side and the V engine was installed . Eventually they took two V-engines and made them the X-engine . Recently, even more cylinders could be accommodated in the radial engine. Nine cylinders made one star. Several stars in a row resulted in up to 36 cylinders in one engine. Every gram of superfluous weight was saved, so that the engines looked like real gems. A single radial engine does as much as two express locomotives and weighs less than the wheels of one. "
The progress in the development of exhaust gas turbines resulted in the development of turbo-compound engines , which were used, for example, in the Lockheed Super Constellation . In compound engines such as the Wright R-3350 , with three turbines and hydraulic clutches each, the kinetic energy of the exhaust gases was also used to drive the propeller shaft.
When propeller turbine air jet engines (PTL, turboprop ) of the same and higher power became available, they ousted radial engines from the market due to their simple construction, great reliability and improved economy. Since the radial engine competes with the cheaper and more compact boxer engines in the lower power range and PTL engines today cover the higher power ranges economically, radial engines are rarely used.
Pratt & Whitney R-985 AN14B radial engine with Townend ring
Water-cooled Russian 42-cylinder in-line radial engine Zvezda M503 for marine use
Wright R-1820 radial engine in a Sikorsky H-34 helicopter
literature
- Ernst Götsch: Aircraft technology . Motorbuchverlag, Stuttgart 2003, ISBN 3-613-02006-8 .
Web links
- Construction of a radial engine (English)
- Inside The Radial Engine (English)
Individual evidence
- ↑ Heinz Gartmann: Fifty years of flight performance , in: Westermanns MONTHS, Issue 4/1954, p. 55