Coal iron stone
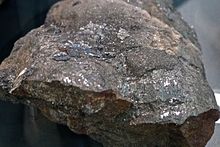
Coal iron stone , also called Blackband or Black Strip, is a seam-like deposit of iron ore in carbonic sediments that often occurs together with hard coal . Due to its appearance, it is very easy to confuse it with coal. For this reason, it was not recognized earlier that this was ore , but rather the coal iron stone was considered to be of inferior quality hard coal and was taken to the mine dump . After discovering the usefulness of the coal iron stone, it was mined and used for iron making.
Emergence
The coal iron stone was created during the Carboniferous Period . In several deposition periods it was deposited in boggy and shallow freshwater basins during the formation of the coal. Moss plants and other plants that keep double acid iron oxide dissolved, excrete iron oxide hydrate in shallow water . This excreted iron oxide hydrate settles in the root area of the plants. This also happens in a similar way with rotting humus matter. The precipitated iron compounds can accumulate on a water-retaining layer. The proportion of the later iron content in the ore depends very much on the amount of iron-containing liquids flowing in. Since these processes take place differently depending on the location, it can happen that different stratifications result when the seams are formed. In one and the same seam it can happen that coal iron stone has formed in one place and not in another.
Appearance and composition
Coal iron stone is a black, matt to shimmering thick slate rock. The coal iron stone gets its black color from its 10% share of hard coal. Coal iron stone is composed of a mixture of iron spar , aluminum silicate and carbon . The carbon content is between 12 and 35%, depending on the deposit . In addition, the ore contains small amounts of up to 1% manganese and 0.5% phosphorus . The ores in some deposits are so rich in phosphorus that they are suitable for the production of superphosphates. In addition, coal iron stone contains small amounts of arsenic and sulfur metals, e.g. B. spear pebbles, arsenic pebbles, pebbles as well as galena and zinc blende. The sulfur content of the ores is up to 0.4%. The ore contains an average iron content of 25–40% iron , the average iron content is 30%. The best varieties show a metallic sheen in the line on the fresh break. The ore is mostly still contaminated by shares of marl , sand or clay .
Occurrence and extraction
Coal-iron stone seams accompany the hard coal seams, especially the seams of the lower seam horizon. Their occurrence is quite different. They occur partly in the hanging wall , partly in the horizontal of the seams. There are also seams in which the coal iron stone occurs in the tailings. In some seams of the hard coal formation, the coal iron stone forms seams up to 0.7 meters thick . In Germany in the Rhenish-Westphalian hard coal district, this occurs increasingly in the Sprockhövel , Gelsenkirchen or Aplerbeck areas . In English or in the Scottish coal fields, the coal-iron stone seams reach significant thicknesses. Coal iron stone was first found in Scotland in 1801. The ore was first discovered in the Ruhr area in the second half of the 19th century. At the Hiddinghausen colliery, a 1.24 meter thick coal-iron stone seam was mined through a tunnel . Significant amounts of coal iron stone were extracted in the 1860s and 1870s .
Processing and smelting
It has been used to make iron since the early 1830s. The once important Scottish iron industry was based on the large deposits of coal iron. In Germany, the finds from Kohlenisenstein meant that large blast furnace huts were built in the area of the villages of Hörde, Haßlinghausen, Aplerbeck and Hattingen. Due to its high liquidity, iron coal is, also due to its impurities, an ore that is difficult to melt. In order to increase the iron content of a maximum of 40%, the ore is processed by roasting . During this process, which takes about a month, the iron content can be increased to 35–65%. On average, the iron content after roasting is around 45%. The roasting process not only increases the iron content, the ore also loses about half of its weight. To roast the ore, depending on the carbon content, pile-like piles with a length of 40 to 60 meters, a width of six to eleven meters and a height of one to five meters were heaped up. These pile-like piles were mostly piled up on or near the Zechenplatz. Most of the fuel used was wood. Due to the carbon content, the coal iron stone burns by itself. During the open roasting process, the volatile components escape into the atmosphere , which leads to severe air pollution. Later, special roasting ovens were used for roasting. The ore is smelted in blast furnaces . The first attempt to fuse coal iron stone was made by Mushet in the calder hut. Because of this successful attempt, larger amounts of coal iron stone were later smelted.
literature
- Friedrich Klockmann : Textbook of Mineralogy. Fifth and sixth improved and enlarged edition, published by Ferdinand Enke, Stuttgart 1912.
- Friedrich Steltmann: The coal iron stone mining in the Dortmund-Aplerbeck area . In: Der Aufschluss, Volume 13, Göttingen 1962, pp. 224–227.
Individual evidence
- ↑ Joachim Huske: The coal mine in the Ruhr area . 3rd edition, self-published by the German Mining Museum, Bochum 2006, ISBN 3-937203-24-9 , p. 41.
- ↑ a b c d e f Ludwig Beck: The history of iron in technical and cultural-historical relation . 4th division the XIX. Century from 1801 to 1860, printed and published by Friedrich Vieweg and Son, Braunschweig 1899, p. 322, 802, 835.
- ↑ a b c d Richard Beck: Doctrine of the ore deposits . Second revised edition, published by Gebrüder Borntraeger, Berlin 1903, pp. 92–95.
- ^ A b c d e f g h Tilo Cramm: The mining between Dortmund-Syburg and Schwerte. Friends of Mining Historic Sites Ruhrrevier eV, Dortmund Working Group (publisher), Uwe Nolte printing company, Dortmund / Iserlohn 2010, p. 75.
- ↑ a b c d Lexicon 88: Kohlenisenstein (last accessed on October 22, 2012).
- ↑ a b c Lexicon 88: Eisen (Brauneisenstein, Spateisen-, Thoneisen- und Kohlenisenstein) (last accessed on October 22, 2012).
- ↑ a b c d C. E. Jullien, Carl Hartmann: Theoretical-practical manual of the iron and steel industry encompassing the pig iron, the cast goods, the bar iron, the steel, and the tinplate manufacture . Authorized German adaptation, Verlag von August Schnee, Brussels and Leipzig 1861, pp. 54–55.
- ^ Gustav Adolf Wüstenfeld: Schlebuscher Revier Bergbau in Wetter. Gustav Adolf Wüstenfeld-Verlag, Wetter-Wengern 1983, ISBN 3-922014-05-4 , p. 12.
- ↑ a b c Bruno Kerl: Outline of the iron and steel industry . Verlag von Arthur Felix, Leipzig 1875, p. 66 ff.