Air hammer
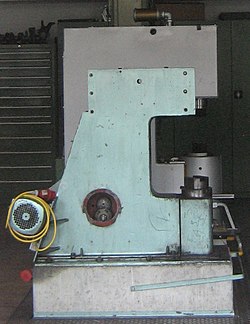
An air hammer (usually referred to as “power hammer” in English , rarely “air hammer” ) is a stationary machine hammer , which is mostly used for artisanal and industrial open- die forging , less often for drop forging . It should not be confused with a pneumatic hammer.
Air hammers were developed at the beginning of the 20th century and, along with presses, are among the modern forging machines. The mode of operation consists in the stretching (forging or forging) of the iron ( steel ), which is usually light cherry red in color, using forged saddles or dies - similar to anvil and hammer.
Standards with regard to quality and operability (control) set up in the 1990s existing company Bêché & Grohs whose surviving air hammers in workshops today ironwork are highly valued. The easy control of the blows makes it possible, with a well-preserved Bêché air hammer with a 100 kg bear weight in the red- hot state, iron ( steel ) of max. 120 mm diameter can be forged down to 5 mm with appropriate intermediate steps and sensitivity.
construction
An air hammer consists of a mostly C-shaped frame (hammer body) that contains an anvil ( scabot ) in the front machine base and two air cylinders in the upper arm. Two pistons move in these cylinders; Compressor piston and working piston. The piston in the compressor, which is mostly driven by electric motors today, generates a negative pressure above itself when it is shut down and compresses the air below it, which flows under the working piston, also known as a bear , when the valves (rotary slide valve) are open and lifts the bear. The air above the bar piston is led into the upper part of the compressor cylinder, where it is shortly afterwards compressed by the advancing compressor piston and pressed back into the bar cylinder, causing the bear to snap downwards. This brings together the saddles or dies , which are usually offset by 45 ° to the hammer body .
With one or two rotary slides, the impact energy ("impact force") and speed of the bear can be regulated by the blacksmith using a pedal , and with older designs also with a hand lever.
Sizes
Air hammers are manufactured today with bar weights of 15 kg to 2 tons. Smaller designs up to 25 kg are more suitable for cutlers . For forming in the trade it should be a hammer between 40 and 100 kg bear weight.
Air hammers with a significantly higher bear weight were the rule until the 1970s. Larger forming machines are currently often used as presses in the industrial sector . Nevertheless, gigantic air hammers continue to be used, such as B. in Germany at the locations Wildau and Bochum .
The largest air hammer ever built - still powered by steam - was built with a bear weight of 113 t (125 short tons ) and had a height of approx. 90 feet . The weight of the cast iron bulkhead was approx. 2150 short tons.
In principle, the very small design of the air hammer is also used in electric drilling and mortising machines (Hilti, Bosch hammer, etc.), see hammer drill . Here, however, the bear often only has a mass of a few grams.
See also
- Forge
- Smithy (workshop)
- Open die forging
- Blacksmith
- iron
- Drop forging hammer
- Spring drop hammer (also spring hammer)
- Drop hammer
Individual evidence
- ^ John Robertson Dunlap, Arthur Van Vlissingen, John M. Carmody: Factory and Industrial Management , 1893, McGraw-Hill publishing house