Corn silage
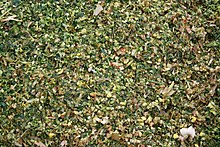
The maize silage is a silage made from the whole maize plant , which is used as basic feed for ruminants and as a substrate for biogas production . As a Corn-Cob-Mix (CCM), corn silage is also used in pig fattening.
generation
With whole plant silage, the above-ground part of the maize plant is harvested with a forage harvester ( maize chopper ) and cut into pieces approx. 5 to 50 mm in size at the end of the dough maturity or the beginning of the flour maturity (depending on the weather, maize type, sowing time and location in Germany) crushed. If the maize is chopped with more than 30% dry matter , a corn cracker is usually also switched on for crushing or grinding the then relatively hard maize kernels in the harvesting machine. The harvested material is then placed in silos introduced and compressed in order to press out excess air and thus prevent aerobic degradation by fungi and bacteria.
The plant mass is covered airtight under a foil and stored until it is used. Due to the residual sugar of the maize plants contained in the mass and the lack of oxygen, lactic acid fermentation begins , which acidifies the silage and thus makes it durable. If the silage is too wet and there is too much residual oxygen, undesirable acetic acid fermentation can also occur. The silage then becomes too acidic and is no longer palatable to the cattle because of the acetic acid ( acetate ) it contains.
The harvest and conservation of energy maize for use in biogas plants is largely identical to the process described above for feed silage. However, the crop is usually shredded to a greater extent in order to increase its degradability. Occasionally, heterofermentative lactic acid bacteria are specifically added to the chopped plant matter in order to increase the acetate content in the silage. This should be easier to implement in the biogas plant than the otherwise mainly formed lactic acid ( lactate ).
properties
Maize silage mainly contains energy in the form of starch from the maize kernels. In addition, due to the use of the entire, relatively large plant, it is also rich in crude fiber . In addition, the corn starch is a long chain with a harvest meal mature state, so that the digestion unlike corn meal is not already in the rumen , but only in the intestine of ruminants occurs. Since ruminants only coarsely chop their food, cows are not able to break down whole corn kernels. These are usually excreted undigested. The Weender feed analysis can be used to precisely determine the ingredients . A distinction is made between raw fiber, raw fat, raw protein, nitrogen-free extracts and raw ash.
material | Biogas yield in m 3 per ton of fresh mass |
Methane content |
---|---|---|
Corn silage | 202 | 52% |
Grass silage | 172 | 54% |
Rye GPS | 163 | 52% |
Pressed sugar beet pulp ensiled |
125 | 52% |
Fodder beet | 111 | 51% |
Biowaste | 100 | 61% |
Chicken litter | 80 | 60% |
Pig manure | 60 | 60% |
Cattle manure | 45 | 60% |
Grain Meat | 40 | 61% |
Pig manure | 28 | 65% |
Cattle manure | 25th | 60% |
In the biogas plant , corn silage as a substrate with 202 m 3 results in a very high biogas yield per ton of fresh mass. The methane content of biogas from maize silage is, however, rather low at 52%.
use

In agriculture, maize silage as whole plant silage or in the form of the lisk cob silage described below is mainly fed to cattle , since in addition to the nutritious, easily accessible constituents of the maize kernels, they can also partially convert the hard-to-reach fibers from the maize plant.
In the pig around since 1980, the maize as has CCM (corn cob mix) arrived. This is a silage made from the corn on the cob. The cobs are picked by a combine that has been converted for grain maize harvest and transferred to a CCM mill in the field. The piston components, i.e. the spindle and the grains , are ground and ensiled there. The hollies are not part of CCM.
Lieschkolben silage (LKS) is also produced regionally from corn on the cob (grains and spindle) and the milkweed leaves. Parts of the remaining plants are also harvested. Most of the harvest is done with a maize chopper with a picking attachment. The lower energy content compared to CCM and the poor compressibility have made the LKS mostly unprofitable. In addition, the contractor has to switch between the forage header and the picker during the season, or later convert the picker several times between the forage harvester and the combine.
Maize silage is also the most frequently used raw material for biogas production : More than 90 percent of biogas plants in Germany that use renewable raw materials use maize silage as a fermentation substrate. Maize makes up 79 percent of the mass of renewable raw materials used for biogas production. Reasons for this are, for example, the high yields of dry matter per hectare , even on poorer soils, the availability of proven cultivation and harvesting technology and the gas yield in the biogas plant.
Individual evidence
- ↑ Fachagentur Nachwachsende Rohstoffe e. V. (FNR): Biogas basic data Germany. (PDF; as of October 2008). Source for all information except for pressed pulp.
- ↑ Biogas yields of different substrates, division potatoes / beets lfl.bayern.de, see pressed pulp ensiled .
- ↑ http://www.lwksh.de/cms/fileadmin/user_upload/Presse/Archiv_2007/PDF_3607_08.09.2007/46-49_Thaysen.pdf LWK SH via LKS / CCM / Hochschnittmaissilage.
- ↑ P. Weiland: Technical requirements for the fermentation of energy crops. ( Memento of the original from February 6, 2015 in the Internet Archive ) Info: The archive link was inserted automatically and has not yet been checked. Please check the original and archive link according to the instructions and then remove this notice. (pdf; 915 kB) Presentation at the DECHEMA Bioenergy Conference, Güstrow, 8. – 9. March 2009.
- ↑ Institute for Energy and Environment, 2008: Monitoring the effect of the Renewable Energy Sources Act (EEG) on electricity generation from biomass. ( Page no longer available , search in web archives ) Info: The link was automatically marked as defective. Please check the link according to the instructions and then remove this notice. Final report on behalf of the BMU, p. 54.