Natural fiber reinforced plastic
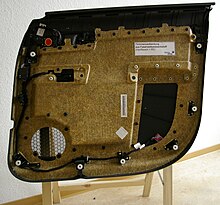
Natural fiber-reinforced plastic , or NFK for short , is a fiber-plastic composite made of a plastic (e.g. polyester resin , epoxy resin or polyamide ) and natural fibers . NFK heard within the biomaterials to biocomposites . It is used both as a long fiber reinforced and as a short fiber reinforced plastic. Natural fiber-reinforced plastics are given a stability thanks to the natural fibers incorporated that would not be possible without them. The main area of application is in vehicle construction , especially in the construction of trim components in the vehicle interior.
history
Natural fiber reinforced plastics were first used in the middle of the 20th century in the form of natural fiber composites in chemical binders such as phenolic resins . In 1941, the automobile manufacturer Henry Ford presented a car with a body made of resin-bonded fibers , the soybean car . Until the 1980s, mainly thermoset materials, equipped with wood and cotton fibers, were used as materials in automobile construction. While these were mainly used internationally for vehicle parts in interior fittings, they formed the material for the body paneling of the Trabant of the GDR . The driver's cabs of LKW are also made from cotton fiber materials embedded in phenolic resin to save weight internationally.
Today, many components in the interior of cars are made of natural fiber-reinforced plastics, including door panels, dashboard components, pillar panels and others. Today, different fibers such as hemp and flax, abacá and still cotton and wood are used, while plastics such as polypropylene and polyethylene serve as the matrix .
Materials used
Polymers
In principle, a distinction is made between thermoset and thermoplastic plastics for polymers . What both have in common, however, is that their main task is to transfer the loads that occur evenly to the reinforcement element, the natural fiber. A good connection between fiber and matrix is a basic requirement for this. In natural fiber composites, it is often difficult to ensure this connection, since natural fibers, due to their hydrophilicity , which is due to the large number of hydroxyl groups in the cellulose , often only allow weak interactions with the polymers. However, poor adhesion between polymer and fiber leads to significantly poorer mechanical properties of the composite material. Because of this, so-called adhesion promoters are added to most polymers , which can form strong chemical bonds with both the plastic and the natural fiber.
Duroplasts are characterized by an irreversible, strong cross-linking of the individual molecules. When exposed to temperature, they do not soften, but rather begin to decompose. As a result, natural fiber-reinforced thermoset materials are usually not recyclable and can therefore only be reused thermally. The most commonly used polymers are phenolic and epoxy resins .
Thermoplastic plastics deform under the influence of temperature, which makes the process of melting and solidification reversible and the materials become formable and recyclable. The most commonly used thermoplastics are polypropylene and polyethylene , polystyrene , polycarbonate and polyamides .
Natural fibers
A large number of different natural fibers can be used for the production of natural fiber composites. Some of the fibers differ drastically both in shape and length, as well as in chemical composition and mechanical properties. This in turn has a major influence on the processing options of the fibers and the properties of the composite materials.
The fibers most frequently used for the production of fiber composites are local flax and hemp fibers , as well as subtropical and tropical fibers such as jute , kenaf , ramie or sisal fibers . Even wood fibers are used as fillers and reinforcing material in fiber composites. In certain processes, these fibers are specifically modified by ultrasound digestion in such a way that they receive reproducible technical properties through the standardizable machining processes. For a better differentiation from the other natural fibers and due to their quantitative importance, composite materials with wood as filler or reinforcement material are called wood-plastic composites .
Biopolymers
Research in the field of biopolymers has been intensified in recent years . By using these plastics, medically safe, biodegradable composite materials can be produced, which often have properties comparable to those of natural and glass fiber-reinforced petroleum-based polymers.
A large number of both thermoset and thermoplastic polymers are now available that can be used as matrices for composite materials. One of the most frequently used bioplastics is polylactide (PLA) made from corn starch . In most cases, however, these polymers are priced well above the petroleum-based plastics, which is why they are used far less often for industrial purposes.
processing
Since natural fibers differ significantly from glass and carbon fibers , it is often necessary to adapt the common manufacturing processes for fiber composite materials to the particularities of natural fibers.
These include, for example, their limited thermal stability, which also greatly limits the selection of possible thermoplastics, and their high hydrophilicity . However, nowadays it is possible, by adapting existing manufacturing processes and developing new processes, to process natural fiber composites using a variety of different methods. One of the most important processing methods for NFK is compression molding , in which fiber mats are used to manufacture the components and both thermoplastic and thermosetting plastics can be used. Natural fiber injection molding and extrusion are among the newer processing methods, which are given great growth opportunities . Other methods for processing NFK are pultrusion , resin transfer molding or sheet molding compounds .
properties
Natural fiber composites have a number of properties that make them interesting as a material.
For example, natural fibers generally have a lower density than glass fibers or mineral fillers, which, with a correspondingly high proportion of fiber volume, can lead to a significant weight saving of a component. Since natural fibers are comparatively stiff and strong , there is great potential for substitution for glass fiber reinforced and filled plastics. A major problem with these materials, however, is their often relatively low impact strength , but this can be improved by adding natural fibers with high elasticity.
Furthermore, the natural fibers and thus also the composite materials are less of a concern from a medical point of view, which leads to improved occupational safety. Natural fiber composites are also less prone to splintering than glass fiber reinforced plastics.
Since natural fibers are relatively stable in price regardless of the strongly fluctuating oil price, the production costs of these materials can be better planned. In addition, natural fibers require less energy to manufacture than glass or carbon fibers, which, in addition to lower manufacturing costs, also leads to a significantly improved CO 2 balance of the materials. Natural fibers burn almost CO 2 -neutral and residue-free.
In addition to the occupational medical aspect, there are other advantages when processing these materials. The natural fibers cause less abrasive wear in the tool and because of the necessary reduction in processing temperatures, cycle times in production are shortened and energy consumption is lower.
NF-EP = flax fibers in connection with epoxy resin with a fiber content of 60% (volume), 12 layers, compression molding process
CF-EP = carbon fibers in connection with epoxy resin, compression molding process
Characteristic values | unit | NF-EP | Aluminum (alloys) | CF-EP |
---|---|---|---|---|
density | g / cm³ | 1.31-1.33 | 2.7 | 1.5 |
tensile strenght | MPa | 330-365 | 49 (-700) | 2850 |
Specific tensile strength | MPa | 248-278 | 18 (-259) | 1900 |
Modulus of elasticity | GPa | 35 | 70 (-73) | 225 |
Specific modulus of elasticity | GPa | 26.3 | 25.9 (-27) | 150 |
application
The main area of application for both thermoplastic and thermosetting natural fiber composites is the automotive industry.
In the years from 1999 to 2005, an increase in the use of materials from 15,000 t of material to 30,000 t in the German automotive industry was recorded, resulting in an average amount of around 3.6 kg of NFK per car. Natural fiber composites are used by practically all well-known automobile manufacturers. Typical areas of application are, in addition to interior door panels , roof linings , dashboards and parcel shelves .
The amount of natural fiber-reinforced plastics used for non-automotive applications in Germany is around 2,000 tons. Since the applications of these materials are not always actively known, it is difficult to record all products that contain NFK. The best-known applications include a grinding wheel carrier made of polypropylene and hemp, urns, a cell phone upper shell, various packaging materials, children's toys, suitcases, organic rotary soap dispensers or furniture.
Another application example is boat building.
literature
- Michael Carus, Jörg Müssig, Christian Gahle: Natural fiber reinforced plastics. Plants - raw materials, products. Fachagentur Nachwachsende Rohstoffe e. V., Gülzow 2008 ( PDF download (PDF))
- Jörg Müssig, Michael Carus: Bio-polymer materials as well as wood and natural fiber reinforced plastics. In: Market Analysis of Renewable Raw Materials Part II. Agency for Renewable Raw Materials e. V., Gülzow 2007, fnr-server.de (PDF)
- AK Bledzki, O. Faruk, VE Sperber: Cars from Bio-Fibers . Macromolecular Materials and Engineering Edition 291, 2006, pp. 449-457
- Kim L. Pickering (Ed.): Properties and performance of natural-fiber composites . Woodhead Publishing, Cambridge, 2008, ISBN 978-1-84569-267-4
- Amar K. Mohanty, Manjusri Misra, Lawrence T. Drzal (Eds.): Natural fibers, biopolymers, and biocomposites . Taylor & Francis Group, Boca Ranton FL 2005, ISBN 0-8493-1741-X
- Tim Huber, Jörg Müssig, Erwin Baur, Frank Otremba: Reinforcement from nature . In: Kunststoffe , 2008, edition 98 (7), pp. 97–101
- Product catalog natural fiber injection molding . nova-Institut, Hürth 2007, ISBN 978-3-9805840-9-8 , pp. 10-13
- K. Van de Velde, P. Kiekens: Material Properties, Biopolymers: overview of several properties and consequences on their applications . In: Polymer Testing , Issue 21, 2002, pp. 433-442
- PA Fowler, JM Hughes, RM Elias: Review Biocomposites: technology, environmental credentials and market forces . In: Journal of the Science of the Food and Agriculture , Issue 86, 2006, pp. 1781–1789
- Walter Michaeli: Introduction to plastics processing . 2006
Individual evidence
- ↑ a b Michael Carus, Christian Gahle, Cezar Pendarovski, Dominik Vogt, Sven Ortmann, Franjo Grotenhermen, Thomas Breuer, Christine Schmidt: Study on the market and competitive situation for natural fibers and natural fiber materials (Germany and EU) . Agency for Renewable Resources (FNR), 2008
- ↑ Soenke Schierer: Eco boat building: On the green wave . ISSN 0174-4909 ( faz.net [accessed August 15, 2019]).