Epoxy resin

Epoxy resins ( EP resins ) are synthetic resins that carry epoxy groups . They are curable resins ( reaction resins ) that can be converted into a thermosetting plastic with a hardener and, if necessary, other additives . The epoxy resins are polyethers with usually two terminal epoxy groups. The hardening agents are reaction partners and together with the resin form the macromolecular plastic.
The thermosets produced by crosslinking have good mechanical properties as well as good temperature and chemical resistance and are considered high-quality, but expensive plastics . You will u. a. Used as reaction and stoving enamels, adhesives , for laminates, as embedding agents in metallography and as molding compounds for components in electrical engineering and electronics .
history
Epoxies were first developed by Paul Schlack in Wolfen (patent application 1934, granted 1939) and Pierre Castan in Switzerland (patent application 1938 in Switzerland, granted 1940, produced by Ciba AG ).
Epoxy resins (prepolymers and monomers)
Most commercially used epoxy resins are made by reacting a compound with hydroxyl groups and epichlorohydrin :
- First, a hydroxy group reacts with epichlorohydrin in a coupling reaction, followed by dehydrohalogenation.
Such epoxy resins are called glycidyl- based epoxy resins. The hydroxyl group can come from aliphatic diols , polyols , phenolic compounds or dicarboxylic acids . Compounds such as bisphenol A and novolaks are used as phenols . Compounds such as 1,4-butanediol are used as polyhydric alcohols . Di- and polyols lead to diglycide polyethers. Dicarboxylic acids such as hexahydrophthalic acid are used for diglycid ester resins . Instead of a hydroxyl group, however, the nitrogen atom of an amine or amide can also react.
The second possibility for the production of epoxy resins is the reaction of aliphatic or cycloaliphatic alkenes with peracids :
As can be seen, in contrast to glycidyl-based epoxy resins, this production does not require an acidic hydrogen atom, but a double bond.
Bisphenol-based epoxy resins
Around 75% of all epoxy resins used worldwide are based on bisphenol A. From this bisphenol A diglycidyl ether is produced in a reaction with epichlorohydrin :
- In a two-stage reaction, epichlorohydrin is first added to bisphenol A (bis (3-chloro-2-hydroxypropoxy) bisphenol A is formed), then the bis-epoxide is formed in a condensation reaction with a stoichiometric amount of sodium hydroxide . The chlorine atom is split off in the form of sodium chloride , the hydrogen atom in the form of water.
Higher-molecular diglycidyl ethers (n ≥ 1) are formed when the epoxide formed reacts with further bisphenol A:
With a few molecular units (n = 1 to 2), a viscous, clear liquid is obtained and one speaks of liquid epoxy resins. If there are more molecular units (n = 2 to 30), the result is a colorless solid, correspondingly one speaks of solid epoxy resins.
Instead of bisphenol A, other bisphenols can also be used (especially bisphenol F ) or brominated bisphenols .
Novolak epoxy resins
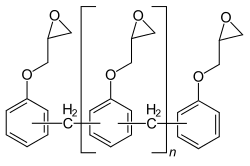
The reaction of phenols with formaldehyde leads to novolaks . The subsequent addition of epoxy groups with epichlorohydrin produces novolaks with glycidyl residues , such as epoxyphenol novolak (EPN) or epoxycresol novolak (ECN). These highly viscous to solid resins typically have 2 to 6 epoxy groups per molecule. Due to the high functionality of these resins, curing forms highly crosslinked polymers with high temperature and chemical resistance, but low mechanical flexibility.
Aliphatic epoxy resins
There are two types of aliphatic epoxy resins: those that are obtained by epoxidizing double bonds (cycloaliphatic epoxides and epoxidized vegetable oils) and those that are formed by reacting with epichlorohydrin (glycidyl ethers and esters).
Cycloaliphatic epoxides contain one or more aliphatic rings in the molecule on which the oxirane ring is contained (e.g. 3,4-epoxycyclohexylmethyl-3 ', 4'-epoxycyclohexane carboxylate). They are produced by the reaction of a cyclic alkene with a peracid ( see above ). Cycloaliphatic epoxides are characterized by their aliphatic structure, a high oxirane content and the absence of chlorine , which leads to low viscosity and (when cured) good weather resistance, low dielectric constants and high T g . However, aliphatic epoxy resins only polymerize very slowly at room temperature, so that higher temperatures and suitable accelerators are usually necessary. Since aliphatics have a lower electron density than aromatics , cycloaliphatic epoxides react less easily with nucleophiles than bisphenol A-based epoxy resins (have aromatic ether groups) . Thus, only poorly common, nucleophilic hardeners such. B. amines can be used for crosslinking. Cycloaliphatic epoxides are therefore usually homopolymerized thermally or UV-initiated in an electrophilic or cationic reaction. Due to their low dielectric constants and the absence of chlorine, cycloaliphatic epoxides are often used to encapsulate electronic systems such as microchips or LEDs . They are also used for radiation-hardened paints and varnishes. Due to their high price, however, they have so far been limited to such applications.
Epoxidized vegetable oils are formed through epoxidation of unsaturated fatty acids , also through reaction with peracids. In this case, the peracids can also be formed in situ by reacting carboxylic acids with hydrogen peroxide. Compared to LERs (liquid epoxy resins), they have very low viscosities. However, if they are used in larger quantities as reactive thinners , this often leads to reduced chemical and thermal resistance and poorer mechanical properties of the cured epoxies. Large-scale epoxidized vegetable oils such as epoxidized soybean and lentil oils are largely used as secondary plasticizers and costabilizers for PVC .
Aliphatic glycidyl epoxy resins of low molar mass (mono-, bi- or even higher-functional ) are formed by the reaction of epichlorohydrin with aliphatic alcohols or polyols ( glycidyl ethers are formed ) or with aliphatic carboxylic acids ( glycidyl esters are formed ). The reaction is carried out in the presence of a base such as sodium hydroxide, analogous to the formation of bisphenol A diglycidether. Aliphatic glycidyl epoxy resins also usually have a low viscosity. They are therefore added to other epoxy resins as reactive diluents or as adhesion promoters to reduce viscosity . Epoxy resins made from (long-chain) polyols are also added to improve tensile and impact strength.
Halogenated epoxy resins
Halogenated epoxy resins are added for special properties, brominated and fluorinated epoxy resins are used.
Brominated bisphenol A is used when flame retardant properties are required, such as in some electrical applications (e.g. printed circuit boards ). The tetrabrominated bisphenol A (TBBPA, 2,2-bis (3,5-dibromophenyl) propane) or its diglycidether, 2,2-bis [3,5-dibromo-4- (2,3-epoxypropoxy) phenyl] propane, can be added to the epoxy formulation . The formulation can then be reacted in the same way as pure bisphenol A. Some (uncrosslinked) epoxy resins with a very high molar mass are added to engineering thermoplastics, also to achieve flame-retardant properties.
Fluorinated epoxy resins have been explored for some high performance applications, such as the fluorinated diglycidyl ether 5-heptafluoropropyl-1,3-bis [2- (2,3-epoxypropoxy) hexafluoro-2-propyl] benzene. Since it has a low surface tension, it is added as a wetting agent ( surfactant ) for contact with glass fibers . The reactivity towards hardeners is comparable to bisphenol A. When hardened, the epoxy resin leads to a thermosetting plastic with high chemical resistance and low water absorption. The commercial use of fluorinated epoxy resins, however, due to their high cost and their low T g limited.
characterization
Epoxy resin products are characterized using different key figures . These include the molar mass or the molar mass distribution , the hydroxyl number and the epoxide equivalent weight . In addition, the already mentioned glass transition temperature determines a decisive role for the properties of the products obtained later.
Hardener and hardening
Harder |
![]() 1,3-diaminobenzene |
![]() Diethylenetriamine |
![]() Hexahydrophthalic - anhydride |
Polyvalent amines (" amine hardeners"), such as 1,3-diaminobenzene , and aliphatic amines, such as diethylenetriamine or 4,4'-methylenebis (cyclohexylamine) , are used as hardeners . Hardening with aliphatic amines takes place at room temperature (cold hardening); aromatic amines require heat curing. In the case of “acidic hardeners”, which are often dicarboxylic acid anhydrides such as hexahydrophthalic anhydride , hardening takes place at higher temperatures, often in the range between 120 ° C and 160 ° C. The reactive ethylene oxide rings of the epoxy resins react in addition reactions with the functional groups of the hardeners. Furthermore, due to the catalytic influence of the amino groups, anionic polymerization of the epoxy groups takes place to a varying extent . Strong acids cause cationic polymerisation .
processing
As with all reaction resins, the stoichiometric resin-hardener ratio must be precisely adhered to when mixing reaction resin compounds - otherwise parts of the resin or hardener remain without a reaction partner. These unreacted functional groups remain and the crosslinking remains incomplete, resulting in a soft product and sticky surfaces. However, some epoxy systems are less sensitive and are expressly suitable for varying the mixing ratio within narrow limits. This can influence hardness, elasticity and other properties; Acid resistance is increased by a higher proportion of epoxy resin. Since an inhomogeneous mixture of the two components has the same negative effect as an incorrect quantity ratio, extensive mixing procedures are necessary when mixing. If the color of the resulting plastic is irrelevant, the two starting materials can be colored in a richly contrasting manner as a mixing indicator. The polyaddition is strongly exothermic . The resulting heat of reaction can become so great that a fire occurs; However, at least the properties of the resin can be negatively influenced by the overheating. Low reactive resins are therefore used for components with large wall thicknesses.
The processing time of reaction resin compounds is called the pot life . It depends on the processing temperature, the setting of the reaction resin compounds and the batch size. Usual pot lives range from a few minutes to several hours. During the pot life, the viscosity of the resin continues to rise in a non-linear curve until processing is finally no longer possible. The specification of the pot life is usually made for a resin / hardener mixture of 100 g at 20 ° C - larger processing quantities develop a higher temperature and have a significantly shorter processing time.
Heating the mixed resin reduces the viscosity and thereby generally improves the processability, but also shortens the pot life. An increase in the processing temperature by 10 ° C halves the pot life or curing time ( RGT rule ). Low reactive epoxy resins require long curing times and, if possible, an increased curing temperature (30 ° C to 40 ° C). If necessary, accelerators (highly reactive hardeners) can be added to shorten the reaction time. Some epoxy resins can be subjected to heat curing after curing for complete crosslinking and to achieve a higher heat resistance.
During hot curing ( tempering ) the glass transition temperature (T g ) of the matrix rises by approx. 20 ° C to 25 ° C above the maximum hot curing temperature - this is the so-called temperature advance. Systems that cure at room temperature sometimes cure at room temperature with a very brittle matrix - curing over 40 ° C / 5 h to 6 h eliminates this and also improves the mechanical properties.
The reaction resin compounds are often modified with low-viscosity additives. Due to the lower viscosity of the reaction resin compound, better penetration into porous materials (impregnation of fabrics, coating of concrete) is achieved or the processability by injection molding (RTM process) is improved. On the other hand, such reaction resin compounds allow a higher loading of fillers, which results in a lower volume shrinkage during curing. The mechanical properties of the cured resin can also be improved, as can the economy. Glycidyl ethers are preferably used for these purposes, as these - in contrast to non-reactive diluents - are covalently bound to the polymer and therefore cannot migrate.
Commonly used as reactive thinners are:
Monoglycidyl ethers tend to terminate the polyaddition because they are only monofunctional. Therefore, they impair strength and temperature resistance, but increase flexibility. Glycidyl ethers of phenols have less of a disadvantageous effect than alkyl glycidyl ethers, but are judged less toxicologically. In the case of the alkyl glycidyl ethers, long-chain (C12-C14) are preferred because of their low vapor pressure; they can be produced cheaply from fatty alcohols .
- Polyglycidyl ether
These multifunctional reactive diluents are used when higher demands are made on the mechanical properties. Since they have at least two epoxide groups (like the frequently used hexane-1,6-diol diglycidyl ether), they do not cause the polyaddition to be terminated.
Reaction resin compounds can be provided with additives (e.g. pyrogenic silicon dioxide ) to make them thixotropic . This thickened resin can be used as a filler or an adhesive. Other additives serve as fillers (hollow spheres made of glass , ceramics or plastics ) to reduce the density of the resin, to improve the grip or abrasion resistance of the surface ( quartz sand , ceramic powder ) or to increase the maximum continuous operating temperature ( metallic Fillers : aluminum , iron / steel powder ). Aggregates (such as aluminum hydroxide ) can improve the fire retardant behavior of epoxy resin. This is particularly important when used in transport.
The curing can be started by adding photoinitiators with ultraviolet, whereby curing times in the range of seconds can be achieved.
properties
The unfilled, cured resin has a density of 1020 to about 1200 kg / m 3 . The modulus of elasticity is 3000-4500 MPa and the tensile strength is about 80 MPa. These values vary depending on the formulation and manufacture.
The dielectric constant is around 4 in the temperature range from −40 to around +60 ° C and, like the dielectric loss factor , increases sharply when it begins to soften (80–100 ° C). The loss factor has a minimum at 40 ° C, there is 50–100 x 10 −4 and increases at 100–120 ° C by orientation polarization of large chain segments to about 10 to 20 times. At −40 ° C there is also a maximum (3 to 10 times the value at 40 ° C), here caused by orientation polarization of short chain segments. Materials with CTI values ( tracking resistance ) of over 600 V are available. Bromination makes the material flame retardant ( UL94 V-1 or better).
The thermal conductivity is 0.21 W / (m · K) and can be significantly increased by using fillers (insulating electrical casting compounds about 1.26 W / (m · K) to 6 W / (m · K)).
The chemical shrinkage during polyaddition is, at 0.5… 5%, significantly lower than with unsaturated polyester resins. It can be reduced even further with fillers.
The unfilled resin is transparent yellowish to water-clear and is also available ultraviolet-resistant or non-yellowing. At wavelengths <400 nm, epoxy resin becomes almost nontransparent, in the infrared it is transparent up to 2 µm. The refractive index is 1.5 to 1.59 (at 589.3 nm sodium D-line ).
use
- Versatile construction adhesive , for example in boat building , household and model making
- Specially adjusted epoxy resins are used as metal adhesives
- Plastic-based mortar (reaction resin mortar)
- for the production of stone carpets
- Cast resin for the production of components in the casting process
- Used in conjunction with glass fiber , carbon fiber and aramid fiber in the construction of modern high performance gliders , but also increasingly for large passenger aircraft (carbon or carbon fiber) and fiber-reinforced plastic used
- Glass fiber reinforced plastic is used to produce the rotor blades of wind turbines for use
- Production of mineral cast frames for mechanical engineering
- Industrial floor; Concrete coating; Concrete repair
- Ion exchange columns (chemistry)
- Painting; heavy corrosion protection (shipbuilding, steel structures)
- Sealing of wooden terrariums (terrarium technology), as non-toxic when cured
- Binder for various paints (lacquers), a combination of phenolic resins creates interior protective lacquers for all types of packaging, from hairspray cans to food packaging (so-called gold lacquers)
- Paints to protect against graffiti
- Production of water-soluble synthetic resins for cathodic dip painting (KTL, automobile construction)
- Rehabilitation of pipes, especially pipe renovation ( e.g. of drinking water pipes, underfloor heating)
- Painting of bike paths
- Potting of electrical components or other objects for the purpose of insulation and corrosion protection
- Printed circuit board material such as FR-4 as a carrier material for electronic circuits
- Matrix material for the manufacture of fiber composite components , including for aviation and space travel , for the motor sport , in orthopedic technology and for the yacht building ; often also by hand lamination
- Plastination
- Is applied to the edges ( coping ) of skateboard ramps for better sliding and protection
- Carrier material in art
- Manufacture of thin sections
The construction of boat hulls has epoxy over some polyester resins , among others, the advantage that it osmosis excludes damage even if sea water by a damaged gel coat penetrates layer and comes with the material in contact. That is why epoxy resin is also used to repair osmosis damage to polyester resin boat hulls.
With the current state of the art, epoxy resin is not recyclable and the materials used to manufacture it are predominantly obtained from petroleum. However, attempts are already being made to obtain epoxy resin based on renewable raw materials. The aim is to develop a non-toxic, odorless and non-allergenic epoxy resin.
Safety and health
Manufacturing
Epoxy resin is usually produced industrially from a reaction of bisphenol A and epichlorohydrin. Due to the specific characteristics of these two reactants in particular, special safety regulations must be observed in the production of epoxy resin (for possible health risks and the state of research, see in particular the articles bisphenol A and epichlorohydrin ).
Epoxy resin was included under the name bisphenol-A-diglycidyl ether in 2013 by the EU in accordance with Regulation (EC) No. 1907/2006 (REACH) as part of the substance evaluation in the Community's ongoing action plan ( CoRAP ). The effects of the substance on human health and the environment are re-evaluated and, if necessary, follow-up measures are initiated. The reasons for the inclusion of the substance were concerns about consumer use , high (aggregated) tonnage and widespread use as well as the dangers arising from a possible assignment to the group of CMR substances and as a potential endocrine disruptor . The re-evaluation has been running since 2015 and is carried out by Denmark . In order to be able to reach a final assessment, further information was requested.
processing
Epoxy resin products
safety instructions | ||||||||
---|---|---|---|---|---|---|---|---|
Surname |
Bisphenol-A-epichlorohydrin resins with an average molar mass ≤700 g / mol |
|||||||
CAS number |
25068-38-6 |
|||||||
|
Epoxy resin is usually supplied in two components that the user has to mix ready for use. The so-called “A component” usually contains the epoxy resin, the “B component” the hardener, which must be added to the resin in a predetermined mixing ratio.
Usually, epoxy resins bear the GHS symbols GHS07 ("Warning") and GHS09 ("Dangerous for the environment") and the corresponding H and P statements. The amine -based epoxy resin hardeners that are widely used must usually also be marked with GHS symbols (often GHS05, "caustic") and also with H and P phrases. Since the hazard and safety information varies depending on the product and hardener type used, special attention must be paid to the safety data sheets for the products used.
Protective equipment during application
Since direct skin contact is far more harmful than absorption through the respiratory tract (e.g. due to insufficient ventilation), personal protective equipment is mandatory when using many epoxy products. Only special nitrile or butyl, butyl / viton and PE laminate gloves are suitable for skin protection . Thin disposable gloves are unsuitable regardless of the material (e.g. latex, vinyl or nitrile). The allergenic substances penetrate these gloves without damage within a few minutes, while the self-protection of the skin is weakened by perspiration in the absence of ventilation. Skin protection ointments also do not offer acceptable protection. Under certain circumstances, it may also be necessary to wear a protective suit.
operation area
With regard to the use of epoxy resin systems, depending on the area of application and area of application, there may be additional - including legal - requirements for safety and health, e.g. B. in the areas of children's toys , drinking water , food contact items, etc.
Osh
The ingredients of epoxy resins have sensitizing properties. In the event of unsuitable working methods, the processor can be sensitized, after which allergic reactions in the form of skin rashes can occur, especially when they come into contact with uncured epoxy resins. In order to develop ways of avoiding allergic skin diseases caused by epoxy resin, various working groups were founded and research projects initiated. The results of this work so far can be found on the epoxy resin page of the Federal Institute for Occupational Safety and Health.
literature
- Walter Krauss (ed.): Kittel: Textbook of paints and coatings. Volume 2: Binders for solvent-based and solvent-free systems, 2nd edition, Hirzel Verlag, 1998, ISBN 978-3-7776-0886-0 .
- Barbara Schmid, Jürgen Wehde, Ursula Vater: Information on hazardous substances and risk assessment when processing epoxy resins. In: Hazardous substances - keeping the air clean. 70 (1/2), 2010, ISSN 0949-8036 , pp. 17-21.
- Edward M. Petrie: Epoxy Adhesive Formulations. Mc Graw-Hill Verlag, 2006, ISBN 0-07-145544-2 .
Web links
- Plastics to get to know: epoxy resins. FU Berlin - Inst. F. Chemistry and Biochemistry, Berlin 2001
- MATERIAL ARCHIVE: Epoxy Resins. - Extensive material information and pictures
- The Chemistry of Epoxide. Polymer Science Learning Center (PSLC), The University of Southern Mississippi - The Department of Polymer Science, Hattiesburg (Mississippi USA) 2005; Easily understandable explanation.
- Practical guidelines from the construction industry association for handling epoxy resins.
- Guideline of the Hamburg office for occupational safety for risk assessment of epoxy resin systems with information on protective measures. (PDF; 814 kB).
Individual evidence
- ↑ Hans-Dieter Jakubke, Ruth Karcher (Ed.): Lexikon der Chemie. 3rd volumes, Spektrum Akademischer Verlag, Heidelberg, 2003, ISBN 978-3-8274-1151-8 .
- ↑ German Institute for Standardization: DIN-Term coating materials. Vincentz Network, 2001, ISBN 978-3-87870-721-9 , p. 65, limited preview in Google Book Search.
- ↑ a b c d e f Ha Q. Pham, Maurice J. Marks: Epoxy Resins . In: Ullmann's Encyclopedia of Industrial Chemistry . August. doi : 10.1002 / 14356007.a09_547.pub2 .
- ^ Wolfgang Kaiser : Synthetic chemistry for engineers. 3rd edition Hanser, Munich 2011, ISBN 978-3-446-43047-1 , p. 437 ff.
- ↑ L. Hammerton, ed. By Rebecca Dolbey: Recent Developments in Epoxy Resins. RAPRA Review Reports, 1996, ISBN 978-1-85957-083-8 , p. 8.
- ↑ Epoxy adhesives (PDF; 757 kB), on panacol.de.
- ↑ M. Beyer, W. Boeck, K. Möller, W. Zaengl: High voltage technology: Theoretical and practical foundations. Springer Verlag, 1992, 362 pages, ISBN 978-3-540-16014-4 (reprint), p. 206 f.
- ^ H. Schürmann: Constructing with fiber-plastic composites. 2nd edition, Springer-Verlag 2007; 672 pages, ISBN 978-3-540-72189-5 , p. 269.
- ↑ Technical data sheet for ER2074 from Electrolube p. 2. (PDF; 93 kB), on files.voelkner.de, accessed on January 28, 2017.
- ↑ Temperature-resistant epoxy casting resin with high thermal conductivity, press release from Kyocera.
- ↑ Tech Tip 18: Understanding the optical properties of epoxy applications (PDF; 353 kB), Kummer Semiconductor Technology.
- ↑ Green coatings for better visibility of bike paths in Berlin. Retrieved April 25, 2019 .
- ↑ Community rolling action plan ( CoRAP ) of the European Chemicals Agency (ECHA): 2,2 '- [(1-methylethylidene) bis (4,1-phenyleneoxymethylene)] bisoxirane , accessed on May 20, 2019.
- ↑ a b Safety data sheet Epoxy Resin L (PDF; 119 kB), from R&G Faserverbundwerkstoffe GmbH, accessed on May 6, 2013.
- ↑ BAuA - Epoxy Resins website of the Federal Institute for Occupational Safety and Health .