flywheel

A flywheel (also known as a flywheel ) is a machine element . It is used, among other things, as an energy store for kinetic energy ( rotational energy and mass inertia ) by storing its rotational movement ( rotation ) with the lowest possible friction loss for use when necessary; For details see flywheel storage .
In the case of crank drives , the flywheel is used to compensate for vibrations and to overcome the upper and lower dead center with no jerk .
Flywheels are also used to stabilize the position of satellites ( spin stabilization , spin wheel ) and aircraft ( gyrocompass ) as well as in toy gyroscopes .
A flywheel stores the rotational energy :
with its moment of inertia at the angular velocity . The moment of inertia is determined by the structure of the flywheel: the more massive the flywheel and the larger its diameter, the greater its moment of inertia.
Applications
Energy storage

Applications include reciprocating piston engines , especially 1-cylinder four-stroke engines. These only have a work cycle every fourth half revolution , which transfers energy to the output via the crankshaft . In the remaining three cycles, they need energy to maintain the rotary motion and to compress the combustion air. The energy of the work cycle is temporarily stored in the flywheel and then continuously released again.
The simplest small toy vehicles manage without spring accumulators and travel typically 3 m with a flywheel drive alone. The flywheel consists of 1 to 3 punched circular discs with a diameter of 2 to 4 cm, made of 1 to 2 mm thick sheet iron, punched and pressed onto a steel axle that is mounted in sheet metal or plastic.
Another application is flywheel storage power plants with a modular design to compensate for sudden increased demand in electricity networks . For storage, a flywheel is driven by an electric motor and the energy is kept available in the form of rotational energy for energy output in the minute range.
In the ASDEX Upgrade fusion experiment , a flywheel generator weighing 400 tons is used, which takes a few minutes to accelerate from 800 to 3000 revs and then call up the stored energy within fractions of a second to heat the plasma.
In 2004, a self-sufficient power grid was built on the Norwegian island of Utsira , with a flywheel storage system (5 kWh) compensating for short-term power fluctuations. The centrifugal masses of all turbines and generators running (synchronously) in the grid power production are important for stabilizing the grid frequency, i.e. energy storage for a period of the order of magnitude of a phase of 1/50 of a second. The centrifugal mass of electric motors for smoothing the torque output means something similar. By means of flywheels in large stationary machines, only amounts of energy can be stored mechanically locally that are used up in pressing, forging , punching, rolling and cutting processes in typically half a second, only to be replenished by an electric motor in several seconds.
Attitude stabilization
Rotating flywheels do not allow any changes in the angle of their axis. This is used to stabilize z. B. in gyrocompasses for ships and the devices referred to as momentum wheel or inertia wheel in satellites .
Rotational irregularity, torsional vibrations
In many dynamic processes on machines, rotational irregularities (fluctuations in speed) occur. These are caused by periodically occurring torques and can lead to torsional vibrations. Due to their inertia, flywheels reduce the rotational irregularity by absorbing energy when accelerating and releasing it when decelerating. The rotational irregularity is lower as a result. The disadvantage is that a large mass has to be set in motion, which means additional weight in vehicles. Therefore, attempts are usually made to keep the irregularity low (for example in internal combustion engines with several cylinders) or to reduce the torsional vibration itself in other ways (vibration damping).
A vibration damper consists of a flywheel and a damping element (such as oil or rubber) that transfers the vibration-damping forces between the flywheel and the component to be damped. The vibrating part "supports" itself, so to speak, via a damping element on the calmer rotating mass. The damping element converts kinetic energy into heat and thus withdraws the kinetic energy (vibration energy) from the vibrating component.
(Actually for vibration damping amplitudes a flywheel in the engine of was first used decrease value) BMW - motorcycle BMW R 69 S from year 1960 to prevent the previously frequent crankshaft breaks due to vibrations in the high-load engine. Here, a small flywheel on the side opposite the clutch at the front of the engine reduced the rotational irregularity of the vibratory crankshaft-flywheel clutch system.
A similar special form of the flywheel in a car is the so-called dual mass flywheel . The use of a primary and a secondary flywheel with an elastic element in between greatly reduces the transmission of engine vibrations to the rest of the drive train (for example, transmission idle rattle). The primary and secondary flywheel masses are separated from each other by a precisely coordinated spring / damper system. The flywheel on the gearbox side (secondary flywheel) is heavier than the flywheel on the engine side (primary flywheel). This increases the mass moment of inertia of the gearbox, which greatly reduces the irregularity, especially at low speeds. The torsional vibration excitation that acts on the drive train is greatly reduced.
The balance of the mechanical watch, in cooperation with the spiral spring, represents a torsional oscillator, the period of which has a high degree of constancy ( isochronism ).
history
Antiquity and the Middle Ages

In ancient times, inertia was used in the form of rotating masses . Spinning whorls made of clay or stone have been documented since the early Neolithic ; B. Achilleion . Simple flywheels were also used on pottery wheels to ensure permanent, uninterrupted and even turning.
In the Middle Ages , wooden flywheels had speeds of around 100 revolutions per minute and were sometimes able to maintain rotation for several minutes . The flywheel as a general machine element for storing kinetic energy is first found in the De diversibus artibus (On various arts) by Theophilus Presbyter (approx. 1070–1125), who used it in several of his machines.
Modern times
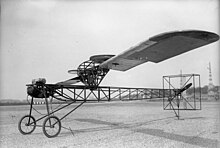
Flywheels are used to compensate for the non-constant torque in steam engines and internal combustion engines . Short-term load peaks in work machines can be compensated for by flywheels and the energy stored therein and often allow a much smaller drive motor, e.g. B. in power generator sets to cover the often very high starting currents in electric motors.
Flywheels were also used in the early development of helicopters . In 1927, in contrast to the gyroscopes and helicopters known up to that time, the rotors of the Zaschka rotary aircraft were inevitably connected to a rotating mass by chief engineer Engelbert Zaschka with a flywheel that was effective at two gyroscopes. This arrangement enabled a safe vertical gliding flight with the engine switched off .
In the 1950s, so-called gyrobuses were in use both in Basel in Switzerland and in Austria . In 1955 a fleet of 12 Gyrobusses was operated in Leopoldsville (then Belgian Congo). The flywheels came from Maschinenfabrik Oerlikon and offered the option of regenerative braking . In the 1990s, buses with flywheel storage were used in Munich and Bremen . These buses obtained their energy for the electric drive exclusively from a flywheel (storage capacity 9.15 kWh). They could travel about 20 kilometers without being connected to the power grid. Then they had to dock to the power grid at breakpoints in order to recharge the flywheel. At the time, this type of energy storage did not prove its worth due to technical inadequacies. Today's flywheels work with magnetic bearings and almost without friction in vacuum housings .
Web links
- Volvo tests innovative flywheel storage technology . Retrieved May 30, 2012.
- DYNASTORE flywheel accumulator . Uli Christian Blessing. March 22, 2012. Retrieved March 22, 2012.
- Diploma thesis by Florian Strossenreuther (PDF; 1.6 MB)
- Development of a magnetically levitated flywheel for AMSAT phase 3-D
Individual evidence
- ↑ Marija Alseikaitė Gimbutas , Shan M. M Winn, Daniel M. Shimabuku, Sándor Bökönyi: Achilleion: a Neolithic settlement in Thessaly, Greece, 6400–5600 BC Los Angeles, Institute of Archeology, University of California 1989, p. 256 (phases IIa-IVa).
- ↑ Lynn White, Jr .: Theophilus Redivivus . In: Technology and Culture , Vol. 5, No. 2 (Spring 1964), Review, pp. 224-233 (233)
- ↑ Lynn White, Jr .: Medieval Engineering and the Sociology of Knowledge . In: The Pacific Historical Review , Vol. 44, No. 1 (Febr. 1975), pp. 1-21 (6)
- ↑ Engelbert Zaschka : rotary wing aircraft. Gyroscopes and helicopters. CJE Volckmann Nachf. E. Wette, Berlin-Charlottenburg 1936, page 47, OCLC 20483709 .
- ↑ Planet e: More energy through flywheel technology. Video in the ZDFmediathek (from 3:30 p.m.), accessed on May 8, 2012 (offline).