Foam
Foams are man-made materials with a cellular structure and low density . Almost all plastics are suitable for foaming . Foams can be compressed, i.e. their volume can be reduced significantly by applying pressure (see compressibility ).
Classification
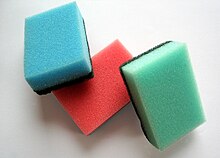
- Closed-cell foam: the walls between the individual cells are completely closed.
- Open-cell foam: the cell walls are not closed, so these foams can absorb liquids .
- Mixed cell foams contain both types of cells.
- Integral foams: They have a closed, thick outer skin and a cellular core, the density decreases towards the inside.
- See also: Reticulating
properties
Foams are characterized by a very low density (here density called) and thermal conductivity with little resistance from. Processing and machining is easy with low tool costs. Due to the internal structure, components made of foam are almost free of residual stress .
Strength and weight
- The strength is in compression hardness z. B. compression hardness 50 = 5.0 kPa at 40% of compression (usually used but inaccurate) or indentation hardness (but unknown meaningful) expressed. For example, the compression hardness of 50 corresponds to approx. 50 g / cm².
- The volume weight is given in kg / m³, also old g / l.
The volume weight z. B. RG 35 ≙ 35 kg / m³ and the compression or indentation hardness are mostly not dependent on each other. Heavy foam does not have to be solid foam. Rather, this depends on the use of raw chemicals, the "weather" (the relative climate during foaming) and the technical skills of the foamer. This results in tolerances . Strength tolerances in the range of ± 15% are accepted from batch to batch and within the batch. The information on foams z. E.g .: RG35 / 50 = volume weight / compression hardness (i.e. 35 kg / m³ / 5 kPa at 40% compression).
Foaming process
Differentiation according to the type of production:
- Physical foaming: The material is foamed by a physical process.
- Chemical foaming: A blowing agent, usually in the form of so-called masterbatch granules , is added to the plastic granulate. When heat is supplied, a volatile component of the blowing agent is split off, which causes the melt to foam.
- Mechanical foaming: Here air is stirred into the resin or paste to be foamed; this foam solidifies by crosslinking the resin or by gelling the paste.
Foam extrusion
When producing PP-E foam (this is also possible for polyethylene , polystyrene , PET or some biopolymers ), propellant gas (e.g. pentane , CO 2 ) is added to the molten polypropylene in the extruder under high pressure . In the past, CFCs were often used as propellants , but their use is now largely prohibited due to their damaging effect on the ozone layer .
When exiting a hole nozzle, the plastic expands to 20 to 50 times its volume. The resulting foam strands can be shortened to foam particles with a diameter of approx. 2-8 mm using rotating knives in the water ring granulator or underwater granulator. They are then separated from the water, dried, conditioned in silos and then processed into molded foam parts in the so-called molding process.
A very important process is the production of foamed foils (e.g. made of PP or PE as impact sound insulation ) or foamed panels (e.g. XPS made of polystyrene). In most cases, however, the continuous extrusion process is carried out with so-called cascade extruders, i.e. two extruders arranged one behind the other. While the plastic granulate is melted ("plasticized") in the first extruder, as already mentioned, after the blowing agent has been added in the second extruder, this blowing agent is mixed in very evenly. In addition, the melt is brought to a defined temperature level (usually a cooling process), after which it is then brought to the approximate width of the later film or plate in a slot die. Due to the lower ambient pressure in relation to the vapor pressure of the blowing agent, the melt expands and is calibrated to the desired plate thickness in a special device. The following units cut the panels to the required size or wind up the film so that the products are then available for further processing.
Molding process
The molding process is used to process foam particles ( EPS , EPP , EPE ) into molded foam parts .
Foam beads with a diameter of approx. 1–8 mm are blown into porous aluminum molds and sintered together using water vapor (approx. 1.2 bar for EPS, approx. 3 bar for EPP). After the cooling and stabilizing phase, the newly created molded parts can be demolded.
This manufacturing process makes it possible to manufacture thermoplastic foam parts in the density range between approx. 12 kg / m³ and 300 kg / m³ with a very homogeneous density distribution over the entire foam part. Direct foaming processes with chemical or physical propellant gases in injection molding do not allow this because of the limited cooling speed with larger wall thicknesses.
The molding process is very energy-intensive , as the tool (mold) and parts of the molding machine (steam chamber) have to be heated up and cooled down again with each cycle (shot) .
Areas of application of the EPP molded parts are z. B. insulated containers, heating insulation, reusable transport packaging and, increasingly, automotive parts such as bumper cores, sun visors, crash pads, toolboxes (which are in the spare wheel rim and hold e.g. trailer hitch, jack and tool kit) or leisure items.
The foam extrusion of particle foams offers the following advantages over particle foams produced in an autoclave :
- Inexpensive production, as one process step is omitted (autoclave treatment)
- Easier and faster color changes
Disadvantages of the extrusion material, on the other hand, are an average higher processing temperature, combined with higher energy consumption and, in some cases, significantly poorer mechanical properties relative to density compared to autoclave material.
Styrofoam process
Expanded polystyrene (EPS) is produced by physical foaming: The blowing agent-containing granulate (5% pentane ) is first pre-expanded to 40 to 80 times its volume by heating with steam at approx. 105 ° C and then between 3 and 48 hours at room temperature temporarily stored so that afterwards the pentane can escape up to a proportion of approx. 3% and air can penetrate. This avoids the creation of a vacuum inside. In the case of finished foaming, the pre-expanded EPS is filled into a mold and expanded by further heating to approx. 130 ° C with water vapor, i.e. it fills the mold and the individual particles melt together at the edges. In the case of large block molds, a vacuum is usually applied before the steam is introduced in order to encourage the EPS particles to expand.
The density is determined by the degree of pre-expansion. However, if this is too large, the finished product will collapse.
Thermoplastic foam casting process (TSG)
By adding blowing agents to a number of thermoplastics , including those with fillers ( glass or carbon fibers ), foam structures can be created in injection molded parts. Depending on the type and consistency, the blowing agents can be mixed with the granulate in a few percent or pumped into the melt in the cylinder in a liquid state under high pressure. In the core, the resulting molded parts have a foam structure and a largely compact outer skin towards the surface. The method is used to e.g. B. to provide thick-walled parts of injection molded parts with a foam core in order to avoid sink marks up to the internal foaming of relatively thick-walled molded parts in order to be able to save weight without having to reduce the wall thickness. The method is used for wall thicknesses from 2 mm, but mostly for wall thicknesses between 4 and 20 mm.
The pressures required for the injection process into the tool and the holding pressure are considerably lower than for normal injection molding. The machines are usually only equipped with injection pressures of up to approx. 1000 bar. The large shot weights are often implemented with piston injection units that are filled by a preplasticizing screw. A holding pressure can usually be omitted, since the contour formation in the tool cavity takes place through the expansion of the propellant. Apart from the last mentioned difference, the process is basically very similar to normal injection molding. Any normal injection molding machine can be used for the process.
The TSG process is suitable for creating particularly rigid constructions, as any wall thickness differences can be produced without sink marks. Often several tools are injected one after the other on rotary table machines. This improves output despite long cooling times (due to the large wall thicknesses).
PUR foams
In contrast to the Styrofoam process, liquid, reactive raw materials are used by the processor. If polyols are mixed with isocyanates and the propellant (usually water), the polyol reacts with the isocyanate in a polyaddition to form PUR ( polyurethane foam ) and the propellant forms gas inclusions (with the propellant water, this reacts with part of the isocyanate, releasing carbon dioxide ). Additives such as the blowing agent are added to the polyol, so that two components are usually used.
The properties can be adjusted depending on the selection of the starting materials. Thus, when using long-chain polyols, soft to elastic foams are obtained, or when using short-chain polyols, strongly crosslinked hard foams are obtained.
The main process is continuous tape foaming and the two discontinuous RSG (reaction foam casting) and RIM (reaction injection molding) or low-pressure and high-pressure processes, with the latter becoming more and more widespread.
In the case of discontinuous processes, it must be ensured that ring lines are installed to prevent "sticking out" or segregation. B. the isocyanate should be warm above 15 ° C, otherwise it will crystallize. A cleaning system should also be provided for the mixing head to prevent it from sticking.
RRIM
With RRIM (Reinforced Reaction Injection Molding), two components ( polyol and isocyanate ) and a reinforcing material (e.g. glass fiber , carbon fiber , rock powder) are mixed in the so-called mixing head and injected under high pressure into a molding tool. After the exothermic reaction of the components, the thermosetting plastic polyurethane was created and can be removed from the tool. Application examples are outer skin parts in the automotive industry, such as fenders, rocker panels and bumper covers. One advantage of polyurethane over thermoplastics is its relatively high heat resistance.
MuCell process
In the MuCell process, an inert gas (either nitrogen or carbon dioxide) is fed to the thermoplastic polymer melt and mixed in the melt cylinder to form a single-phase solution. When this single-phase solution is injected into the cavity of the injection molding or blow molding tool, or during extrusion when it exits the nozzle, the mixture experiences a pressure drop, which means that the gas nucleates over the component and millions of tiny cells grow. These cells then replace a defined volume, which leads to a reduction in density in the component.
Recent developments
In conventional manufacturing processes, foams are often obtained from polymer melts and gaseous blowing agents. An alternative is to use microscopic stencils (so-called templates ) to give the foam the right structure. For example, tiny water droplets can be finely dispersed in a monomer solution and removed after the polymerization. Another method uses particles to stabilize air bubbles in the reaction mixture. A newly developed process for the production of expanded polystyrene is based on the polymerisation of foamed oil-in-water emulsions . Styrene (oil phase) is first emulsified in an aqueous phase. Then the emulsion stabilized by an anionic surfactant is foamed with nitrogen. This creates foam bubbles surrounded by tightly packed drops of emulsion. In the final step, the polymerization is triggered by exposure to UV light. The emulsion droplets react while the structure of the foam is retained. The resulting polymer foams contain pores that are partially interconnected. This enables air, fluids or other materials to flow through the foam, which makes the application for filter materials or bio-inspired framework structures interesting.
Examples
- Thermoplastic foams (e.g. PS-E , PP-E and PVC-E )
- Elastomer foams (e.g. PUR flexible foam , NBR )
- Duroplastic foams (e.g. PUR rigid foam, PF )
See also
- Floral foam
- Cellular rubber
- Blowing agents or foaming agents for the production of foams are described in the English Wikipedia in the article Blowing agent .
Web links
Individual evidence
- ^ EPP forum in Bayreuth: Expanded polypropylene network for EPP
- ↑ Fabian Schüler, Debora Schamel, Anniina Salonen, Wiebke Drenckhan , Michael D. Gilchrist, Cosima Stubenrauch: Synthesis of macroporous polystyrene by polymerizing foamed emulsions . In: Angewandte Chemie . tape 124 , no. 9 , 2012, ISSN 1433-7851 , p. 2256–2260 , doi : 10.1002 / anie.201107806 .