Capacity (economy)
Capacity ( english "capacity" ) is in economics and business administration , the maximum the production process related to a certain period of time available number of personnel , equipment , tools and spaces .
General
Since economics and business administration have different objects of knowledge , the definition of the term capacity has turned out differently. The only thing in common in both disciplines is the maximum efficiency of production factors per unit of time. Economics primarily deals with questions about production potentials and bottleneck sectors that can limit the gross domestic product and capacity utilization. Otherwise, it uses the individual operational capacities provided by business administration within the framework of an aggregation .
Business administration
The capacity of a production system depends on three components, namely the intensity with which production is carried out, the number of units (machines) or the number of workers and the period in which they are used. If the period in which production factors are used is shortened (e.g. by reducing working hours ), the capacity is reduced and vice versa. A long period of time selected for the purpose of capacity measurement shows capacity fluctuations more than a short one.
While the capacity reflects the maximum possible quantity production, the capacity utilization (output quantity) makes statements about the quantity actually produced in relation to the maximum possible quantity. Accordingly, the degree of capacity utilization (or degree of utilization for short) is the percentage at which the capacity assumed to be 100% is actually used. The intensity provides information on whether the capacity can be increased through technical possibilities (increasing the output volume per unit of time) or time options (introducing shift work ). In order to measure capacities, the intensity must therefore remain constant.
species
Business administration describes a large number of types of capacity. Erich Gutenberg and Konrad Mellerowicz have primarily dealt with qualitative and quantitative capacity , but a number of other types are also discussed. Depending on production factors, one can differentiate between work or personnel capacity , procurement capacity and machine capacity . Since operational capital , be it in the form of equity or debt , is also only available to a limited extent, one can also speak of financial capacity . Gutenberg sees a corresponding use of financial capacity for investments . If equity and debt capital are not available, the necessary mechanical investments cannot be made, so that the financial sector represents a bottleneck.
Other types:
-
Quantitative capacity : maximum achievable output quantity at constant intensities within a certain period of time.
- Quantity limitation : the maximum capacity is the technically possible output quantity based on the given technical data of individual items of equipment, without taking economic aspects into account; before the technical capacity is reached, the unit costs rise disproportionately. Many resources have a minimum technical capacity . They are only able to work if they achieve a certain minimum performance limit. Their functional reliability decreases or is even no longer guaranteed if this minimum capacity is not reached. For example, at least two tugs are required for certain seagoing vessels. The optimum capacity is usually between the minimum and maximum capacity and characterizes the output volume at which a resource has the highest efficiency and thus works most economically. Specifically, it concerns the production capacity of a company at the optimal cost point with the lowest unit costs. In the case of volume adjusters with a given market price, the maximum profit capacity is that output volume for which the marginal costs are identical to the price.
- empirical production volume : average and normal capacity . Average capacity utilization in the past is used as a basis for normal capacity.
- Performance evaluation : technical and economic capacity. The economic minimum capacity is associated with an economic minimum utilization, because if this minimum capacity is not reached, the use becomes uneconomical.
-
Qualitative capacity : expresses the highest possible quality and precision with which the existing production factors are equipped for the provision of services; This also includes the mutual harmonization of production factors. Konrad Mellerowicz points out that in flow production, full coordination of the operational elements must be guaranteed. Both the personnel and operating resources capacities have a qualitative component.
- Realizable or available capacity : results from the consideration of personnel ( fluctuation , sick leave ) and machine (maintenance work, malfunctions) downtimes.
Determination of the capacity
For a single production machine, the production capacity can easily be determined. Based on the manufacturer's technical data, the technically possible output of a machine I in 8-hour operation is limited to 9600 production units without any technical errors occurring. This means that this machine can produce 20 pieces per minute; this is the maximum technical capacity. Of these, Maintenance / faults, breaks and debugging the software withdraw so that a technical maximum capacity of 15 pieces / minute remains. However, due to the greater technical wear and tear, it is not opportune to use this maximum technical capacity in the long term. Rather, based on operational experience with other machines of this type, it is assumed that the realizable economic maximum capacity is 12 pieces per minute (i.e. 80% of the technical maximum capacity). The 12 pieces / minute produced are then automatically transported to a processing machine II of a different type, whose maximum economic capacity, however, is only 10 pieces / minute. Then there is a bottleneck sector which also limits the economic maximum capacity of machine I to 10 pieces / minute, unless it makes sense to store the surplus production of machine I.
In general, capacities in passenger transport and freight transport can be precisely measured because the number of seats and the transportable amount of freight, especially in civil aviation, are precisely defined for each type of aircraft . In commercial civil aviation, IATA, as the umbrella association of airlines, publishes the occupancy rates of individual airlines. It differentiates between two business indicators for capacity utilization, namely the seat load factor ( passenger transport ) and the cargo load factor ( air freight ). In its annual report for 2015, Lufthansa reports that its seat load factor (seat kilometers, i.e. sales volumes) was 80.4% and that with 66.3% load factor (tonne-kilometers) it is Europe's leading cargo airline . This means that Lufthansa still has around 19% or 33% market potential worldwide due to underutilized capacities. From these underutilized capacities, the maximum capacity can be determined, both in terms of quantity and sales.
Capacity bottleneck
The bottleneck ( English bottleneck , "bottleneck" ) is a stoppage in the production process, which occurs due to scarce capacity. A bottleneck arises in the production process when the available partial capacities are not sufficient to cope with the production requirements. The possible production utilization then exceeds the available capacity. Capacity bottlenecks can often arise in companies; removing one bottleneck brings about the appearance of other bottlenecks. It is therefore not important to eliminate all bottlenecks, but to coordinate them. This is the subject of congestion planning . The bottleneck determines the maximum possible utilization per unit of time, it limits the performance of the entire chain. The total capacity is limited by the sector with the lowest capacity - the bottleneck. Sectors in which bottlenecks occur are called minimum sectors . The bottleneck in the minimum sector limits the total operational capacity. The minimum sector has an adverse effect on operational performance, which must be eliminated through bottleneck planning. The aim of bottleneck planning is to optimize the production flow. Companies with standardized mass products require a different type of bottleneck planning than those with order-related or one-off production.
Adaptation
Companies can also change their capacity bottlenecks through various forms of adaptation:
- intensity adjustment : production processes are accelerated or slowed down ( assembly line speed , shift work );
- time adjustment : introduction of overtime , short-time work ;
-
quantitative adjustment by increasing or decreasing the production factors.
- selective adjustment by eliminating the less good workers and machines.
- qualitative adjustment by changing the nature of production factors.
Increases in capacity require financial investments in machines and personnel and are usually only carried out if capacities are already fully utilized in the medium term.
Elimination
Capacity scheduling deals with short-term capacity bottlenecks . Strategies for removing bottlenecks are:
- Increase available capacity
- for staff: overtime , jumpers , temporary work , shift work ;
- for products (procurement and sales): warehouse ;
- for machines: production monitoring and time targets for individual production steps, commissioning of decommissioned units.
- Reduce required capacity
- Postpone maintenance measures
- Reduce order backlog
- Awarded to other business economies
Capacity terms
Overcapacity is a capacity that is too high compared to the sales opportunities, which results in reduced profitability and in the longrun can leadto a company crisis. Economic overcapacity cantriggera crisis and depression . Empty capacities are not as can be formed in particular by shortages or excess capacity auslastbare parts of capacity about. The economic maximum capacity of machine II results in an empty capacity of 2 pieces / minute in the example, corresponding fixed costs are called empty costs . Fixed costs are associated with the capacity created (time wages for the workforce, machine depreciation , interest on loans ), which are also incurred without production. These costs are also called standby costs, which decreaseonly disproportionatelywith a decline in employment ( cost retention ). The higher the proportion of fixed costs in the total costs (companies with high fixed costs such as airlines ), the higher the existing capacities have to be used in orderto reachthe break-even point . Usable capacities are corresponding to the part of the capacity that is fully utilized. Capacity reconciliationor capacity leveling is the leveling of the available capacity with the capacity requirement (see: Resource Requirements ).
National economy
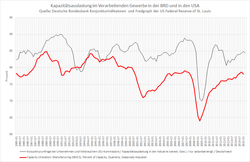
While the operational production potential can usually be determined relatively reliably, as it is usually technically specified, the calculation of an economic production potential is extremely difficult because it cannot be clearly determined when the full capacity utilization of all production factors will be reached. The production potential corresponds to the production capacity (total economic output) of an economy with normal employment of all economic production factors. The Council of Economic Experts considers a normal utilization of the production potential as given when the existing production factors are utilized to 96.75%. In its annual report 2003/2004, the Council of Economic Experts described what is to be understood by economic growth, namely a long-term development of gross domestic product with full or at least normal utilization of all capacities, i.e. the change in production potential. The lower the potential growth, the more likely an upswing will hit existing capacity limits. “The degree of utilization of the production capacities can be used as a benchmark for the economic situation of the industry”. Then the term of the economy ultimately describes the state of the degree of utilization of the overall economic production capacity. Capacity utilization is one of the general economic indicators . The data on capacity utilization ("capacity utilization"; in percent of full capacity utilization) in industry in the European Monetary Union are collected by the European Commission every quarter in the European Union as part of harmonized business surveys. The economic research institutes indicate capacity utilization as a percentage of the production potential.
Against this background, some empirical figures show the capacity situation of the German economy. The loss of capacity of the German economy as a result of the Second World War in the three western zones in 1948 was only 15.4% of the capacity in 1936, 8.1% of which was due to war destruction and 7.3% to dismantling by the Allies, while the production capacity was fully utilized 1932 was only about 45%. After the start of the financial crisis in 2007 , capacity utilization in the manufacturing sector in Germany fell from 88.2% to the low point in 2009 to 70.2%, before returning to the level of 83.2% in 2013.
See also
Web links
- Capacity utilization of US industry (English)
Individual evidence
- ^ Hans Corsten, Ralf Gössinger: Production economy. 12., completely revised. and exp. Edition. Oldenbourg, Munich 2009, pp. 10-14
- ↑ Kurt Wille, capacity determination in the company , 1985, p. 27 f.
- ↑ Carl Ruberg, Concept of operating capacity and its measurement in trading companies , in: ZfB 1953, p. 465 ff. With further evidence
- ↑ Erich Gutenberg, Fundamentals of Business Administration, Volume 3: The Finances , 1969, p. 333.
- ↑ In the case of credit institutions, the financial value sector is even an independent production factor.
- ↑ Heinz-Josef Bontrup, Economics: Fundamentals of Micro- and Macroeconomics , 2004, p. 229.
- ↑ Peter Metge, Transport Science Research: The Structure of Port Shipping , 1964, p. 78.
- ↑ Holger Beckmann, Process-Oriented Supply Chain Engineering , 2012, p. 235.
- ↑ Joachim Funk / Herbert Hax / Erich Potthoff (eds.), Capacity Risks and Corporate Policy , in: Zeitschrift für Betriebswirtschaftliche Forschung, special issue, Volume 18, 1984, p. 27
- ↑ Konrad Mellerowicz: General Business Administration , Volume 2. 1954, p. 38 f. ( limited preview in Google Book search).
- ↑ Jörg Rösner, Service , 1998, p. 41.
- ↑ Lufthansa Group, Annual Report 2015 , p. 198.
- ↑ Lufthansa Group, Annual Report 2015 , p. 50.
- ↑ Charles T. Horngren / George Foster / Srikant Dalar, cost accounting: Decision-oriented perspective , 2001, p 661st
- ^ Hans Bartels in: Lexikon der Unternehmensführung , 1973, p. 65.
- ↑ Torsten Becker, Processes in Production and Suplly Chain Optimizing , Volume 10, 2008, p. 54.
- ↑ Erich Gutenberg, Fundamentals of Business Administration , Volume One, 1963, p. 164.
- ^ Rolf Bühner, Betriebswirtschaftliche Organizationslehre , 2004, p. 264.
- ^ Corsten: Production Management 6th Edition, p. 608, Figure 208.
- ↑ Klaus Ritterbruch, Macroeconomics, 11th edition, Munich 2000, p. 136.
- ↑ Expert Council, Report 2003/2004 , p. 109.
- ↑ Expert Council, report 2003/2004 , p. 1.
- ↑ JD Lindlbauer, capacity utilization partially still unsatisfactory , in: ifo Schnelldienst 29 (24), 1976, pp. 6-7.
- ↑ Josef Puhani, Economics: Basic Knowledge , 2003, p. 127.
- ↑ DIW Berlin, capacity utilization in manufacturing in% of production potential
- ↑ Heinz-Josef Bontrup, Economics: Fundamentals of Micro and Macroeconomics , 2004, p. 133
- ↑ Josef Puhani, Economics: Basic Knowledge , 2003, p. 93
- ↑ TradingEconomics of November 15, 2013, Germany