Offset (mining)
The miner describes material for filling underground cavities as offset . The introduction of these materials is called offset .
need
Offset is primarily used to stabilize the hanging wall . When mining sedimentary mineral resources (e.g. from coal seams), the lowering of the hanging wall in the Altes Mann basically leads to subsidence on the surface of the day. For various reasons (buildings, bodies of water, etc.) it may be necessary to minimize these subsidence. Depending on the offset technology used, it is possible to reduce the depressions to approx. 10–15%. Another reason to introduce offset results from the geology of the deposit, if z. For example, by caving would enter stock losses because other parts of the deposit would then be mechanically mountain no longer dominates. Finally, there is a third reason for the introduction of backfill if a high proportion of tailings occurs during dismantling , which must remain underground for reasons of cost or due to a lack of stockpile fall capacity . This type of offset is called self- offset and is mainly used in gangue ore mining (ridge construction). If the excavation cavities remain without offset, but are filled by breaking up the roof layers, this is known as fracture construction .
A relatively new type of backfill is the backfilling of exploited underground mines with non -mining hazardous waste. This is not technologically necessary, but mainly serves for disposal. Decommissioned mines that are only used for waste disposal are sometimes referred to as backfill mines or underground landfills .
Types of offset
Full offset / partial offset
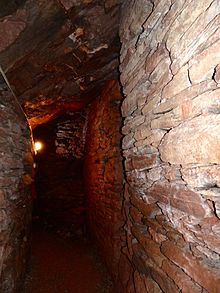
If the entire cavity is offset, it is referred to as full offset ; only parts are filled in by partial offset . In the case of partial offset, either (in the case of chamber-pillar construction with offset) only the chambers are fully offset and the piers obtained thereafter are left unmoved, or the offset is not introduced in full - for example in longwall construction.
Degree of filling
The degree of filling is defined as the ratio of the volumes of the introduced backfill material to the original cavity.
Manual offset
Manual offset is the oldest type of offset. When mining ore veins, which are guided in a floating manner (i.e. from bottom to top), there are usually enough mountains for self-displacement. If this is not the case, backfill material has to be added either from other mines or from above ground. This is especially the case when the gear is very powerful and completely won. Mountain mills are occasionally opened up to obtain backfill , mostly when the self-backing is temporarily insufficient due to fluctuating thickness. On the Rammelsberg , the communion quarry, the so-called slate mill, was set up to extract offsets above ground. While the introduction of the offset in the above-mentioned steep deposits is naturally easy, since the mountains almost reach the desired location by gravity and only have to be leveled occasionally; In addition, the offset serves as a work platform, a lot of manual work has to be done when moving flat-bedded dismantles. If the mountains are shoveled in, the degree of filling is approx. 40–50%; if they are put in like a dry stone wall, the degree of filling is up to 70%.
Blind location offset
The blind location offset is a staggering method of the hard coal mining, which was used in shallow, up to 2 m thick seams. The blind location shift was mainly used for striking longwall mining with floating or striking cutting .
method
Blind spots are tracked in the already charred area of the strut. The distance between the blind locations depends on the amount of offset required and is between 5 and 8 meters. The cross-section of the blind location is adapted to the mountain conditions and barely exceeds 8 m². The roof of the blind spots is torn down, mostly by drilling and shooting . The resulting mountains are heaped up or stacked to the left and right of the blind locations to form offset walls or pillars.
Advantages and disadvantages
An advantage is the possibility of getting along without foreign mountains and accordingly not needing any falls, mountain transport and the like. The dismantling speed of the strut depends only on the tracking of the blind locations and not on the efficiency of the mountain transport for the dismantling.
The disadvantage is the difficult weather conditions, as the charred face is not completely relocated, which leads to a lot of creeping weather . This affects the fresh weather supply for the face crew and worsens their working conditions. In addition, the blind spots are a major source of danger, as firedamp accumulations often form under their roofs. Furthermore, there were often pit fires due to the spontaneous ignition of residual coal that was not completely extracted in the blind areas, which, if they did not cause a major mine fire, were difficult to fight and their CO and CO 2 emissions endangered the workforce.
The blind location offset can only be used meaningfully in partially mechanized struts, in which coal is extracted with a pick hammer. In today's fully mechanized mining, this offset method can no longer be used or only at high cost. These struts are usually carried out as broken structures. A second, perhaps even more important reason for not using the blind location offset is the high risk mentioned above. In 1956, only 4% of West German hard coal production was generated from mining with blind location.
Blow offset

Blasversatz was first used in Germany in 1924 by the German trade union . It is so called because the mountains are blown into the excavation cavities using compressed air according to the injector principle. The air flow serves as a carrier medium here. For this reason, this method is particularly suitable for rolling material of medium grain size. Pieces over 65 mm in size and / or sharp-edged pieces are not suitable because they have a poor surface / weight ratio, which makes it difficult to carry them in the air stream. In order to mix the mountains with the air flow, blow molding machines are used, which have the task of metering the material to be packaged while avoiding compressed air losses. There are two basic principles: the chamber design and the cellular wheel design. The former is particularly suitable for installation in roller holes or blind shafts; Once the hermetically sealed bunker has been emptied, the offset work must be interrupted in order to fill the bunker again. The cell wheel machine, in which a cell wheel with six chambers rotates around its horizontal axis, enables continuous displacement work, the displacement material being fed into the upper chamber and entering the displacement line from the lower chamber, so that an essentially uniform displacement flow is achieved .
Blow staggering was previously used in all mining branches, but it is inherently very expensive because compressed air is the most expensive underground energy source. For this reason, blow offset is now only used where flushing offset is not applicable, e.g. B. in salt mining.
The achievable degree of filling is around 60–70% when stored flat .
Flush offset
Flush offset is an offset method with which fill levels of up to 90% can be achieved under good conditions. The items to be washed are usually fine-grained, typically sand or gravel sand. Mountains are used less often.
Introduction of flushing offset
The backfill is mixed with water for days and fed to the excavations to be moved via pipelines. The workings have previously with offset or dams and drainage offset canvas against the other workings devious be and for the emptying of the offset line is a Abfahrort provided. Furthermore, the water draining from the excavation must be collected and - possibly via a primary treatment - fed to the dewatering. If the dismantling or the offset section is fully flushed, the line is shut down. After the water contained in the wash ware has drained off, there is a volume reduction of approx. 10–20%. The resulting residual cavity either remains open or - if necessary for mechanical reasons - is refilled.
Self-hardening offset
Self-hardening offset is a sub-form of flushing offset. A binding agent is added to the sand / water mixture. This can be cement; For cost reasons, hard or lignite filter ash (power station ash) is often used. A kind of lean concrete is produced. Self-hardening backfill is the most expensive variant of all backfill types and is used where complete dismantling of the deposit is desired. In Germany, this was particularly the case in the uranium mining of SDAG Wismut. The self-hardening backfill was used here on the one hand in the Thuringian area around Ronneburg, on the other hand in the Königstein mining company. The mining method used in Thuringia was partial level construction with offset (TmV). Here, irregularly shaped ore lenses were mined into disks from top to bottom. The dismantled part of the floor was moved, then the offset was driven under and used as an artificial roof, as it had better and above all defined rock-mechanical properties than the actual hanging wall. In Königstein, the process of building piers with an offset was used. In doing so, parallel locations (the chambers) are initially driven upwards or downwards from the device routes. Then the places are moved and then the pillars that remained between them are recovered. Here the offset serves as a joint and support for the hanging wall. The pillars were also relocated or just hermetically sealed in order to keep radon levels within limits.
Self-hardening backfill is also used for the rehabilitation and safekeeping of mine structures where water permeability is not desired for various reasons. When manholes are stored, sagging of the backing column and a possible break in daylight can be excluded.
Self-hardening backfill is also used nationwide to secure and store old mines.
Spin offset
The backfill is conveyed by a conveyor belt to the location where the backfill is placed and thrown into the space to be filled with a high-speed centrifugal belt (approx. 10–15 m / s) that runs at an angle of 90 ° to the conveyor belt. The centrifugal displacement machine can be moved on rails that are mounted on the belt support frame. Degree of filling around 60–70%, offset amount approx. 130–150 m³ / h, the nature of the backfill material (piece size) is relatively irrelevant, but should not be too fine-grained due to the formation of dust. The use of centrifugal offset is limited by the collapse, thickness and field width. It is also disadvantageous that the conveyor belt can only be used for the offset material, but not at the same time for coal / ore transport, as is the case, for. B. is the case with the blow offset through the separate delivery line.
Offset with non-mining waste
Non-mining waste is used as backfill material in underground landfills or backfill mines .
In particular in former German salt mines and salt caverns , because of the lack of groundwater influence there, hazardous waste is often stored which, due to its high toxicity and environmentally hazardous properties , must not be stored in an above-ground hazardous waste dump .
Basics
Depending on their properties, the packing materials are either packed in barrels or in big bags (mechanical packing ) and stored in a controlled manner . Liquid waste is introduced by means of hydraulic offset (also known as flushing offset ). The waste is mixed with pit lye and fed into the cavities via our own pipe systems. Furthermore, the bulk material offset is used. Another possible application for filling in salt deposits is the construction of petroleum storage caverns. For this purpose, however, as a rule, not former mines, but specially rinsed salt caverns are used.
The backfilling of hazardous waste in salt mines is recognized within the EU as recovery process R5 in accordance with Annex II of Directive 2008/98 / EC of 19 November 2008 and is currently (as of 2009) only practiced in Germany.
Examples (selection)
A distinction is made between underground landfills (disposal), backfill mines (recovery) and disposal mines. Does the offset serve an economic purpose, e.g. B. the collapse protection by means of air-free backfilling, it is legally not considered as waste disposal , but as waste recycling . Shipment of “waste for recycling” is significantly cheaper for those who want to get rid of it than “waste for disposal”.
Underground landfills
- UTD Herfa-Neurode (Hessen), the world's largest underground hazardous waste dump
- UTD Heilbronn in the Heilbronn mine of the Southwest German Salt Works (Baden-Württemberg)
- UTD Zielitz (Saxony-Anhalt)
- UTD Sondershausen (Thuringia)
- UTD Lower Rhine
- UTD Lower Saxony
Backfill mines
German backfill mines are
- Teutschenthal mine (Saxony-Anhalt)
- Gersheim (Saarland) ceased operations
- Wohlverwahrt-Nammen (North Rhine-Westphalia)
- Bleicherode (Thuringia)
- Bad Friedrichshall salt mine of the Southwest German Salt Works (Baden-Württemberg)
- Stetten (Baden-Wuerttemberg)
- Hattorf
- Walsum (North Rhine-Westphalia)
- Glückauf Sondershausen
literature
- Siegfried Naujoks (editor): The mining manual . Ed .: Wirtschaftsvereinigung Bergbau eV Bonn. Glückauf, Essen 1994.
- Helmut Schaefer: VDI-Lexikon Energietechnik (= technical reference works for the common authority file ). VDI-Verlag, Düsseldorf 1994, ISBN 3-18-400892-4 .
- Bladder displacement systems, prospectus Maschinenfabrik Karl Brieden GmbH & Co., Bochum-Linden
Web links
- Teutschenthal mine. GTS Grube Teutschenthal Sicherheits GmbH & Co.KG, accessed on April 13, 2014 .
- Business areas. Glückauf Sondershausen GmbH, archived from the original on April 13, 2014 ; Retrieved April 13, 2014 .
- Matthias Brendel: Toxic waste as a building material. How German salt and coal mines bury expensive hazardous waste cheaply. Die Zeit , January 27, 2000, accessed April 13, 2014 .
Individual evidence
- ↑ a b Heinz Steffen, Ferdinand v. Praun: The practical miner . 4th edition. Teaching material service, Hagen / Essen 1954, p. 55-57 .
- ↑ Horst Roschlau, Wolfram Heinze: Knowledge storage mining technology . Ed .: SDAG Wismut. 1st edition. German publishing house for basic industry, Leipzig 1974, p. 248 .
- ↑ Stefan Dützer; World cultural heritage Rammelsberg (Ed.): On steel paths. Railways on the Rammelsberg. Goslarsche Zeitung, Goslar 2008, ISBN 978-3-9809704-5-7 , p. 18.
- ↑ Christoph Bartels; Preussag AG Metall (ed.): The ore mine Rammelsberg. Preussag AG Metall, Goslar 1988, p. 70.
- ↑ a b c d Fritz Heise, Fr. Herbst, Carl Hellmut Fritzsche: Bergbaukunde . Textbook of, with special consideration of the coal mining industry. 8th edition. tape 1 . Springer, Berlin 1942, p. 332, 353, 354, 404-408 .
- ↑ These stretches are called blind locations because they have no other function apart from the extraction of backfill material.
- ↑ Kurt Hoffmann et al .: Expertise for the hard coal mining . tape 1 . People and Knowledge, Berlin 1952, p. 124 .
- ↑ Erich Lewien, Peter Hartmann: Technology of mining . Ed .: University of the German Trade Unions "Fritz Heckert". Fachbuchverlag, Leipzig 1958, p. 109 .
- ↑ Suitability of processed lignite fly ash for use as an additive for self-compacting concrete. (PDF; 21.6 MB) Retrieved April 21, 2012 .
- ↑ Pocket calendar for mine officials 1951 . Karl Marklein, Düsseldorf 1950, p. 136 f .
- ↑ Ordinance on the displacement of waste underground (Versatzverordnung - VersatzV). February 24, 2012, accessed April 13, 2014 .