Stone putty

As Steinkitte or mastics are designated in the one German stone lexicon adhesives and putties, the natural stone industry used. Stone glue is also used in various ways . With these systems, natural stones , artificial stones or the so-called composite materials are glued in a force- fit manner , reinforcements are glued into natural panels subject to flexural tension and small holes and pores in rock with a dense structure are cemented or filled.
The stone putties used today are mainly two-component systems based on polyester , epoxy resin, polyurethane and acrylic resin . These plastics can be individually adapted to the tint of the natural stone by adding colors. After the two-component systems have hardened, the natural stone slabs or stone can be processed, sawed, ground and polished.
Demarcation
According to DIN EN 923, adhesives are defined as “non-metallic substances” that connect materials. Stonemasons use the historical term stone putty when they fill pores or glue slabs with cracks or glue slabs together. The term stone putty is still in use today. Since the 1980s, silicate adhesive systems have been used in the preservation of monuments for restoration work. If the term stone adhesive is used, it should not be confused with tile adhesive , which is a special mortar for laying ceramic and natural stone tiles .
Historical methods
Since the bonding strength of historical putties was low, successful use of historical adhesive and putty systems primarily required experience. The hardening time of the masses often took long periods of time, and rapid drying caused cracks to form. In addition, some of these substances were toxic. In 1952, the Akemi company from Nuremberg, in cooperation with a chemical company, developed a stone adhesive based on polyester , which Akemi called Stone and Marble Putty Universal . With this two-component adhesive system, the use of historical stone putty ended. Akemi is active worldwide (as of 2017) and sells stone putty and other similar products for natural stone in 90 countries. Akemi has offices in the United States (Atlanta), Brazil (Sao Paulo), India (Bangalore) and China (Beijing).
Soft rock
Limestone, marble and other soft stones
For bonding and cementing limestone , marble and soft stone , baked magnesite and liquid chlorine magnesium stone putties were made, the chlorine magnesium stone putties. The putties made from burnt magnesite and chlorine magnesium were called patent putties. Stone powder and stone gravel were added to the patent putties. They were suitable for cementing limestone and sandstone with stone-cut stone surfaces. These putties could be matched in color with stone flour and earth colors. There were also putties made from glycerine with the addition of black lead , the so-called black lead-glycerine putties. Resin and wax were also melted into a paste, plaster of paris mixed with it, and the breakpoints glued together. The break points had to be heated accordingly before the paste was applied. These putties were toxic.
But egg white or quark were mixed with marble dust and unslaked lime as putty. Water glass was mixed with Portland cement , slaked lime, fine sand and kieselguhr . The break points did not have to be heated.
There was also the so-called marble cement on the market. With this adhesive system, the breakages and defects did not have to be heated.
Sandstone
For the cementing of sandstone, 20 parts of dry, fine sand, 2 parts of lead oxide and 1 part of slaked lime were mixed. This mixture mixed with linseed oil varnish or linseed oil . There were also mixtures of this type with kieselguhr . The patent putty mentioned above was not only suitable for limestone, but also sandstone.
Hard rock
In hard stone cracks were filled with water glass . Shellac was dyed and hard rock dust was mixed in to fill imperfections . The mass was heated and then applied.
Today's adhesive and filler systems
Adhesive and filler systems for natural stone that are used today are based either on polyester systems or synthetic resins (epoxy and acrylic). They are made up, in contrast to the historical stone putties.
polyester
In the 1950s, stone putties came on the market that replaced the historical adhesives. For example, they had the trade names Akemi, Granidur, Helco, Ultra-Rapid etc. The putty called Akemi was so widespread that this trade name was included in the only German-language natural stone dictionary. With these adhesives it was possible to permanently glue or cement natural stone. The basic mass of the stone putty is mixed with the addition of a hardener, which sets a polymerisation process in motion. The hardening process can be regulated depending on the addition of the hardener. Before the compound is applied, the fracture surfaces to be connected must be dry and free of dust. The cement itself is harder than marble and the fracture points have at least the same tensile and compressive strength as the fragments. These masses were adapted for special uses, for example with regard to transparency, fillings of porous stone, adhesions, kneading putty, etc. These polyester-based adhesives were particularly suitable for interiors, as they only fulfilled their purpose to a limited extent when exposed to frost and moisture.
In the natural stone production porous Steinplattenrohstücke in the course of industrial processing will sanding lines (z. B. in between the coarse and fine grinding processes with a so-called Kittstrecke by application of polyester putty Jura marble ) treated, of the pores prior to subsequent grinding passes by means of a doctor blade closes . Before applying the leveling compound, the natural stone slabs must be dried, as the sanding operations are carried out with the addition of water. For faster hardening of these masses, UV ovens integrated into the processing lines are usually used after the dosing and filling systems.
Synthetic resins
With the development of epoxy and acrylic resins, stone putties were created that achieved significantly higher tensile strength values and were more weather-resistant than the polyester-based stone putties. With the development of synthetic resin-based adhesives, it was also possible to combine metals with natural stone with high tensile strength values.
Epoxy resin
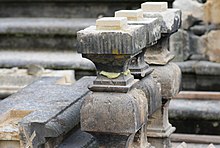
Stone adhesives based on epoxy resin made permanent bonding and anchoring of natural stone slabs possible, even on external facades. These adhesive systems thus enable a permanent connection in areas that are subject to weathering in general and a freeze-thaw cycle. For restoration work on natural stone, epoxy resin-bonded stone substitutes are also produced from pigments and quartz sands, which, when properly processed, achieve high adhesive strength values. When applied to the respective purpose, the special and precise mixing ratio of hardener and compound is important.
The putties with the trade names Akepox and Akemi Marmorkitt have also proven themselves in the restoration. They were used, for example, for restoration work on the Pergamon Altar and for gluing figures of the great clay warrior army in the Qin Shihuangdis mausoleum .
Another application is the so-called resinizing ("setting") of natural stone. Stone slabs are soaked with epoxy resin before they are polished, with the result that cracks in the slabs and microcracks in the minerals are filled and connected with a force-fit connection. If necessary, the synthetic resins are tinted appropriately with dyes.
When using epoxy resin, personal protective measures must be taken, whereby the wearing of suitable protective gloves is particularly important.
Acrylic resin
Two-component stone putties, which are based on highly viscous, liquid reaction resins containing methyl methacrylate , can be used for the frictional connection of cracks and filling of open-pored stone surfaces as well as for the production of stone substitute compounds.
There are, however, also photoinitiated hardening acrylates which are one-component and are mainly used to remove damage to kitchen worktops .
restoration
When the temples of Abu Simbel were rebuilt, Akemi marble putty was used and the low-strength blocks made of Nubian sandstone were reinforced with 33 tons of epoxy resin.
Applications
All natural stones can be glued and cemented. The main application of these systems is in the building industry ( window sills , stair coverings and kitchen worktops made of natural stone, which are glued or filled).
Basically, the cement and glued areas must be dry and dust-free when used. With epoxy resin-based putties, there may be some residual moisture in the stone. The ambient temperature and the ratio of base material and hardener have a decisive influence on the duration of hardening. The stone putties can be colored to match the natural stone used. Rock powder, sand and rock fragments can also be inserted into the putty, which can then be handcrafted, ground and polished after hardening. When preparing the masses, a distinction is made between viscous, liquid and thin.
Web links
Individual evidence
- ^ Albrecht Germann, Ralf Kownatzki, Günter Mehling (eds.): Natural stone lexicon . S. 187. 5th completely revised and updated edition. Callwey, Munich 2003, ISBN 3-7667-1555-0
- ↑ History , on akemi.de. Retrieved June 30, 2017
- ↑ Albrecht Germann, Ralf Kownatzki, Günter Mehling (eds.): NatursteinLexikon . S. 275. 5th completely revised and updated edition. Callwey, Munich 2003, ISBN 3-7667-1555-0
- ↑ a b c Moritz Klein: The marble and its use for building and craft purposes . P. 31. Fifth enlarged and improved edition. Publishing house Bernhard and Friedrich Voigt. Leipzig 1909
- ↑ Moritz Klein: The marble and its use for building and craft purposes . P. 56. Fifth enlarged and improved edition. Bernhard and Friedrich Voigt. Leipzig 1909
- ↑ Moritz Klein: The marble and its use for building and craft purposes . P. 46. Fifth enlarged and improved edition. Bernhard and Friedrich Voigt. Leipzig 1909
- ↑ Albrecht Germann, Ralf Kownatzki, Günter Mehling (eds.): NatursteinLexikon , p. 15. 5. completely revised and updated edition. Callwey, Munich 2003, ISBN 3-7667-1555-0
- ↑ It started in a garden shed. Pp. 48-49. In: Tiles & Slabs. Issue 6/2008
- ↑ Albrecht Germann, Ralf Kownatzki, Günter Mehling (eds.): NatursteinLexikon , p. 374/75. 5th completely revised and updated edition. Callwey, Munich 2003, ISBN 3-7667-1555-0
- ↑ Albrecht Germann, Ralf Kownatzki, Günter Mehling (eds.): NatursteinLexikon . S. 343. 5th completely revised and updated edition. Callwey, Munich 2003, ISBN 3-7667-1555-0
- ^ Museum of the Terracotta Army. Final Report 2010-2013 (English), (BMBF Forschungsprojekt / Research project 01UG1001). P. 29 and 85. Edited by the Technical University of Munich and by the Museum of the Terracotta Warriors & Horses of Qin Shihuang, Lintong, China. Retrieved June 28, 2017
- ↑ Technical data sheet. Marble putty super , on centralconnect.de. Retrieved on
- ^ Giovanna Magi: Aswan. Philae, Abu Simbel . Florence 1992, p. 93