Spring contact pin
Spring contact pins ( spring contacts or spring pins for short ) are contacting elements that are used for testing printed circuit boards , electronic assemblies, components such as plug connectors and other components in the electronics industry.
Other areas of application are detachable connections in battery charging stations, battery compartments of mobile electronic devices and similar applications. As the name suggests, the contacting, i.e. the closing of an electrical circuit, is not created by inserting a pin into a socket, as is the case with connectors, but rather by touching it with a spring-assisted pin. Other terms from the technical jargon of testing technology are test pin , test tip , spring-loaded contact , test pin or pogo pin , although the latter is the registered trademark of a US manufacturer. English terms are Spring Contact Probe , Testprobe or Spring Probe , the terms Spring Loaded Contact and Spring Loaded Connector are also used, for which the abbreviation SLC has become established.
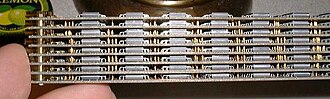
Structure and principle of operation
Except for a few special designs, which will be discussed later, the spring contact consists of three components: a guide tube (also called a pin sleeve or housing), a spring and a piston. The three components are assembled with one another using special crimping techniques in such a way that they can no longer fall apart, but the piston can nevertheless freely perform a certain spring travel in the longitudinal direction. When assembling the individual parts, the compression spring is pre-tensioned, so that the spring contact pin already has a certain initial force in its zero position - usually referred to as pre-tensioning. The spring force assigned to the product as a nominal value is achieved by the contact after the so-called nominal spring deflection , which is usually 2 ⁄ 3 of the maximum possible spring deflection. This nominal spring travel is usually matched to the design of the test adapter in which the spring contact pin is installed.
The shape and size of the actual probe head at the front at the tip of the spring contact pin can vary in great variety. The user often has his own preferences and wishes, which he would like to see implemented, and the different designs of connector tongues, soldering surfaces, etc. require a correspondingly large number of different variants.
Market standards
Maximum spring travel of around 2 mm to 12 mm is customary in the market, depending on the type and structure of the test adapter in which the spring contacts are usually installed. The diameter of the spring contact pins depends on the distance between the test points on the circuit board . This distance is referred to as grid spacing , grid dimension or pitch . The usual distances are 2.54 mm, 1.91 mm and 1.27 mm - each based on the inch system. For example, many connectors have a 1 ⁄ 10- inch (or 2.54 mm) gap between the connector pins. The soldering eyes or vias are then placed on the circuit board at this pitch, and in order to be able to contact them during the electrical test, the spring contact pins must fit into the 2.54 mm pitch. Other standard pitches used today in electronics are 1.91 mm (corresponding to 75 mil or 0.075 inch) and 1.27 mm (50 mil or 0.050 inch).
The corresponding spring contact pins are designed in terms of their diameter based on these spacing dimensions. A standard spring contact for a 2.54 mm grid (i.e. 1 ⁄ 10 inch grid) has a housing diameter of approx. 1.37 mm to a max. 1.66 mm and thus has sufficient distance to the next contact to avoid short circuits .
Receptacles
Another special feature are the receptacles that are commonly used. Since the spring contact pin is used very frequently and is worn out after a certain period of use , it is inserted into a receptacle for easy interchangeability. The replacement can be carried out by simply pulling out the worn contact and inserting a new one. The electrical connection line (soldered or wound using wire-wrap technology ) remains unchanged and unaffected on the receptacle. When calculating the minimum distance in the respective installation grid (pitch), the outer diameter of the receptacle is of course decisive.
Spring force
The spring force of the individual spring contact pin is another variable. Usually there are several different spring force options to choose from within a series. Here, the compromise must be made between reliable contact force on the one hand and the total force of all spring contacts in a test adapter on the other. As a rule, you can achieve reliable contact with soldered test points on an assembled circuit board with a spring force of 1.5 N (approx. 150 grams) or more. If, however, a test adapter has a total of 1,000 spring contacts, this leads to a total force of 1,500 Newtons (or around 150 kg) which the test adapter has to overcome mechanically. In other words: the assembled assembly must be pressed with at least 150 force on the needle bed made of spring contacts in order to establish the desired test contact.
Vacuum adapters are therefore very often used in the quality inspection departments of electronics manufacturers . The vacuum adapter uses a simple physical principle: if the air is evacuated from a sealed chamber, the atmospheric air of the surroundings presses evenly on the walls of this chamber. With the vacuum adapter, the assembly to be tested is, so to speak, the cover of a cuboid chamber and is consequently pressed down with a force of approx. 10 N / cm² (theoretical value at 100% vacuum). In practice a vacuum of 70% to 80% is achieved, consequently this would be 7 to 8 N / cm². The problem with the vacuum adapter, however, is that these values can only be achieved if the vacuum chamber is sufficiently tight. Every small leak immediately reduces the efficiency dramatically. Just as the assembly to be tested represents the “cover” of the vacuum chamber, the needle carrier plate with the installed spring contact pins forms its bottom. As a result, all the receptacles and spring contacts installed in them must be made airtight so as not to destroy the vacuum as a result of many tiny leaks.
Product features
Since the spring contact pin is an essential element in the quality inspection of high quality electronic assemblies , the quality requirements for this component are very high. The most important are:
- The lowest possible ohmic resistance
- Resistance value that is as constant as possible, even over longer periods of use
- Longest possible spring with constant spring force
- A surface that is as dirt-repellent as possible, in order to avoid the build-up of contamination ( flux residues , tin oxides, other substances from the surrounding area) that reduce contact
Special designs for special areas of application enable the transmission of very high currents (20 to 400 A), have a built-in switching function or are suitable for the transmission of high-frequency signals (coaxial spring contacts with shielding).
For the diverse applications in electronics, many different probe head shapes have developed over the past 20 to 30 years, always with the aim of creating a counter surface that is optimally adapted to the contact point. Since there are always new developments in the field of circuit board and assembly technology, there is no end in sight to the creation of new shapes and sizes of spring contact pins.
Certain standards have become established in the global market, but they have not yet been laid down in specific norms or similar standards. Virtually all well-known manufacturers have a certain range of types that are compatible with designs from other manufacturers. This means that the spring contact pins are interchangeable with regard to their geometric size and the spring travel and forces and fit into the receptacles from other manufacturers. In their inner workings, with the surface coatings and base materials used, however, each manufacturer uses its own principle, and this is where the qualitative differences lie. Important manufacturers for these niche products can be found in Germany, Japan and the USA.
Materials / materials
Since the spring contact pin is a contact element, only good electrical conductors should normally be used as materials . Common and commonly used materials are:
- Beryllium copper CuBe for the pistons / probes
- alternatively: in order to increase the mechanical stability, pistons with aggressive head shapes of steel made
- Brass or nickel silver for the case
- Spring steel wire , stainless steel or beryllium copper for the compression spring
surfaces
As with other contact elements - for example in connectors - the individual parts of spring contact probes are given a high-quality surface coating. On the one hand, this is necessary to improve the electrical conductivity; on the other hand, the base materials made of Cu alloys or steels must be protected from corrosion and oxidation . Common surface finishes are:
- Hard gold ( gold plating ), nickel ( nickel plating ) or rhodium for the pistons
- Hard gold for the housing and receptacles
- Silver or gold for the compression springs
To avoid sticking to the contacts, which led to massive problems mainly due to the introduction of lead-free solders in the electronics industry, there is, for example, a new development from the nanotechnology sector . This as XXLonglife surface called nanocoating prevents accumulation of dirt and ensures extremely long life compared to conventional gold-plated contacts.
Technologies
The following basic technologies are required to manufacture the components of spring contact probes:
- Turned parts production ( CNC -technical and conventional), comparable to the watch industry
- Deep drawing of sleeves
- Pipe processing
- Spring winding technology
- galvanic finishing
- Handling and assembly of precision parts
A few manufacturers have their own expertise and vertical integration in all of these areas, while others have the components manufactured by suitable suppliers and limit themselves to the assembly of the finished product. Basically, this does not say much about the quality of the end product; in terms of flexibility in the case of special types, new designs or customer-specific requests, the manufacturers with a high degree of vertical integration naturally have an advantage.
Use in the rigid needle adapter
With the rigid needle adapter , the spring contact pins are arranged in a fine grid (> 0.6 mm) in order to achieve a high test point density. The contacting force of the contact spring pins is then deflected from these grid points to the desired test point via a rigid needle . This adapter design has the advantage that up to 280 test points / cm² can be resolved and contact distances of > 150 µm can be achieved.
Individual evidence
- ^ ECT Contact Solutions. (No longer available online.) Everett Charles Technologies, 2014, archived from the original on October 16, 2014 ; accessed on December 2, 2014 . Info: The archive link was inserted automatically and has not yet been checked. Please check the original and archive link according to the instructions and then remove this notice.