Pull magnet


A pull magnet is an electromagnet with an armature, which is used to operate and trigger mechanical devices or in contactors or relays to generate mechanical movement.
Depending on the type and application, pull magnets are operated with direct or alternating voltage . The reluctance force of a pull magnet is independent of the direction of the current and, under otherwise identical conditions, depends on the square of the current strength.
Structure and special features
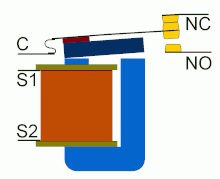
anchor
The anchor can be a hinged or a tie rod. Tie rods have a round cross section for small magnets and a rectangular cross section for contactors and AC tension magnets. In the case of Sagittarius, the anchor is T- or E-shaped. Very large holding forces are achieved with small actuation paths with disk-shaped armatures, as they also occur in a similar way in magnetic clutches and magnetically operated brakes.
yoke
The yoke forms the magnetic return path and must have good sliding properties inside the tie rods. The yoke carries the actuation coil. An arrow-shaped design of the magnetic circuit interruption between armature and yoke is intended to improve the tractive force curve in DC magnets.
Kitchen sink
In order to achieve the lowest possible energy consumption, the available winding space is wound with a high fill factor . To generate a high magnetic field strength with the lowest possible power consumption, as many turns as possible are required. It is enamelled copper wire used.
Traction curve
The change in the parameters in the magnetic circuit is not negligibly small when actuated. With magnets operated with constant DC voltage, there is a hyperbolic dependence of the force on the path. Since the magnet mostly works against the deflection of a pretensioned spring , whose characteristic is linear to a good approximation, problems can arise.
The tightening force is determined by the intersection of the two characteristics. To be attracted, the magnetic force must exceed the threshold value given by the spring force. The force of the pull magnet in the attracted state (holding force), on the other hand, is much greater than the attraction force. Some pull magnets therefore have a switching contact to reduce energy consumption, the interruption of which switches on a series resistor in the circuit shortly before the stop. Electronic driver circuits can also simulate this type of behavior: first, a large current ensures safe pick-up, then the current can be reduced to a fraction.
Alternating voltage magnets (see below), on the other hand, are more attractive and do not need such devices.
The magnetic field leads to a remanence in the magnetic circuit, which can be sufficient to keep the armature unintentionally attracted even in the de-energized state. This is avoided by an air gap in the magnetic circuit, which is also forced in the tightened state , designed for example as a so-called anti-stick pin (brass rivet in the armature) or a separating plate / foil with low magnetic conductivity between armature and yoke.
AC voltage operation
With direct voltage, there is a constant force in the steady state - when operating with alternating voltage, the zero crossing of the current also leads to a periodic drop in the magnetic flux density in the core to zero and, as a result, to an interruption of the tensile force. This leads to mechanical vibrations (hum) due to the brief opening of the magnetic circuit.
DC tension magnets can therefore not easily be operated with AC voltage. Remedy:
- Using a DC tension magnet with an upstream rectifier
- AC tension magnet with shaded pole in armature or yoke
- Three-phase pull magnet (3 coils, armature and yoke three-legged)
For larger AC tension magnets, the armature and yoke are laminated in order to avoid eddy current losses.
Shaded pole
As a result of the alternating voltage with the frequency , shown in the adjacent figure in light blue dotted as a field curve, the value for the holding force also fluctuates as a function of time. The course of the force from the main field, shown in dark blue in the figure, shows when supplied with harmonic alternating voltage with the angular frequency , due to the relationship :
twice the frequency. This follows from the fact that the reluctance force depends on the square of the current or, when fed from an AC voltage source, is directly proportional to the square of the voltage. The force of the main field, which always has a positive effect, decreases periodically to the value 0. Depending on the size of the masses in the magnetic circuit, unwanted vibrations or, in extreme cases, unwanted opening of the magnetic circuit occur.
This deficiency is remedied by an additional short-circuit winding which is introduced into the magnetic circuit and which is routed around part of the core in the area of the pole face, as shown in the adjacent figure in the form of a copper ring. This technical solution in the form of a shaded pole is similar to the procedure in shaded pole motors : In the short-circuit winding, part of the main field induces a current whose magnetic field, the so-called "gap field", has a phase shift compared to the main field . It is shown in light green dotted over time. As a result of the above relationship, the force effect due to the shaded pole also shows a phase shift with twice the frequency; the course is shown in green.
The sum of the two forces, shown in black in the figure, gives a shaded pole magnet the course of the entire force effect when operating on AC voltage. The total force no longer drops to zero, but fluctuates between two positive extreme values with a cosine curve and twice the frequency. Appropriate dimensioning, as well as ensuring that the resistance of the winding is determined by its impedance and not just by the ohmic DC resistance , can constructively avoid falling below the minimum holding force.
AC voltage pull magnets have a much higher attraction force than DC magnets, because the current absorbed at the moment of attraction is much higher than when the magnetic circuit is open due to the lower inductance when the magnetic circuit is open. AC magnets can be thermally destroyed if their attraction is prevented.
application
Amongst other things:
- Actuation of the pressure roller , the brakes and the magnetic couplings in tape recorders
- Triggering mechanical interlocks (e.g. switching off cassette tape at the end of the tape)
- Slot machines, money changers, automation technology
- Relays and contactors
- Door opener
- Impulse switch (installation remote switch )
- Toaster - The 'ON switch' is held in place by an electromagnet after it is pressed down and released again after the preset toasting time has elapsed
literature
- Rüdiger G. Ballas, Günther Pfeifer, Roland Werthschützky: Electromechanical systems of microtechnology and mechatronics. Dynamic Design - Fundamentals and Applications. 2nd Edition. Springer, Berlin a. a. 2009, ISBN 978-3-540-89317-2 , pp. 253-306: Chapter 8: Magnetic transducers.
- Walter Baumann et al .: LV switchgear practice. Function, choice, use. Edited by Roland Werner. VDE publishing house, Berlin a. a. 1984, ISBN 3-8007-1353-5 .