Railway depot (steam locomotives)
A railway depot , also in short Betriebswerk (abbreviated Bw or BW ), is responsible for the maintenance of the locomotives used in rail traffic . Especially in the age of steam locomotives, it was of great importance for the smooth running of operations. Bw had a large number of systems in order to be able to carry out these maintenance tasks. The Bw therefore needed a lot of staff - they were mostly one of the largest employers in the region. If locomotives were used at a greater distance from the depot, this was done in a locomotive station attached to the Bw .
The history and today's importance of these facilities is presented in the article Bahnbetriebswerk .
tasks
Gear up
Before a steam locomotive was allowed on the line , the locomotive staff had to do a lot of preparatory work. When the scheduled start of duty, the locomotive staff - the engine driver and stoker - reported to the locomotive management of the respective depot. There they were given the keys to their locomotive, a repair book, a route and timetable, and a list of the speed limits . After completing all formalities, the engine driver and stoker went to their steam locomotive, which was either parked in the locomotive shed or on an open track. After climbing the driver's cab, the driver began with the most important checks: regulator check, tightness of the valves, water level indicators and brake test. The stoker checked the equipment as well as the fuel supplies. Only after these checks had been carried out did the staff begin their actual task.
The stoker started heating the locomotive, then the steam locomotive drove to an investigation pit. While the engine driver was looking under the locomotive and looking for any damage, the stoker - equipped with an oil can and oil syringe - had to supply all of the locomotive's lubrication points (see picture).
Once all the checks were carried out and the boiler's operating pressure had been reached, the locomotive could drive out of the locomotive shed and go to the turntable. After the signal box cleared the tracks , the locomotive officially went into service and set off on the line.
Disarm
On the last few kilometers to the terminus, the stoker began disarming the fire by slowly letting the fire burn down depending on the route requirements. After the train arrived at the terminus or the scheduled end of the locomotive route, the stoker turned off the steam heating on passenger trains and the locomotive was uncoupled from the train and drove to the depot. There, the coal stocks were first replenished in the coaling plant ; there were corresponding bunker systems for machines with oil and coal dust firing in the Bw-s that housed or supplied such machines. Then the machine rolled to a slag pit , where the boiler was slagged out by workers by removing the combustion residues ( ash and slag ) from the fire box , extinguishing them in the pit and storing them temporarily. Discharge was a pretty dirty job. After the drainage was complete, we went to the water crane , where the water supplies were replenished. The next station was the sanding system for replenishing the brake sand supplies, which was done by hand at smaller workshops - with the help of ladders and buckets - on the sand dome on top of the boiler .
After the locomotive was ready for the next use, it was either parked in the locomotive shed or on an open track and cleaned by the stoker. Repairs were carried out by the responsible staff during the rest period. Machines that were supposed to be used again at short notice were kept warm, for which a shed heater in the fire box maintained a quiet fire.

Wash out
The boiler of a steam locomotive had to be cleaned of evaporation residues at regular intervals. This happened in the depot on precisely defined dates. How far apart the two dates were determined by the quality of the boiler feed water , the frequency of use and the stress on the locomotive from the routes it traveled. Washing a steam locomotive consisted of six work steps:
First the steam and after the kettle had cooled down, the water in the kettle had to be drained. After that, cleaning of the boiler could begin, whereby the limescale deposits on the boiler floor and the sludge were flushed into sludge collecting devices through special wash hatches on the outside of the boiler wall with a sharp water jet. The standing kettle was then washed out from top to bottom. If necessary, excessive calcium deposits had to be removed. Then the boiler was filled and heated up again.
During the last run of the locomotive before the scheduled cleaning, the preparations for washing began.
Deadline and planned work
While the factory workers were busy washing out a locomotive, locksmiths did deadline and planning work. This work was necessary to keep the machine operational for as long as possible between the main inspections. In order to keep the machine shutdown time as short as possible, this work was spread over the whole year. The most important work included the half-yearly brake inspection, the quarterly stability test procedure and an annual main brake inspection. Other work is listed in the table below.
|
|
Special purpose trains
In addition to the maintenance of all locomotives, some depots are also responsible for the maintenance of special service trains. The most important units are relief trains or special service trains (Switzerland) (e.g. for reloading derailed vehicles) and snow clearing vehicles . There were also fire extinguishing trains to put out fires in the vicinity as quickly as possible. For the smooth operation in a depot or be towed shunting locomotives needed, the wagons and not drivable traction vehicles move. Almost every depot had a wide variety of special vehicles.
Investments
Operating facilities
A large number of different systems were required to maintain a steam locomotive.
Water supply
In addition to coal, water was needed to run steam locomotives . That is why the water supply for a depot played an important role. In order to be able to guarantee this, almost all railway depots had their own railway waterworks. These waterworks were equipped with various systems for water extraction (pumps, pipes, water tanks and extraction points). Some railway depots had two different waterworks: a railway waterworks that provided usable water for the operation of the machines and a drinking waterworks that stored water for the employees of the depot. As a result of the connection to the regional water network, many railway depots no longer have drinking water works. The water was taken from springs, wells and ponds and then purified. Industrial water for the operation of steam locomotives had to be able to meet a high level of quality. That is why the railway waterworks developed their own filter systems, where the water was treated so that it was usable for operation. In particular, the salt content and the degree of hardness of the water were decisive for the usability.
After cleaning the service water, it was pumped into a water tower and stored there. These systems had different shapes, there was no uniform design. All water towers had several risers and downpipes. The water towers supplied all systems with usable water, including the water cranes . With the help of these devices, the water supplies of steam locomotives were replenished (either tender or water tank). Water cranes were mostly located near the investigation pits or near the coaling plant. There was also a wide variety of designs, but these were gradually replaced by standard designs.
Larger and medium-sized railway depots had their own laboratory that constantly monitored the water treatment , with the treatment of the boiler feed water being checked in particular . Investigations of the boiler feed water were carried out. The laboratory determined the salt content, the pH value and the composition of the boiler feed water. The locomotive staff had to bring samples of the boiler feed water to the laboratory at regular intervals. In addition to the water controls, the laboratory was also responsible for checking the lubricating oils and fats supplied .
Engine shed
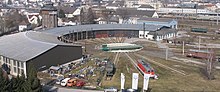
Each major depot had its own roundhouse with a turntable . The locomotives were turned on the turntable and parked in the locomotive shed. These could be heated, because the steam locomotives were not allowed to cool down completely, otherwise heating up would take too long. To move cold shut off steam locomotives were mostly locomotive delay winds installed. It was mandatory for almost all railway companies to be able to park at least 75 percent of all locomotives in the locomotive shed, the rest was parked on open tracks. Large depots also often had two or three roundhouse sheds with the associated turntables. However, the roundhouse was dependent on the turntable, in the event of a failure the locomotives could not be driven out of the shed. The turntable therefore had an emergency drive (with compressed air). In the course of time, a standard design with a stage length of 26 meters was developed. Turntables were always exposed to the weather and had to be serviced at regular intervals. Actually every depot with a turntable should have had a track triangle so that the locomotives could continue to turn in the event of failure of the turntables, which were usually very heavily loaded. However, since track triangles required a lot of space, they were rarely found. Smaller depots often only had a rectangular shed that could be reached with the help of switches . Every railway depot had to have enough building ground to be able to expand it on all sides. Smaller maintenance work was carried out in the locomotive shed itself, for other repair and maintenance work there was usually a locomotive workshop, which usually also had a loading crane with which the heavy spare parts could be moved.
Sanding system
Sufficient static friction between wheel and rail is necessary for trouble-free railway operation. Steam locomotives therefore had one or two sand containers on the top of the boiler, which were serviced at sand systems. These had a bunker or a sanding tower and a storage facility for the processed sand. On a sanding tower, a telescopic tube was latched into the locomotive's sand container and this was then filled up as required. Depots typically had a supply of sand for about 30 days.
Coaling plant

Each railway depot had one or more coaling systems (coal bans) that had the following tasks: It was responsible for feeding and unloading the coal . She also had to store the fuel and replenish the locomotives' fuel supplies. Coaling plants came in different types and sizes, with these two criteria depending on the daily fuel delivery to the steam locomotives. The fuel was delivered by rail, either with normal freight wagons or with special self-unloading wagons. The coal was stored in large coal bunkers, these mostly had side walls made of concrete (in the case of smaller depots, these consisted of old sleepers and pieces of track ). Each depot stored the daily fuel requirements in a main bunker, the remaining coal was stored in one or more reserve bunkers.
The delivery to the locomotives could be done in different ways. Many depots brought the coal from the Bansen with Hunten on its own track to a rotating crane, which then picked up the hunt and tipped the contents into the tender of the locomotive. Large depots had falling platforms or large coaling systems that had four filled, funnel-like bunkers that were provided with a lock. If this was removed, the coal trickled into the tenders of the locomotives. In this variant, the coal was fed to the four small bans from the main bans by a large crane. Since these two variants required a lot of space, inclined coaling plants were built in small and medium-sized operations. The coal was also transported with Hunten, these were then pushed into a kind of elevator, pulled up and then tipped - so the coal also trickled into the tender of the steam locomotive.
In addition to the coaling plant, there were often water cranes and service buildings. In addition, there were often storage rooms in the vicinity of these facilities.
Purification plant
In the purification plant, when a steam locomotive was dismantled, the grate, ash pan and smoke chamber were cleaned, because up to 20 percent of combustion residues remained when coal was burned. These were scraped off with various tools (scrapers, hooks and special scraping brushes) and placed in the slag pit. Slag pits or slag channels were located outside on special slag tracks. The slag sump left over after cleaning was stored in the pit until it was emptied. This was done either by hand or with an inclined elevator (see picture on the right). The slag was shoveled into Hunte, these were pulled up, tipped and the slag fell into a wagon with which it was transported away.
Blow-out devices
During operation, unburned coal pieces, ash and slag particles were deposited in the heating and smoke pipes, which is why these pipes had to be blown out at fixed intervals. This procedure usually took place after 500 to 1,000 kilometers of running of the machine. The blow-out device consisted of a mobile working platform and a pipe. Compressed air was pumped into this pipe, then all heating and smoke pipes were blown out with it. There were employees for this activity, and this work was carried out on a specific open track. The blowing out of all pipes could take up to an hour, a 01.5 had up to 168 heating and smoke pipes, for example.
Washout level
The boilers of the steam locomotives had to be cleaned at regular intervals. Although the boiler feed water was filtered elaborately, it contained some chemical compounds that did not completely evaporate. These compounds then settle in the form of sludge and scale, which could lead to clogging of the pipes, hinder the heat transfer in the boiler and thus endanger the operation of the machine. For this reason, the boiler had to be washed out either every ten to 14 days or after 2,000 kilometers for express locomotives and 1,500 for freight locomotives. Cold washing of the boiler took up to 14 hours, and hot washing required a special washing system. For this operation there was a separate wash-out track in the locomotive shed with a wash-out channel, and each depot had another wash-out track outside the locomotive shed. The water used flowed into this channel and could be used for other purposes if necessary.
Water tower in the Bochum-Dahlhausen Railway Museum
Water crane in Stützerbach
Technical equipment
In addition to the operating systems, each depot also had numerous technical systems. These included transfer platforms and turntables , for example . Axle sinks were also very important . These were mostly housed in the engine shed or in the workshop. With these machines, changing axes was relatively easy. There were many different designs, which is why a standard design was developed. With the help of an axle recess, the installation and removal of an axle could be carried out in just half an hour.
The workshops of the railway depot also had their own wheelset lathes for smaller repair work. Increased wear and tear on the wheel tires made it necessary to work on the outline before the scheduled visits to the repair shop. Each workshop was also equipped with an extensive range of tools. In the case of medium-sized and larger railway depots, the workshop was divided into different departments. So there was a separate mechanical workshop, a forge , a tool production , a locksmith , a foundry and an electrical workshop (but this had little meaning). In addition to the departments, there were also some groups for special work. For example, we have set up our own workshops for repairs to pumps and boilers.
Other plants
In addition to the operating facilities, a depot also included social rooms (shower and washing facilities, lounges for the depot and locomotive personnel, sleeping facilities for the locomotive personnel and, in larger depots, a canteen). Since a depot often had extensive track systems, it was often assigned its own signal box , from which the course of action was controlled and directed.
administration
Working groups
In order to optimize the workflow, individual tasks were assigned to different working groups:
- Group A: administrative matters,
- Group B: Locomotive Service,
- Group C: Locomotive repairs,
- Group D: wagon operation service and wagon repair,
- Group E: mechanical systems,
- Group F: fuel storage and
- Group K: vehicle service.
This system was used by both the Deutsche Bundesbahn and the Deutsche Reichsbahn, the Reichsbahn just had different names for the groups. The administration functioned similarly in Austria, the work processes were also precisely divided here.
Group A: Administrative Matters
Group A usually only existed in larger depots, as this was where the administrative effort was greatest. In the case of smaller departments, the depot manager took on these tasks, whereas in the case of medium-sized depots, the administrative tasks were divided between groups B and C. Group A had to create a profitability overview and a locomotive performance overview. She was also responsible for the entire payroll (payment of fuel-saving bonuses and payment of vacation and sick pay). The maintenance of service books and locomotive service lists (including mileage and fuel consumption of the rolling stock) as well as the monitoring of energy consumption and the consumption of operating materials (especially coal, water and gas ) was also the task of this group.
Group B: Locomotive Service
Group B was responsible for locomotive operations. It was headed by an inspector, who was usually also the deputy head of the service, who was supported by various helpers and locomotive managers. The task of creating duty rosters and work schedules was later taken over by so-called technologists. Most of the large railway depots also had an external train driver and their own service scheduler. Smaller depots transferred the tasks of this group to the locomotive dispatcher. Group B, which at the Deutsche Reichsbahn was designated as the locomotive operation section , had to take care of all matters relating to locomotive and feeder services. This also included operational monitoring of the traction vehicles, clarification of malfunctions and malfunctions, creation of duty and vehicle schedules, allocation of personnel and machines, control of service books, training of staff, management of all documents and supply and care of all traction vehicles (heating up, coaling, cleaning) to their duties.
Group C: Locomotive repairs
Group C - locomotive repairs - was also managed by a Reichsbahn inspector. This was mostly the deputy head of the service, to whom several foremen were subordinate depending on the size of the respective depot. This group consisted of several work columns (a maximum of 30 employees), who in turn were subordinate to several foremen. The Deutsche Reichsbahn also referred to this group as the locomotive entertainment department . Group C was responsible for carrying out repair and maintenance work, handing over damaged rolling stock to the repair shops, ordering spare parts and materials including managing the spare parts magazine, monitoring new assemblies on vehicles, providing a rescue train and troubleshooting.
Group D: Car service and repair
Group D played a special role in the depots, because not every depot had such a department. Smaller operations plants assigned the tasks of this group to a separate championship of group C, which had a maximum of 40 employees. Larger D-groups were combined into independent departments at both the Bundesbahn and the Reichsbahn in the 1950s, which were referred to as company car works. If this was not the case, Group D was headed by a Reichsbahn inspector, to whom, depending on the size of the plant, up to three wagon masters were subordinate. This area was used for checking damage reports, repairs of damage and defects, checking the wagon masters at train stations, clarifying operational irregularities, filling the gas filling and disinfection systems for wagons, cleaning, lighting and heating the wagons, maintenance and repair work, delivery of wagons Responsible for repair shops, ordering of spare parts and materials including administration of the spare parts magazine and observation of new assemblies on wagons.
Group E: mechanical systems
The composition of group E depended on the size of the respective depot. At DR, this group was referred to as the “Technical Systems” department. At the Bundesbahn, this department was again divided into two subgroups. The group was headed by a Reichsbahn inspector at medium-sized and larger railway depots. For smaller departments, group E consisted of a maximum of 20 railway workers - these mostly belonged to group C. This group was crucial for a smooth operation. Her area of responsibility included looking after the gas, water, steam and heating systems as well as the coaling, sanding and loading systems (the crane systems, turntables and transfer platforms were also part of her area of responsibility), maintenance of the electrical systems, maintenance of the scales and rail brakes , Ordering of spare parts and materials including administration of the spare parts magazine and instruction and control of the machinists.
Group F: Storage of consumables
Larger depots had their own department that was responsible for the fuel store - group F. Smaller departments distributed the tasks of this group to group A. The tasks of group F were the ordering and installation of fuel supplies and devices, management of the Equipment ledger (a kind of inventory) and storage of operating materials and control of warehouse employees.
Group K: vehicle service
Group K was formed in the 1930s, but it only existed at a few depots. In the 1950s, the Reichsbahn and Bundesbahn spun off Group K and finally converted it into so-called motor vehicle depots . Group K was subordinate to a Reichsbahn inspector and had the tasks of deploying and maintaining the vehicles, transferring vehicles to repair shops, checking and managing the fuel store and checking the drivers.
Workforce
The workforce of a railway depot consisted of a chief of staff, the supervisory officers, the company officials, the craftsmen, the factory workers and the administrative employees. The head of a railway depot was the head of service - he mostly had a mechanical engineering training and was an engineer . In the case of smaller offices, it often happened that the longest-serving driver took over the lead. The head of service was responsible for selecting the personnel and was also allowed to conduct exams. He was also a kind of head of security, because he had to monitor compliance with safety and work regulations; he was also responsible for the cleanliness of the depot. Since almost all service heads had train driver training, they had to help out on duty when traffic was high. In the event of serious accidents or other events, the head of the service had to appear immediately.
See also
literature
- Volker Großkopf, Dirk Rohde, Markus Tiedtke: Bahnbetriebswerke Part 1, Small Locomotive Stations . In: Eisenbahn-Journal Anlagenplanung 2, 2001. Verlagsgruppe Bahn GmbH, Fürstenfeldbruck 2001, ISBN 3-89610-073-4 .
- Volker Großkopf, Dirk Rohde, Markus Tiedtke: Bahnbetriebswerke. Part 2: Medium-sized locomotive stations . In: Eisenbahn-Journal Anlagenplanung 4, 2002. Verlagsgruppe Bahn GmbH, Fürstenfeldbruck 2002, ISBN 3-89610-102-1 .
- Peter Koehler, Wolfgang List: Das Bahnbetriebswertk for the steam locomotive era, transpress 1987 alba ISBN 3-87094-216-9
- Michael U. Kratzsch-Leichsering, Dirk Endisch: The steam locomotive in the depot . Transpress, Stuttgart 1999, ISBN 3-613-71096-X .
- Jan Reiners: This is how the depot works . Transpress, Stuttgart 2006, ISBN 3-613-71279-2 .
- Dirk Rohde, Markus Tiedtke: Bahnbetriebswerke. Part 3: Large Locomotive Stations . In: Eisenbahn-Journal Anlagenplanung 4, 2003. Verlagsgruppe-Bahn GmbH, Fürstenfeldbruck 2003, ISBN 3-89610-116-1 .
- Dirk Rohde, Markus Tiedtke: Bahnbetriebswerke Part 4: Groß-Bw . In: Eisenbahn-Journal Anlagenplanung 4, 2004. Verlagsgruppe Bahn GmbH, Fürstenfeldbruck 2004, ISBN 3-89610-129-3 .
- Markus Tiedtke: Railway depot. Part 1: coaling and sanding . In: EK-Special 19. EK-Verlag GmbH, Freiburg.
- Markus Tiedtke: Railway depot. Part 2: water on . In: EK-Special 24. EK-Verlag GmbH, Freiburg.
- Markus Tiedtke: Railway depot. Part 3: turntables and engine shed . In: EK-Special 34. EK-Verlag GmbH, Freiburg.
- Walter Weikelt, Manfred Teufel: The technology of repairing steam locomotives . Transpress, Stuttgart 2005, ISBN 3-613-71256-3 (reprint of the Berlin 1962 edition).
Footnotes
- ↑ This is how the depot works , pp. 142–148.
- ^ Profession train driver , pp. 57–71.
- ↑ This is how the depot works , pp. 149–152.
- ↑ This is how the depot works , pp. 152–156.
- ↑ This is how the depot works , p. 156.
- ↑ This is how the depot works , p. 153.
- ↑ How the depot works , pp. 126–139.
- ↑ Modellbahnreport 73, Der Kohlen-Elevator , 2005, p. 16.
- ↑ Modelleisenbahner , Issue 6, June 2006, pp. 18–23
- ↑ This is how the depot works , pp. 14-18.