Equal space process

The constant space process is a thermodynamic comparison process for heat engines , in which the heat supply occurs predominantly with the same volume ( isochoric ) (for a reciprocating piston engine practically in top dead center ), whereby the technical constant space process of an internal combustion engine with gas exchange and emission of exhaust gas is called the Otto cycle process becomes.
In contrast to this is the constant pressure process (technically referred to as the diesel cycle process for piston engines ), in which the heat supply or combustion takes place predominantly at constant pressure ( isobaric ; in piston engines therefore predominantly only after dead center , while expansion is already beginning ).
Technically, real engines mostly work in the transition area between the ideal constant space and constant pressure process, for which the mixed Seiliger cycle process in particular provides a better approximation that can be used for both diesel and gasoline engines.
At the beginning of the 20th century, Hans Holzwarth developed constant-space gas turbines that use the constant-space process with cyclical combustion of the fuel-air mixture and do not need a compressor . However, they have been replaced by continuously operating gas turbines with compressors, which tend to implement the constant pressure process.
Another older application with cyclic combustion is the pulse jet engine with flutter valves on the air inlet. A more recent development is the ramjet engine with discontinuous operation without moving mechanical parts.
Ideal equal space process
Thermodynamic state diagrams of an ideal constant space process ( Otto cycle ) | |
---|---|
![]()
Equal space process in the pV diagram
|
![]()
Equal space process in the Ts diagram
|
The theoretically ideal constant- space process comprises neither chemical conversion ( combustion ) nor gas exchange with the emission of exhaust gas and strictly consists of four changes of state of an ideal gas within a closed system :
- 1➝2: isentropic compression
- 2➝3: isochoric (hence heat constant-volume process)
- 3➝4: isentropic expansion
- 4➝1: isochoric pressure reduction through heat dissipation (practically often through the emission of exhaust gas = gas exchange)
The area enclosed by the line 1-2-3-4 in the pV diagram corresponds to the specific process work w .
Thermal efficiency in the constant room process
For the simplified calculation of the state variables, an ideal gas with a temperature-independent specific heat capacity is assumed as the working medium . In contrast to the constant pressure process , the thermal efficiency does not depend on the amount of heat supplied in the constant room process :
The higher the expansion ratio (geometric compression ratio) and the isentropic exponent , the higher the efficiency.
- ; Initial volume = expansion volume
- ; Compression volume
- ; Displacement ( displacement )
- ; geometric compression ratio
The isentropic exponent drops sharply at high temperatures. Combustion gas or exhaust gas from internal combustion engines has an isentropic exponent of approx. 1.3 at 1000 ° C
- ; Specific heat capacity at constant pressure (exhaust gas at 1000 ° C has approx.1.25 kJ / (kgK)
- ; Specific heat capacity at constant volume (exhaust gas at 1000 ° C has approx.0.95 kJ / (kgK)
The specific gas constant , on the other hand, remains constant over a wide temperature range and is approx. 0.295 kJ / (kg · K) for fresh gas and for exhaust gas.
Comparison of the efficiency of constant space and constant pressure processes
Mathematically, with the same compression ratio, the thermal efficiency of the constant space process is higher than that of the constant pressure process . From a technical point of view, however, the diesel cycle process in modern engines in particular is easier to control than the constant -space process (especially the Otto cycle process ), so that in practice it ultimately achieves a better degree of efficiency with higher-tolerance process parameters .
Maximum pressure and maximum temperature
The specific heat supply or heating energy of the fuel determines the pressure or temperature increase and thus the ratio . In the pure constant space process, this number does not play a role in the efficiency.
- ; Pressure ratio or temperature ratio (combustion pressure or temperature to compression pressure or temperature)
H u is the lower specific calorific value (kJ / kg), e.g. B. 42,000 kJ / kg for gasoline or diesel. m H is the specific heating mass to the fuel mass (kg / kg), e.g. B. 18 kg of air and residual exhaust gas per kg of gasoline. The specific heat capacity c V of exhaust gas at 1000 ° C is approx. 0.95 kJ / (kg K).
- ; Compression pressure; p 1 is the initial pressure, e.g. B. 1 bar
- ; Compression temperature; T 1 is the initial temperature after suction and before compression, e.g. B. 400 K (approx. 127 ° C)
- ; p 3 corresponds to the pressure after the supply of heat (maximum pressure)
- ; T 3 corresponds to the temperature after the supply of heat (maximum temperature)
Otto cycle
Supplemented by a charge exchange with combustion and emissions of exhaust gas from the constant volume process for piston engines as Otto-cycle , respectively. This includes both two-stroke - as well as four-stroke - piston engines whose stroke of a respective piston stroke or half a crankshaft revolution there. The ratios can in principle be transferred to rotary piston engines and rotary piston engines such as the rotary engine .
The ideal gasoline engine

The theoretically ideal gasoline engine has no dissipation losses, mechanical friction losses, auxiliary units, cylinder cooling or leakage losses. The working gas has the same properties over the entire cycle and no flow losses. The ideal charge exchange takes place without mixing fresh charge with exhaust gas.
For the four-stroke gasoline engine , the curves in the status diagram can be assigned to the 4 work cycles as follows ( the numbering in the status diagram should not be confused with the work cycles! ):
- "Priming" cycle (0-1): Filling with fresh charge
- "Compression" cycle (1➝2): isentropic compression, then in top dead center (2➝3) isochoric heat supply through ignition and combustion of the compressed mixture at constant volume (constant volume combustion )
- "Expand" cycle (3➝4): isentropic expansion of the hot exhaust gas does work
- "Push out" cycle (4➝1): Deviating from the ideal constant space process, there is now no isochoric pressure reduction through heat dissipation in the bottom dead center, but the heat is released from the working chamber by opening the exhaust valve with the exhaust gas , with the residual pressure dynamically expanding into the exhaust . The remaining exhaust gas is then expelled by the piston stroke (10).
While the four-stroke cycle requires a complete crank rotation with 2 working cycles for the gas exchange, the two-stroke engine does this very quickly while passing through the bottom dead center, so that the working cycles "suction" (0-1) and "exhaust" (1-0 ) simply omitted. The technical processes of the gas exchange are not shown in the thermodynamic state diagram for the ideal constant pressure process, where they practically accumulate in point 1.
The real Otto engine
The changes in state of the real Otto engine deviate considerably from the ideal course of the theoretical Otto cycle process:
State diagram for a real four-stroke - petrol engine | |
---|---|
![]()
4-stroke cycle of an ideal, typically slow-running gasoline engine : 1: intake ➝ 2: compression ➝ 3: expanding ➝ 4: pushing out
|
For the two-stroke engine , only the gas exchange loop of the "pushing out" and "sucking in" work cycles is essentially omitted .
- the combustion is not completely isochoric because it requires time in which the crankshaft continues to turn: the ignition takes place before top dead center and the combustion is only completed during expansion. The extreme pressure peak (3) in the state diagram is reduced and rounded to the right, which is gentle on the motor but reduces efficiency.
- In a real gasoline engine, the knock resistance of the fuel-air mixture limits the compression pressure, because a sudden, complete combustion in the same space at top dead center causes extremely high pressure peaks as detonation , which damage the engine as undesirable knocking . Therefore, a slower deflagration is sought, the combustion of which extends into the area of expansion in the manner of a constant pressure process . This hybrid form is described much better with the Seiliger cycle .
- The fuel-air mixture is not an ideal gas , but has a smaller isentropic exponent and increases its heat capacity at high temperatures. In addition, the combustion changes the material composition of the working gas and thus its thermodynamically relevant properties, in particular the heat capacities of the reaction products water vapor and carbon dioxide .
For these reasons, the constant space process or Otto cycle process has little predictive power for real engines. The mixed Seiliger cycle , which can be used for both gasoline and diesel engines, provides a better approximation, especially for the transition area between the ideal constant space and constant pressure process .
Real motor losses
Compared to the comparison process, the real cycle process in the engine does less work:
- The gas exchange with suction and discharge is comparable to a pumping process, which consumes a certain part of the engine power due to friction and flow losses (gas exchange work = counterclockwise loop between 0 and 1 in the pV diagram).
- In addition to incomplete combustion and the endothermic formation of nitrogen oxides , part of the heat energy is lost on the combustion chamber surfaces and does not contribute to the work performance.
- Since the outlet also needs some time, the outlet valve has to open shortly before bottom dead center so that the process surface is cut in point 4 (loss of expansion): The residual pressure of typically around 3-5 bar "fizzles out" into the exhaust system , if not An exhaust gas turbine whose further expansion is used: The power that is still gained in this way can preferably be transferred to the crankshaft via a turbocharger if the compressed charge air drives the piston during the intake cycle, instead of having to work against negative pressure as in the naturally aspirated engine .
The ratio of the work released in the engine to the theoretical work of the cycle is called the quality level. Real motors also have a mechanical power loss due to friction, auxiliary drives and auxiliary drives, which can amount to more than 10% of the rated power and reduce the efficiency accordingly.
Humphrey cycle
The Humphrey cycle differs from the Otto cycle in that it has unlimited gas expansion and thus utilizes the exhaust gas pressure down to ambient pressure, so that, in contrast to the piston engine, no residual pressure "fizzles out" at the end of the work cycle . It differs from the Joule cycle in that it has a higher peak temperature and the resulting higher peak pressure.
Ideal Humphrey comparison process
Thermodynamic state diagrams for the ideal Humphrey comparison process | |
---|---|
![]()
Humphrey cycle in a pV diagram
|
![]()
Humphrey cycle in the Ts diagram
|
Like the theoretically ideal constant space process, the Humphrey comparison process does not take into account any gas exchange and ideally consists of four changes of state of an ideal gas within a closed system :
- 1➝2: isentropic compression
- 2➝3: isochoric (hence heat constant-volume process)
- 3➝4: isentropic expansion
- 4➝1: isobaric heat dissipation
Thermal efficiency
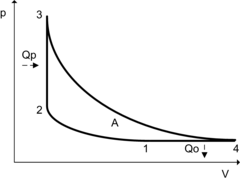
With pulsating combustion, a higher maximum temperature and thus a higher maximum pressure is possible with the same thermal load on the material than with continuous combustion. The Humphrey cycle corresponds formally to the Carnot cycle .
Using the equation for the temperature change in isentropic compression gives:
- ; Isentropic coefficient cp / cV of the working gas
- ; Initial and final pressure
- ; Compression pressure and temperature
- ; Maximum pressure and temperature after isochoric combustion
- ; Final temperature
- ; Initial temperature or ambient temperature
The pressure increase p 3 -p 2 and the temperature increase T 3 -T 2 are calculated in the same way as in the Otto process. The higher the isentropic coefficient and the pressure ratio (larger p 3 , smaller p 41 ), the higher the efficiency.
See also
literature
- Literature on technical thermodynamics
- Wolfgang Kalide: Pistons and flow machines. 1st edition, Carl Hanser Verlag, Munich / Vienna 1974, ISBN 3-446-11752-0 .
- Jan Drummans: The car and its technology. 1st edition, Motorbuchverlag, Stuttgart 1992, ISBN 3-613-01288-X .
- Karl-Heinz Dietsche, Thomas Jäger, Robert Bosch GmbH: Automotive pocket book. 25th edition, Friedr. Vieweg & Sohn Verlag, Wiesbaden 2003, ISBN 3-528-23876-3 .
Web links
- Humphrey Cycle (PDF; 1.6 MB)
- Thermodynamics University of Munich (PDF; 9.7 MB)
- University of Duisburg-Essen, basics of technical thermodynamics with exercises and solutions (PDF; 2.6 MB)