Aerodynamics of the Eurofighter Typhoon
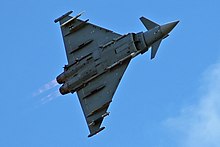
The aerodynamics of the Eurofighter Typhoon was the greatest challenge in the development of the aircraft. The reason for this is that a fighter aircraft should be built with the maximum possible instability. This article describes the development necessary for this, from the first attempts at walking with the F-104G CCV to the X-31. Alternative developments for a European fighter aircraft are not discussed here, the economic and political development history of the Eurofighter Typhoon can be found in the main article .
overview

In 1971 the requirements for a new combat aircraft were formulated in Great Britain . The requirements published in 1972 resulted in a conventional P.96 design in the late 1970s. Due to the similarity to the F / A-18 Hornet , the design was dropped. British Aerospace instead joined the draft tactical combat aircraft 90 (TKF-90) by Messerschmitt-Bölkow-Blohm . Both published a proposal called the European Collaborative Fighter or European Combat Fighter , while France relied on an in-house development.
BAE then developed two of its own designs: The P.106 was a light fighter aircraft with one engine, the P.110 had two engines and two vertical stabilizers. Both were conventional Delta - Canard Designs, where the duck wings were arranged just before and above the wing. The P.106 draft was rejected by the Royal Air Force , but BAe Systems further developed the concept in cooperation with Saab Technologies to create the Saab 39 Gripen . Since no agreement could be reached with France, the Panavia partner companies (BAe, MBB and Aeritalia) started the Agile Combat Aircraft Program (ACA) in April 1982, which led to the Experimental Aircraft Program (EAP).
In 1983 the United Kingdom, France, Germany, Italy and Spain started the Future European Fighter Aircraft (FEFA) program. However, in 1984 the other states withdrew from the program due to completely different performance demands from the French. France insisted on an aircraft carrier version, 50 percent of the workload and system leadership from Dassault. The aircraft was supposed to be lighter and simpler, as Dassault believed it would offer better export opportunities. These demands were unacceptable to the other manufacturing countries and incompatible with their own requirements. With France, the "Euro hunter" would be qualitatively worse than desired, without France noticeably more expensive. The then Federal Minister of Defense Manfred Wörner even threatened a German-American solution.
On August 1, 1985, Great Britain, Germany and Italy agree on the construction of the EFA (European Fighter Aircraft, in Germany referred to as Jäger 90). Spain also joined in September. In 1986, the Eurofighter Jagdflugzeug GmbH was founded in Munich to manage the project, and EuroJet Turbo GmbH was also founded in Munich to develop the EJ200 engine. The aircraft, like the Advanced Tactical Fighter, was originally planned as an air superiority fighter with air-to-ground capabilities. In addition, it should have an empty weight of 9750 kg and be able to transport a weapon load of 6500 kg. With the collapse of the Soviet Union , the concept became obsolete, which resulted in a revision of the treaties in 1992. The cell life was doubled and the weapon load increased to 7500 kg, in return the empty weight of the aircraft rose to 11,000 kg. The EFA / Jäger 90 was then renamed the Eurofighter EF 2000 .
Basics
In early 1960, Colonel John Boyd and mathematician Thomas Christie developed the Energy Maneuverability Theory (EM theory), which was published in two volumes in 1964. In it, the maneuverability of a fighter aircraft is determined based on the specific excess power (SEP) . The resulting parameters such as short-term turning rate, permanent turning rate, climb power , acceleration and deceleration are still used today to assess the performance of a combat aircraft.
When considering the short-term turning rate, the focus is on the ability of an aircraft to achieve a high turning rate at which energy loss may occur. The permanent turn rate is reached when the aircraft can fly as tight a turn as possible without slowing down. Is an even tighter turn flown taking flow resistance of the aircraft about by the higher angle of attack and the larger control surface deflections. The aircraft would have to be accelerated or descended with more thrust in order to convert potential energy into kinetic energy . If the aircraft is slower, it could be the stalling speed (ger .: stall speed) below, a stall would result.
In order to achieve the highest possible permanent turning rate, a low wing loading and a high thrust is useful. However, the largest possible wing increases the curb weight of the machine and increases the moments of inertia , which leads to a deterioration in the thrust-to-weight ratio and to an increase in air resistance when maneuvering. So a compromise is necessary. One possibility is to make the aircraft unstable. To achieve certain turning rates, smaller rudder deflections are necessary than with an identical, stable aircraft whose center of gravity is in front of the lift vector. The turning rates can be increased in this way.
To ensure the necessary stability, a fly-by-wire system with a flight attitude computer is required. It should be noted that the pressure point (the point at which the lift force acts) can shift during flight. With a small increase in the angle of attack it moves forward, with supersonic flight it moves backwards. The problem can be reduced, among other things, by a low profile depth , which, however, leads to a (relatively) high load on the wing. Another problem is the need for linear aerodynamics. Classic flight controllers need them to control the aircraft. Non-linear aerodynamics exist, for example, when the lift coefficient no longer depends linearly on the angle of attack . Further possibilities are that actuators have to exert different forces depending on the maneuver load or that there is hysteresis .
In unstable canard combat aircraft, effects of non-linear aerodynamics are inevitable. The trick is to linearize these effects or to immunize the Flight Control System (FCS) against them. Due to the high instability of the Eurofighter, the requirement for linear aerodynamics was much more binding. However, there was the opinion that the FCS could also deal with extremely non-linear aerodynamics (“Never mind, the FCS will take care of it!”). The whole success of the concept depended on whether it would be possible to control the aircraft carefree handling in its envelope .
development

The development history of the Eurofighter Typhoon began quite early, when the Federal Ministry of Defense placed a development contract with Messerschmitt-Bölkow-Blohm in 1974 . A modified F-104G was to be used to investigate the degree of instability that could still be controlled by a flight controller. In addition, it should be examined how the flight control system (FCS) required for this would have to be structured, what degree of redundancy was necessary and what performance advantages such an aircraft would have. The knowledge gained in this way should flow into the development of a tactical combat aircraft (TKF). A similar development also took place in Japan from 1978, where a Mitsubishi T-2 was equipped with 3 canards and called the T-2 CCV.
In the first step, an F-104G was equipped with a fly-by-wire system and called the F-104G CCV (Control Configured Vehicle). For this purpose, four flight measurement data sensors were attached to the lower fuselage directly behind the radome . This configuration was named B1. The pilot was able to switch off the fly-by-wire system in order to control the aircraft "by hand" using the classic method. In the next step, a trim weight of 600 kg was placed in the rear of the machine, which led to an instability of 10% of the mean aerodynamic wing depth (mean aerodynamic cord, MAC) . This configuration of the F-104G CCV was named B2. Instead of using up the fuel in the wing tip containers, the fuel in the fuselage was first used to increase the stability margin for landing. In addition, the fuel could be pumped around the aircraft before landing in order to increase stability. In the third step, the stern ballast was removed and two canards were mounted on a narrow bridge on the back of the machine behind the cockpit. In order to compensate for the forward shift of the pressure point, 320 kg of ballast was installed in the nose. The F-104G CCV was stable and could also be flown manually, the designation was E1. On November 20, 1980, test pilot Nils Meister took off from Manching for the first time . In the E2 configuration, the rear ballast was reattached. The most unstable configuration E3 dispensed with the nose ballast, so an instability of 20% of the mean aerodynamic wing chord was achieved. It was possible to drop the tail ballast in flight in order to be able to stabilize the machine more quickly in emergencies. The program ended in 1984 after 176 test flights.
On April 26, 1978, MBB presented its Delta Canard Design TKF-90 to the public. This already contained the essential aerodynamic features of the later Eurofighter with the duck wings lying far forward, the wedge-shaped belly inlet and a vertical stabilizer. A thrust vector control was also planned. The instability should be 8%, a maximum of 10% of the mean aerodynamic wing chord, this value was determined from the F-104G CCV data. At the same time, from 1977 to 1985, a joint study by MBB and IABG examined the tactical advantages of CCV technology in flight maneuvers after a stall with this design. The advantage here are the canards, which are arranged far forward, which generate additional lift even after the wing has stalled or can direct the fuselage towards a target.
Since BAE Systems had joined the MBB concept in 1979, a joint concept was presented on September 5, 1982 together with Aeritalia at the Farnborough Airshow . With the ACA (Agile Combat Aircraft) the support of the governments was to be won to finance the construction of a prototype. On May 26, 1983, the contract for the development and production of a demonstrator was signed. In addition to BAe, Italian and German companies were also involved. The first flight of the resulting Experimental Aircraft Program (EAP) took place in 1986 and was the breakthrough in the development of the Eurofighter, as the feasibility of the concept was proven. The aircraft tested many new technologies, some of which were later used in the Eurofighter. The wing was made entirely of carbon fiber reinforced plastic (CFRP), i.e. not only the outer skin but also the frames were made of CFRP. While the individual parts were conventionally riveted together on the upper side of the wing , a new joining process was used on the underside . The parts there have been glued together to reduce labor and avoid possible leakage. The instability of the aircraft could be increased to 15% of the mean aerodynamic wing depth. The hull shape of the EAP has also been optimized to generate the lowest possible pitching moment in the transonic range. The air inlet was equipped with a movable lower lip and slot exhaust.
In the further course MBB was able to win Rockwell International as a partner. Rockwell presented the ARPA in 1983 with the draft for a fighter aircraft called SNAKE (Super Normal Attitude Kinetic Enhancement), which was almost identical to the later Eurofighter. From 1981 to 1984, both companies carried out investigations from their own resources. In May 1986 the governments of Germany and the USA signed a contract for the construction of two demonstrator aircraft, the X-31 EFM (Enhanced Fighter Maneuverability). Among other things, the fly-by-wire system and the flight control software were supplied by MBB, as well as the CFRP wings for both test aircraft. The first flight took place on October 11, 1990, the project lasted until October 1994. The autumn maneuver was also demonstrated for the first time , which, according to the team leader of the German part of the X-31 project, Dr. Wolfgang Herbst, was named. In the following VECTOR program, the ability to fly in a controlled manner even at extreme angles of attack was used, landings with angles of attack of up to 24 ° were flown in order to reduce the required landing distance. During the test program, a prototype crashed on January 19, 1995, but the test pilot Karl-Heinz Lang was able to shoot himself out of the machine in 18,000 ft. But suffered leg injuries when shooting out of the cockpit through contact with the instrument panel who ended his flying career as an active test pilot. The sister model, the Vector 2, was reactivated in 2002 for advanced FCS studies, flew a further test program with additionally reduced rudder and is now open to the public in the flight museum in Oberschleißheim as the highlight of the FCS design at the beginning of the new millennium.
The aircraft in the studies and in both experimental programs had articulated deltas. Articulated deltas have a lower pressure point shift with increasing speed and increasing angle of attack, but higher air resistance at supersonic. The controllability could be improved in this way, due to the better flight performance it was dispensed with with the Eurofighter. The instability there could be increased further to 16% of the mean aerodynamic wing depth. The first flight was carried out on March 27, 1994 by DASA magazine test pilot Peter Weger. The development aircraft DA1 (Development Aircraft) was operated from Manching in order to validate the aerodynamic data. BAE Systems in Warton also supplied to data DA2 to expand the envelope, in which the aircraft carefree (engl. Carefree) could be controlled. External tank configurations were investigated in Italy with DA3 and DA7 from Alenia Aeronautica in Caselle. The aerodynamic properties of the two-seater DA6 were tested by CASA in Getafe, BAe did this with the DA4 in Warton. In 2009, small extensions were fitted to the fuselage-wing transition ( strakes ) on DA5 in order to be able to increase the maximum angle of attack to over 30 °.
aerodynamics
Canards
While the horizontal stabilizers are mounted directly in front of and above the wing in less unstable Delta-Canard aircraft, in the Typhoon they are positioned far forward. The reason for this is the ability to get the nose of the aircraft back down from high angles of attack (pitch recovery) . If the angle of attack is increased, the pressure point of the wing moves forward and the aircraft becomes even more unstable. Due to the larger lever arm towards the center of gravity, the effect of the canards as a control surface increases, the advantage is maintained even at high angles of attack. The large lever arm also helps to reduce trim resistance in straight subsonic flight as well as improve maneuverability. The size of the canards can be reduced, which lowers their drag, especially in supersonic flight.
A horizontal stabilizer positioned at the front generates lift when turning and thus reduces the effective load on the wing, while a tail unit must generate downforce and thus increases the effective load on the wing. With a conventional canard arrangement, the buoyancy of the duck wings when turning is higher due to the shorter lever arm. With the Eurofighter, this effect has little influence on maneuverability due to the high level of instability.
The deep position of the canards also influences the flow over the wing. The (edge) vortices of the canards reinforce the vortex system on the wing, the lift of the entire system is thus higher than the sum of the lift forces of both components. This effect helps increase short-term turning rates.
The canards consist of superplastically deformed , diffusion- welded titanium parts .
Wing
The requirement for consistently high performance in supersonic conditions resulted in a delta wing with a leading edge sweep of 53 °. Delta wings with a sweep between 50 ° and 60 ° are particularly suitable for supersonic aircraft with very good maneuverability in the transonic speed range. The leading edge flaps are not only used to increase the maximum angle of attack, but are also automatically extended during the air combat in order to increase the wing area and thus the lift. The resulting higher air resistance is accepted and has to be compensated by the engines. The flaps are also deployed in transonic flight to reduce trim resistance. The reason for this is that the pressure point moves far back in the transonic speed range, much further than in supersonic flight. Extending the leading edge flaps extends the effective tread depth forwards and thus also shifts the pressure point in this direction in order to reduce trim resistance and increase maneuverability.
As in the Experimental Aircraft Program and the Rockwell / MBB X-31, the wings are made of carbon fiber reinforced plastic. Not only the panels of the outer skin, but also the frames are made of CFRP in order to keep the weight as low as possible. The leading edge flaps are made from an aluminum-lithium alloy . The outer trailing edge flaps are made of a superplastically deformed titanium alloy, the inner ones made of carbon fiber reinforced plastic. At the wing tips are the containers of the Praetorian self-protection system, which are an integral part of the structure.
hull
In supersonic flight, most of the air resistance of an aircraft is generated by the fuselage or by the interaction between fuselage and wing. The reason for this is that the air forces acting on the fuselage generate a torque around the transverse axis, which must be compensated by the rudder, which increases the trim resistance. Therefore, great efforts have been made to predict the influence of the hull shape on the pitching moment. The hull shape of the EAP has been optimized to generate the lowest possible pitching moment in the transonic range. However, the predictions deviated greatly from the measured values, so that a great deal of modeling effort was made when developing the Eurofighter. Compared to the EAP, the fuselage and wing root were changed and the results were validated using CFD simulations and transonic wind tunnel measurements. As a result, the pitching moment on the Typhoon could be significantly reduced. Although the real values again deviated strongly from the simulated ones, the difference was less drastic than with the EAP. The concept was also followed at the MiG-MFI .
The air brake is located behind the cockpit and is generously dimensioned for an aircraft of this size and weight class and is normally only found on larger and heavier models such as the Su-27 Flanker or F-15 Eagle . The air brake can be folded out to about 50 ° in order to reduce the speed of the aircraft quickly. It is also used on landing to reduce brake wear.
The aircraft's air data transducers are located under the nose . As with the F-104G CCV, the system was positioned as far forward as possible in order to remain unaffected by interference effects. The nose was beveled a little on the side to accommodate the outer measuring probes. The probes work on the principle of a pitot static system and are arranged to be rotatable in order to work as error-free as possible, even at high angles of incidence and sliding. For example, the outer probes can turn downwards at high angles of attack and thus adapt to the direction of flow.
The fuselage of the machine consists of an aluminum construction with CFRP planking, and superplastically deformed, diffusion-welded titanium is also used in the rear of the engines. The wedge-shaped air inlet has four receiving stations for the semi-submerged transport of air-to-air missiles.
Air inlet
The task of an air inlet is to achieve the highest possible total pressure recovery over a wide range of pitch, slip angle and speed. In order to perform this task as well as possible, the Typhoon's air inlet is very complex. It essentially consists of three components: the movable lower lip , the inlet ramp with boundary layer separator and ramp bleed system, as well as the slot suction (eng .throat bleed slot) in the inlet channel. The choice of an abdominal enema improves the independence of the angle of attack and sliding angle, the protruding nose also contributes to a compression effect at high angles of attack. The free flow is dammed up through the lower side of the nose and thus the air supply to the engine is improved. In combat aircraft with side inlets such as the F / A-18 Hornet , an air inlet is shielded from the free flow during flight at a high angle of slide, which leads to a loss of thrust.
When the Eurofighter is flying at low angles of attack, the air flow into the engine is controlled by the movable lower lip in order to reduce spillage drag . Overflow resistance occurs when the mass flow into the air inlet is greater or less than the air mass requirement of the engine. The problem here is that the air density changes with altitude and the inflow speed depends on the airspeed. In the case of an immobile inlet, the air column that is sucked in by the engine must either be "squeezed" or "pulled apart" into the air inlet, since the cross-sectional area of the inlet and the sucked in volume flow do not match.
When flying slowly at low altitude with little power requirement, only a small volume flow is required in the inlet, the lower lip is in the highest position here. If the engine is now run up to full power, the inflowing air mass flow must increase. Since the flow speed of the incoming air depends on the flight speed, the inlet geometry must be enlarged in order to increase the volume flow. The lower lip now folds down as you can see in the picture on the right at the start. The boundary layer separator keeps the turbulent air of the fuselage away from the inlet. Since air that is sucked in and flows through the ramp suction also becomes turbulent due to its rough surface, it is removed with the help of the slot suction and directed onto the wings, where it helps to increase lift.
When turning, the lower lip adjusts to the angle of attack of the aircraft. The reason for this is that the flow into the air inlet should not tear off and swirl at its lower edge. At high angles of attack, the effective area of the inlet opening is increased by the inlet ramp, and a significantly larger volume flow can now flow into the engine, which is an advantage at great heights. The regulation of the volume throughput to the engine now takes place via the ramp suction. The excess air is removed through the holes of the ramp suction and blown out again at the side slits. Due to the difference in level between the discharge opening and the leading edge of the wing when flying at an angle of attack, this air flows over the wings, where it contributes to the increase in lift.
The effectiveness of the air inlet can be seen in the following table. For comparison, the air inlets of a Su-27 and the rigid inlet of an F-16 are shown. The Flanker series uses movable lamellae under the inlet opening to reduce the total pressure loss at high angles of attack and to keep the thrust as high as possible. The data refer to an airspeed of Mach 0.5. The numbers are the pressure recovery at the appropriate angle of attack. Put simply, an engine with 100kN static thrust at an angle of attack of 50 ° has an installation thrust of 88kN with an F-16 inlet and 90kN with the air inlet of a Su-27 flanker.
Air inlet | 0 ° | 10 ° | 20 ° | 30 ° | 40 ° | 50 ° | 60 ° | 70 ° |
---|---|---|---|---|---|---|---|---|
Su-27 flanker | 0.97 | 0.96 | 0.94 | 0.92 | 0.91 | 0.90 | 0.88 | 0.86 |
F-16 Fighting Falcon | 0.97 | 0.96 | 0.94 | 0.91 | 0.90 | 0.88 | 0.84 | 0.81 |
Eurofighter | 0.97 | 0.97 | 0.97 | 0.97 | 0.97 | 0.965 | 0.96 | 0.95 |
In supersonic flight, the incoming air has to be slowed down to subsonic speed, which is also the task of an air inlet. In order to keep the total pressure loss as low as possible, as many oblique shock waves as possible should be used for braking. With the Typhoon, a sloping, downward-going compression shock is generated in supersonic flight at the tip of the wedge-shaped inlet ramp. The air is thereby slowed down, but it still moves at Mach> 1. The final, vertical shock wave then takes place on the ramp itself, through which the flow passes into subsonic. With increasing airspeed, the front compression shock becomes more oblique, the shock system moves backwards on the ramp. Above a certain speed, two further compression shocks form on the central wedge in the middle of the inlet, going off to the left and right. At the base of the shock waves on the ramp, there is a pressure jump in the boundary layer in the wall flow, causing it to become detached. The slot suction transports this swirling air to the wings, where it helps to increase lift. Compared to inlets that use movable ramps, the air inlet is not quite as effective, but it does not have any moving parts and can therefore be built more easily. Inlet systems without diagonal thrust compression have very high total pressure losses at high speeds. Due to the associated loss of thrust, such aircraft rarely reach speeds above Mach 2. The table shows the approximate pressure recovery of the individual inlets over the Mach number. While the F-16 inlet only performs a vertical surge, the Flanker series have movable ramps Commitment.
Air inlet | Do 1 | Do 1.25 | Mach 1.5 | Mach 1.75 | Do 2 | Mach 2.25 | Do 2.5 |
---|---|---|---|---|---|---|---|
Su-27 flanker | 1 | 1 | 0.98 | 0.96 | 0.93 | 0.90 | 0.86 |
F-16 Fighting Falcon | 1 | 0.96 | 0.90 | 0.85 | 0.75 | 0.6 | 0.5 |
Eurofighter | 1 | 0.98 | > 0.96 | > 0.95 | > 0.90 | > 0.87 | > 0.80 |
The air inlet is made of an aluminum alloy due to its complexity.
Vertical stabilizer
In the course of the development history of the Eurofighter Typhoon, the vertical stabilizer was the component that was subject to the most changes. While the TKF-90 and designs based on it such as the ACA had two vertical stabilizers, studies have shown that a single stabilizer is the best solution in terms of drag, flow interference and mass. The possibility of installing a fully movable pendulum vertical stabilizer was also examined. However, due to the lower overall mass and higher aeroelastic stiffness, it was decided to use a conventional vertical tail unit. As a compromise, the rudder is the largest actuator surface on the entire aircraft.
Like the wings, the tail unit is made of CFRP, the leading edges are made of an aluminum-lithium alloy for protection .
Effects
The greatest possible instability improves the performance data of the Typhoon significantly compared to other machines. The pressure point, which is far forward, moves backwards in supersonic flight, making the aircraft stable. Compared to other combat aircraft, however, the stability is much lower. As a result, the Eurofighter is the only combat aircraft capable of performing 9 g maneuvers in supersonic conditions. According to official information, this is possible up to Mach 1.2. The stability does not change with increasing speed, however, up to at least Mach 1.6. Furthermore, Mach 1.6 is the maximum maneuver speed according to which the aircraft was designed, which suggests a higher speed.
In subsonic flight the pressure point is very far forward, and an increase in the angle of attack shifts the lift vector further forward. If the pilot wants to push the typhoon's nose downwards (pitch recovery) , the duck wings must have a large angle of attack, which was the design limit of instability. The envelope is released to + 9 / -3g in subsonic. In an emergency, however, it is possible to achieve higher g-loads (override) . Load multiples of up to +12 g can be flown. Such stresses also occur at the Red Bull Air Race World Championship , so the development of liquid-filled anti-g suits for Air Race and Eurofighter pilots is understandable. The normal anti-g-suit Aircrew Equipment Assembly (AEA) consists of anti-g-pants, socks, vest and press ventilation for the pilot. The disadvantage here is that the system needs a certain amount of time to build up the counter pressure. The onset g-rate of the Eurofighter is therefore limited to 15 g / s by the Flight Control System (FCS).
When flying at low speed and thrust vector control , air forces can still be generated with the canards even at extreme angles of attack. The exposed position of this ensures an undisturbed flow, the long lever arm to the center of gravity for high effectiveness. This enables the nose to be aligned more quickly to a target or the torques of the thrust vector control to be compensated for in order to fly in a controlled manner at high angles of attack. In the Mongoose maneuver, for example, the aircraft pulls into the middle of the curve, straightens up and then stops on the thrust jet. At the moment (2010) it is not yet possible to foresee when scaffolding will take place.
The high maneuverability is part of the self-protection. The Praetorian self-protection system calculates the evasive course for approaching guided missiles and shows it on the head-up display . The pilot only has to follow the instructions on the screen and hold the aircraft within rectangles in order to follow the evasive course, all further countermeasures are taken initiated fully automatically.
Data table
- Since the TKF-90 was a concept, its data are hypothetical and vary depending on the state of the design
Characteristic value | Tactical fighter 90 | Experimental Aircraft Programs | Enhanced Fighter Maneuverability | European fighter aircraft | Eurofighter Typhoon |
---|---|---|---|---|---|
abbreviation | TKF-90 | EAP | EFM | EFA | EF 2000 |
Type | Air superiority fighter |
Aerodynamic prototype | Air superiority fighter |
Multipurpose fighter |
|
Empty mass | about 7710 kg | 10000 kg | 4633 kg | 9750 kg | 11000 kg |
length | 14.90 m | 14.70 m | 13.20 m | 15.96 m | |
height | 4.90 m | 5.52 m | 4.40 m | 5.28 m | |
span | 11.36 m | 11.77 m | 7.3 m | 10.95 m | |
Hydrofoil | Kink delta (57 °, 45 °) | Buckling Delta (N / A) | Delta (53 °) | ||
Wing area | 54 m² | 52 m² | 21 m² | 50 m² 1 | |
Wing extension | 2.38 | 2.66 | 2.53 | 2.39 | |
Wing loading (minimal) | 143 kg / m² | 192 kg / m² | 220 kg / m² | 195 kg / m² | 220 kg / m² |
ditto with full tanks | 225 kg / m² | N / A | N / A | 285 kg / m² | 320 kg / m² |
instability | 8-10% MAC | 15% MAC | N / A | 16% MAC | |
Vertical stabilizers | two | one | |||
Engine | Turbo-Union RB199 D | GE F404 | Eurojet EJ200 | ||
Maximum thrust | 2 × 75.5 kN | 1 × 71 kN | 2 × 95 kN | ||
Fuel mass | about 4150 kg | N / A | N / A | about 4500 kg 3 | 4996 kg |
Fuel mass fraction | 0.349 | N / A | N / A | 0.315 | 0.312 |
Thrust-to-weight ratio (maximum) | 1.99 | 1.53 | 1.56 | 1.98 | 1.76 |
ditto with full tanks | 1.25 | N / A | N / A | 1.35 | 1.21 |
Top speed | about Mach 2 | Mach 2.0 | Mach 1.28 | Mach 2.35 4 |
1 51.2 m² with extended slats
2 data for the war setting , with which the flight is flown
3 data unclear
4 2,495 km / h at 10,975 m altitude, at 1062 km / h speed of sound
Web links
- Artist's impression of the Rockwell SNAKE, note the similarity to the Eurofighter
- Pictures of the F-104G CCV
- Der Spiegel, edition 31/1985: With mention of Eurojäger and Advanced Tactical Fighter
- Popular Science, February 1989: On the Development of the X-31 and Its Maneuverability (Google Books)
- Keith McKay, British Aerospace: Eurofighter: Aerodynamics within a Multi-Disciplinary Design Environment (PDF; 1.4 MB)
- Eurofighter Typhoon Evening Display at Airbourne . The condensation effects are caused by negative pressure on the top of the wing ( YouTube video, 1:20)
Individual evidence
- ↑ a b c d e f g Keith McKay, British Aerospace: Eurofighter: Aerodynamics within a Multi-Disciplinary Design Environment ( Memento of March 3, 2012 in the Internet Archive ) (PDF; 1.4 MB)
- ↑ a b Der Spiegel, edition 31/1985
- ↑ Non-linearities in flight control systems ( Memento from December 2, 2010 in the Internet Archive )
- ↑ a b c d e f g Aeronautical research in Germany: from Lilienthal until today (preview of Google books)
- ↑ http://www.916-starfighter.de/Large/Special/f104CCV5.htm
- ↑ http://www.916-starfighter.de/Historie_CCV-F-104G.pdf
- ↑ http://www.airpower.at/flugzeuge/eurofighter/geschichte-konzept.htm
- ^ New Scientist of May 29, 1986: Europe's new fighter flies out of trouble
- ↑ http://www.waffenhq.de/specials/experimental/x-31.html
- ↑ Flying - traveling. In: Focus Online . October 14, 2018, accessed October 14, 2018 .
- ↑ a b Recent Experiences on Aerodynamic Parameter Identification for EUROFIGHTER at Alenia, British Aerospace, CASA and Daimler-Benz Aerospace ( Memento of March 3, 2012 in the Internet Archive ) (PDF; 1.1 MB)
- ↑ FliegerRevue September 2009, pp. 24–28, "Manching - Fitness Studio for the Air Force"
- ↑ a b c d e Eurofighter technology for the 21st century ( Memento from March 11, 2012 in the Internet Archive ) (PDF; 1.4 MB)
- ↑ Archive link ( Memento from June 20, 2014 in the Internet Archive )
- ↑ a b c BAE Systems: Aspects of Wing Design for Transonic and Supersonic Combat Aircraft ( Memento from August 29, 2013 in the Internet Archive ) (PDF; 1.6 MB)
- ^ A b Aircraft Systems: Mechanical, electrical, and avionics subsystems integration. 1. Flight Control Systems (PDF; 3.6 MB)
- ↑ http://www.ausairpower.net/Analysis-Typhoon.html
- ↑ a b c Paul Owen: Eurofighter Typhoon Structural Design ( Memento from June 20, 2014 in the Internet Archive )
- ↑ http://www.airpower.at/flugzeuge/eurofighter/technik-struktur.htm
- ↑ JG 74 Press Kit: Deactivation of the F-4F Phantom II and the Eurofighter QRA Presentation at Fighter Wing 74
- ↑ a b Troop service: The Eurofighter "Typhoon" (IV): materials, aerodynamics, flight control
- ↑ a b Aspects of altitude physiology when introducing the EF 2000 Eurofighter ( Memento from December 24, 2013 in the Internet Archive ) (PDF; 4.3 MB)
- ↑ Archive link ( Memento from November 7, 2012 in the Internet Archive )
- ^ Operational Capabilities of The Eurofighter Typhoon. ( Memento of March 27, 2009 in the Internet Archive ) P. 19/60.
- ↑ Page no longer available , search in web archives: Typhoon for Japan - 機体 概要
- ^ Bundesheer: Eurofighter EF 2000 - Technical data