Haber & Brandner
Georg Haber & Joh. LL Brandner GmbH
|
|
---|---|
legal form | GmbH |
founding | 1860 |
Seat | Regensburg / Berlin |
management | Georg J. Haber |
Number of employees | 40 |
sales | € 3 million (2008) |
Branch | Restoration , church equipment |
Website | haber-brandner.de |
The Georg Haber & Joh. LL Brandner GmbH is a German restoration company based in Regensburg and Berlin .
history
Haber & Brandner
The company Haber & Brandner was created in 1987 from the merger of the long-established companies Johann L. L. Brandner AG and the workshops for church art Georg Haber in Regensburg . Until the mid-1980s, Brandner AG and Haber were competing companies in the field of the production of church utensils. After economic difficulties, Brandner AG was sold and the Hotel Sorat was built in place of the former workshops on Oberen Wöhrd . Brandner's workforce found new jobs at Haber. Since 1987 this company has been operating under the name Georg Haber & Johann L. L. Brandner GmbH under the management of Georg J. Haber.
Since then, Haber & Brandner has still been one of the leading manufacturers of church equipment, but at the same time has developed into a workshop for metal restoration that is active throughout Europe.
Johann LL Brandner AG
In 1860 Johannes Brandner, a resourceful master craftsman and patent tinkerer, registered his company for metal turning and turnery in Regensburg . The actual history of the Brandner company began with his son, Johann Ludwig Leonhard Brandner, who took over the workshop in 1889. In a success story that is almost exemplary for the early days of the company, Johann L. L. Brandner transformed this small craft business into what is probably the largest church appliance factory in Central Europe. In the years up to 1909, the extensive workshops and operating facilities were built directly on the Danube . In the heyday before the First World War, the Brandner employed over 130 people. The factory was thus an important economic factor in the city.
Johann LL Brandner died in 1924. In his will, he had entrusted his nephew Hans Schneider with the management of the silver and metal goods factory , which was converted into a stock corporation the following year . Schneider successfully led the company through the following decades, riddled with crises, up to 1952.
The leading metal sculptor and designer in the workshops was Franz Weichmann from 1920 to 1942 , who after completing his apprenticeship as a chaser and engraver at Brandner had graduated from the state arts and crafts institute in Aachen . Then Adolf Engl, an academically trained goldsmith and metal artist, headed Brandner's business from 1952 to 1976.
The years after Engl were marked by economic problems, triggered by the declining demand for ecclesiastical equipment and the ever increasing pressure on the market, cheap competition from southern Europe. The history of this company culminated in 1987 when the name was changed to Georg Haber & Johann L. L. Brandner GmbH .
Georg Haber - Workshops for Church Art
In 1905 Georg Friedrich I. Haber founded a metal spinning shop after his training at the Regensburg church equipment manufacturer Deplaz . A few years later, the company established itself as a metal spinning and turning shop , manufacturing and trading in church equipment in today's office building at Schwanenplatz 1, formerly Kalmünzergasse 7, in Regensburg . Despite the addition of “fabrication”, the Haber workshop, in contrast to Brandner, always remained strongly oriented towards handicrafts; mass production was not planned. The family business also paid attention to clear structures, and the number of employees was also adapted to these circumstances.
In 1935 Georg Friedrich II. Haber took over the company, which he managed as a master belt maker and chaser until his death in 1965 . His son Georg Maximilian Haber, master belt maker and metal pusher, continued the family business in the traditional way. Together with his workshop manager Max Weiß, master silversmith and designer , he met the overpowering competitor Brandner with his own, modern designs.
In 1982 his son Georg Josef Haber joined the company and in 1985 he became managing director at Brandner. In 1987 they founded the new Haber & Brandner company together . Since the death of his father, Georg J. Haber is now the fourth generation to run the Haber & Brandner workshops .
Worldwide export in the 19th century
Since the middle of the 19th century, under the influence of Catholic clergy, Regensburg had become an important center for the manufacture of church utensils, from here the Catholic churches throughout the German Empire were supplied. The newly founded Brandner silver and metal goods factory thus had strong competition in the city. The long-established silversmiths and belts workshops of Joseph Goetz, Anton F. X. Fröhlich and Johann J. Deplaz dominated the market with their handcrafted church equipment.
Brandner opposed its competition with a new, modern production and sales concept. His workshops produced the church utensils, which had hitherto been painstakingly handcrafted, using machines and modern manufacturing processes in large numbers. The distribution was organized very successfully via product catalogs and resellers far beyond the German borders to America. Brandner also produced for the needs of the Evangelical Lutheran Church.
Craft tradition and industrialization
In its prime, Brandner had over 130 employees, but in contrast to other conditions in the manufacturing industry, there were only a few unskilled workers. The workshops were fully planned by Johann L. L. Brandner from the start. All professions and techniques required for production were found in the generously sized shops ( silversmiths , Gürtler , chasers , foundry and die makers, metal handles, Spengler , ironwork and locksmiths , toolmakers , turners , depositors and polishers, technical draftsman and administrative merchants).
In the first few years of his factory's boom, Johann LL Brandner had to get qualified employees from the competition in order to fulfill the orders. Later, all of the above-mentioned professions were trained according to the traditional craft rules. In Regensburg, training with Brandner was the basis for a successful professional life. Brandner was therefore never a factory in the classic sense. Its production was too complex and subject to constantly changing tastes.
From the production of church utensils to the restoration workshop
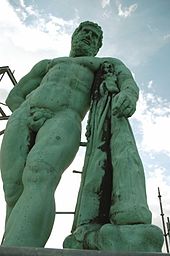
With the research of the Regensburg cathedral treasure and the restoration of the silver cathedral altar under Achim Hubel , a new era began in church monument preservation . To this end, in 1975 Hubel brought together the two leading Regensburg silversmiths' workshops, Haber and Brandner. Together, employees of the competing companies restored the baroque altar.
The preservation of monuments and their objectives had thus found their way into the workshops. Since joining the company in 1982, Georg J. Haber has intensified contacts with state and church monument preservation and consistently developed the workshop from a focus on new production to a restoration workshop for devices and objects made of metal.
Haber & Brandner in the 21st century
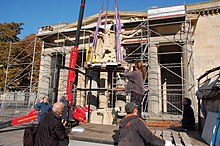
Haber & Brandner, based in Regensburg and Berlin, is a company with forty employees. The work spectrum of the workshops includes the restoration of historical objects and works of art made of gold , silver , bronze , brass , copper , iron , tin , zinc and lead . Colored frames on metal, gilding and silvering as well as organic and inorganic materials that appear in combination with metals are also restored and preserved.
The Berlin workshop has established itself in a listed craftsman's yard on Lehder Strasse in Weißensee. The building, built around 1904 with over 1,000 m² of workshop space, offers space for the extensive metal restoration tasks in Berlin and the new federal states.
education
The metal restoration workshops themselves train goldsmiths and silversmiths, metal workers (artistic blacksmiths and locksmiths), metalworkers (belt makers, engravers and chasers) and church painters. The objective of the training is the later activity in the restoration of art objects and cultural assets made of metal.
Since 2009, interested young people have been able to do a voluntary social year in monument protection in the workshops. The Jugendbauhütte is a project of the German Foundation for Monument Protection .
literature
- Georg J. Haber, Maximilian Heimler: The restoration of the equestrian statue of Ludwig I. In: Hans-Christopf Dittscheid, Peter Styra, Bernhard Lübbers (eds.): “You have an art-loving king” Ludwig I. and Regensburg . In: Catalogs and writings of the Regensburg State Library , Volume 2, Regensburg 2010, pp. 107–121 ff.
- Georg J. Haber, Maximilian Heimler: Zinc sculptures from Herrenchiemsee Palace. Restoration and transportation . In: Restauro , Heft 1, Callwey, Munich 1998, ISSN 0933-4017
- Georg J. Haber, Maximilian Heimler, Rolf-Jürgen Grote: Current restoration measures on the baroque lead sculptures of the hedge theater in Hanover-Herrenhausen. An interim report . In: Reports on the preservation of monuments in Lower Saxony , Volume 25, Issue 2/2005, pp. 45 ff, ISSN 0720-9835
- Georg J. Haber, Mandy Reimann: Metallic building plastic. Metal ornaments. In: Staatl. Museums zu Berlin - Prussian Cultural Heritage Foundation (ed.): The New Museum Berlin. Conservation, restoration, further construction in the World Heritage , 2009.
- Georg J. Haber, Maximilian Heimler: Galvanoplastic grave monuments of the turn of the century and their restoration problems. In: Restauro Heft 6, 1991, Callwey Verlag Munich, ISSN 0933-4017
- Meißner, Birgit, Haber, Georg J., Martin Mach: The Leipziger Mende fountain - history and restoration. In: B. Meißner, A. Doktor, M. Mach (eds.): Bronze and electroplating, history - material analysis - restoration , workbook 5, State Office for Monument Preservation Saxony and State Office for Monument Preservation Saxony-Anhalt, 1st edition, January 2000 .
- Stefan Brüggerhoff, Peter Königfeld , Heinrich Fendel, Vera Fendel, Georg J. Haber, Maximilian Heimler: The choir grids of the Osnabrück Cathedral - metal conservation and restoration of the color scheme, taking into account studies on the aspect of corrosion protection. In: Colored iron grids of the Baroque period , pp. 56–68. Ed .: Lower Saxony State Office for Monument Preservation (workbook No. 27) and German Mining Museum Bochum. 2002.
- Georg J. Haber, Mandy Reimann, Shane Casey: Techniques of carrying out conservation works - Experiences gained during research and "test applications" at the Museum in Jaworzyna Slaska. In: The Forms of Protection of the Monuments of Technology. Ed .: Oficyna Wydawnicza Politechniki Wrocławskiej, Wrocław, 2008.
- Georg J. Haber, Maximilian Heimler: Copper electroplating: history, manufacturing techniques and restoration problems of art industrial catalog goods. In: Peter Heinrich (Ed.): Metal restoration, contributions to analysis, conception and technology , 1994.
- Georg J. Haber, Maximilian Heimler: Regensburg belt makers and goldsmiths workshops. The development of a handicraft since the middle of the 19th century . In: The goldsmith Hugo Högner , exhibition catalog City Museum Regensburg, 1999.
- Georg J. Haber, Maximilian Heimler: The new-Romanesque high altar retable of St. Jakob in Regensburg. In: Yearbook of Bavarian Monument Preservation ; Vol. 41, 1987.
- Georg J. Haber, Maximilian Heimler: Restoration measures on large bronzes of the 19th century. In: Martin Mach (ed.): Metallrestaurierung - Metal Restoration . Workbooks of the Bavarian State Office for Monument Preservation, Volume 94, Munich 1998.
Web links and sources
- Haber & Brandner (company website)