Control valve
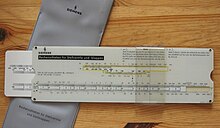
A control valve , also usually armature is as continuous valve often the actuator in a control loop . As a throttle device , it can be used to set the desired flow rate in a pipe .
The variable flow rate can be used to regulate the pressure, temperature, level or even the flow rate itself in a process engineering system . Control valves are therefore also used in process engineering . Because these have a typical appearance, valves that are not part of a control loop but have the same design are often referred to as control valves.
Orifice plates are also part of the throttle devices, but are not adjustable and therefore cannot be an actuator. Throttle valves are adjustable and are therefore a cost-effective alternative to control valves, especially for gases or with large pipeline diameters.
Working principle
The valve stem is connected to the valve cone . This closes the seat ring in the closed position. When the valve stem moves upwards, the annular flow opening becomes larger and the flow rate increases.
All throttle devices in a pipeline locally narrow the flow cross-section. This reduces the pressure of the medium and increases the speed. After the cross-section narrowing, the speed almost returns to the old value if the pipe diameter is the same before and after the constriction. However, there is a permanent loss of pressure .
The geometric shape of the cone determines the flow characteristic . This is linear , equal percentage or in rare cases different. The flow ratio that can be used for the regulation is 1:10 for simple valves, 1:50 is possible for complex valves.
interpretation
For cost reasons and because of the valve authority required for control, the nominal valve size is often chosen one or two nominal size steps smaller than the pipeline itself. An attempt is often made to get by with just a few nominal sizes in the entire system. This results in advantages in terms of stocking spare parts .
The necessary adjustment to the flow conditions is achieved by selecting the seat and cone. Different seat-plug combinations fit into one valve housing.
The key figure is the valve flow rate . Furthermore, it must be examined whether the maximum speed in extreme cases is below the speed of sound or, as a rule, below a few meters per second in order to avoid cavitation or excessive noise .
Control valves usually have a certain leak rate . In view of the need to save energy , however, the importance of tightly closing valves continues to increase in building technology, and this applies to all three ways in the case of three-way valves .
The installation conditions ( welded , clamped / sandwich construction or flanged ) result from the requirements of the associated pipe class .
material
The material is determined by the required corrosion resistance :
- in building technology ( heating and air conditioning ):
- usually gray cast iron and brass
- in special cases gunmetal and ductile cast iron
- in industry : also cast steel , stainless steel or plastics .
drive
The drive of control valves, actuator called, can pneumatically through a membrane , electrically or hydraulically via a piston carried. The choice of actuator depends on the application and the availability of the necessary auxiliary energy .
Most process engineering systems have a compressed air network (typically 6 bar ), which is why pneumatically driven control valves are widely used. In most cases, mechanical springs generate the necessary counterforce; if the compressed air fails, the valve then closes automatically; in a few cases it has to be the other way round, then the spring force opens the valve. Pneumatic drives have the advantage of a high positioning speed.
Electric drives, on the other hand, have the advantage of not requiring a compressed air supply. In addition, control valves with electric actuators are far less prone to undesired oscillations , since pressure changes in the medium have practically no effect on the position of the valve cone due to the self-locking of the gear unit . In the case of technical building applications (heating, air conditioning), almost exclusively electric valve drives are used.
Additional positioners are often used to standardize the control of the control valve drive .