Thermal power plant
A thermal power plant converts heat , more precisely thermal energy , partially into electrical energy. It is also called a thermal power plant or caloric power plant and only works if there are two heat reservoirs with a sufficient temperature difference . The heat is first converted into usable kinetic energy in a prime mover and this is then converted into electrical energy by a generator , i.e. energy conversions take place.
Many thermal power plants are steam power plants . However, there are also power plants that have no steam turbines or even a water cycle, such as historical power plants with steam engines or modern diesel / gas engine or gas turbine power plants . A common characteristic of today's thermal power plants are the thermodynamic cycles of the working medium , which are closed in steam power plants and open in gas power plants.
Importance of the thermal power plant
In most industrialized countries (exceptions: Norway , Switzerland and Austria ), thermal power plants provide a large part (60–100% depending on the region) of the electrical energy. The reason for this position are the very large, easily accessible energy reserves in the form of fossil fuels such as crude oil , coal and natural gas , as well as the decades of use of this technology. Alternative processes are becoming increasingly important because fossil deposits are limited.
Heat source
Most thermal power plants generate the heat they need themselves by burning fossil fuels or using the waste heat from nuclear processes in nuclear power plants . Geothermal energy and solar radiation can be used as natural heat sources .
Efficiency
The Carnot process on which the thermal power plants are based imposes fundamental limits on their electrical efficiency, so that considerable losses, mainly as heat, are unavoidable during energy conversion.
If the waste heat is not used for heating, the efficiency of today's power plant is typically between 30% and 45%. Higher efficiencies can be achieved in systems with more than one turbine , but the technical effort is correspondingly greater. Such systems are practically implemented, for example, in combined cycle power plants .
A significantly better utilization of the primary energy used can be achieved in thermal power stations by decoupling district or process heat ( combined heat and power ). As a result, overall efficiencies (more precisely: overall efficiency ) of 60% to 70% can be achieved, in block-type thermal power stations even over 90%.
Factors for practical usability
In addition to the efficiency, the following factors must be taken into account:
- General amount of energy available from the primary energy source
- Developable deposits
- Costs per unit of energy generated
- Technical feasibility of combustion
- Environmental pollution through emissions , waste heat or ionizing radiation
- Operational risks
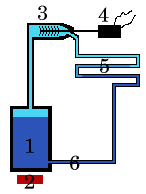
3: Steam turbine 4: Generator
5: Condenser 6: Connecting pipeline
cooling
Thermal power plants obtain their energy from a temperature difference ; the higher this is, the more energy can be obtained. In addition to a heat source that is as hot as possible, a heat sink that is as cold as possible is also helpful, which is why many thermal power plants have their working fluid cooled at a suitable location.
Many thermal power plants use the water of rivers flowing past to cool them. This saves or supports the cooling tower with its many disadvantages and the temperature at the outlet of the steam turbine can be lowered more effectively. However, this can make the river water too warm. For this reason, limit values are set for how many degrees Celsius or what maximum temperature the river can be heated to in order to prevent it from tipping over . In summer, when the water temperature is high, this can mean that a power plant has to be shut down. So-called heat load plans have been set up since the 1970s , from which the maximum temperature of the water can be found. Another option, which can also be combined, is the use of cooling towers, through which the waste heat is given off, provided that it cannot be used to heat neighboring residential areas or greenhouses via the combined heat and power system.
Thermal power plants are among the largest water consumers in the economy. In the industrialized countries around 40% of the total water abstraction from fresh water sources is attributable to thermal power plants, with nuclear power plants and (future) coal-fired power plants with CO2 capture and storage having the highest consumption .
Cooling method
With each of the cooling methods described below, the water must be cleaned of dirt with the help of filter systems so that the coarse dirt that is always present does not clog the downstream turbine condenser and thus render it ineffective. Flotsam rakes and filters are used for this purpose, the filters primarily protecting individual components such as condenser and heat exchanger . The cooling water is then cooled down in a cooling tower or a cooling pond to such an extent that it can either be discharged into a river or used again in the cooling circuit . Furthermore, the cooling towers of large power plants act like air washers. Their cleaning effect on the air flowing through them remains low for the environment , but the washed-out dust is concentrated in the cooling water and can cause considerable contamination of the downstream system components. The condensers of the steam turbines are particularly affected and must therefore be cleaned using the recirculating ball system.
Cooling system | Efficiency factor |
---|---|
Throughflow cooling (sea water) | 1.024 |
Flow cooling (river water) | 1.015 |
Wet cooling tower | 1,000 |
Dry cooling tower | 0.952 |
Continuous cooling without a cooling tower
If the heated cooling water is returned untreated into the water, it is a once-through cooling . Continuous cooling is the most efficient and economical form of cooling. However, it can only be used where the heat input does not pose an unreasonable burden on the body of water. The summer months are critical because the water body can then overturn . In Germany, once-through cooling is mainly operated at coastal locations or on the Rhine. Especially on the Rhine, the "Working Group of the Federal States to Keep the Rhine Clean (ARGE Rhein)" presented a heat load plan for the German section of the Rhine as early as 1971 , which is still valid today.
Drain cooling with cooling tower
In this process, the necessary cooling water is taken from flowing water, heated in the condenser and then sprayed in the cooling tower. The water that has not evaporated and has cooled down to its original temperature is fed back into the running water to flush out salts and impurities. The concentration of the latter would steadily increase if the water not released into the atmosphere were used repeatedly in the tower.
Circulation cooling with cooling tower
The circulation cooling, however, always uses the same water; only the losses from evaporation and drainage are added. This method has proven itself very well with a small supply of cooling water. However, the constant evaporation results in an increase in salt ( thickening ) of the cooling water, so that deposits of calcium and magnesium carbonates (hardness components) in particular occur. To counteract this effect, the cooling water is stabilized with chemicals (e.g. phosphonic acid ). Above a certain upper limit of the total salt content and the total hardness, a dilution of the cooling water must be brought about via the drainage and fresh water supply. State environmental requirements apply when the drainage is discharged into urban wastewater systems (indirect discharge) or bodies of water (direct discharge). Another problem with circulating cooling is the growth of microorganisms. In addition to fouling , hygienic problems with respirable bacteria in the cooling tower ( Legionella spec. , Pseudomonas aeruginosa ) must be taken into account. Therefore, the cooling water is also treated with biocide and bio-dispersant.
heater
The turbine shaft contracts when it cools from operating temperature to ambient temperature. Often so strong that it jams in its housing and can no longer turn. It must therefore be preheated before starting up (again). The shaft can also only be installed or removed when it is hot.
Often other components also have to be preheated before a thermal power plant can go into operation.
Technical implementation of the thermal power plant principle
- Heat extraction from nature (see also regenerative energy ):
- Heat release in the power plant itself:
-
Nuclear power plant (actually nuclear fission power plant )
- Nuclear fusion power plant (also a form of nuclear power plants but so far only research facilities)
-
coal-fired power station
- Lignite power plant
- Hard coal power plant
- Peat power plant
- Heating oil power plant
- Natural gas power plant
- Gas turbine power plant
- Combined cycle power plant
- Biomass power plant
-
Nuclear power plant (actually nuclear fission power plant )
- Heat extraction from other technical processes:
See also
Web links
Individual evidence
- ^ Edward A. Byers, Jim W. Hall, Jaime M. Amezaga, Electricity generation and cooling water use: UK pathways to 2050 . Global Environmental Change 25, (2014), 16–30, doi : 10.1016 / j.gloenvcha.2014.01.005 .
- ↑ Power Generation From Coal , p. 53